
- •Содержание
- •Глава 1 - Общие сведения о газотурбинных двигателях
- •1.1 — Введение
- •1.2.1.2 — Турбовинтовые двигатели и вертолетные ГТД
- •1.2.1.3 — Двухконтурные турбореактивные двигатели (ТРДД)
- •1.2.1.4 — Двигатели для самолетов вертикального взлета и посадки
- •1.2.1.5 - Комбинированные двигатели для больших высот и скоростей полета
- •1.2.1.6 - Вспомогательные авиационные ГТД и СУ
- •1.2.2 - Авиационные СУ
- •1.2.3 - История развития авиационных ГТД
- •1.2.3.1 - Россия
- •1.2.3.2 - Германия
- •1.2.3.3 – Англия
- •1.3 - ГТД наземного и морского применения
- •1.3.1 - Области применения наземных и морских ГТД
- •1.3.1.1 -Механический привод промышленного оборудования
- •1.3.1.2 - Привод электрогенераторов
- •1.3.1.3 - Морское применение
- •1.3.2 - Основные типы наземных и морских ГТД
- •1.3.2.1 - Стационарные ГТД
- •1.3.2.2 - Наземные и морские ГТД, конвертированные из авиадвигателей
- •1.3.2.3 - Микротурбины
- •1.4 - Основные мировые производители ГТД
- •1.4.1 - Основные зарубежные производители ГТД
- •1.4.2 - Основные российские производители ГТД
- •1.6 - Перечень использованной литературы
- •Глава 2 - Основные параметры и требования к ГТД
- •2.1 - Основы рабочего процесса ГТД
- •2.1.1 - ГТД как тепловая машина
- •2.1.1.1 – Простой газотурбинный цикл
- •2.1.1.2 - Применение сложных циклов в ГТД
- •2.1.2 - Авиационный ГТД как движитель
- •2.1.3 - Полный к.п.д. и топливная эффективность (экономичность) ГТД
- •2.2 - Параметры ГТД
- •2.2.1 - Основные параметры авиационных ГТД
- •2.2.2 - Основные параметры наземных и морских приводных ГТД
- •2.3 - Требования к авиационным ГТД
- •2.3.1 - Требования к тяге (мощности)
- •2.3.2 – Требования к габаритным и массовым характеристикам
- •2.3.3 - Возможность развития ГТД по тяге (мощности)
- •2.3.4 - Требования к используемым горюче-смазочным материалам
- •2.3.4.1 - Топлива авиационных ГТД
- •2.3.4.2 – Авиационные масла
- •2.3.4.3 - Авиационные гидравлические жидкости
- •2.3.5 – Надежность авиационных ГТД
- •2.3.5.1 – Основные показатели
- •2.3.5.1.1 – Показатели безотказности, непосредственно влияющие на безопасность работы двигателя
- •2.3.5.2 – Методология обеспечения надежности
- •2.3.5.2.1 – Этап проектирования
- •2.3.6 - Ресурс авиационных ГТД
- •2.3.6.1 - Методология обеспечения ресурса
- •2.3.6.2 - Количественные показатели ресурса
- •2.3.7 - Требования производственной технологичности
- •2.3.8 - Требования эксплуатационной технологичности
- •2.3.8.1 - Эксплуатационная технологичность - показатель совершенства ГТД
- •2.3.8.2 - Основные качественные характеристики ЭТ
- •2.3.8.3 - Количественные показатели ЭТ
- •2.3.9 - Экономические требования к авиационным ГТД
- •2.3.9.1 - Себестоимость производства
- •2.3.9.2 - Стоимость ЖЦ двигателя
- •2.3.10 - Экологические требования
- •2.3.10.2 - Ограничения по шуму
- •2.3.12 - Соответствие требованиям летной годности
- •2.4 - Особенности требований к ГТД наземного применения
- •2.4.1 - Особенности требований к приводным ГТД для ГПА
- •2.4.1.1 - Требования к характеристикам ГТД
- •2.4.1.2 - Требования к ресурсам и надежности
- •2.4.1.4 - Используемые ГСМ
- •2.4.1.5 - Требования экологии и безопасности
- •2.4.1.6 - Требования производственной и эксплуатационной технологичности
- •2.4.2 - Особенности требований к ГТД энергетических установок
- •2.4.2.1 - Требования к характеристикам ГТД
- •2.4.2.2 - Используемые ГСМ
- •2.4.2.3 - Требования к ресурсам и надежности
- •2.4.2.4 - Требования к экологии и безопасности
- •2.4.2.5 - Требования к контролепригодности, ремонтопригодности и др.
- •2.5 - Методология проектирования
- •2.5.1 - Основные этапы проектирования ГТД
- •2.5.1.1 - Техническое задание
- •2.5.1.2 – Техническое предложение
- •2.5.1.3 – Эскизный проект
- •2.5.1.4 – Технический проект
- •2.5.1.5 – Разработка конструкторской документации
- •2.5.2 - Разработка конструкций ГТД на основе базовых газогенераторов
- •2.5.2.1 - Газогенератор – базовый узел ГТД
- •2.5.2.2 – Основные параметры и конструктивные схемы газогенераторов ГТД
- •2.5.2.3 – Создание ГТД различного назначения на базе единого газогенератора
- •2.6.1.1 — Общие положения по авиационным ГТД
- •2.6.1.2 — Общие положения по сертификации наземной техники
- •2.6.1.3 — Общие положения по сертификации производства и СМК
- •2.6.1.4 — Органы регулирования деятельности
- •2.6.1.4.1 — Авиационная техника
- •2.6.1.4.2 — Органы регулирования деятельности по сертификации производства и СМК
- •2.6.2.1 — Авиационная техника
- •2.6.2.2 — Наземная техника
- •2.6.2.3 Производство и СМК
- •2.6.2.4 — Принятые сокращения и обозначения
- •2.6.3.1 — Основные этапы создания авиационных ГТД
- •2.6.3.2 — Этапы процесса сертификации авиационных ГТД
- •Глава 3 - Конструктивные схемы ГТД
- •3.1 - Конструктивные схемы авиационных ГТД
- •3.1.1 - Турбореактивные двигатели
- •3.1.2 - Двухконтурные турбореактивные двигатели
- •3.1.3 - Турбовинтовые и вертолетные ГТД
- •3.2 - Конструктивные схемы наземных и морских ГТД
- •3.2.1 - Одновальные ГТД
- •3.2.2 - ГТД со свободной силовой турбиной
- •3.2.3 - ГТД со «связанным» КНД
- •3.2.4 - Конструктивные особенности наземных ГТД различного назначения
- •3.2.5 - Конструктивные особенности ГТД сложных циклов
- •3.4 - Перечень использованной литературы
- •Глава 4 - Силовые схемы ГТД
- •4.1 - Усилия, действующие в ГТД
- •4.1.2 - Крутящие моменты от газовых сил
- •Глава 5 - Компрессоры ГТД
- •6.4.4 - Корпуса КС
- •6.4.4.1 - Наружный корпус КС
- •6.4.4.2 - Внутренний корпус КС
- •6.4.4.3 - Разработка конструкции корпусов
- •6.4.5 - Системы зажигания ГТД
- •6.5 - Экспериментальная доводка КС
- •6.6 - Особенности КС двигателей наземного применения
- •6.7 - Перспективы развития камер сгорания ГТД
- •Глава 7 - Форсажные камеры
- •7.1 - Характеристики ФК
- •7.2 - Работа ФК
- •7.3 - Требования к ФК
- •7.4 - Схемы ФК
- •7.4.2 - Вихревые ФК
- •7.4.3 - ФК с аэродинамической стабилизацией
- •7.5 - Основные элементы ФК
- •7.5.1 - Смеситель
- •7.5.2 - Диффузоры
- •7.5.3 - Фронтовые устройства
- •7.5.4 - Корпусы и экраны
- •7.6 - Управление работой ФК
- •7.6.1 - Розжиг ФК
- •7.6.2 - Управление ФК на режимах приемистости и сброса
- •7.6.3 - Управление ФК на стационарных режимах
- •Глава 8 - Турбины ГТД
- •8.2 - Аэродинамическое проектирование турбины
- •8.2.2 - Технология одномерного проектирования турбины
- •8.2.4 - 2D/3D-моделирование невязкого потока в проточной части турбины
- •8.2.5 - 2D/3D-моделирование вязкого потока в турбине
- •8.2.6 - Синтез геометрии профилей и лопаточных венцов
- •8.2.7 - Одномерное проектирование турбины
- •8.2.7.1 - Выбор количества ступеней ТВД
- •8.2.7.2 - Выбор количества ступеней ТНД
- •8.2.7.3 - Аэродинамическое проектирование и к.п.д. турбины
- •8.2.9 - Методы управления пространственным потоком в турбине
- •8.2.10 - Экспериментальное обеспечение аэродинамического проектирования
- •8.2.11 - Перечень использованной литературы
- •8.3 - Охлаждение деталей турбины
- •8.3.1 - Тепловое состояние элементов турбин
- •8.3.1.1 - Принципы охлаждения
- •8.3.2 - Конвективное, пленочное и пористое охлаждение
- •8.3.3 - Гидравлический расчет систем охлаждения
- •8.3.4 - Методология расчета температур основных деталей турбин
- •8.3.5 - Расчет полей температур в лопатках
- •8.3.6 - Перечень использованной литературы
- •8.4 - Роторы турбин
- •8.4.1 - Конструкции роторов
- •8.4.1.1 - Диски турбин
- •8.4.1.2 - Роторы ТВД
- •8.4.1.3 - Роторы ТНД и СТ
- •8.4.1.4 - Примеры доводки и совершенствования роторов
- •8.4.1.5 - Предотвращение раскрутки и разрушения дисков
- •8.4.2 - Рабочие лопатки турбин
- •8.4.2.1 - Соединение рабочих лопаток с диском
- •8.4.3 - Охлаждение рабочих лопаток
- •8.4.4 - Перечень использованной литературы
- •8.5 - Статоры турбин
- •8.5.1 - Корпусы турбин
- •8.5.2 - Сопловые аппараты
- •8.5.3 - Аппараты закрутки
- •8.5.4 – Перечень использованной литературы
- •8.6 - Радиальные зазоры в турбинах
- •8.6.1 - Влияние радиального зазора на к.п.д. турбины
- •8.6.2 - Изменение радиальных зазоров турбины в работе
- •8.6.3 - Управление радиальными зазорами
- •8.6.4 - Выбор радиального зазора при проектировании
- •8.6.5 - Перечень использованной литературы
- •8.7 - Герметизация проточной части
- •8.7.1 - Герметизация ротора и статора от утечек охлаждающего воздуха
- •8.7.2 - Уплотнения между ротором и статором
- •8.7.3 - Перечень использованной литературы
- •8.8 - Материалы основных деталей турбины
- •8.8.1 - Диски и роторные детали турбины
- •8.8.2 - Сопловые и рабочие лопатки
- •8.8.3 - Покрытия лопаток
- •8.8.4 - Корпусы турбин
- •8.9.1 - Перечень использованной литературы
- •8.10.1 - Прогары и трещины лопаток ТВД
- •8.10.3 - Недостаточный циклический ресурс и поломки роторных деталей
- •8.10.4 - Устранение дефектов турбины в ходе доводки
- •8.11 - Перспективы развития конструкций и методов проектирования турбин
- •8.11.1 - 2D-аэродинамика: эффективные охлаждаемые лопатки ТВД
- •8.11.2 - 2D-аэродинамика: сокращение количества лопаток
- •8.11.3 - Противоположное вращение роторов ТВД и ТНД
- •8.11.4 - 2D-аэродинамика: эффективные решетки профилей ТНД
- •8.11.5 - 3D-аэродинамика: эффективные формы лопаточных венцов
- •8.11.6 - Новые материалы и покрытия для лопаток и дисков
- •8.11.7 - Совершенствование конструкций охлаждаемых лопаток
- •8.11.8 - Оптимизированные системы управления радиальными зазорами
- •8.11.9 - Развитие средств и методов проектирования
- •Глава 9 - Выходные устройства ГТД
- •9.1 - Нерегулируемые сопла
- •9.2 - Выходные устройства ТРДД
- •9.2.1 - Выходные устройства со смешением потоков
- •9.2.2 - Выходные устройства ТРДД с раздельным истечением потоков
- •9.3 - Регулируемые сопла
- •9.3.1 - Осесимметричные регулируемые сопла
- •9.3.1.1 - Регулируемое сопло двигателя Д30-Ф6
- •9.3.2 - Плоские сопла
- •9.4 - Выходные устройства двигателей самолетов укороченного и вертикального взлета-посадки
- •9.5 - «Малозаметные» выходные устройства
- •9.6 - Реверсивные устройства
- •9.6.1 - Реверсивные устройства ковшового типа
- •9.6.2 - Реверсивные устройства створчатого типа
- •9.6.3.1 - Гидравлический привод реверсивного устройства
- •9.6.3.3 - Механический замок фиксации положения реверсивного устройства
- •9.7 - Приводы выходных устройств
- •9.7.1 - Пневмопривод
- •9.7.2 - Пневмомеханический привод
- •9.8 - Выходные устройства диффузорного типа
- •9.8.1 - Конические диффузоры
- •9.8.2 - Осекольцевые диффузоры
- •9.8.3 - Улитки
- •9.8.4 - Соединения с выхлопными шахтами
- •9.8.5 - Выходные устройства вертолетных ГТД
- •9.12 - Перечень использованной литературы
- •Глава 10 - Привод агрегатов, редукторы, муфты ГТД
- •10.1 - Привод агрегатов ГТД
- •10.1.1 - Центральный привод
- •10.1.2 - Коробки приводов агрегатов
- •10.2 - Редукторы ГТД
- •10.2.1 - Редукторы ТВД
- •10.2.1.1 - Общие требования, кинематические схемы
- •10.2.1.2 - Конструкция редукторов ТВД
- •10.2.2 - Редукторы привода несущего и рулевого винтов вертолетов
- •10.2.2.1 - Редукторы привода несущего винта
- •10.2.2.1.1 - Кинематические схемы главных редукторов вертолетов
- •10.2.2.1.2 - Конструкция главных редукторов вертолетов
- •10.2.2.2 - Редукторы хвостовые и промежуточные
- •10.2.3 - Редукторы ГТУ
- •10.2.3.1 - Конструкция редукторов
- •10.3 - Муфты приводов ГТД и ГТУ
- •10.3.1 - Требования к муфтам
- •10.3.2 - Конструкция муфт
- •10.4 - Проектирование приводов агрегатов ГТД
- •10.4.1 - Проектирование центрального привода
- •10.4.1.1 - Конструкция центрального привода
- •10.4.2 - Проектирование коробок приводов агрегатов
- •10.4.2.1 - Конструкция коробки приводов агрегатов
- •10. 5 - Проектирование редукторов
- •10.5.1 - Особенности проектирования редукторов ТВД
- •10.5.2 - Особенности проектирования вертолетных редукторов
- •10.5.3 - Особенности проектирования редукторов ГТУ
- •10.6.1 - Требования к зубчатым передачам
- •10.6.2 - Классификация зубчатых передач
- •10.6.3 - Исходный производящий контур
- •10.6.4 - Нагруженность зубчатых передач
- •10.6.5 - Конструктивные параметры зубчатых передач
- •10.6.5.1 - Конструкции зубчатых колес
- •10.6.6 - Материалы зубчатых колес, способы упрочнения
- •Глава 11 - Пусковые устройства
- •11.1 - Общие сведения
- •11.1.1 - Основные типы пусковых устройств современных ГТД
- •11.1.2 - Технические характеристики пусковых устройств современных ГТД
- •11.2 - Электрические пусковые устройства ГТД
- •11.3 - Воздушные пусковые устройства ГТД
- •11.3.1 - Воздушно - турбинные пусковые устройства ГТД
- •11.3.2 - Регулирующие и отсечные воздушные заслонки
- •11.3.3 - Струйное пусковое устройство ГТД
- •11.4 - Турбокомпрессорные пусковые устройства ГТД
- •11.4.1 - Классификация ТКС ГТД
- •11.4.2 - Принцип действия ТКС
- •11.4.3 - Одновальный ТКС
- •11.4.4 - ТКС со свободной турбиной
- •11.4.5 - Особенности систем ТКС
- •11.5 - Гидравлические пусковые устройства ГТД
- •11.5.1 - Конструкция гидравлических стартеров
- •11.6 - Особенности пусковых устройств ГТД наземного применения
- •11.6.1 - Электрические пусковые устройства
- •11.6.2 - Газовые пусковые устройства
- •11.6.3 - Гидравлические пусковые устройства
- •11.7 - Редукторы пусковых устройств
- •11.8 - Муфты свободного хода пусковых устройств
- •11.8.1 - Муфты свободного хода роликового типа
- •11.8.2 – Муфты свободного хода храпового типа
- •11.9 – Системы смазки пусковых устройств
- •11.11 - Перечень используемой литературы
- •Глава 12 - Системы ГТД
- •12.1.1 - Системы автоматического управления и контроля авиационных ГТД
- •12.1.1.1 - Назначение САУ
- •12.1.1.2 - Состав САУ
- •12.1.1.3 - Основные характеристики САУ
- •12.1.1.5.2 - Порядок разработки САУ
- •12.1.1.5.3 - Основные принципы выбора варианта САУ в процессе проектирования
- •12.1.1.5.4 - Структурное построение САУ
- •12.1.1.5.5 - Программы управления ГТД
- •12.1.1.5.6 - Расчет и анализ показателей надежности
- •12.1.2 - САУ наземных ГТУ
- •12.1.2.1 - Назначение САУ
- •12.1.2.2 - Выбор САУ ГТУ и ее элементов
- •12.1.2.3 - Состав САУ ГТУ
- •12.1.2.4 - Основные характеристики САУ
- •12.1.2.5 - Работа САУ ГТУ
- •12.1.2.6 - Блок управления двигателем (БУД)
- •12.1.2.7 - Особенности системы контроля и диагностики наземных ГТД
- •12.1.4 – Перечень использованной литературы
- •12.2 - Топливные системы ГТД
- •12.2.1 - Топливные системы авиационных ГТД
- •12.2.1.1 - Назначение топливной системы
- •12.2.1.2 - Состав топливной системы
- •12.2.1.3 - Основные характеристики топливной системы
- •12.2.1.4 - Работа топливной системы
- •12.2.1.5 - Выбор топливной системы и ее элементов
- •12.2.1.5.1 – Выбор топливной системы
- •12.2.1.5.2 - Выбор насосов топливной системы
- •12.2.1.5.3 - Определение подогревов топлива в топливной системе
- •12.2.1.5.5 - Математическая модель топливной системы
- •12.2.1.6 - Гидроцилиндры
- •12.2.1.7 - Топливные фильтры
- •12.2.2 - Особенности топливных систем ГТУ
- •12.2.2.1 - Назначение топливной системы
- •12.2.2.2 - Выбор топливной системы и ее элементов
- •12.2.2.3 - Основные характеристики топливной системы
- •12.2.2.4 - Работа топливной системы
- •12.2.4 – Перечень использованной литературы
- •12.3 - Системы диагностики
- •12.3.1 - Общие вопросы диагностирования
- •12.3.1.1 - Задачи диагностирования ГТД
- •12.3.1.3 - Диагностируемые системы ГТД
- •12.3.1.4 - Виды наземного и бортового диагностирования ГТД
- •12.3.1.5 - Структура систем диагностики
- •12.3.1.6 - Регламент диагностирования ГТД
- •12.3.1.7 - Регистрация параметров ГТД
- •12.3.2 - Диагностирование системы механизации ГТД, САУ и ТП ГТД
- •12.3.3 - Диагностирование работы маслосистемы и состояния узлов ГТД, работающих в масле
- •12.3.3.1 - Неисправности маслосистемы и узлов ГТД, работающих в масле
- •12.3.3.2 - Диагностирование по параметрам маслосистемы
- •12.3.3.3 - Контроль содержания в масле частиц износа (трибодиагностика)
- •12.3.4 - Контроль и диагностика по параметрам вибрации ГТД
- •12.3.4.1 - Параметры вибрации и единицы изменения
- •12.3.4.2 - Статистические характеристики вибрации
- •12.3.4.3 - Причины возникновения вибрации в ГТД
- •12.3.4.4 - Датчики измерения вибрации
- •12.3.4.5 - Вибрационная диагностика ГТД
- •12.3.5 - Диагностирование ГТД по газодинамическим параметрам
- •12.3.5.1 - Неисправности проточной части ГТД
- •12.3.5.2 - Требования к перечню контролируемых параметров
- •12.3.5.3 - Алгоритмы диагностирования проточной части ГТД
- •12.3.6 - Обеспечение диагностирования ГТД инструментальными методами
- •12.3.6.1 - Виды неисправностей, выявляемых инструментальными методами
- •12.3.6.2 - Методы и аппаратура инструментальной диагностики
- •12.3.6.2.1 - Оптический осмотр проточной части ГТД
- •12.3.6.2.2 - Ультразвуковой метод диагностирования
- •12.3.6.2.3 - Вихретоковый метод диагностирования
- •12.3.6.2.4 - Капиллярный метод диагностирования с применением портативных аэрозольных наборов
- •12.3.6.2.5 - Диагностирование состояния проточной части ГТД перспективными методами
- •12.3.7 - Особенности диагностирования технического состояния ГТД наземного применения на базе авиационных двигателей
- •12.3.7.1 - Особенности режимов эксплуатации
- •12.3.7.2 - Общие особенности диагностирования наземных ГТД
- •12.3.7.3 - Особенности диагностирования маслосистемы
- •12.3.7.5 - Особенности диагностирования проточной части
- •12.4 - Пусковые системы
- •12.4.1 - Пусковые системы авиационных ГТД
- •12.4.1.1 - Назначение
- •12.4.1.2 - Общие требования
- •12.4.1.3 - Состав пусковых систем
- •12.4.1.4 - Область эксплуатации двигателя, область запуска
- •12.4.1.6 - Надежность запуска
- •12.4.1.7 - Характеристики запуска
- •12.4.1.8. - Выбор типа и параметров стартера
- •12.4.1.9 - Особенности запуска двигателей двухроторных схем
- •12.4.1.10 - Системы зажигания
- •12.4.1.11 - Обеспечение характеристик запуска на разгоне
- •12.4.1.12 - Регулирование компрессора на пусковых режимах
- •12.4.2 - Особенности пусковых систем наземных ГТУ
- •12.4.4 - Перечень использованной литературы
- •12.5 - Воздушные системы ГТД
- •12.5.1 - Функции ВС
- •12.5.2 - Основные требования к ВС
- •12.5.3 - Общие и локальные ВС ГТД
- •12.5.4 - Работа локальных ВС
- •12.5.4.1 - ВС охлаждения турбин ГТД
- •12.5.4.2 - ВС наддува и охлаждения опор
- •12.5.4.2.1 - Работа ВС наддува и охлаждения опор
- •12.5.4.2.2 - Типы ВС наддува и охлаждения опор
- •12.5.4.2.3 - Построение общей схемы ВС наддува и охлаждения опор
- •12.5.4.3 - Противообледенительная система (ПОС)
- •12.5.4.4 - Система кондиционирования воздуха
- •12.5.4.5 - Система активного управления зазорами
- •12.5.4.6 - Системы внешнего охлаждения ГТД
- •12.5.4.7 - Системы внешнего обогрева ГТД
- •12.5.5 - Подготовка воздуха для ВС ГТД
- •12.5.6 - Особенности ВС наземных ГТУ
- •12.5.7 - Агрегаты ВС
- •12.5.9 - Перечень использованной литературы
- •12.6.1 - Общие требования
- •12.6.2 - Схемы маслосистем ГТД
- •12.6.2.1 - Маслосистема с регулируемым давлением масла
- •12.6.2.2 - Маслосистема с нерегулируемым давлением масла
- •12.6.2.3 - Маслосистемы ГТД промышленного применения
- •12.6.3 - Маслосистемы редукторов
- •12.6.3.1 - Маслосистемы авиационных редукторов
- •12.6.3.2 - Маслосистемы редукторов ГТУ
- •12.6.4 - Особенности проектирование маслосистем
- •12.6.5 - Агрегаты маслосистемы
- •12.6.5.1 - Бак масляный
- •12.6.5.2 - Насосы масляные
- •12.6.5.3 - Теплообменники
- •12.6.5.4 - Фильтры и очистители
- •12.6.5.5 - Воздухоотделители и суфлеры
- •12.6.6 - Перспективы развития маслосистем
- •12.6.8 – Перечень использованной литературы
- •12.7 - Гидравлические системы ГТД
- •12.7.1 - Гидросистемы управления реверсивными устройствами
- •12.7.1.1 - Централизованная гидросистема управления реверсивным устройством
- •12.7.1.2 - Автономная гидросистема управления реверсивным устройством
- •12.7.1.3 - Порядок проектирования гидросистем
- •12.7.3 - Перечень использованной литературы
- •12.8 - Дренажные системы
- •12.8.1 - Назначение и классификация систем
- •12.8.2 - Характеристика объектов дренажа
- •12.8.3 - Основные схемы и принцип действия систем
- •12.8.4 - Основные требования к дренажным системам
- •12.8.5 - Обеспечение работоспособности дренажных систем
- •12.8.6 - Особенности конструкции дренажных баков
- •12.8.8 - Перечень использованной литературы
- •Глава 13 - Обвязка авиационных ГТД
- •13.1 - Общая характеристика обвязки
- •13.2 - Конструкция обвязки
- •13.2.1 - Трубопроводные коммуникации
- •13.2.1.1 - Основные сведения
- •13.2.1.2 - Трубы и патрубки
- •13.2.1.3 - Соединения
- •13.2.1.4 - Компенсирующие устройства
- •13.2.1.5 - Соединительная арматура
- •13.2.1.6 - Узлы крепления
- •13.2.1.7 - Неисправности трубопроводов
- •13.2.2 - Электрические коммуникации
- •13.2.2.1 - Общие сведения
- •13.2.2.2 - Конструкция элементов
- •13.2.2.2.1 - Электрические жгуты
- •13.2.2.2.2 - Электрические провода
- •13.2.2.2.3 - Электрические соединители
- •13.2.2.2.4 - Материалы для изготовления электрических жгутов
- •13.2.3 - Узлы крепления агрегатов и датчиков
- •13.2.4 - Механическая проводка управления
- •13.3 - Проектирование обвязки
- •13.3.1 - Требования к обвязке
- •13.3.2 - Основные принципы и порядок проектирования обвязки
- •13.3.3 - Методы отработки конструкции обвязки
- •13.3.3.1 - Натурное макетирование
- •13.3.3.2 - Электронное макетирование обвязки
- •13.3.5 - Проектирование трубопроводных коммуникаций
- •13.3.6 - Проектирование электрических коммуникаций
- •13.3.6.1 - Требования к электрическим коммуникациям
- •13.3.6.2 - Порядок проектирования электрических коммуникаций
- •13.3.6.3 - Разработка электрических схем
- •13.3.6.4 - Разработка монтажных схем
- •13.3.6.5 - Разработка чертежей электрических жгутов
- •13.6 - Перечень использованной литературы
- •Глава 14 - Динамика и прочность ГТД
- •14.1 - Теоретические основы динамики и прочности ГТД
- •14.1.1 - Напряженное состояние, тензор напряжений
- •14.1.2 - Уравнения равновесия
- •14.1.3 - Перемещения в деформируемом твердом теле. Тензор деформаций
- •14.1.4 - Уравнения совместности деформаций
- •14.1.5 - Обобщенный закон Гука
- •14.1.7 - Плоская задача теории упругости
- •14.1.8 - Пластическая деформация материала. Простое и сложное нагружение
- •14.1.11 - Ползучесть. Релаксация напряжений. Длительная прочность
- •14.1.12 - Усталостное разрушение элементов конструкций
- •14.1.13 - Малоцикловая усталость. Термическая усталость
- •14.1.14 - Накопление повреждений при нестационарном нагружении
- •14.1.15 - Закономерности развития трещин в элементах конструкций
- •14.1.16 - Свободные колебания системы с одной степенью свободы
- •14.1.17 - Вынужденные колебания системы с одной степенью свободы
- •14.1.18 - Колебания системы с вязким сопротивлением. Демпфирование колебаний
- •14.1.19 - Вынужденные колебания системы с одной степенью свободы под действием произвольной периодической возмущающей силы
- •14.1.21 - Колебания системы с распределенной массой
- •14.2 - Статическая прочность и циклическая долговечность лопаток
- •14.2.1 - Нагрузки, действующие на лопатки. Расчетные схемы лопаток
- •14.2.2 - Напряжения растяжения в профильной части рабочей лопатки от центробежных сил
- •14.2.3 - Изгибающие моменты и напряжения изгиба от газодинамических сил
- •14.2.5 - Суммарные напряжения растяжения и изгиба в профильной части лопатки
- •14.2.6 - Температурные напряжения в лопатках
- •14.2.7 - Особенности напряженного состояния широкохордных рабочих лопаток
- •14.2.9 - Расчет соединения рабочих лопаток с дисками
- •14.2.10 - Расчет на прочность антивибрационных (бандажных) полок и удлинительной ножки лопатки
- •14.2.11 - Особенности расчета на прочность лопаток статора
- •14.2.13 - Анализ трехмерных полей напряжений и деформаций в лопатках
- •14.3 - Статическая прочность и циклическая долговечность дисков
- •14.3.1 - Расчетные схемы дисков
- •14.3.2 - Расчет напряжений в диске в плоской оссесимметричной постановке
- •14.3.3 - Общие закономерности напряженного состояния дисков
- •14.3.7 - Подтверждение циклического ресурса дисков на основе концепции допустимых повреждений
- •14.3.8 - Расчет роторов барабанного типа
- •14.3.9 - Расчет дисков радиальных турбомашин
- •14.3.10 - Оптимальное проектирование дисков. Равнопрочный диск
- •14.4 - Колебания и вибрационная прочность лопаток осевых компрессоров и турбин
- •14.4.2 - Приближенный расчет собственных частот колебаний лопаток
- •14.4.3 - Трехмерные модели колебаний лопаток
- •14.4.4 - Влияние конструктивных и эксплуатационных факторов на собственные частоты колебаний лопатки
- •14.4.6 - Автоколебания лопаток
- •14.4.7 - Демпфирование колебаний лопаток
- •14.4.8 - Вынужденные колебания лопаток. Резонансная диаграмма
- •14.4.9 - Математическое моделирование вынужденных колебаний лопаток
- •14.4.10 - Экспериментальное исследование колебаний лопаток
- •14.4.11 - Коэффициент запаса вибрационной прочности лопаток, пути его повышения
- •14.4.12 - Колебания дисков
- •14.5 - Динамика роторов. Вибрация ГТД
- •14.5.1 - Критическая частота вращения ротора. История вопроса
- •14.5.2 - Динамика одномассового ротора. Поступательные перемещения
- •14.5.3 - Динамика одномассового ротора. Угловые перемещения
- •14.5.4 - Динамика одномассового несимметричного ротора
- •14.5.5 - Ротор с распределенными параметрами
- •14.5.6 - Особенности колебаний системы роторов и корпусов
- •14.5.7 - Демпфирование колебаний роторов
- •14.5.7.1 - Конструкция и принцип действия демпферов колебаний роторов
- •14.5.7.2 - Расчет параметров демпфирования
- •14.5.7.3 - Особенности гидромеханики реальных демпферов
- •14.5.8 - Вибрация ГТД
- •14.5.8.1 - Источники возмущающих сил и спектр вибрации
- •14.5.8.3 - Статистические характеристики вибрации
- •14.5.8.4 - Измерение и нормирование вибрации
- •14.6 - Прочность корпусов и подвески двигателя
- •14.6.1 - Силовая схема корпуса. Условия работы силовых корпусов
- •14.6.4 - Устойчивость корпусных деталей
- •14.6.5 - Расчет корпусов на непробиваемость
- •14.6.6 - Расчет элементов подвески
- •14.8 – Перечень использованной литературы
- •Глава 15 - Шум ГТД
- •15.1 - Источники шума ГТД
- •15.3 - Методы оценки акустических характеристик
- •15.4 - Снижение шума ГТД
- •15.4.1 - Методология проектирования систем шумоглушения
- •15.4.2 - Шумоглушение в выходных устройствах авиационных ГТД
- •15.4.3 - Конструкция звукопоглощающих узлов авиационных ГТД
- •15.4.4 – Глушители шума в наземных ГТУ
- •15.4.5 – Конструкция глушителей шума наземных ГТД
- •15.7 – Список использованной литературы
- •Глава 16 - Газотурбинные двигатели как силовой привод
- •16.1 - ГТД в силовом приводе ГТЭС и ГПА
- •16.2 - ГТД в силовых (энергетических) установках кораблей и судов
- •16.3 - ГТД в силовых установках танков
- •16.5 - Компоновка корабельных и судовых ГГТД
- •16.6 - Компоновка ГТД в силовой установке танка
- •16.8 – Перечень использованной литературы
- •Глава 17 - Автоматизация проектирования и поддержки жизненного цикла ГТД
- •17.1 - Проектирование и информационная поддержка жизненного цикла ГТД (идеология CALS)
- •17.2 - Жизненный цикл изделия. Обзор методов проектирования
- •17.3 - Программные средства проектирования
- •17.4 - Аппаратные средства систем проектирования
- •17.5 - PDM-системы: роль и место в организации проектирования
- •17.6 - Организация производства и ERP-системы
- •17.7 - Параллельный инжиниринг. Интеграция эскизного и технического проектирования
- •17.8 - Переход на безбумажную технологию
- •17.10 - ИПИ-технологии и эксплуатация изделий
- •17.11 - ИПИ-технологии и управление качеством
- •17.12 - Анализ и реинжиниринг бизнес-процессов
- •17.13 - Основы трехмерного проектирования
- •17.13.1 - Общие принципы трехмерного проектирования
- •17.13.1.1 - Способы создания геометрических моделей
- •17.13.1.2 - Основные термины объемной геометрической модели
- •17.13.1.3 - Принцип базового тела
- •17.13.1.4 - Основные термины при проектировании геометрической модели детали
- •17.13.2 - Управляющие структуры
- •17.13.3 - Принцип «Мастер-модели»
- •17.13.5 - Моделирование сборок
- •17.15 - Перечень использованной литературы
- •Глава 18 - Уплотнения в ГТД
- •18.1 - Уплотнение неподвижных соединений
- •18.2 - Уплотнения подвижных соединений
- •18.2.1 - Гидравлический расчет уплотнений подвижных соединений
- •18.3 - Уплотнение газового тракта между ротором и статором ГТД
- •18.3.1 - Лабиринтные уплотнения
- •18.3.2 - Щеточные уплотнения
- •18.3.3 - Скользящие сухие уплотнения газодинамические
- •18.3.4 - Скользящие сухие уплотнения газостатические
- •18.3.5 - Сравнение эффективностей уплотнений газового тракта между ротором и статором ГТД
- •18.4 - Примеры уплотнений газового тракта ГТД
- •18.4.1 - Пример 1
- •18.4.2 - Пример 2. Уплотнение статорной и роторной частей турбины
- •18.5 - Уплотнения масляных полостей опор роторов, редукторов, коробок приводов
- •18.7 - Перечень использованной литературы

Глава 14 - Динамика и прочность ГТД
мента M, изменяется по высоте сечения стержня линейно:
(14.1.10-7)
ãäå I – момент инерции сечения стержня. Остаточное напряжение определяется как раз-
ность напряжения, определяемого соотношением (14.1.10-2) и напряжения разгрузки:
σîñò(y) = σ(y) - σразгр(y). |
(14.1.10-8) |
Поле остаточных напряжений показано на Рис. 14.1.10_1в. Видно, что на верхней поверхности, в волокнах которой под нагрузкой возникает растягивающее напряжение, остаточное напряжение - сжимающее и составляет:
σ |
îñò |
(h/2) = σ |
ò |
– 6M/bh2. |
(14.1.10-9) |
|
|
|
|
На нижней поверхности остаточное напряжение имеет такую же величину, но противоположный знак. Из Рис. 14.1.10_1в видно, что поле остаточных напряжений - самоуравновешенное: сумма проекций всех напряжений на ось x равна нулю. Кроме остаточных напряжений в стержне возникают остаточные деформации и перемещения (прогиб). В рассматриваемой задаче остаточный прогиб направлен вниз, что и определяет знаки остаточных напряжений – сжатия в верхних волокнах и растяжения – в нижних.
При последующем нагружении остаточные напряжения складываются с напряжениями от новой нагрузки. Результирующие напряжения могут оказаться больше или меньше, чем в конструкции, не подвергавшейся пластической деформации. Поле остаточных напряжений с этой точки зрения может быть благоприятным или неблагоприятным. В первом случае говорят о приспособляемости конструкции и ее упрочнении (автофретировании) путем предварительной деформации. В частности, благоприятные поля остаточных напряжений возникают при предварительной пластической деформации дисков ГТД.
14.1.11 - Ползучесть. Релаксация напряжений. Длительная прочность
Напряжения и деформации, возникшие при нагружении деталей, изменяются во времени, даже если нагрузки остаются постоянными. Это явление называется ползучестью материала. Одна сторона этого явления — изменение во времени де-
формаций — называется собственно ползучестью или последействием, а вторая — изменение напряжений — релаксацией. Ползучесть может приводить к недопустимому увеличению необратимой деформации детали или конструкции, и ее разрушению при напряжениях ниже предела прочности. Примером негативного проявления ползучести может служить постепенное необратимое удлинение лопаток ротора газовой турбины, которое может привести к задеванию лопаток о статор и заклиниванию ротора.
Задачами расчета конструкций на ползучесть являются определение деформаций, накапливаемых в конструкции во время работы, и определение времени до разрушения детали.
На Рис. 14.1.11_1 проиллюстрирован процесс ползучести, происходящий при одноосном растяжении стержня под действием постоянного во времени напряжения.
Деформация, возникшая мгновенно при приложении нагрузки (отрезок ОА на Рис. 14.1.11_1) - упругая: она равна σ/E. С течением времени при постоянной нагрузке появляется и постепенно увеличивается пластическая деформация – деформация ползучести (кривая А-A3). При этом наблюдаются три характерных участка. На первом (A-A1) деформация растет относительно быстро, затем замедляется и на участке A1-A2 растет с постоянной скоростью. Участок A1-A2 называют участком установившейся ползучести. На третьем участке (A2-A3) скорость деформации снова возрастает, и в точке A3 происходит разрушение.
Рисунок 14.1.11_1 - Ползучесть при постоянном напряжении и в цикле нагрузкаразгрузка
937

Глава 14 - Динамика и прочность ГТД
Рассмотренную зависимость деформации от времени при постоянном напряжении называют кривой ползучести. Семейство кривых ползучести, полученных при разных напряжениях и температурах, является основной характеристикой ползучести материала и определяется экспериментально.
Если в момент времени, соответствующий точке B, снять нагрузку, происходит уменьшение деформации. Сначала деформация скачкообразно уменьшается на величину упругой деформации (участок ВС), а в дальнейшем падает постепенно (кривая CD). Это явление называется обратным последействием или обратной ползучестью.
Ползучесть проявляется при напряжениях, меньших предела текучести материала. Кривые ползучести при постоянном напряжении для больших значений напряжений располагаются выше, что соответствует более высокой скорости деформации ползучести и меньшему времени до разрушения t3 < t2 < t1 (ñì. Ðèñ. 14.1.11_2à).
Существенное влияние на процессы ползуче- сти оказывает температура. В металлах ползучесть проявляется при высоких температурах, начиная приблизительно с 35% абсолютной температуры плавления. В полимерных материалах ползучесть проявляется при комнатной температуре. Скорость ползучести всех материалов при более высоких температурах выше, а время до разрушения меньше, чем при более низких температурах (см. Рис. 14.1.11_2б).
Одно из важных в практическом отношении проявлений ползучести - релаксация напряжений. Она проявляется в ситуации, когда тело нагружено и зафиксировано таким образом, что суммарная деформация его не может изменяться. Например, растянутый и закрепленный в растянутом положении образец. Другой пример – растянутый при затяжке болт, соединяющий две детали. Полная деформация, не изменяющаяся во времени, представляет собой сумму упругой деформации εe и пластической деформации ползучести εc (индекс с – начальная буква английского «creep» -ползучесть):
ε = εe+ εc = const |
(14.1.11-1) |
В момент нагружения t = 0 деформации ползучести еще нет, суммарная деформация равна упругой. Напряжение определяется из закона Гука: σ(0) = Eσ(0). Подставляя в (14.1.11_1) получаем:
(14.1.11-2)
Рисунок 14.1.11_2 - Кривые ползучести а) при различных напряжениях
σ1<σ2<σ3; б) при различных - температурах T1<T2<T3
Из (14.1.11-2) следует, что при увеличении пластической деформации с течением времени напряжение будет постепенно уменьшаться (см. Рис. 14.1.11_3). Релаксация напряжений может иметь негативные последствия, выражающиеся, например, в ослаблении затяжки болтовых соединений.
Релаксация проявляется также в постепенном снижении напряжений и увеличении пластических деформаций в зонах концентрации напряжений.
Одним из негативных проявлений релаксации является постепенное снижение остаточных напряжений, созданных в конструкции с целью ее упроч- нения.
Таким образом, ползучесть проявляется в том, что напряжения и деформации в теле при заданной нагрузке зависят не только от пространственных координат, но и от времени.
Важной характеристикой сопротивления материала ползучести является предел ползучести.
Рисунок 14.1.11_3 - Релаксация напряжений
938
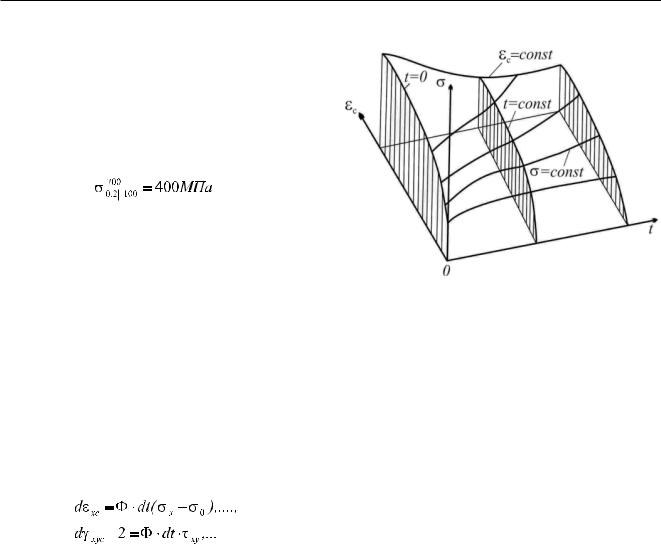
Глава 14 - Динамика и прочность ГТД
Так называется напряжение, при котором пласти- ческая деформация за заданный промежуток времени достигает заданной величины. При обозна- чении предела ползучести указывают величину деформации, время и температуру. Например, для жаропрочного никелевого сплава ХН77ТЮР для предельной деформации 0.2% при температуре 7000С и времени 100 часов предел ползучести
Математические модели ползучести опираются, обычно, на следующие согласующиеся с экспериментальными данными положения.
Деформацию, вызываемую действующей нагрузкой и нагревом, представляют как сумму деформаций упругости, пластичности, ползучести и теплового расширения. Аналогичным образом представляют приращение полной деформации:
dε= dεe+dεp+dεc+αt |
(14.1.11-3) |
В трехмерном напряженно-деформированном состоянии приращение отдельных компонент деформаций ползучести принимается в виде:
(14.1.11-4)
ãäå t - время;
Ô - функция ползучести, определяемая на основании экспериментальных данных;
σ0 - среднее напряжение (σ0 = (σx+σy+σz )/3).
Существует несколько гипотез (иногда их называют теориями) ползучести, различающихся видом этой функции. В теории течения принимают Ô = Ô (σi, T, t ) в теории упрочнения Ô = Ô( σi , T , εi*c) , (здесь σi –интенсивность напряжений, εi*c- интенсивность накопленной деформации ползучести).
Остановимся подробнее на теории старения. Согласно этой теории предполагается, что при заданной температуре между напряжением, деформацией и временем существует постоянная зависимость Ô(σ, ε, t) = 0 . Для сложного напряженного состояния вместо напряжений и деформаций в этой зависимости записываются их интенсивности.
Эта зависимость представляет собой поверхность в координатах σ, ε, t (14.1.5-5). Данные для ее построения определяются из семейства кривых ползучести при разных напряжениях и температу-
Рисунок 14.1.11_4 - Поверхность Ф(σ, ε, τ) = 0 в теории старения
рах (см. Рис. 14.1.11_2). Рассекая ее плоскостью σ = const, получаем кривые ползучести, ε = const - кривые релаксации, t = const – изохронные (при одинаковом времени) кривые деформации.
Для момента t = 0 изохронная кривая представляет собой диаграмму σ - ε, получаемую при обычных кратковременных испытаниях. Для последующих моментов кривая проходит ниже (см. Рис. 14.1.11_4), что можно интерпретировать как постепенное снижение сопротивления материала деформации (отсюда название «старение»). Когда изохронные кривые найдены, задача сводится к рас- чету деформаций в упруго-пластическом теле по деформационной теории.
Модели ползучести, основанные на теории старения, позволяют описывать процессы ползу- чести при постоянном напряжении, монотонном нагружении, релаксацию. Один из основных недостатков теории старения состоит в том, что не учи- тывается история нагружения. От этого недостатка свободны теории течения и упрочнения, несколько более сложные в реализации. Более подробные сведения о них можно найти в специальной литературе (см., например [14.8.25]).
Эффект ползучести, как отмечалось выше, проявляется при напряжениях, ниже предела теку- чести материала, и при таких напряжениях может приводить к разрушению конструкции. В отличие от обычных кратковременных испытаний на растяжение, ползучесть приводит к разрушению не сразу, а по прошествии некоторого, возможно длительного, периода времени. Прочность материала при высоких температурах характеризуется пределом длительной прочности.
939

Глава 14 - Динамика и прочность ГТД
Пределом длительной прочности называется напряжение, при котором материал разрушается при постоянной нагрузке не ранее заданного времени. Предел длительной прочности не следует путать с пределом ползучести.
При обозначении предела длительной прочности указываются температура и время. Например, для жаропрочного никелевого сплава ХН77ТЮР при температуре 7000С и времени 100 часов предел длительной прочности (для сравнения – предел ползучести при той же температуре и времени несколько выше
; при той же температуре при кратковременных испытаниях предел прочности σb = 830 ÌÏà).
Зависимость предела длительной прочности от времени (см. Рис. 14.1.11_5) представляют в виде степенной зависимости:
, откуда
(14.1.11-5)
ãäå C è m – экспериментально определяемые характеристики материала, зависящие от температуры.
Показатель степени m для различных материалов лежит в пределах 4…20, поэтому даже незначительное изменение напряжения приводит к существенному изменению долговечности. С увеличением температуры предел длительной прочности заметно снижается (см. Рис. 14.1.11_5).
При обеспечении прочности авиационной техники принято оперировать коэффициентами запаса прочности. При постоянном по во времени напряжении σ и времени нагружения t определяют запасы прочности по напряжениям nσ и по долговечности nt, равные, соответственно:
(14.1.11-6)
Пользуясь соотношением (14.1.11-5), связывающим долговечность с напряжением можно получить связь между этими коэффициентами запаса:
(14.1.11-7)
Учитывая, что для конструкционных материалов m = 4…20, оказывается, что запас по долговечности должен быть во много раз больше, чем по напряжениям, так, например, пятикратный запас по долговечности соответствует при m = 4 небольшому запасу по напряжениям nσ = 1,5.
Рисунок 14.1.11_5 - Зависимость предела длительной прочности от времени
èтемпературы. T1 < T2 < T3
14.1.12- Усталостное разрушение элементов конструкций
Усталостные поломки составляют основной вид разрушения элементов машиностроительных конструкций, в частности, авиационных двигателей. Нередко усталостное разрушение приводит
êопасным последствиям. Особенность усталостного разрушения состоит в том, что оно может иметь длительный инкубационный период, составляющий иногда годы эксплуатации изделия, в те- чение которого диагностирование признаков приближающегося разрушения затруднительно. Кроме того, механизмы усталостного разрушения для разных материалов и условий многообразны и чувствительны к множеству случайных факторов, что затрудняет расчеты, требует проведения большого объема экспериментальных работ.
При циклическом нагружении закономерности процесса накопления повреждений зависят главным образом от величины возникающих переменных напряжений и числа циклов их изменения.
Напряжения, связанные с вибрацией деталей, имеют сравнительно небольшую амплитуду (зна- чительно ниже предела текучести), но количество циклов нагружения за время эксплуатации достигает миллиардов. Эти напряжения могут приводить
êусталостному разрушению - многоцикловой усталости. Характерная особенность такого разрушения - отсутствие макроскопических пластических деформаций в материале. Многоцикловая усталость - определяющий процесс разрушения для многих деталей ГТД (лопатки компрессора, корпуса, валы, шестерни).
940

Глава 14 - Динамика и прочность ГТД
Изменение режима работы изделия во время эксплуатации приводит к изменению статических напряжений в деталях, при длительной эксплуатации количество циклов изменения напряжений доходит до десятков тысяч, а амплитуда может превышать предел текучести. Накопление повреждений при действии таких напряжений может привести к разрушению от малоцикловой усталости (МЦУ), отличающейся от многоцикловой усталости появлением макроскопических пластических деформаций материала в каждом цикле нагружения. Накопление повреждений при МЦУ часто определяет ресурс работы деталей, работающих при повышенных температурах, например, дисков, рабочих и сопловых лопаток турбины, элементов камер сгорания ГТД. Процессы разрушения при МЦУ рассмотрены в следующем разделе, здесь мы остановимся на закономерностях многоцикловой усталости.
Процесс усталостного разрушения принято делить на две стадии. На первой под действием переменных напряжений происходят необратимые изменения в структуре металла, связанные с перемещением микродефектов вследствие локальной концентрации напряжений на случайных неоднородностях исходной структуры материала. При слиянии микродефектов образуются микротрещины, объединяющиеся при дальнейшем циклическом нагружении в макроскопическую магистральную трещину, размеры которой соизмеримы с размерами зерна и составляют десятые доли миллиметра. На второй стадии процесса усталостного разрушения происходит рост макроскопической трещины, заканчивающийся окончательным разрушением детали. Процессы, связанные с развитием макроскопических трещин, рассмотрены ниже в разделе 14.1.15.
Упрощенно переменные напряжения представляют изменяющимися во времени по простому синусоидальному циклу, который характеризуется максимальным σmax и минимальным σmin значениями, а также частотой f = 1/tö (см. Рис. 14.1.12_1). Чаще для характеристики переменных напряжений используют амплитуду σa, среднее напряжение σm и коэффициент асимметрии цикла R:
σà = 0,5(σmax - σmin);
σm = 0,5(σmax + σmin); (14.1.12-1)
R = σmax / σmin.
Если среднее напряжение цикла нулевое σm = 0, цикл называют симметричным, для него
R = -1. Öèêë ñ σmin = 0 è R = 0 называют пульсирующим.
Рисунок 14.1.12_1 - Характеристики цикла переменных напряжений
Для определения характеристик усталостной прочности материалов проводят специальные испытания. Образцы нагружают переменным напряжением с заданными амплитудой и коэффициентом асимметрии и определяют количество циклов до разрушения NÐ. Если образец не сломался до некоторого базового числа циклов NÁ (обычно это 20 или 100 миллионов циклов), испытание прекращают. Количество циклов до разрушения одинаковых образцов при одном и том же напряжении может различаться в несколько раз, или даже в десятки раз.
По результатам испытаний серии образцов строят график зависимости числа циклов от амплитуды (см. Рис. 14.1.12_2). В логарифмических координатах он состоит из двух прямолинейных участков. Точка перелома соответствует значению N0, примерно равному 107 циклов.
Некоторые материалы имеют физический предел выносливости (предел усталости), под которым подразумевается максимальное напряжение, не вызывающее разрушения детали при любом количе- стве циклов нагружения. В этом случае правая ветвь кривой усталости параллельна оси N. Для симметричного цикла с R = -1 предел выносливости обозначают σ-1. Цветные металлы и сплавы физического предела выносливости не имеют, и правая ветвь кривой усталости не горизонтальна, но имеет меньший наклон, чем левая. В этом случае под σ-1 подразумевают условный предел выносливости при базе NÁ.
В логарифмических координатах левую ветвь кривой усталости обычно аппроксимируют прямой:
σmN = C, |
(14.1.12-2) |
Ð |
|
ãäå m è C - характеристики материала; обычно m = 4…12.
941
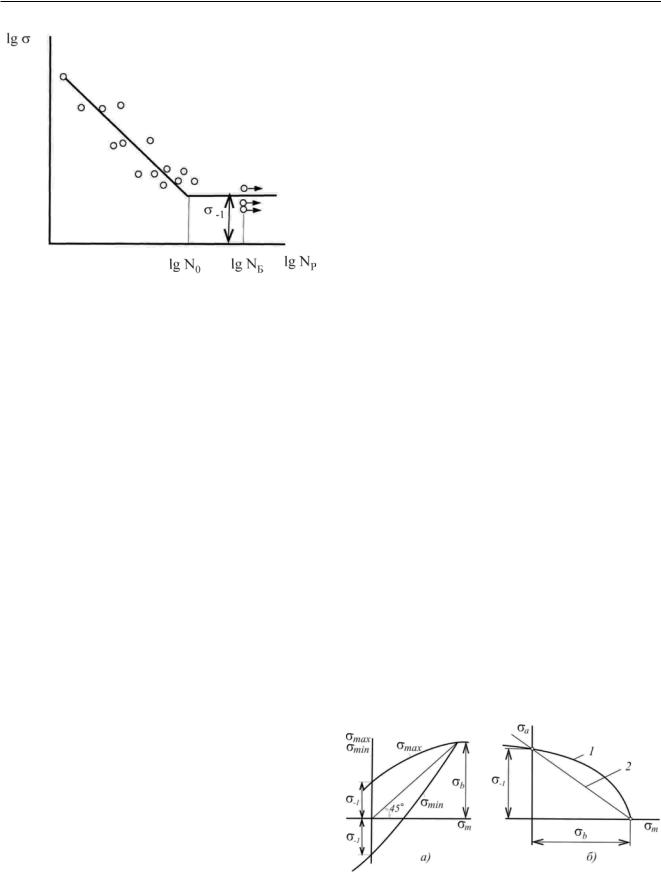
Глава 14 - Динамика и прочность ГТД
Рисунок 14.1.12_2 - Кривые усталости по результатам испытаний
Для обеспечения усталостной прочности детали необходимо, чтобы рабочая амплитуда вибронапряжений σa была ниже предела выносливости σa < σ-1. Предел выносливости весьма чувствителен к влиянию конструктивных, технологических и эксплуатационных факторов. В реальных деталях он существенно ниже значения, получаемого при испытаниях образцов.
Наличие в детали концентраторов напряжений существенно снижает ее усталостную проч- ность. Для оценки этого снижения используют эффективный коэффициент концентрации, равный отношению предела усталости гладкого образца σ-1 к пределу усталости σ-1k образца с концентратором:
kσ = σ-1 / σ-1k |
(14.1.12-3) |
Как показывают результаты испытаний, этот коэффициент заметно ниже теоретического (полу- чаемого из решения задачи теории упругости) коэффициента концентрации ασ :
kσ = 1+q(ασ - 1), |
(14.1.12-4) |
ãäå q – коэффициент чувствительности к концентрации напряжений.
Для хрупких материалов он близок к единице и эффективный коэффициент концентрации близок к теоретическому, для пластичных материалов q < 1. Для литых материалов q = 0,1…0,2, для малоуглеродистых сталей и жаропрочных никелевых сплавов q = 0,2…0,4, для титановых сплавов q = 0,8…0,9.
Весьма существенно влияние на предел выносливости состояния поверхностного слоя детали, характеризующегося чистотой поверхности, наклепом, остаточными напряжениями. Отношение предела выносливости стандартного образца σ-1 с эталонным поверхностным слоем (обычно образцы полируют) к пределу выносливости образца σ-1Ï с такими же характеристиками поверхностного слоя, как у детали:
β = σ-1 / σ-1Ï |
(14.1.12-4) |
отражает влияние технологических факторов на усталостную прочность. Он может быть представлен произведением коэффициентов, отражающих влияние отдельных факторов: чистоты поверхности, поверхностного упрочнения, коррозии.
Известно, что предел выносливости крупных деталей ниже, чем у стандартных образцов. Этот масштабный эффект связан с большей вероятностью наличия микроскопических дефектов материала в большем объеме. Коэффициент масштабного фактора:
εd = σ-1 / σ-1d , |
(14.1.12-5) |
ãäå σ-1d - предел выносливости образца с диаметром d.
Предел выносливости при наличии среднего растягивающего напряжения цикла заметно снижается по сравнению со случаем симметричного нагружения. Влияние асимметрии цикла определяют экспериментально, проводя специальные испытания образцов при несимметричном цикле нагружения. Результаты этих экспериментов можно представить в виде диаграммы предельных напряжений (см. Рис. 14.1.12_3а) или в виде диаграммы предельных амплитуд (см. Рис. 14.1.12_3б). На первой приводятся максимальное и минимальное
Рисунок 14.1.12_3 - Влияние среднего напряжения цикла на характеристики усталостной прочности. Диаграммы предельных напряжений
(а) и предельных амплитуд (б)
942
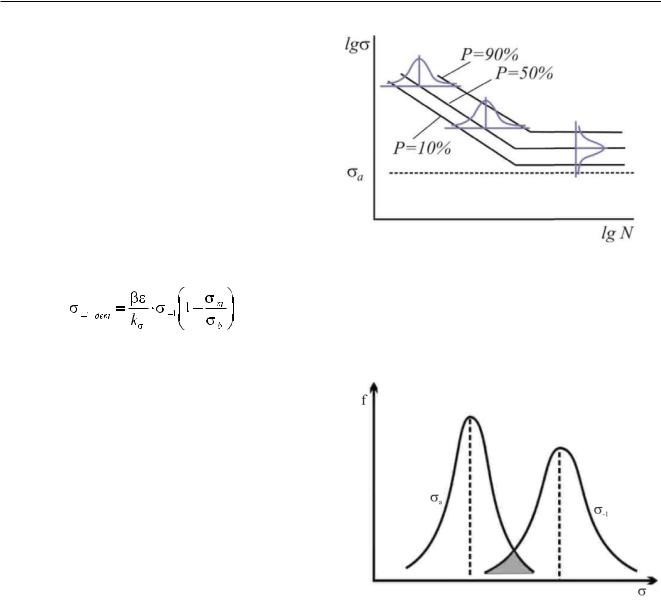
Глава 14 - Динамика и прочность ГТД
напряжения цикла в зависимости от среднего, на второй – амплитуда. Диаграмму предельных амплитуд часто аппроксимируют линейной зависимостью (кривая 2):
σa = σ-1 - ψσm ,
(14.1.12-6)
ψ = σ-1 / σb
ãäå ψ - коэффициент влияния асимметрии цикла; σb - предел прочности материала.
Для материала реальной детали предел выносливости σ-1äåò с учетом перечисленных факторов равен:
(14.1.12-7)
Коэффициент запаса усталостной прочности вводится как отношение предела выносливости с учетом влияния конструктивных, технологических и эксплуатационных факторов (8) к амплитуде переменных напряжений, возникающих в детали во время работы:
Kν = σ-1äåò / σa. |
(14.1.12-8) |
Следует отметить, что расчет коэффициента запаса по соотношениям (14.1.12-7), (14.1.12-8) с использованием справочных данных о значениях предела выносливости стандартных образцов при симметричном цикле нагружения может привести к значительным погрешностям. В соотношении (14.1.12-7) учтены не все факторы, влияющие на предел выносливости: рабочая температура, форма цикла напряжений, частота нагружения и т.д. Данные о влиянии этих факторов приведены в многочисленных литературных источниках (см., например [14.8.14]). Поправочные коэффициенты, входящие в (14.1.12-7), сами зависят от марки материала, термообработки, температуры и других факторов. Для правильной оценки предела выносливости эти коэффициенты (а не только предел выносливости при симметричном цикле) необходимо определять на образцах, имеющих тот же химический состав, структуру, что и натурная деталь, при рабочей температуре. Для того, чтобы учесть влияние конструктивных и технологических факторов, в ряде случаев при проведении испытаний в качестве образцов используют натурные детали и проводят испытания в условиях, максимально приближенных к эксплуатационным. В ча-
Рисунок 14.1.12_4 - Кривые усталости для различ- ных значений вероятности разрушения
Рисунок 14.1.12_5 - Рассеяние переменных напряжений и предела выносливости
стности, именно так определяют пределы выносливости лопаток компрессоров и турбин ГТД.
Как отмечалось, результаты усталостных испытаний имеют значительное рассеяние. Поэтому число циклов до разрушения при заданном напряжении и предел выносливости являются величинами случайными и должны характеризоваться не только средним значением, но и законом распределения. Если провести испытания большого количе- ства образцов так, чтобы на каждом уровне напряжений было испытано их несколько десятков, можно получить кривые усталости для разных зна- чений вероятности разрушения (см. Рис. 14.1.12_4). Такие кривые позволяют статистически обосновать нормативное значение запаса усталостной прочно-
943