
- •Содержание
- •Глава 1 - Общие сведения о газотурбинных двигателях
- •1.1 — Введение
- •1.2.1.2 — Турбовинтовые двигатели и вертолетные ГТД
- •1.2.1.3 — Двухконтурные турбореактивные двигатели (ТРДД)
- •1.2.1.4 — Двигатели для самолетов вертикального взлета и посадки
- •1.2.1.5 - Комбинированные двигатели для больших высот и скоростей полета
- •1.2.1.6 - Вспомогательные авиационные ГТД и СУ
- •1.2.2 - Авиационные СУ
- •1.2.3 - История развития авиационных ГТД
- •1.2.3.1 - Россия
- •1.2.3.2 - Германия
- •1.2.3.3 – Англия
- •1.3 - ГТД наземного и морского применения
- •1.3.1 - Области применения наземных и морских ГТД
- •1.3.1.1 -Механический привод промышленного оборудования
- •1.3.1.2 - Привод электрогенераторов
- •1.3.1.3 - Морское применение
- •1.3.2 - Основные типы наземных и морских ГТД
- •1.3.2.1 - Стационарные ГТД
- •1.3.2.2 - Наземные и морские ГТД, конвертированные из авиадвигателей
- •1.3.2.3 - Микротурбины
- •1.4 - Основные мировые производители ГТД
- •1.4.1 - Основные зарубежные производители ГТД
- •1.4.2 - Основные российские производители ГТД
- •1.6 - Перечень использованной литературы
- •Глава 2 - Основные параметры и требования к ГТД
- •2.1 - Основы рабочего процесса ГТД
- •2.1.1 - ГТД как тепловая машина
- •2.1.1.1 – Простой газотурбинный цикл
- •2.1.1.2 - Применение сложных циклов в ГТД
- •2.1.2 - Авиационный ГТД как движитель
- •2.1.3 - Полный к.п.д. и топливная эффективность (экономичность) ГТД
- •2.2 - Параметры ГТД
- •2.2.1 - Основные параметры авиационных ГТД
- •2.2.2 - Основные параметры наземных и морских приводных ГТД
- •2.3 - Требования к авиационным ГТД
- •2.3.1 - Требования к тяге (мощности)
- •2.3.2 – Требования к габаритным и массовым характеристикам
- •2.3.3 - Возможность развития ГТД по тяге (мощности)
- •2.3.4 - Требования к используемым горюче-смазочным материалам
- •2.3.4.1 - Топлива авиационных ГТД
- •2.3.4.2 – Авиационные масла
- •2.3.4.3 - Авиационные гидравлические жидкости
- •2.3.5 – Надежность авиационных ГТД
- •2.3.5.1 – Основные показатели
- •2.3.5.1.1 – Показатели безотказности, непосредственно влияющие на безопасность работы двигателя
- •2.3.5.2 – Методология обеспечения надежности
- •2.3.5.2.1 – Этап проектирования
- •2.3.6 - Ресурс авиационных ГТД
- •2.3.6.1 - Методология обеспечения ресурса
- •2.3.6.2 - Количественные показатели ресурса
- •2.3.7 - Требования производственной технологичности
- •2.3.8 - Требования эксплуатационной технологичности
- •2.3.8.1 - Эксплуатационная технологичность - показатель совершенства ГТД
- •2.3.8.2 - Основные качественные характеристики ЭТ
- •2.3.8.3 - Количественные показатели ЭТ
- •2.3.9 - Экономические требования к авиационным ГТД
- •2.3.9.1 - Себестоимость производства
- •2.3.9.2 - Стоимость ЖЦ двигателя
- •2.3.10 - Экологические требования
- •2.3.10.2 - Ограничения по шуму
- •2.3.12 - Соответствие требованиям летной годности
- •2.4 - Особенности требований к ГТД наземного применения
- •2.4.1 - Особенности требований к приводным ГТД для ГПА
- •2.4.1.1 - Требования к характеристикам ГТД
- •2.4.1.2 - Требования к ресурсам и надежности
- •2.4.1.4 - Используемые ГСМ
- •2.4.1.5 - Требования экологии и безопасности
- •2.4.1.6 - Требования производственной и эксплуатационной технологичности
- •2.4.2 - Особенности требований к ГТД энергетических установок
- •2.4.2.1 - Требования к характеристикам ГТД
- •2.4.2.2 - Используемые ГСМ
- •2.4.2.3 - Требования к ресурсам и надежности
- •2.4.2.4 - Требования к экологии и безопасности
- •2.4.2.5 - Требования к контролепригодности, ремонтопригодности и др.
- •2.5 - Методология проектирования
- •2.5.1 - Основные этапы проектирования ГТД
- •2.5.1.1 - Техническое задание
- •2.5.1.2 – Техническое предложение
- •2.5.1.3 – Эскизный проект
- •2.5.1.4 – Технический проект
- •2.5.1.5 – Разработка конструкторской документации
- •2.5.2 - Разработка конструкций ГТД на основе базовых газогенераторов
- •2.5.2.1 - Газогенератор – базовый узел ГТД
- •2.5.2.2 – Основные параметры и конструктивные схемы газогенераторов ГТД
- •2.5.2.3 – Создание ГТД различного назначения на базе единого газогенератора
- •2.6.1.1 — Общие положения по авиационным ГТД
- •2.6.1.2 — Общие положения по сертификации наземной техники
- •2.6.1.3 — Общие положения по сертификации производства и СМК
- •2.6.1.4 — Органы регулирования деятельности
- •2.6.1.4.1 — Авиационная техника
- •2.6.1.4.2 — Органы регулирования деятельности по сертификации производства и СМК
- •2.6.2.1 — Авиационная техника
- •2.6.2.2 — Наземная техника
- •2.6.2.3 Производство и СМК
- •2.6.2.4 — Принятые сокращения и обозначения
- •2.6.3.1 — Основные этапы создания авиационных ГТД
- •2.6.3.2 — Этапы процесса сертификации авиационных ГТД
- •Глава 3 - Конструктивные схемы ГТД
- •3.1 - Конструктивные схемы авиационных ГТД
- •3.1.1 - Турбореактивные двигатели
- •3.1.2 - Двухконтурные турбореактивные двигатели
- •3.1.3 - Турбовинтовые и вертолетные ГТД
- •3.2 - Конструктивные схемы наземных и морских ГТД
- •3.2.1 - Одновальные ГТД
- •3.2.2 - ГТД со свободной силовой турбиной
- •3.2.3 - ГТД со «связанным» КНД
- •3.2.4 - Конструктивные особенности наземных ГТД различного назначения
- •3.2.5 - Конструктивные особенности ГТД сложных циклов
- •3.4 - Перечень использованной литературы
- •Глава 4 - Силовые схемы ГТД
- •4.1 - Усилия, действующие в ГТД
- •4.1.2 - Крутящие моменты от газовых сил
- •Глава 5 - Компрессоры ГТД
- •6.4.4 - Корпуса КС
- •6.4.4.1 - Наружный корпус КС
- •6.4.4.2 - Внутренний корпус КС
- •6.4.4.3 - Разработка конструкции корпусов
- •6.4.5 - Системы зажигания ГТД
- •6.5 - Экспериментальная доводка КС
- •6.6 - Особенности КС двигателей наземного применения
- •6.7 - Перспективы развития камер сгорания ГТД
- •Глава 7 - Форсажные камеры
- •7.1 - Характеристики ФК
- •7.2 - Работа ФК
- •7.3 - Требования к ФК
- •7.4 - Схемы ФК
- •7.4.2 - Вихревые ФК
- •7.4.3 - ФК с аэродинамической стабилизацией
- •7.5 - Основные элементы ФК
- •7.5.1 - Смеситель
- •7.5.2 - Диффузоры
- •7.5.3 - Фронтовые устройства
- •7.5.4 - Корпусы и экраны
- •7.6 - Управление работой ФК
- •7.6.1 - Розжиг ФК
- •7.6.2 - Управление ФК на режимах приемистости и сброса
- •7.6.3 - Управление ФК на стационарных режимах
- •Глава 8 - Турбины ГТД
- •8.2 - Аэродинамическое проектирование турбины
- •8.2.2 - Технология одномерного проектирования турбины
- •8.2.4 - 2D/3D-моделирование невязкого потока в проточной части турбины
- •8.2.5 - 2D/3D-моделирование вязкого потока в турбине
- •8.2.6 - Синтез геометрии профилей и лопаточных венцов
- •8.2.7 - Одномерное проектирование турбины
- •8.2.7.1 - Выбор количества ступеней ТВД
- •8.2.7.2 - Выбор количества ступеней ТНД
- •8.2.7.3 - Аэродинамическое проектирование и к.п.д. турбины
- •8.2.9 - Методы управления пространственным потоком в турбине
- •8.2.10 - Экспериментальное обеспечение аэродинамического проектирования
- •8.2.11 - Перечень использованной литературы
- •8.3 - Охлаждение деталей турбины
- •8.3.1 - Тепловое состояние элементов турбин
- •8.3.1.1 - Принципы охлаждения
- •8.3.2 - Конвективное, пленочное и пористое охлаждение
- •8.3.3 - Гидравлический расчет систем охлаждения
- •8.3.4 - Методология расчета температур основных деталей турбин
- •8.3.5 - Расчет полей температур в лопатках
- •8.3.6 - Перечень использованной литературы
- •8.4 - Роторы турбин
- •8.4.1 - Конструкции роторов
- •8.4.1.1 - Диски турбин
- •8.4.1.2 - Роторы ТВД
- •8.4.1.3 - Роторы ТНД и СТ
- •8.4.1.4 - Примеры доводки и совершенствования роторов
- •8.4.1.5 - Предотвращение раскрутки и разрушения дисков
- •8.4.2 - Рабочие лопатки турбин
- •8.4.2.1 - Соединение рабочих лопаток с диском
- •8.4.3 - Охлаждение рабочих лопаток
- •8.4.4 - Перечень использованной литературы
- •8.5 - Статоры турбин
- •8.5.1 - Корпусы турбин
- •8.5.2 - Сопловые аппараты
- •8.5.3 - Аппараты закрутки
- •8.5.4 – Перечень использованной литературы
- •8.6 - Радиальные зазоры в турбинах
- •8.6.1 - Влияние радиального зазора на к.п.д. турбины
- •8.6.2 - Изменение радиальных зазоров турбины в работе
- •8.6.3 - Управление радиальными зазорами
- •8.6.4 - Выбор радиального зазора при проектировании
- •8.6.5 - Перечень использованной литературы
- •8.7 - Герметизация проточной части
- •8.7.1 - Герметизация ротора и статора от утечек охлаждающего воздуха
- •8.7.2 - Уплотнения между ротором и статором
- •8.7.3 - Перечень использованной литературы
- •8.8 - Материалы основных деталей турбины
- •8.8.1 - Диски и роторные детали турбины
- •8.8.2 - Сопловые и рабочие лопатки
- •8.8.3 - Покрытия лопаток
- •8.8.4 - Корпусы турбин
- •8.9.1 - Перечень использованной литературы
- •8.10.1 - Прогары и трещины лопаток ТВД
- •8.10.3 - Недостаточный циклический ресурс и поломки роторных деталей
- •8.10.4 - Устранение дефектов турбины в ходе доводки
- •8.11 - Перспективы развития конструкций и методов проектирования турбин
- •8.11.1 - 2D-аэродинамика: эффективные охлаждаемые лопатки ТВД
- •8.11.2 - 2D-аэродинамика: сокращение количества лопаток
- •8.11.3 - Противоположное вращение роторов ТВД и ТНД
- •8.11.4 - 2D-аэродинамика: эффективные решетки профилей ТНД
- •8.11.5 - 3D-аэродинамика: эффективные формы лопаточных венцов
- •8.11.6 - Новые материалы и покрытия для лопаток и дисков
- •8.11.7 - Совершенствование конструкций охлаждаемых лопаток
- •8.11.8 - Оптимизированные системы управления радиальными зазорами
- •8.11.9 - Развитие средств и методов проектирования
- •Глава 9 - Выходные устройства ГТД
- •9.1 - Нерегулируемые сопла
- •9.2 - Выходные устройства ТРДД
- •9.2.1 - Выходные устройства со смешением потоков
- •9.2.2 - Выходные устройства ТРДД с раздельным истечением потоков
- •9.3 - Регулируемые сопла
- •9.3.1 - Осесимметричные регулируемые сопла
- •9.3.1.1 - Регулируемое сопло двигателя Д30-Ф6
- •9.3.2 - Плоские сопла
- •9.4 - Выходные устройства двигателей самолетов укороченного и вертикального взлета-посадки
- •9.5 - «Малозаметные» выходные устройства
- •9.6 - Реверсивные устройства
- •9.6.1 - Реверсивные устройства ковшового типа
- •9.6.2 - Реверсивные устройства створчатого типа
- •9.6.3.1 - Гидравлический привод реверсивного устройства
- •9.6.3.3 - Механический замок фиксации положения реверсивного устройства
- •9.7 - Приводы выходных устройств
- •9.7.1 - Пневмопривод
- •9.7.2 - Пневмомеханический привод
- •9.8 - Выходные устройства диффузорного типа
- •9.8.1 - Конические диффузоры
- •9.8.2 - Осекольцевые диффузоры
- •9.8.3 - Улитки
- •9.8.4 - Соединения с выхлопными шахтами
- •9.8.5 - Выходные устройства вертолетных ГТД
- •9.12 - Перечень использованной литературы
- •Глава 10 - Привод агрегатов, редукторы, муфты ГТД
- •10.1 - Привод агрегатов ГТД
- •10.1.1 - Центральный привод
- •10.1.2 - Коробки приводов агрегатов
- •10.2 - Редукторы ГТД
- •10.2.1 - Редукторы ТВД
- •10.2.1.1 - Общие требования, кинематические схемы
- •10.2.1.2 - Конструкция редукторов ТВД
- •10.2.2 - Редукторы привода несущего и рулевого винтов вертолетов
- •10.2.2.1 - Редукторы привода несущего винта
- •10.2.2.1.1 - Кинематические схемы главных редукторов вертолетов
- •10.2.2.1.2 - Конструкция главных редукторов вертолетов
- •10.2.2.2 - Редукторы хвостовые и промежуточные
- •10.2.3 - Редукторы ГТУ
- •10.2.3.1 - Конструкция редукторов
- •10.3 - Муфты приводов ГТД и ГТУ
- •10.3.1 - Требования к муфтам
- •10.3.2 - Конструкция муфт
- •10.4 - Проектирование приводов агрегатов ГТД
- •10.4.1 - Проектирование центрального привода
- •10.4.1.1 - Конструкция центрального привода
- •10.4.2 - Проектирование коробок приводов агрегатов
- •10.4.2.1 - Конструкция коробки приводов агрегатов
- •10. 5 - Проектирование редукторов
- •10.5.1 - Особенности проектирования редукторов ТВД
- •10.5.2 - Особенности проектирования вертолетных редукторов
- •10.5.3 - Особенности проектирования редукторов ГТУ
- •10.6.1 - Требования к зубчатым передачам
- •10.6.2 - Классификация зубчатых передач
- •10.6.3 - Исходный производящий контур
- •10.6.4 - Нагруженность зубчатых передач
- •10.6.5 - Конструктивные параметры зубчатых передач
- •10.6.5.1 - Конструкции зубчатых колес
- •10.6.6 - Материалы зубчатых колес, способы упрочнения
- •Глава 11 - Пусковые устройства
- •11.1 - Общие сведения
- •11.1.1 - Основные типы пусковых устройств современных ГТД
- •11.1.2 - Технические характеристики пусковых устройств современных ГТД
- •11.2 - Электрические пусковые устройства ГТД
- •11.3 - Воздушные пусковые устройства ГТД
- •11.3.1 - Воздушно - турбинные пусковые устройства ГТД
- •11.3.2 - Регулирующие и отсечные воздушные заслонки
- •11.3.3 - Струйное пусковое устройство ГТД
- •11.4 - Турбокомпрессорные пусковые устройства ГТД
- •11.4.1 - Классификация ТКС ГТД
- •11.4.2 - Принцип действия ТКС
- •11.4.3 - Одновальный ТКС
- •11.4.4 - ТКС со свободной турбиной
- •11.4.5 - Особенности систем ТКС
- •11.5 - Гидравлические пусковые устройства ГТД
- •11.5.1 - Конструкция гидравлических стартеров
- •11.6 - Особенности пусковых устройств ГТД наземного применения
- •11.6.1 - Электрические пусковые устройства
- •11.6.2 - Газовые пусковые устройства
- •11.6.3 - Гидравлические пусковые устройства
- •11.7 - Редукторы пусковых устройств
- •11.8 - Муфты свободного хода пусковых устройств
- •11.8.1 - Муфты свободного хода роликового типа
- •11.8.2 – Муфты свободного хода храпового типа
- •11.9 – Системы смазки пусковых устройств
- •11.11 - Перечень используемой литературы
- •Глава 12 - Системы ГТД
- •12.1.1 - Системы автоматического управления и контроля авиационных ГТД
- •12.1.1.1 - Назначение САУ
- •12.1.1.2 - Состав САУ
- •12.1.1.3 - Основные характеристики САУ
- •12.1.1.5.2 - Порядок разработки САУ
- •12.1.1.5.3 - Основные принципы выбора варианта САУ в процессе проектирования
- •12.1.1.5.4 - Структурное построение САУ
- •12.1.1.5.5 - Программы управления ГТД
- •12.1.1.5.6 - Расчет и анализ показателей надежности
- •12.1.2 - САУ наземных ГТУ
- •12.1.2.1 - Назначение САУ
- •12.1.2.2 - Выбор САУ ГТУ и ее элементов
- •12.1.2.3 - Состав САУ ГТУ
- •12.1.2.4 - Основные характеристики САУ
- •12.1.2.5 - Работа САУ ГТУ
- •12.1.2.6 - Блок управления двигателем (БУД)
- •12.1.2.7 - Особенности системы контроля и диагностики наземных ГТД
- •12.1.4 – Перечень использованной литературы
- •12.2 - Топливные системы ГТД
- •12.2.1 - Топливные системы авиационных ГТД
- •12.2.1.1 - Назначение топливной системы
- •12.2.1.2 - Состав топливной системы
- •12.2.1.3 - Основные характеристики топливной системы
- •12.2.1.4 - Работа топливной системы
- •12.2.1.5 - Выбор топливной системы и ее элементов
- •12.2.1.5.1 – Выбор топливной системы
- •12.2.1.5.2 - Выбор насосов топливной системы
- •12.2.1.5.3 - Определение подогревов топлива в топливной системе
- •12.2.1.5.5 - Математическая модель топливной системы
- •12.2.1.6 - Гидроцилиндры
- •12.2.1.7 - Топливные фильтры
- •12.2.2 - Особенности топливных систем ГТУ
- •12.2.2.1 - Назначение топливной системы
- •12.2.2.2 - Выбор топливной системы и ее элементов
- •12.2.2.3 - Основные характеристики топливной системы
- •12.2.2.4 - Работа топливной системы
- •12.2.4 – Перечень использованной литературы
- •12.3 - Системы диагностики
- •12.3.1 - Общие вопросы диагностирования
- •12.3.1.1 - Задачи диагностирования ГТД
- •12.3.1.3 - Диагностируемые системы ГТД
- •12.3.1.4 - Виды наземного и бортового диагностирования ГТД
- •12.3.1.5 - Структура систем диагностики
- •12.3.1.6 - Регламент диагностирования ГТД
- •12.3.1.7 - Регистрация параметров ГТД
- •12.3.2 - Диагностирование системы механизации ГТД, САУ и ТП ГТД
- •12.3.3 - Диагностирование работы маслосистемы и состояния узлов ГТД, работающих в масле
- •12.3.3.1 - Неисправности маслосистемы и узлов ГТД, работающих в масле
- •12.3.3.2 - Диагностирование по параметрам маслосистемы
- •12.3.3.3 - Контроль содержания в масле частиц износа (трибодиагностика)
- •12.3.4 - Контроль и диагностика по параметрам вибрации ГТД
- •12.3.4.1 - Параметры вибрации и единицы изменения
- •12.3.4.2 - Статистические характеристики вибрации
- •12.3.4.3 - Причины возникновения вибрации в ГТД
- •12.3.4.4 - Датчики измерения вибрации
- •12.3.4.5 - Вибрационная диагностика ГТД
- •12.3.5 - Диагностирование ГТД по газодинамическим параметрам
- •12.3.5.1 - Неисправности проточной части ГТД
- •12.3.5.2 - Требования к перечню контролируемых параметров
- •12.3.5.3 - Алгоритмы диагностирования проточной части ГТД
- •12.3.6 - Обеспечение диагностирования ГТД инструментальными методами
- •12.3.6.1 - Виды неисправностей, выявляемых инструментальными методами
- •12.3.6.2 - Методы и аппаратура инструментальной диагностики
- •12.3.6.2.1 - Оптический осмотр проточной части ГТД
- •12.3.6.2.2 - Ультразвуковой метод диагностирования
- •12.3.6.2.3 - Вихретоковый метод диагностирования
- •12.3.6.2.4 - Капиллярный метод диагностирования с применением портативных аэрозольных наборов
- •12.3.6.2.5 - Диагностирование состояния проточной части ГТД перспективными методами
- •12.3.7 - Особенности диагностирования технического состояния ГТД наземного применения на базе авиационных двигателей
- •12.3.7.1 - Особенности режимов эксплуатации
- •12.3.7.2 - Общие особенности диагностирования наземных ГТД
- •12.3.7.3 - Особенности диагностирования маслосистемы
- •12.3.7.5 - Особенности диагностирования проточной части
- •12.4 - Пусковые системы
- •12.4.1 - Пусковые системы авиационных ГТД
- •12.4.1.1 - Назначение
- •12.4.1.2 - Общие требования
- •12.4.1.3 - Состав пусковых систем
- •12.4.1.4 - Область эксплуатации двигателя, область запуска
- •12.4.1.6 - Надежность запуска
- •12.4.1.7 - Характеристики запуска
- •12.4.1.8. - Выбор типа и параметров стартера
- •12.4.1.9 - Особенности запуска двигателей двухроторных схем
- •12.4.1.10 - Системы зажигания
- •12.4.1.11 - Обеспечение характеристик запуска на разгоне
- •12.4.1.12 - Регулирование компрессора на пусковых режимах
- •12.4.2 - Особенности пусковых систем наземных ГТУ
- •12.4.4 - Перечень использованной литературы
- •12.5 - Воздушные системы ГТД
- •12.5.1 - Функции ВС
- •12.5.2 - Основные требования к ВС
- •12.5.3 - Общие и локальные ВС ГТД
- •12.5.4 - Работа локальных ВС
- •12.5.4.1 - ВС охлаждения турбин ГТД
- •12.5.4.2 - ВС наддува и охлаждения опор
- •12.5.4.2.1 - Работа ВС наддува и охлаждения опор
- •12.5.4.2.2 - Типы ВС наддува и охлаждения опор
- •12.5.4.2.3 - Построение общей схемы ВС наддува и охлаждения опор
- •12.5.4.3 - Противообледенительная система (ПОС)
- •12.5.4.4 - Система кондиционирования воздуха
- •12.5.4.5 - Система активного управления зазорами
- •12.5.4.6 - Системы внешнего охлаждения ГТД
- •12.5.4.7 - Системы внешнего обогрева ГТД
- •12.5.5 - Подготовка воздуха для ВС ГТД
- •12.5.6 - Особенности ВС наземных ГТУ
- •12.5.7 - Агрегаты ВС
- •12.5.9 - Перечень использованной литературы
- •12.6.1 - Общие требования
- •12.6.2 - Схемы маслосистем ГТД
- •12.6.2.1 - Маслосистема с регулируемым давлением масла
- •12.6.2.2 - Маслосистема с нерегулируемым давлением масла
- •12.6.2.3 - Маслосистемы ГТД промышленного применения
- •12.6.3 - Маслосистемы редукторов
- •12.6.3.1 - Маслосистемы авиационных редукторов
- •12.6.3.2 - Маслосистемы редукторов ГТУ
- •12.6.4 - Особенности проектирование маслосистем
- •12.6.5 - Агрегаты маслосистемы
- •12.6.5.1 - Бак масляный
- •12.6.5.2 - Насосы масляные
- •12.6.5.3 - Теплообменники
- •12.6.5.4 - Фильтры и очистители
- •12.6.5.5 - Воздухоотделители и суфлеры
- •12.6.6 - Перспективы развития маслосистем
- •12.6.8 – Перечень использованной литературы
- •12.7 - Гидравлические системы ГТД
- •12.7.1 - Гидросистемы управления реверсивными устройствами
- •12.7.1.1 - Централизованная гидросистема управления реверсивным устройством
- •12.7.1.2 - Автономная гидросистема управления реверсивным устройством
- •12.7.1.3 - Порядок проектирования гидросистем
- •12.7.3 - Перечень использованной литературы
- •12.8 - Дренажные системы
- •12.8.1 - Назначение и классификация систем
- •12.8.2 - Характеристика объектов дренажа
- •12.8.3 - Основные схемы и принцип действия систем
- •12.8.4 - Основные требования к дренажным системам
- •12.8.5 - Обеспечение работоспособности дренажных систем
- •12.8.6 - Особенности конструкции дренажных баков
- •12.8.8 - Перечень использованной литературы
- •Глава 13 - Обвязка авиационных ГТД
- •13.1 - Общая характеристика обвязки
- •13.2 - Конструкция обвязки
- •13.2.1 - Трубопроводные коммуникации
- •13.2.1.1 - Основные сведения
- •13.2.1.2 - Трубы и патрубки
- •13.2.1.3 - Соединения
- •13.2.1.4 - Компенсирующие устройства
- •13.2.1.5 - Соединительная арматура
- •13.2.1.6 - Узлы крепления
- •13.2.1.7 - Неисправности трубопроводов
- •13.2.2 - Электрические коммуникации
- •13.2.2.1 - Общие сведения
- •13.2.2.2 - Конструкция элементов
- •13.2.2.2.1 - Электрические жгуты
- •13.2.2.2.2 - Электрические провода
- •13.2.2.2.3 - Электрические соединители
- •13.2.2.2.4 - Материалы для изготовления электрических жгутов
- •13.2.3 - Узлы крепления агрегатов и датчиков
- •13.2.4 - Механическая проводка управления
- •13.3 - Проектирование обвязки
- •13.3.1 - Требования к обвязке
- •13.3.2 - Основные принципы и порядок проектирования обвязки
- •13.3.3 - Методы отработки конструкции обвязки
- •13.3.3.1 - Натурное макетирование
- •13.3.3.2 - Электронное макетирование обвязки
- •13.3.5 - Проектирование трубопроводных коммуникаций
- •13.3.6 - Проектирование электрических коммуникаций
- •13.3.6.1 - Требования к электрическим коммуникациям
- •13.3.6.2 - Порядок проектирования электрических коммуникаций
- •13.3.6.3 - Разработка электрических схем
- •13.3.6.4 - Разработка монтажных схем
- •13.3.6.5 - Разработка чертежей электрических жгутов
- •13.6 - Перечень использованной литературы
- •Глава 14 - Динамика и прочность ГТД
- •14.1 - Теоретические основы динамики и прочности ГТД
- •14.1.1 - Напряженное состояние, тензор напряжений
- •14.1.2 - Уравнения равновесия
- •14.1.3 - Перемещения в деформируемом твердом теле. Тензор деформаций
- •14.1.4 - Уравнения совместности деформаций
- •14.1.5 - Обобщенный закон Гука
- •14.1.7 - Плоская задача теории упругости
- •14.1.8 - Пластическая деформация материала. Простое и сложное нагружение
- •14.1.11 - Ползучесть. Релаксация напряжений. Длительная прочность
- •14.1.12 - Усталостное разрушение элементов конструкций
- •14.1.13 - Малоцикловая усталость. Термическая усталость
- •14.1.14 - Накопление повреждений при нестационарном нагружении
- •14.1.15 - Закономерности развития трещин в элементах конструкций
- •14.1.16 - Свободные колебания системы с одной степенью свободы
- •14.1.17 - Вынужденные колебания системы с одной степенью свободы
- •14.1.18 - Колебания системы с вязким сопротивлением. Демпфирование колебаний
- •14.1.19 - Вынужденные колебания системы с одной степенью свободы под действием произвольной периодической возмущающей силы
- •14.1.21 - Колебания системы с распределенной массой
- •14.2 - Статическая прочность и циклическая долговечность лопаток
- •14.2.1 - Нагрузки, действующие на лопатки. Расчетные схемы лопаток
- •14.2.2 - Напряжения растяжения в профильной части рабочей лопатки от центробежных сил
- •14.2.3 - Изгибающие моменты и напряжения изгиба от газодинамических сил
- •14.2.5 - Суммарные напряжения растяжения и изгиба в профильной части лопатки
- •14.2.6 - Температурные напряжения в лопатках
- •14.2.7 - Особенности напряженного состояния широкохордных рабочих лопаток
- •14.2.9 - Расчет соединения рабочих лопаток с дисками
- •14.2.10 - Расчет на прочность антивибрационных (бандажных) полок и удлинительной ножки лопатки
- •14.2.11 - Особенности расчета на прочность лопаток статора
- •14.2.13 - Анализ трехмерных полей напряжений и деформаций в лопатках
- •14.3 - Статическая прочность и циклическая долговечность дисков
- •14.3.1 - Расчетные схемы дисков
- •14.3.2 - Расчет напряжений в диске в плоской оссесимметричной постановке
- •14.3.3 - Общие закономерности напряженного состояния дисков
- •14.3.7 - Подтверждение циклического ресурса дисков на основе концепции допустимых повреждений
- •14.3.8 - Расчет роторов барабанного типа
- •14.3.9 - Расчет дисков радиальных турбомашин
- •14.3.10 - Оптимальное проектирование дисков. Равнопрочный диск
- •14.4 - Колебания и вибрационная прочность лопаток осевых компрессоров и турбин
- •14.4.2 - Приближенный расчет собственных частот колебаний лопаток
- •14.4.3 - Трехмерные модели колебаний лопаток
- •14.4.4 - Влияние конструктивных и эксплуатационных факторов на собственные частоты колебаний лопатки
- •14.4.6 - Автоколебания лопаток
- •14.4.7 - Демпфирование колебаний лопаток
- •14.4.8 - Вынужденные колебания лопаток. Резонансная диаграмма
- •14.4.9 - Математическое моделирование вынужденных колебаний лопаток
- •14.4.10 - Экспериментальное исследование колебаний лопаток
- •14.4.11 - Коэффициент запаса вибрационной прочности лопаток, пути его повышения
- •14.4.12 - Колебания дисков
- •14.5 - Динамика роторов. Вибрация ГТД
- •14.5.1 - Критическая частота вращения ротора. История вопроса
- •14.5.2 - Динамика одномассового ротора. Поступательные перемещения
- •14.5.3 - Динамика одномассового ротора. Угловые перемещения
- •14.5.4 - Динамика одномассового несимметричного ротора
- •14.5.5 - Ротор с распределенными параметрами
- •14.5.6 - Особенности колебаний системы роторов и корпусов
- •14.5.7 - Демпфирование колебаний роторов
- •14.5.7.1 - Конструкция и принцип действия демпферов колебаний роторов
- •14.5.7.2 - Расчет параметров демпфирования
- •14.5.7.3 - Особенности гидромеханики реальных демпферов
- •14.5.8 - Вибрация ГТД
- •14.5.8.1 - Источники возмущающих сил и спектр вибрации
- •14.5.8.3 - Статистические характеристики вибрации
- •14.5.8.4 - Измерение и нормирование вибрации
- •14.6 - Прочность корпусов и подвески двигателя
- •14.6.1 - Силовая схема корпуса. Условия работы силовых корпусов
- •14.6.4 - Устойчивость корпусных деталей
- •14.6.5 - Расчет корпусов на непробиваемость
- •14.6.6 - Расчет элементов подвески
- •14.8 – Перечень использованной литературы
- •Глава 15 - Шум ГТД
- •15.1 - Источники шума ГТД
- •15.3 - Методы оценки акустических характеристик
- •15.4 - Снижение шума ГТД
- •15.4.1 - Методология проектирования систем шумоглушения
- •15.4.2 - Шумоглушение в выходных устройствах авиационных ГТД
- •15.4.3 - Конструкция звукопоглощающих узлов авиационных ГТД
- •15.4.4 – Глушители шума в наземных ГТУ
- •15.4.5 – Конструкция глушителей шума наземных ГТД
- •15.7 – Список использованной литературы
- •Глава 16 - Газотурбинные двигатели как силовой привод
- •16.1 - ГТД в силовом приводе ГТЭС и ГПА
- •16.2 - ГТД в силовых (энергетических) установках кораблей и судов
- •16.3 - ГТД в силовых установках танков
- •16.5 - Компоновка корабельных и судовых ГГТД
- •16.6 - Компоновка ГТД в силовой установке танка
- •16.8 – Перечень использованной литературы
- •Глава 17 - Автоматизация проектирования и поддержки жизненного цикла ГТД
- •17.1 - Проектирование и информационная поддержка жизненного цикла ГТД (идеология CALS)
- •17.2 - Жизненный цикл изделия. Обзор методов проектирования
- •17.3 - Программные средства проектирования
- •17.4 - Аппаратные средства систем проектирования
- •17.5 - PDM-системы: роль и место в организации проектирования
- •17.6 - Организация производства и ERP-системы
- •17.7 - Параллельный инжиниринг. Интеграция эскизного и технического проектирования
- •17.8 - Переход на безбумажную технологию
- •17.10 - ИПИ-технологии и эксплуатация изделий
- •17.11 - ИПИ-технологии и управление качеством
- •17.12 - Анализ и реинжиниринг бизнес-процессов
- •17.13 - Основы трехмерного проектирования
- •17.13.1 - Общие принципы трехмерного проектирования
- •17.13.1.1 - Способы создания геометрических моделей
- •17.13.1.2 - Основные термины объемной геометрической модели
- •17.13.1.3 - Принцип базового тела
- •17.13.1.4 - Основные термины при проектировании геометрической модели детали
- •17.13.2 - Управляющие структуры
- •17.13.3 - Принцип «Мастер-модели»
- •17.13.5 - Моделирование сборок
- •17.15 - Перечень использованной литературы
- •Глава 18 - Уплотнения в ГТД
- •18.1 - Уплотнение неподвижных соединений
- •18.2 - Уплотнения подвижных соединений
- •18.2.1 - Гидравлический расчет уплотнений подвижных соединений
- •18.3 - Уплотнение газового тракта между ротором и статором ГТД
- •18.3.1 - Лабиринтные уплотнения
- •18.3.2 - Щеточные уплотнения
- •18.3.3 - Скользящие сухие уплотнения газодинамические
- •18.3.4 - Скользящие сухие уплотнения газостатические
- •18.3.5 - Сравнение эффективностей уплотнений газового тракта между ротором и статором ГТД
- •18.4 - Примеры уплотнений газового тракта ГТД
- •18.4.1 - Пример 1
- •18.4.2 - Пример 2. Уплотнение статорной и роторной частей турбины
- •18.5 - Уплотнения масляных полостей опор роторов, редукторов, коробок приводов
- •18.7 - Перечень использованной литературы

Глава 13 - Обвязка авиационных ГТД
13.2.1.5 - Соединительная арматура
Подсоединение трубопровода к штуцерам (фланцам) на агрегатах, датчиках, других трубопроводах может осуществляться непосредственно или через элементы соединительной арматуры, к которым относятся (см. Рис. 13.2.1.5_1) проходники, переходники, угольники, тройники, крестовины и др. детали. За счет применения соединительной арматуры можно унифицировать до 50…70% трубопроводов, что позволяет снизить стоимость и повысить качество их изготовления.
Рисунок 13.2.1.5_1 – Элементы соединительной арматуры а) проходник; б) угольник;
в) тройник; г) крестовина
13.2.1.6 - Узлы крепления
Для снижения статических и динамических нагрузок на трубопроводы осуществляется их крепление к корпусам основных узлов двигателя, к агрегатам или к другим трубопроводам.
Широкое распространение для крепления трубопроводов получили одинарные и парные колодочные хомуты. Одинарный хомут, показанный на Рис. 13.2.1.6_1а, состоит из двух колодок 4 и 6, стяжного винта 2, контровочной шайбы 1 и прокладки 3. При заворачивании винта колодки притягиваются к корпусу 7, зажимая установленный между ними трубопровод 5. Прокладка предотв-
ращает возможное повреждение трубопровода
èизготавливается из меди, алюминиевых сплавов или фторопласта.
Между хомутом и корпусом может устанавливаться кронштейн. Это существенно расширяет возможности узла крепления, так как позволяет использовать его при самых различных положениях трубопровода относительно креп¸жного отверстия на корпусе. Особенно эффективным в этом плане является применение кронштейна со сфери- ческой головкой (см. Рис. 13.2.1.6_1б), относительно которой может разворачиваться хомут при монтаже.
Парный колодочный хомут, представленный на Рис. 13.2.1.6_1в), в основном, используется для крепления одного трубопровода за другой. В отдельных случаях с помощью парных хомутов может обеспечиваться крепление трубопроводов к корпусным деталям. Кроме парных иногда применяются групповые колодочные хомуты для одновременного крепления тр¸х, четыр¸х и большего количества трубопроводов.
Наряду с колодочными применяются хомуты пластинчатого типа. Конструктивно такой узел крепления (см. Рис. 13.2.1.6_1г) содержит собственно хомут 12 в виде металлической пластины, об¸рнутой вокруг трубы 5, стяжной винт 2 и прокладку 3. При затяжке винта происходит плотное охватывание трубы хомутом. Для крепления трубопроводов наружным диаметром более 20 мм хомут 12 может выполняться из двух половин и устанавливается на кронштейн (см. Рис. 13.2.1.6_1д).
Рассмотренные выше узлы крепления не допускают перемещений закрепленного участка трубопровода относительно точки крепления на работающем двигателе. В отличие от этого на Рис. 13.2.1.6_1е показан узел крепления сферотелескопического типа, позволяющий трубопроводу за сч¸т установки с зазором между половинками 15 и 17 хомута-кронштейна и трубой 5 сферического кольца 16 поворачиваться и перемещаться в осевом направлении. Применяются и другие типы узлов крепления, допускающие подвижность трубопроводов.
Для снижения вибронапряжений в трубопроводах могут устанавливаться узлы крепления с упругодемпфирующими прокладками, выполненными из резины или металлорезины (стальная прессованная проволока), или специальные упру- го-демпферные опоры.
Колодочные хомуты изготавливаются из стали, титановых или алюминиевых сплавов; пластин- чатые хомуты – из стали; кронштейны – из стали
èтитановых сплавов.
888
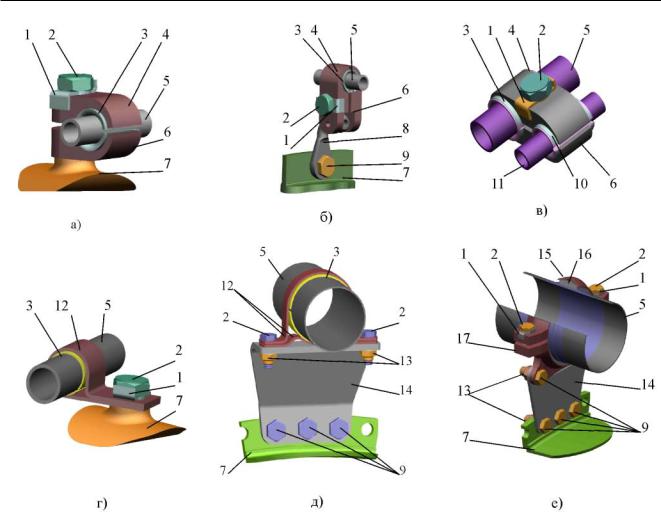
Глава 13 - Обвязка авиационных ГТД
Рисунок 13.2.1.6_1 – Примеры крепления трубопроводов 1 – шайба контровочная; 2 и 9 – винты; 3 и 10 – прокладки; 4 и 6 – колодки; 5 и 11 –
трубопроводы; 7 – корпус; 8 – кронштейн со сферической головкой; 12 - хомут пластинчатый; 13 – гайка самоконтрящаяся; 14 – кронштейн; 15 и 17 – половинки хому- та-кронштейна; 16 – кольцо сферическое
13.2.1.7 - Неисправности трубопроводов
Наиболее часто встречающимися дефектами ТК являются усталостные поломки трубопроводов от воздействия вибраций, вызываемых вращением роторов двигателя, и механические повреждения поверхности труб. Усталостным поломкам подвержены, в основном, трубопроводы малых диаметров (D = 6…12 мм); поломки происходят в местах соединения трубы с концевой арматурой (с ниппелями, фланцами, штуцерами) и местах установки колодочных хомутов. Трещина развивается от поверхности трубы и постепенно распространяется на вс¸ поперечное сечение.
При отсутствии своевременного выявления дефекта происходит полное рассоединение частей
трубопровода. Появлению усталостных поломок способствует наличие высоких статических напряжений в трубопроводах, которые могут быть вызваны некачественным монтажом, нерасчетными тепловыми нагрузками, отклонениями при изготовлении.
Механические повреждения (вмятины, забоины, риски, наклепы, выработки) связаны либо
ñкасанием трубопроводов друг с другом или
ñдругими элементами конструкции двигателя изза недостаточных зазоров, либо являются следствием неосторожного обращения с трубопроводами при монтажно-демонтажных операциях (повреждения от инструмента). Чаще всего требуемый зазор не выдерживается при монтаже трубопровода, однако величина зазора может быть неправильно выбрана и при отработке конструкции ТК. Следствием
889