
- •Содержание
- •Глава 1 - Общие сведения о газотурбинных двигателях
- •1.1 — Введение
- •1.2.1.2 — Турбовинтовые двигатели и вертолетные ГТД
- •1.2.1.3 — Двухконтурные турбореактивные двигатели (ТРДД)
- •1.2.1.4 — Двигатели для самолетов вертикального взлета и посадки
- •1.2.1.5 - Комбинированные двигатели для больших высот и скоростей полета
- •1.2.1.6 - Вспомогательные авиационные ГТД и СУ
- •1.2.2 - Авиационные СУ
- •1.2.3 - История развития авиационных ГТД
- •1.2.3.1 - Россия
- •1.2.3.2 - Германия
- •1.2.3.3 – Англия
- •1.3 - ГТД наземного и морского применения
- •1.3.1 - Области применения наземных и морских ГТД
- •1.3.1.1 -Механический привод промышленного оборудования
- •1.3.1.2 - Привод электрогенераторов
- •1.3.1.3 - Морское применение
- •1.3.2 - Основные типы наземных и морских ГТД
- •1.3.2.1 - Стационарные ГТД
- •1.3.2.2 - Наземные и морские ГТД, конвертированные из авиадвигателей
- •1.3.2.3 - Микротурбины
- •1.4 - Основные мировые производители ГТД
- •1.4.1 - Основные зарубежные производители ГТД
- •1.4.2 - Основные российские производители ГТД
- •1.6 - Перечень использованной литературы
- •Глава 2 - Основные параметры и требования к ГТД
- •2.1 - Основы рабочего процесса ГТД
- •2.1.1 - ГТД как тепловая машина
- •2.1.1.1 – Простой газотурбинный цикл
- •2.1.1.2 - Применение сложных циклов в ГТД
- •2.1.2 - Авиационный ГТД как движитель
- •2.1.3 - Полный к.п.д. и топливная эффективность (экономичность) ГТД
- •2.2 - Параметры ГТД
- •2.2.1 - Основные параметры авиационных ГТД
- •2.2.2 - Основные параметры наземных и морских приводных ГТД
- •2.3 - Требования к авиационным ГТД
- •2.3.1 - Требования к тяге (мощности)
- •2.3.2 – Требования к габаритным и массовым характеристикам
- •2.3.3 - Возможность развития ГТД по тяге (мощности)
- •2.3.4 - Требования к используемым горюче-смазочным материалам
- •2.3.4.1 - Топлива авиационных ГТД
- •2.3.4.2 – Авиационные масла
- •2.3.4.3 - Авиационные гидравлические жидкости
- •2.3.5 – Надежность авиационных ГТД
- •2.3.5.1 – Основные показатели
- •2.3.5.1.1 – Показатели безотказности, непосредственно влияющие на безопасность работы двигателя
- •2.3.5.2 – Методология обеспечения надежности
- •2.3.5.2.1 – Этап проектирования
- •2.3.6 - Ресурс авиационных ГТД
- •2.3.6.1 - Методология обеспечения ресурса
- •2.3.6.2 - Количественные показатели ресурса
- •2.3.7 - Требования производственной технологичности
- •2.3.8 - Требования эксплуатационной технологичности
- •2.3.8.1 - Эксплуатационная технологичность - показатель совершенства ГТД
- •2.3.8.2 - Основные качественные характеристики ЭТ
- •2.3.8.3 - Количественные показатели ЭТ
- •2.3.9 - Экономические требования к авиационным ГТД
- •2.3.9.1 - Себестоимость производства
- •2.3.9.2 - Стоимость ЖЦ двигателя
- •2.3.10 - Экологические требования
- •2.3.10.2 - Ограничения по шуму
- •2.3.12 - Соответствие требованиям летной годности
- •2.4 - Особенности требований к ГТД наземного применения
- •2.4.1 - Особенности требований к приводным ГТД для ГПА
- •2.4.1.1 - Требования к характеристикам ГТД
- •2.4.1.2 - Требования к ресурсам и надежности
- •2.4.1.4 - Используемые ГСМ
- •2.4.1.5 - Требования экологии и безопасности
- •2.4.1.6 - Требования производственной и эксплуатационной технологичности
- •2.4.2 - Особенности требований к ГТД энергетических установок
- •2.4.2.1 - Требования к характеристикам ГТД
- •2.4.2.2 - Используемые ГСМ
- •2.4.2.3 - Требования к ресурсам и надежности
- •2.4.2.4 - Требования к экологии и безопасности
- •2.4.2.5 - Требования к контролепригодности, ремонтопригодности и др.
- •2.5 - Методология проектирования
- •2.5.1 - Основные этапы проектирования ГТД
- •2.5.1.1 - Техническое задание
- •2.5.1.2 – Техническое предложение
- •2.5.1.3 – Эскизный проект
- •2.5.1.4 – Технический проект
- •2.5.1.5 – Разработка конструкторской документации
- •2.5.2 - Разработка конструкций ГТД на основе базовых газогенераторов
- •2.5.2.1 - Газогенератор – базовый узел ГТД
- •2.5.2.2 – Основные параметры и конструктивные схемы газогенераторов ГТД
- •2.5.2.3 – Создание ГТД различного назначения на базе единого газогенератора
- •2.6.1.1 — Общие положения по авиационным ГТД
- •2.6.1.2 — Общие положения по сертификации наземной техники
- •2.6.1.3 — Общие положения по сертификации производства и СМК
- •2.6.1.4 — Органы регулирования деятельности
- •2.6.1.4.1 — Авиационная техника
- •2.6.1.4.2 — Органы регулирования деятельности по сертификации производства и СМК
- •2.6.2.1 — Авиационная техника
- •2.6.2.2 — Наземная техника
- •2.6.2.3 Производство и СМК
- •2.6.2.4 — Принятые сокращения и обозначения
- •2.6.3.1 — Основные этапы создания авиационных ГТД
- •2.6.3.2 — Этапы процесса сертификации авиационных ГТД
- •Глава 3 - Конструктивные схемы ГТД
- •3.1 - Конструктивные схемы авиационных ГТД
- •3.1.1 - Турбореактивные двигатели
- •3.1.2 - Двухконтурные турбореактивные двигатели
- •3.1.3 - Турбовинтовые и вертолетные ГТД
- •3.2 - Конструктивные схемы наземных и морских ГТД
- •3.2.1 - Одновальные ГТД
- •3.2.2 - ГТД со свободной силовой турбиной
- •3.2.3 - ГТД со «связанным» КНД
- •3.2.4 - Конструктивные особенности наземных ГТД различного назначения
- •3.2.5 - Конструктивные особенности ГТД сложных циклов
- •3.4 - Перечень использованной литературы
- •Глава 4 - Силовые схемы ГТД
- •4.1 - Усилия, действующие в ГТД
- •4.1.2 - Крутящие моменты от газовых сил
- •Глава 5 - Компрессоры ГТД
- •6.4.4 - Корпуса КС
- •6.4.4.1 - Наружный корпус КС
- •6.4.4.2 - Внутренний корпус КС
- •6.4.4.3 - Разработка конструкции корпусов
- •6.4.5 - Системы зажигания ГТД
- •6.5 - Экспериментальная доводка КС
- •6.6 - Особенности КС двигателей наземного применения
- •6.7 - Перспективы развития камер сгорания ГТД
- •Глава 7 - Форсажные камеры
- •7.1 - Характеристики ФК
- •7.2 - Работа ФК
- •7.3 - Требования к ФК
- •7.4 - Схемы ФК
- •7.4.2 - Вихревые ФК
- •7.4.3 - ФК с аэродинамической стабилизацией
- •7.5 - Основные элементы ФК
- •7.5.1 - Смеситель
- •7.5.2 - Диффузоры
- •7.5.3 - Фронтовые устройства
- •7.5.4 - Корпусы и экраны
- •7.6 - Управление работой ФК
- •7.6.1 - Розжиг ФК
- •7.6.2 - Управление ФК на режимах приемистости и сброса
- •7.6.3 - Управление ФК на стационарных режимах
- •Глава 8 - Турбины ГТД
- •8.2 - Аэродинамическое проектирование турбины
- •8.2.2 - Технология одномерного проектирования турбины
- •8.2.4 - 2D/3D-моделирование невязкого потока в проточной части турбины
- •8.2.5 - 2D/3D-моделирование вязкого потока в турбине
- •8.2.6 - Синтез геометрии профилей и лопаточных венцов
- •8.2.7 - Одномерное проектирование турбины
- •8.2.7.1 - Выбор количества ступеней ТВД
- •8.2.7.2 - Выбор количества ступеней ТНД
- •8.2.7.3 - Аэродинамическое проектирование и к.п.д. турбины
- •8.2.9 - Методы управления пространственным потоком в турбине
- •8.2.10 - Экспериментальное обеспечение аэродинамического проектирования
- •8.2.11 - Перечень использованной литературы
- •8.3 - Охлаждение деталей турбины
- •8.3.1 - Тепловое состояние элементов турбин
- •8.3.1.1 - Принципы охлаждения
- •8.3.2 - Конвективное, пленочное и пористое охлаждение
- •8.3.3 - Гидравлический расчет систем охлаждения
- •8.3.4 - Методология расчета температур основных деталей турбин
- •8.3.5 - Расчет полей температур в лопатках
- •8.3.6 - Перечень использованной литературы
- •8.4 - Роторы турбин
- •8.4.1 - Конструкции роторов
- •8.4.1.1 - Диски турбин
- •8.4.1.2 - Роторы ТВД
- •8.4.1.3 - Роторы ТНД и СТ
- •8.4.1.4 - Примеры доводки и совершенствования роторов
- •8.4.1.5 - Предотвращение раскрутки и разрушения дисков
- •8.4.2 - Рабочие лопатки турбин
- •8.4.2.1 - Соединение рабочих лопаток с диском
- •8.4.3 - Охлаждение рабочих лопаток
- •8.4.4 - Перечень использованной литературы
- •8.5 - Статоры турбин
- •8.5.1 - Корпусы турбин
- •8.5.2 - Сопловые аппараты
- •8.5.3 - Аппараты закрутки
- •8.5.4 – Перечень использованной литературы
- •8.6 - Радиальные зазоры в турбинах
- •8.6.1 - Влияние радиального зазора на к.п.д. турбины
- •8.6.2 - Изменение радиальных зазоров турбины в работе
- •8.6.3 - Управление радиальными зазорами
- •8.6.4 - Выбор радиального зазора при проектировании
- •8.6.5 - Перечень использованной литературы
- •8.7 - Герметизация проточной части
- •8.7.1 - Герметизация ротора и статора от утечек охлаждающего воздуха
- •8.7.2 - Уплотнения между ротором и статором
- •8.7.3 - Перечень использованной литературы
- •8.8 - Материалы основных деталей турбины
- •8.8.1 - Диски и роторные детали турбины
- •8.8.2 - Сопловые и рабочие лопатки
- •8.8.3 - Покрытия лопаток
- •8.8.4 - Корпусы турбин
- •8.9.1 - Перечень использованной литературы
- •8.10.1 - Прогары и трещины лопаток ТВД
- •8.10.3 - Недостаточный циклический ресурс и поломки роторных деталей
- •8.10.4 - Устранение дефектов турбины в ходе доводки
- •8.11 - Перспективы развития конструкций и методов проектирования турбин
- •8.11.1 - 2D-аэродинамика: эффективные охлаждаемые лопатки ТВД
- •8.11.2 - 2D-аэродинамика: сокращение количества лопаток
- •8.11.3 - Противоположное вращение роторов ТВД и ТНД
- •8.11.4 - 2D-аэродинамика: эффективные решетки профилей ТНД
- •8.11.5 - 3D-аэродинамика: эффективные формы лопаточных венцов
- •8.11.6 - Новые материалы и покрытия для лопаток и дисков
- •8.11.7 - Совершенствование конструкций охлаждаемых лопаток
- •8.11.8 - Оптимизированные системы управления радиальными зазорами
- •8.11.9 - Развитие средств и методов проектирования
- •Глава 9 - Выходные устройства ГТД
- •9.1 - Нерегулируемые сопла
- •9.2 - Выходные устройства ТРДД
- •9.2.1 - Выходные устройства со смешением потоков
- •9.2.2 - Выходные устройства ТРДД с раздельным истечением потоков
- •9.3 - Регулируемые сопла
- •9.3.1 - Осесимметричные регулируемые сопла
- •9.3.1.1 - Регулируемое сопло двигателя Д30-Ф6
- •9.3.2 - Плоские сопла
- •9.4 - Выходные устройства двигателей самолетов укороченного и вертикального взлета-посадки
- •9.5 - «Малозаметные» выходные устройства
- •9.6 - Реверсивные устройства
- •9.6.1 - Реверсивные устройства ковшового типа
- •9.6.2 - Реверсивные устройства створчатого типа
- •9.6.3.1 - Гидравлический привод реверсивного устройства
- •9.6.3.3 - Механический замок фиксации положения реверсивного устройства
- •9.7 - Приводы выходных устройств
- •9.7.1 - Пневмопривод
- •9.7.2 - Пневмомеханический привод
- •9.8 - Выходные устройства диффузорного типа
- •9.8.1 - Конические диффузоры
- •9.8.2 - Осекольцевые диффузоры
- •9.8.3 - Улитки
- •9.8.4 - Соединения с выхлопными шахтами
- •9.8.5 - Выходные устройства вертолетных ГТД
- •9.12 - Перечень использованной литературы
- •Глава 10 - Привод агрегатов, редукторы, муфты ГТД
- •10.1 - Привод агрегатов ГТД
- •10.1.1 - Центральный привод
- •10.1.2 - Коробки приводов агрегатов
- •10.2 - Редукторы ГТД
- •10.2.1 - Редукторы ТВД
- •10.2.1.1 - Общие требования, кинематические схемы
- •10.2.1.2 - Конструкция редукторов ТВД
- •10.2.2 - Редукторы привода несущего и рулевого винтов вертолетов
- •10.2.2.1 - Редукторы привода несущего винта
- •10.2.2.1.1 - Кинематические схемы главных редукторов вертолетов
- •10.2.2.1.2 - Конструкция главных редукторов вертолетов
- •10.2.2.2 - Редукторы хвостовые и промежуточные
- •10.2.3 - Редукторы ГТУ
- •10.2.3.1 - Конструкция редукторов
- •10.3 - Муфты приводов ГТД и ГТУ
- •10.3.1 - Требования к муфтам
- •10.3.2 - Конструкция муфт
- •10.4 - Проектирование приводов агрегатов ГТД
- •10.4.1 - Проектирование центрального привода
- •10.4.1.1 - Конструкция центрального привода
- •10.4.2 - Проектирование коробок приводов агрегатов
- •10.4.2.1 - Конструкция коробки приводов агрегатов
- •10. 5 - Проектирование редукторов
- •10.5.1 - Особенности проектирования редукторов ТВД
- •10.5.2 - Особенности проектирования вертолетных редукторов
- •10.5.3 - Особенности проектирования редукторов ГТУ
- •10.6.1 - Требования к зубчатым передачам
- •10.6.2 - Классификация зубчатых передач
- •10.6.3 - Исходный производящий контур
- •10.6.4 - Нагруженность зубчатых передач
- •10.6.5 - Конструктивные параметры зубчатых передач
- •10.6.5.1 - Конструкции зубчатых колес
- •10.6.6 - Материалы зубчатых колес, способы упрочнения
- •Глава 11 - Пусковые устройства
- •11.1 - Общие сведения
- •11.1.1 - Основные типы пусковых устройств современных ГТД
- •11.1.2 - Технические характеристики пусковых устройств современных ГТД
- •11.2 - Электрические пусковые устройства ГТД
- •11.3 - Воздушные пусковые устройства ГТД
- •11.3.1 - Воздушно - турбинные пусковые устройства ГТД
- •11.3.2 - Регулирующие и отсечные воздушные заслонки
- •11.3.3 - Струйное пусковое устройство ГТД
- •11.4 - Турбокомпрессорные пусковые устройства ГТД
- •11.4.1 - Классификация ТКС ГТД
- •11.4.2 - Принцип действия ТКС
- •11.4.3 - Одновальный ТКС
- •11.4.4 - ТКС со свободной турбиной
- •11.4.5 - Особенности систем ТКС
- •11.5 - Гидравлические пусковые устройства ГТД
- •11.5.1 - Конструкция гидравлических стартеров
- •11.6 - Особенности пусковых устройств ГТД наземного применения
- •11.6.1 - Электрические пусковые устройства
- •11.6.2 - Газовые пусковые устройства
- •11.6.3 - Гидравлические пусковые устройства
- •11.7 - Редукторы пусковых устройств
- •11.8 - Муфты свободного хода пусковых устройств
- •11.8.1 - Муфты свободного хода роликового типа
- •11.8.2 – Муфты свободного хода храпового типа
- •11.9 – Системы смазки пусковых устройств
- •11.11 - Перечень используемой литературы
- •Глава 12 - Системы ГТД
- •12.1.1 - Системы автоматического управления и контроля авиационных ГТД
- •12.1.1.1 - Назначение САУ
- •12.1.1.2 - Состав САУ
- •12.1.1.3 - Основные характеристики САУ
- •12.1.1.5.2 - Порядок разработки САУ
- •12.1.1.5.3 - Основные принципы выбора варианта САУ в процессе проектирования
- •12.1.1.5.4 - Структурное построение САУ
- •12.1.1.5.5 - Программы управления ГТД
- •12.1.1.5.6 - Расчет и анализ показателей надежности
- •12.1.2 - САУ наземных ГТУ
- •12.1.2.1 - Назначение САУ
- •12.1.2.2 - Выбор САУ ГТУ и ее элементов
- •12.1.2.3 - Состав САУ ГТУ
- •12.1.2.4 - Основные характеристики САУ
- •12.1.2.5 - Работа САУ ГТУ
- •12.1.2.6 - Блок управления двигателем (БУД)
- •12.1.2.7 - Особенности системы контроля и диагностики наземных ГТД
- •12.1.4 – Перечень использованной литературы
- •12.2 - Топливные системы ГТД
- •12.2.1 - Топливные системы авиационных ГТД
- •12.2.1.1 - Назначение топливной системы
- •12.2.1.2 - Состав топливной системы
- •12.2.1.3 - Основные характеристики топливной системы
- •12.2.1.4 - Работа топливной системы
- •12.2.1.5 - Выбор топливной системы и ее элементов
- •12.2.1.5.1 – Выбор топливной системы
- •12.2.1.5.2 - Выбор насосов топливной системы
- •12.2.1.5.3 - Определение подогревов топлива в топливной системе
- •12.2.1.5.5 - Математическая модель топливной системы
- •12.2.1.6 - Гидроцилиндры
- •12.2.1.7 - Топливные фильтры
- •12.2.2 - Особенности топливных систем ГТУ
- •12.2.2.1 - Назначение топливной системы
- •12.2.2.2 - Выбор топливной системы и ее элементов
- •12.2.2.3 - Основные характеристики топливной системы
- •12.2.2.4 - Работа топливной системы
- •12.2.4 – Перечень использованной литературы
- •12.3 - Системы диагностики
- •12.3.1 - Общие вопросы диагностирования
- •12.3.1.1 - Задачи диагностирования ГТД
- •12.3.1.3 - Диагностируемые системы ГТД
- •12.3.1.4 - Виды наземного и бортового диагностирования ГТД
- •12.3.1.5 - Структура систем диагностики
- •12.3.1.6 - Регламент диагностирования ГТД
- •12.3.1.7 - Регистрация параметров ГТД
- •12.3.2 - Диагностирование системы механизации ГТД, САУ и ТП ГТД
- •12.3.3 - Диагностирование работы маслосистемы и состояния узлов ГТД, работающих в масле
- •12.3.3.1 - Неисправности маслосистемы и узлов ГТД, работающих в масле
- •12.3.3.2 - Диагностирование по параметрам маслосистемы
- •12.3.3.3 - Контроль содержания в масле частиц износа (трибодиагностика)
- •12.3.4 - Контроль и диагностика по параметрам вибрации ГТД
- •12.3.4.1 - Параметры вибрации и единицы изменения
- •12.3.4.2 - Статистические характеристики вибрации
- •12.3.4.3 - Причины возникновения вибрации в ГТД
- •12.3.4.4 - Датчики измерения вибрации
- •12.3.4.5 - Вибрационная диагностика ГТД
- •12.3.5 - Диагностирование ГТД по газодинамическим параметрам
- •12.3.5.1 - Неисправности проточной части ГТД
- •12.3.5.2 - Требования к перечню контролируемых параметров
- •12.3.5.3 - Алгоритмы диагностирования проточной части ГТД
- •12.3.6 - Обеспечение диагностирования ГТД инструментальными методами
- •12.3.6.1 - Виды неисправностей, выявляемых инструментальными методами
- •12.3.6.2 - Методы и аппаратура инструментальной диагностики
- •12.3.6.2.1 - Оптический осмотр проточной части ГТД
- •12.3.6.2.2 - Ультразвуковой метод диагностирования
- •12.3.6.2.3 - Вихретоковый метод диагностирования
- •12.3.6.2.4 - Капиллярный метод диагностирования с применением портативных аэрозольных наборов
- •12.3.6.2.5 - Диагностирование состояния проточной части ГТД перспективными методами
- •12.3.7 - Особенности диагностирования технического состояния ГТД наземного применения на базе авиационных двигателей
- •12.3.7.1 - Особенности режимов эксплуатации
- •12.3.7.2 - Общие особенности диагностирования наземных ГТД
- •12.3.7.3 - Особенности диагностирования маслосистемы
- •12.3.7.5 - Особенности диагностирования проточной части
- •12.4 - Пусковые системы
- •12.4.1 - Пусковые системы авиационных ГТД
- •12.4.1.1 - Назначение
- •12.4.1.2 - Общие требования
- •12.4.1.3 - Состав пусковых систем
- •12.4.1.4 - Область эксплуатации двигателя, область запуска
- •12.4.1.6 - Надежность запуска
- •12.4.1.7 - Характеристики запуска
- •12.4.1.8. - Выбор типа и параметров стартера
- •12.4.1.9 - Особенности запуска двигателей двухроторных схем
- •12.4.1.10 - Системы зажигания
- •12.4.1.11 - Обеспечение характеристик запуска на разгоне
- •12.4.1.12 - Регулирование компрессора на пусковых режимах
- •12.4.2 - Особенности пусковых систем наземных ГТУ
- •12.4.4 - Перечень использованной литературы
- •12.5 - Воздушные системы ГТД
- •12.5.1 - Функции ВС
- •12.5.2 - Основные требования к ВС
- •12.5.3 - Общие и локальные ВС ГТД
- •12.5.4 - Работа локальных ВС
- •12.5.4.1 - ВС охлаждения турбин ГТД
- •12.5.4.2 - ВС наддува и охлаждения опор
- •12.5.4.2.1 - Работа ВС наддува и охлаждения опор
- •12.5.4.2.2 - Типы ВС наддува и охлаждения опор
- •12.5.4.2.3 - Построение общей схемы ВС наддува и охлаждения опор
- •12.5.4.3 - Противообледенительная система (ПОС)
- •12.5.4.4 - Система кондиционирования воздуха
- •12.5.4.5 - Система активного управления зазорами
- •12.5.4.6 - Системы внешнего охлаждения ГТД
- •12.5.4.7 - Системы внешнего обогрева ГТД
- •12.5.5 - Подготовка воздуха для ВС ГТД
- •12.5.6 - Особенности ВС наземных ГТУ
- •12.5.7 - Агрегаты ВС
- •12.5.9 - Перечень использованной литературы
- •12.6.1 - Общие требования
- •12.6.2 - Схемы маслосистем ГТД
- •12.6.2.1 - Маслосистема с регулируемым давлением масла
- •12.6.2.2 - Маслосистема с нерегулируемым давлением масла
- •12.6.2.3 - Маслосистемы ГТД промышленного применения
- •12.6.3 - Маслосистемы редукторов
- •12.6.3.1 - Маслосистемы авиационных редукторов
- •12.6.3.2 - Маслосистемы редукторов ГТУ
- •12.6.4 - Особенности проектирование маслосистем
- •12.6.5 - Агрегаты маслосистемы
- •12.6.5.1 - Бак масляный
- •12.6.5.2 - Насосы масляные
- •12.6.5.3 - Теплообменники
- •12.6.5.4 - Фильтры и очистители
- •12.6.5.5 - Воздухоотделители и суфлеры
- •12.6.6 - Перспективы развития маслосистем
- •12.6.8 – Перечень использованной литературы
- •12.7 - Гидравлические системы ГТД
- •12.7.1 - Гидросистемы управления реверсивными устройствами
- •12.7.1.1 - Централизованная гидросистема управления реверсивным устройством
- •12.7.1.2 - Автономная гидросистема управления реверсивным устройством
- •12.7.1.3 - Порядок проектирования гидросистем
- •12.7.3 - Перечень использованной литературы
- •12.8 - Дренажные системы
- •12.8.1 - Назначение и классификация систем
- •12.8.2 - Характеристика объектов дренажа
- •12.8.3 - Основные схемы и принцип действия систем
- •12.8.4 - Основные требования к дренажным системам
- •12.8.5 - Обеспечение работоспособности дренажных систем
- •12.8.6 - Особенности конструкции дренажных баков
- •12.8.8 - Перечень использованной литературы
- •Глава 13 - Обвязка авиационных ГТД
- •13.1 - Общая характеристика обвязки
- •13.2 - Конструкция обвязки
- •13.2.1 - Трубопроводные коммуникации
- •13.2.1.1 - Основные сведения
- •13.2.1.2 - Трубы и патрубки
- •13.2.1.3 - Соединения
- •13.2.1.4 - Компенсирующие устройства
- •13.2.1.5 - Соединительная арматура
- •13.2.1.6 - Узлы крепления
- •13.2.1.7 - Неисправности трубопроводов
- •13.2.2 - Электрические коммуникации
- •13.2.2.1 - Общие сведения
- •13.2.2.2 - Конструкция элементов
- •13.2.2.2.1 - Электрические жгуты
- •13.2.2.2.2 - Электрические провода
- •13.2.2.2.3 - Электрические соединители
- •13.2.2.2.4 - Материалы для изготовления электрических жгутов
- •13.2.3 - Узлы крепления агрегатов и датчиков
- •13.2.4 - Механическая проводка управления
- •13.3 - Проектирование обвязки
- •13.3.1 - Требования к обвязке
- •13.3.2 - Основные принципы и порядок проектирования обвязки
- •13.3.3 - Методы отработки конструкции обвязки
- •13.3.3.1 - Натурное макетирование
- •13.3.3.2 - Электронное макетирование обвязки
- •13.3.5 - Проектирование трубопроводных коммуникаций
- •13.3.6 - Проектирование электрических коммуникаций
- •13.3.6.1 - Требования к электрическим коммуникациям
- •13.3.6.2 - Порядок проектирования электрических коммуникаций
- •13.3.6.3 - Разработка электрических схем
- •13.3.6.4 - Разработка монтажных схем
- •13.3.6.5 - Разработка чертежей электрических жгутов
- •13.6 - Перечень использованной литературы
- •Глава 14 - Динамика и прочность ГТД
- •14.1 - Теоретические основы динамики и прочности ГТД
- •14.1.1 - Напряженное состояние, тензор напряжений
- •14.1.2 - Уравнения равновесия
- •14.1.3 - Перемещения в деформируемом твердом теле. Тензор деформаций
- •14.1.4 - Уравнения совместности деформаций
- •14.1.5 - Обобщенный закон Гука
- •14.1.7 - Плоская задача теории упругости
- •14.1.8 - Пластическая деформация материала. Простое и сложное нагружение
- •14.1.11 - Ползучесть. Релаксация напряжений. Длительная прочность
- •14.1.12 - Усталостное разрушение элементов конструкций
- •14.1.13 - Малоцикловая усталость. Термическая усталость
- •14.1.14 - Накопление повреждений при нестационарном нагружении
- •14.1.15 - Закономерности развития трещин в элементах конструкций
- •14.1.16 - Свободные колебания системы с одной степенью свободы
- •14.1.17 - Вынужденные колебания системы с одной степенью свободы
- •14.1.18 - Колебания системы с вязким сопротивлением. Демпфирование колебаний
- •14.1.19 - Вынужденные колебания системы с одной степенью свободы под действием произвольной периодической возмущающей силы
- •14.1.21 - Колебания системы с распределенной массой
- •14.2 - Статическая прочность и циклическая долговечность лопаток
- •14.2.1 - Нагрузки, действующие на лопатки. Расчетные схемы лопаток
- •14.2.2 - Напряжения растяжения в профильной части рабочей лопатки от центробежных сил
- •14.2.3 - Изгибающие моменты и напряжения изгиба от газодинамических сил
- •14.2.5 - Суммарные напряжения растяжения и изгиба в профильной части лопатки
- •14.2.6 - Температурные напряжения в лопатках
- •14.2.7 - Особенности напряженного состояния широкохордных рабочих лопаток
- •14.2.9 - Расчет соединения рабочих лопаток с дисками
- •14.2.10 - Расчет на прочность антивибрационных (бандажных) полок и удлинительной ножки лопатки
- •14.2.11 - Особенности расчета на прочность лопаток статора
- •14.2.13 - Анализ трехмерных полей напряжений и деформаций в лопатках
- •14.3 - Статическая прочность и циклическая долговечность дисков
- •14.3.1 - Расчетные схемы дисков
- •14.3.2 - Расчет напряжений в диске в плоской оссесимметричной постановке
- •14.3.3 - Общие закономерности напряженного состояния дисков
- •14.3.7 - Подтверждение циклического ресурса дисков на основе концепции допустимых повреждений
- •14.3.8 - Расчет роторов барабанного типа
- •14.3.9 - Расчет дисков радиальных турбомашин
- •14.3.10 - Оптимальное проектирование дисков. Равнопрочный диск
- •14.4 - Колебания и вибрационная прочность лопаток осевых компрессоров и турбин
- •14.4.2 - Приближенный расчет собственных частот колебаний лопаток
- •14.4.3 - Трехмерные модели колебаний лопаток
- •14.4.4 - Влияние конструктивных и эксплуатационных факторов на собственные частоты колебаний лопатки
- •14.4.6 - Автоколебания лопаток
- •14.4.7 - Демпфирование колебаний лопаток
- •14.4.8 - Вынужденные колебания лопаток. Резонансная диаграмма
- •14.4.9 - Математическое моделирование вынужденных колебаний лопаток
- •14.4.10 - Экспериментальное исследование колебаний лопаток
- •14.4.11 - Коэффициент запаса вибрационной прочности лопаток, пути его повышения
- •14.4.12 - Колебания дисков
- •14.5 - Динамика роторов. Вибрация ГТД
- •14.5.1 - Критическая частота вращения ротора. История вопроса
- •14.5.2 - Динамика одномассового ротора. Поступательные перемещения
- •14.5.3 - Динамика одномассового ротора. Угловые перемещения
- •14.5.4 - Динамика одномассового несимметричного ротора
- •14.5.5 - Ротор с распределенными параметрами
- •14.5.6 - Особенности колебаний системы роторов и корпусов
- •14.5.7 - Демпфирование колебаний роторов
- •14.5.7.1 - Конструкция и принцип действия демпферов колебаний роторов
- •14.5.7.2 - Расчет параметров демпфирования
- •14.5.7.3 - Особенности гидромеханики реальных демпферов
- •14.5.8 - Вибрация ГТД
- •14.5.8.1 - Источники возмущающих сил и спектр вибрации
- •14.5.8.3 - Статистические характеристики вибрации
- •14.5.8.4 - Измерение и нормирование вибрации
- •14.6 - Прочность корпусов и подвески двигателя
- •14.6.1 - Силовая схема корпуса. Условия работы силовых корпусов
- •14.6.4 - Устойчивость корпусных деталей
- •14.6.5 - Расчет корпусов на непробиваемость
- •14.6.6 - Расчет элементов подвески
- •14.8 – Перечень использованной литературы
- •Глава 15 - Шум ГТД
- •15.1 - Источники шума ГТД
- •15.3 - Методы оценки акустических характеристик
- •15.4 - Снижение шума ГТД
- •15.4.1 - Методология проектирования систем шумоглушения
- •15.4.2 - Шумоглушение в выходных устройствах авиационных ГТД
- •15.4.3 - Конструкция звукопоглощающих узлов авиационных ГТД
- •15.4.4 – Глушители шума в наземных ГТУ
- •15.4.5 – Конструкция глушителей шума наземных ГТД
- •15.7 – Список использованной литературы
- •Глава 16 - Газотурбинные двигатели как силовой привод
- •16.1 - ГТД в силовом приводе ГТЭС и ГПА
- •16.2 - ГТД в силовых (энергетических) установках кораблей и судов
- •16.3 - ГТД в силовых установках танков
- •16.5 - Компоновка корабельных и судовых ГГТД
- •16.6 - Компоновка ГТД в силовой установке танка
- •16.8 – Перечень использованной литературы
- •Глава 17 - Автоматизация проектирования и поддержки жизненного цикла ГТД
- •17.1 - Проектирование и информационная поддержка жизненного цикла ГТД (идеология CALS)
- •17.2 - Жизненный цикл изделия. Обзор методов проектирования
- •17.3 - Программные средства проектирования
- •17.4 - Аппаратные средства систем проектирования
- •17.5 - PDM-системы: роль и место в организации проектирования
- •17.6 - Организация производства и ERP-системы
- •17.7 - Параллельный инжиниринг. Интеграция эскизного и технического проектирования
- •17.8 - Переход на безбумажную технологию
- •17.10 - ИПИ-технологии и эксплуатация изделий
- •17.11 - ИПИ-технологии и управление качеством
- •17.12 - Анализ и реинжиниринг бизнес-процессов
- •17.13 - Основы трехмерного проектирования
- •17.13.1 - Общие принципы трехмерного проектирования
- •17.13.1.1 - Способы создания геометрических моделей
- •17.13.1.2 - Основные термины объемной геометрической модели
- •17.13.1.3 - Принцип базового тела
- •17.13.1.4 - Основные термины при проектировании геометрической модели детали
- •17.13.2 - Управляющие структуры
- •17.13.3 - Принцип «Мастер-модели»
- •17.13.5 - Моделирование сборок
- •17.15 - Перечень использованной литературы
- •Глава 18 - Уплотнения в ГТД
- •18.1 - Уплотнение неподвижных соединений
- •18.2 - Уплотнения подвижных соединений
- •18.2.1 - Гидравлический расчет уплотнений подвижных соединений
- •18.3 - Уплотнение газового тракта между ротором и статором ГТД
- •18.3.1 - Лабиринтные уплотнения
- •18.3.2 - Щеточные уплотнения
- •18.3.3 - Скользящие сухие уплотнения газодинамические
- •18.3.4 - Скользящие сухие уплотнения газостатические
- •18.3.5 - Сравнение эффективностей уплотнений газового тракта между ротором и статором ГТД
- •18.4 - Примеры уплотнений газового тракта ГТД
- •18.4.1 - Пример 1
- •18.4.2 - Пример 2. Уплотнение статорной и роторной частей турбины
- •18.5 - Уплотнения масляных полостей опор роторов, редукторов, коробок приводов
- •18.7 - Перечень использованной литературы

Глава 12 - Системы ГТД
12.3 - Системы диагностики
Техническая диагностика – это новая область знаний, возникшая в связи с потребностями современной техники. Она охватывает теорию, методы и средства определения технического состояния различных объектов, в том числе и авиационных ГТД. Применение диагностики при их эксплуатации обусловлено невозможностью изготовления абсолютно надежных отдельных деталей и узлов, а также вероятностью некачественной сборки и ремонта двигателей. Вложение средств в техническую диагностику можно считать «платой» за экономию при разработке, тестировании, изготовлении, сборке и испытаниях газотурбинных двигателей. Диагностика решает задачи их безопасной эксплуатации, поэтому экономическая эффективность диагностики может выражаться, прежде всего, в стоимости последствий несостоявшихся аварий и катастроф.
Но есть и более тонкая составляющая экономической эффективности применения диагностики – это возможность оптимизации загрузки оборудования, планирование ремонтов и замены модулей, агрегатов, деталей, увеличение ресурса за счет обеспечения эксплуатации ГТД по техни- ческому состоянию с учетом фактического времени работы на наиболее напряженных режимах.
Исправное состояние – состояние объекта, при котором он соответствует всем требованиям нормативно-технической и конструкторской (проектной) документации.
Неисправное состояние – состояние объекта, при котором он не соответствует хотя бы одному из требований нормативно-технической и конструкторской (проектной) документации.
Работоспособное состояние – состояние объекта, при котором значения всех параметров, характеризующих способность выполнять заданные функции, соответствуют требованиям норма- тивно-технической и конструкторской (проектной) документации.
Диагностический (контролируемый) параметр – параметр объекта, используемый при его диагностировании (контроле).
Прогнозирование технического состояния –
определение технического состояния объекта с заданной вероятностью на предстоящий интервал времени.
Алгоритм технического диагностирования –
совокупность предписаний, определяющих последовательность при проведении диагностирования.
Термин «техническое диагностирование» в отличие от словосочетания «техническая диагностика» обозначает сам рабочий процесс.
12.3.1 - Общие вопросы диагностирования
Ниже представлены наиболее часто применяемые диагностические термины и определения в соответствии с ГОСТ [12.3.9.1…12.3.9.6].
Техническое диагностирование – определение технического состояния объекта.
Техническое состояние – состояние, которое характеризуется в определенный момент времени, при определенных условиях внешней среды, зна- чениями параметров, установленных технической документацией на объект.
Контроль технического состояния – проверка соответствия значений параметров объекта требованиям технической документации и определение на этой основе одного из заданных видов технического состояния в данный момент. Видами технического состояния являются, например, исправное, работоспособное, неисправное, неработоспособное и т.п. в зависимости от значений параметров в данный момент времени.
Параметр технического состояния – величи- на, характеризующая способность объекта диагностирования выполнять возложенные на него функции.
12.3.1.1 - Задачи диагностирования ГТД
Диагностирование представляет собой комплексную процедуру, разделяющуюся в общем слу- чае на три этапа.
1.Контроль технического состояния, заключа- ющийся согласно [12.3.9.4…12.3.9.6] «в проверке соответствия значений параметров требованиям технической документации и определении на этой основе одного из заданных видов технического состояния в данный момент времени» в минимально необходимом объеме и на основании формальных правил.
2.Поиск места и определение причин отказа для постановки диагноза с учетом прошлого (генеза) и настоящего состояний объекта диагностики.
3.Прогнозирование технического состояния за счет экстраполяции оценок состояния объекта при построении тренда (тенденции) и разработки прогноза на будущее.
Диагностирование авиационных ГТД выполняется, как правило, при наземном обслуживании. Для этого в эксплуатирующих организациях функционируют лаборатории диагностики, в которых практикуется узкая специализация по видам диаг-
758
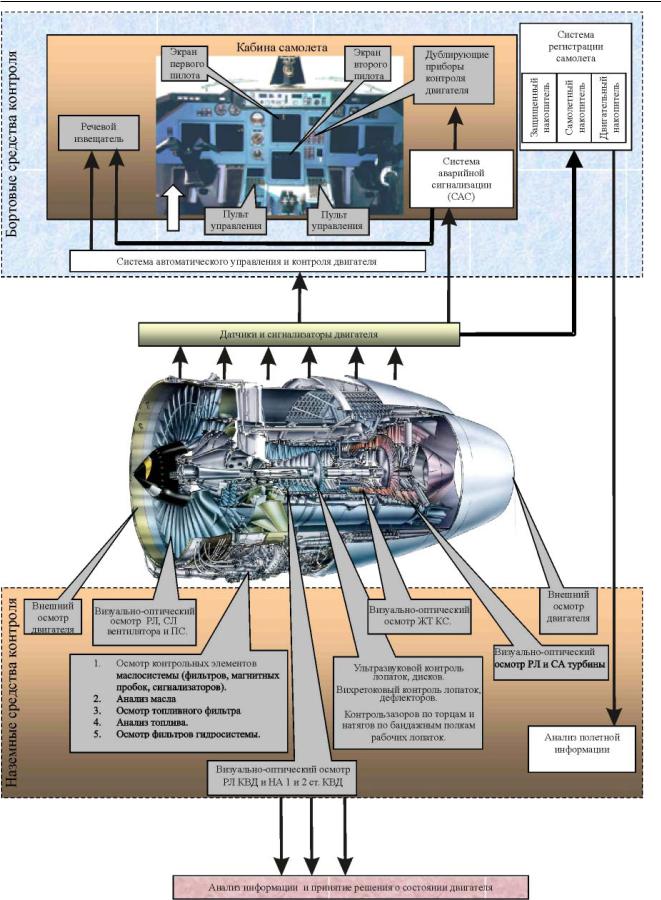
Глава 12 - Системы ГТД
Рисунок 12.3.1.1_1 - Б лок–схема комплексной системы диагностирования технического состояния двигателя ПС-90А
759

Глава 12 - Системы ГТД
ностирования, что обусловлено большим объемом специфических знаний, которыми должен обладать исполнитель в каждом виде диагностирования. Системы диагностики обеспечивают выявление неисправностей на ранней стадии их развития, предоставление обслуживающему персоналу сведений для скорейшего и наименее трудоемкого выявления отказавшего узла или системы, прогнозирование наступления неисправного или неработоспособного состояния ГТД, а также ряд сопутствующих функций, обусловленных информационной емкостью некоторых систем диагностирования (расчет наработок, учет комплектации, контроль действий экипажа и т.д.).
На Рис. 12.3.1.1_1 показан вариант блок схемы комплексной системы диагностики технического состояния современного двигателя на примере двигателя ПС-90А. Показаны не только функции диагностирования, но и функции оперативного контроля технического состояния, выполняемые в полете экипажем и бортовой системой контроля двигателя (БСКД) и при наземном обслуживании техническим персоналом.
По мере развития науки и техники расширяется применение средств автоматизации в диагностике. Применение мощных компактных средств автоматизации позволяет осуществлять некоторые функции диагностирования непосредственно в процессе выполнения полета бортовыми средствами или наземными средствами с использованием передачи информации с самолета по беспроводным коммуникационным каналам. Результатом применения таких систем является повышение степени готовности самолета к вылету, снижение риска вылета неисправного самолета из транзитного аэропорта, возможность длительной эксплуатации в отрыве от базового аэродрома.
12.3.1.2 - Оптимальная контролепригодность ГТД – основа
эффективного диагностирования
Конструкция авиационного газотурбинного двигателя должна удовлетворять требованиям контролепригодности, изложенным в основном нормативном документе [12.3.9.7], в частности, допускать слежение за дефектами, потенциально опасными для данного типа ГТД (осмотр кромок лопаток, контроль трещин в покрывных дисках и т.п.).
Приспособленность объекта к диагностированию заданными средствами и есть контролепригодность. Общие требования к контролепригодности устанавливаются едиными нормами летной годности самолетов (ЕНЛГС). Они должны обеспечиваться на всех стадиях разработки новых
èмодернизации серийно выпускаемых двигателей с учетом трудоемкости и затрат на их обеспечение
èдостигаемого экономического эффекта.
Одним из основных средств обеспечения контролепригодности обычно является наличие специального перечня (спецификации) контролируемых параметров и способов их измерения, а также стандартизация и унификация процесса определения значений параметров и конструктивных решений с целью осуществления доступа к контрольным точкам, установка встроенных измерительных датчиков и гнезд для их подключения и т.п. Базовой характеристикой контролепригодности является перечень измеряемых в полете функциональных
èспециальных диагностических параметров, а также перечень узлов и деталей двигателя, доступных для средств неразрушающего контроля и диагностирования без разборки двигателя в процессе эксплуатации.
Хорошая контролепригодность узлов двигателя – иначе говоря, уровень их приспособленности к проведению операций по выполнению необходимых видов диагностирования технического состояния газотурбинных двигателей - является одним из главных условий для осуществления современных требований по эксплуатации авиационных ГТД по состоянию. Контролепригодность для современных ГТД должна обеспечиваться уже на стадии проектирования путем введения в конструкцию специальных отверстий (лючков) с быстросъ¸мными заглушками. Такие отверстия в соответствии с нормативными требованиями должны быть выполнены в корпусах компрессора и турбины для обеспе- чения диагностирования состояния всех рабочих лопаток. Кроме того, для осуществления эффективного диагностирования ответственных деталей ГТД должны быть разработаны методы, средства неразрушающего контроля и инструменты, приспособленные для надежной доставки датчиков к местам диагностирования даже без визуального наблюдения за этим процессом.
Требования ЕНЛГС для самолетов всех типов, предъявляемые к маршевым ГТД:
1.Двигатель и его агрегаты должны быть спроектированы и изготовлены так, чтобы была возможность для осмотра, технического обслуживания и замены деталей, агрегатов и других элементов конструкции двигателя в эксплуатации в соответствии с руководством по эксплуатации
èобслуживанию двигателя.
2.На двигателе в соответствии с действующей нормативно-технической документацией должна быть установлена аппаратура, обеспечивающая проверку исправности двигателя и прогнозирование его
760

Глава 12 - Системы ГТД
технического состояния, в том числе с помощью бортового устройства регистрации параметров.
3. Двигатель должен быть оснащен средствами обнаружения механических повреждений для выявления отказов на ранних стадиях их развития
èоценки технического состояния двигателей в эксплуатации. Эти средства должны включать:
-магнитные пробки, сигнализаторы в масляной системе и удобно расположенные сливные краны для периодического отбора масла и его анализа на содержание в нем железа и других металлов;
-устройства в виде окон и люков для периодического осмотра деталей газовоздушного тракта с помощью ультразвуковых, токовихревых и других приборов зондового типа, причем, количество и размещение окон и люков должно быть выбрано так, чтобы была обеспечена возможность оценки состояния рабочих лопаток всех ступеней компрессора
èтурбины, внутренней поверхности камеры сгорания и других элементов конструкции;
-датчики и сигнализаторы для измерения необходимых параметров.
Контролепригодность является свойством двигателя, обеспечивающим информационную базу диагностирования.
Чем выше контролепригодность, тем больше возможностей для диагностирования. Однако обеспечение максимальной контролепригодности ведет за собой увеличение стоимости, массы двигателя
èвозможное снижение надежности конструкции. Поэтому, при разработке двигателя следует стремиться к оптимальному уровню контролепригодности. Необходимо помнить, что задача создания надежной конструкции является приоритетной по отношению к задаче обеспечения возможности диагностирования.
Оптимизация обеспечивается не только принятием решения о введении в конструкцию како- го-либо средства контролепригодности, но и выбором между разными способами диагностирования одних и тех же неисправностей, хотя в некоторых случаях, когда требуется максимальная достоверность диагноза, возможно одновременное применение альтернативных методов.
Необходимость обеспечения контролепригодности различных узлов двигателя должна быть сопоставлена с тяжестью возможных последствий при их поломке. Следует также сопоставлять стоимость объекта диагностирования и стоимость средств диагностирования.
Обеспечение контролепригодности на стадии проектирования двигателя может носить потенциальный характер: в конструкцию двигателя и систем могут закладываться возможности введения при
небольших доработках дополнительных возможностей диагностирования. Это достигается резервированием мест для дополнительных датчиков, лючков для осмотра, резервированием САУ двигателя по информационному обеспечению. По мере доводки конструкции двигателя возможно прекращение некоторых видов его диагностирования в эксплуатации, сопровождаемое, например, исключением соответствующих датчиков.
Контролепригодность дополнительно к выполнению уже упомянутых требований может обеспечи- ваться модульностью конструкции двигателя. В некоторых случаях узел, подозреваемый в наличии неисправности, может быть оперативно заменен и исследован уже отдельно от двигателя для обеспечения высокой готовности самолета к вылету.
12.3.1.3 - Диагностируемые системы ГТД
С точки зрения оценки технического состояния двигатель можно разделить на следующие системы
èузлы: компрессор, турбина, КС, выходное устройство (реверсивное устройство, реактивное сопло), центральный привод, коробка приводов, редуктор, система механизации, воздушная система, система отборов воздуха, система смазки и суфлирования , система топливопитания, САУ, БСКД, гидравлическая система.
Все системы и узлы ГТД в той или иной мере подвергаются диагностированию. Глубина диагностирования в каждом случае различна, и это обусловлено, прежде всего, контролепригодностью системы или узла.
Некоторые системы, как, например, САУ
èБСКД, обладают функциями самодиагностирования, а иногда и парирования возникающих отказов. Другие системы и узлы ГТД, такие, как компрессор, турбина, система смазки и суфлирования, имеют достаточное количество датчиков и сигнализаторов, позволяющих получать объективную информацию об их состоянии по параметрам.
Проточная часть компрессора, КС, турбины в значительной мере может быть осмотрена с помощью эндоскопов, проверена ультразвуковым
èвихретоковым методами, возможна оценка ее состояния с помощью методов заряженных частиц. Для системы смазки и суфлирования и деталей двигателя, работающих в масле, применимы различные методы анализа наличия частиц износа в масле.
Âто же время существуют системы двигателя, исправность которых обеспечивается конструктивно при изготовлении, например, системы газовых уплотнений. Безусловно, их неисправное состояние
761