
- •Содержание
- •Глава 1 - Общие сведения о газотурбинных двигателях
- •1.1 — Введение
- •1.2.1.2 — Турбовинтовые двигатели и вертолетные ГТД
- •1.2.1.3 — Двухконтурные турбореактивные двигатели (ТРДД)
- •1.2.1.4 — Двигатели для самолетов вертикального взлета и посадки
- •1.2.1.5 - Комбинированные двигатели для больших высот и скоростей полета
- •1.2.1.6 - Вспомогательные авиационные ГТД и СУ
- •1.2.2 - Авиационные СУ
- •1.2.3 - История развития авиационных ГТД
- •1.2.3.1 - Россия
- •1.2.3.2 - Германия
- •1.2.3.3 – Англия
- •1.3 - ГТД наземного и морского применения
- •1.3.1 - Области применения наземных и морских ГТД
- •1.3.1.1 -Механический привод промышленного оборудования
- •1.3.1.2 - Привод электрогенераторов
- •1.3.1.3 - Морское применение
- •1.3.2 - Основные типы наземных и морских ГТД
- •1.3.2.1 - Стационарные ГТД
- •1.3.2.2 - Наземные и морские ГТД, конвертированные из авиадвигателей
- •1.3.2.3 - Микротурбины
- •1.4 - Основные мировые производители ГТД
- •1.4.1 - Основные зарубежные производители ГТД
- •1.4.2 - Основные российские производители ГТД
- •1.6 - Перечень использованной литературы
- •Глава 2 - Основные параметры и требования к ГТД
- •2.1 - Основы рабочего процесса ГТД
- •2.1.1 - ГТД как тепловая машина
- •2.1.1.1 – Простой газотурбинный цикл
- •2.1.1.2 - Применение сложных циклов в ГТД
- •2.1.2 - Авиационный ГТД как движитель
- •2.1.3 - Полный к.п.д. и топливная эффективность (экономичность) ГТД
- •2.2 - Параметры ГТД
- •2.2.1 - Основные параметры авиационных ГТД
- •2.2.2 - Основные параметры наземных и морских приводных ГТД
- •2.3 - Требования к авиационным ГТД
- •2.3.1 - Требования к тяге (мощности)
- •2.3.2 – Требования к габаритным и массовым характеристикам
- •2.3.3 - Возможность развития ГТД по тяге (мощности)
- •2.3.4 - Требования к используемым горюче-смазочным материалам
- •2.3.4.1 - Топлива авиационных ГТД
- •2.3.4.2 – Авиационные масла
- •2.3.4.3 - Авиационные гидравлические жидкости
- •2.3.5 – Надежность авиационных ГТД
- •2.3.5.1 – Основные показатели
- •2.3.5.1.1 – Показатели безотказности, непосредственно влияющие на безопасность работы двигателя
- •2.3.5.2 – Методология обеспечения надежности
- •2.3.5.2.1 – Этап проектирования
- •2.3.6 - Ресурс авиационных ГТД
- •2.3.6.1 - Методология обеспечения ресурса
- •2.3.6.2 - Количественные показатели ресурса
- •2.3.7 - Требования производственной технологичности
- •2.3.8 - Требования эксплуатационной технологичности
- •2.3.8.1 - Эксплуатационная технологичность - показатель совершенства ГТД
- •2.3.8.2 - Основные качественные характеристики ЭТ
- •2.3.8.3 - Количественные показатели ЭТ
- •2.3.9 - Экономические требования к авиационным ГТД
- •2.3.9.1 - Себестоимость производства
- •2.3.9.2 - Стоимость ЖЦ двигателя
- •2.3.10 - Экологические требования
- •2.3.10.2 - Ограничения по шуму
- •2.3.12 - Соответствие требованиям летной годности
- •2.4 - Особенности требований к ГТД наземного применения
- •2.4.1 - Особенности требований к приводным ГТД для ГПА
- •2.4.1.1 - Требования к характеристикам ГТД
- •2.4.1.2 - Требования к ресурсам и надежности
- •2.4.1.4 - Используемые ГСМ
- •2.4.1.5 - Требования экологии и безопасности
- •2.4.1.6 - Требования производственной и эксплуатационной технологичности
- •2.4.2 - Особенности требований к ГТД энергетических установок
- •2.4.2.1 - Требования к характеристикам ГТД
- •2.4.2.2 - Используемые ГСМ
- •2.4.2.3 - Требования к ресурсам и надежности
- •2.4.2.4 - Требования к экологии и безопасности
- •2.4.2.5 - Требования к контролепригодности, ремонтопригодности и др.
- •2.5 - Методология проектирования
- •2.5.1 - Основные этапы проектирования ГТД
- •2.5.1.1 - Техническое задание
- •2.5.1.2 – Техническое предложение
- •2.5.1.3 – Эскизный проект
- •2.5.1.4 – Технический проект
- •2.5.1.5 – Разработка конструкторской документации
- •2.5.2 - Разработка конструкций ГТД на основе базовых газогенераторов
- •2.5.2.1 - Газогенератор – базовый узел ГТД
- •2.5.2.2 – Основные параметры и конструктивные схемы газогенераторов ГТД
- •2.5.2.3 – Создание ГТД различного назначения на базе единого газогенератора
- •2.6.1.1 — Общие положения по авиационным ГТД
- •2.6.1.2 — Общие положения по сертификации наземной техники
- •2.6.1.3 — Общие положения по сертификации производства и СМК
- •2.6.1.4 — Органы регулирования деятельности
- •2.6.1.4.1 — Авиационная техника
- •2.6.1.4.2 — Органы регулирования деятельности по сертификации производства и СМК
- •2.6.2.1 — Авиационная техника
- •2.6.2.2 — Наземная техника
- •2.6.2.3 Производство и СМК
- •2.6.2.4 — Принятые сокращения и обозначения
- •2.6.3.1 — Основные этапы создания авиационных ГТД
- •2.6.3.2 — Этапы процесса сертификации авиационных ГТД
- •Глава 3 - Конструктивные схемы ГТД
- •3.1 - Конструктивные схемы авиационных ГТД
- •3.1.1 - Турбореактивные двигатели
- •3.1.2 - Двухконтурные турбореактивные двигатели
- •3.1.3 - Турбовинтовые и вертолетные ГТД
- •3.2 - Конструктивные схемы наземных и морских ГТД
- •3.2.1 - Одновальные ГТД
- •3.2.2 - ГТД со свободной силовой турбиной
- •3.2.3 - ГТД со «связанным» КНД
- •3.2.4 - Конструктивные особенности наземных ГТД различного назначения
- •3.2.5 - Конструктивные особенности ГТД сложных циклов
- •3.4 - Перечень использованной литературы
- •Глава 4 - Силовые схемы ГТД
- •4.1 - Усилия, действующие в ГТД
- •4.1.2 - Крутящие моменты от газовых сил
- •Глава 5 - Компрессоры ГТД
- •6.4.4 - Корпуса КС
- •6.4.4.1 - Наружный корпус КС
- •6.4.4.2 - Внутренний корпус КС
- •6.4.4.3 - Разработка конструкции корпусов
- •6.4.5 - Системы зажигания ГТД
- •6.5 - Экспериментальная доводка КС
- •6.6 - Особенности КС двигателей наземного применения
- •6.7 - Перспективы развития камер сгорания ГТД
- •Глава 7 - Форсажные камеры
- •7.1 - Характеристики ФК
- •7.2 - Работа ФК
- •7.3 - Требования к ФК
- •7.4 - Схемы ФК
- •7.4.2 - Вихревые ФК
- •7.4.3 - ФК с аэродинамической стабилизацией
- •7.5 - Основные элементы ФК
- •7.5.1 - Смеситель
- •7.5.2 - Диффузоры
- •7.5.3 - Фронтовые устройства
- •7.5.4 - Корпусы и экраны
- •7.6 - Управление работой ФК
- •7.6.1 - Розжиг ФК
- •7.6.2 - Управление ФК на режимах приемистости и сброса
- •7.6.3 - Управление ФК на стационарных режимах
- •Глава 8 - Турбины ГТД
- •8.2 - Аэродинамическое проектирование турбины
- •8.2.2 - Технология одномерного проектирования турбины
- •8.2.4 - 2D/3D-моделирование невязкого потока в проточной части турбины
- •8.2.5 - 2D/3D-моделирование вязкого потока в турбине
- •8.2.6 - Синтез геометрии профилей и лопаточных венцов
- •8.2.7 - Одномерное проектирование турбины
- •8.2.7.1 - Выбор количества ступеней ТВД
- •8.2.7.2 - Выбор количества ступеней ТНД
- •8.2.7.3 - Аэродинамическое проектирование и к.п.д. турбины
- •8.2.9 - Методы управления пространственным потоком в турбине
- •8.2.10 - Экспериментальное обеспечение аэродинамического проектирования
- •8.2.11 - Перечень использованной литературы
- •8.3 - Охлаждение деталей турбины
- •8.3.1 - Тепловое состояние элементов турбин
- •8.3.1.1 - Принципы охлаждения
- •8.3.2 - Конвективное, пленочное и пористое охлаждение
- •8.3.3 - Гидравлический расчет систем охлаждения
- •8.3.4 - Методология расчета температур основных деталей турбин
- •8.3.5 - Расчет полей температур в лопатках
- •8.3.6 - Перечень использованной литературы
- •8.4 - Роторы турбин
- •8.4.1 - Конструкции роторов
- •8.4.1.1 - Диски турбин
- •8.4.1.2 - Роторы ТВД
- •8.4.1.3 - Роторы ТНД и СТ
- •8.4.1.4 - Примеры доводки и совершенствования роторов
- •8.4.1.5 - Предотвращение раскрутки и разрушения дисков
- •8.4.2 - Рабочие лопатки турбин
- •8.4.2.1 - Соединение рабочих лопаток с диском
- •8.4.3 - Охлаждение рабочих лопаток
- •8.4.4 - Перечень использованной литературы
- •8.5 - Статоры турбин
- •8.5.1 - Корпусы турбин
- •8.5.2 - Сопловые аппараты
- •8.5.3 - Аппараты закрутки
- •8.5.4 – Перечень использованной литературы
- •8.6 - Радиальные зазоры в турбинах
- •8.6.1 - Влияние радиального зазора на к.п.д. турбины
- •8.6.2 - Изменение радиальных зазоров турбины в работе
- •8.6.3 - Управление радиальными зазорами
- •8.6.4 - Выбор радиального зазора при проектировании
- •8.6.5 - Перечень использованной литературы
- •8.7 - Герметизация проточной части
- •8.7.1 - Герметизация ротора и статора от утечек охлаждающего воздуха
- •8.7.2 - Уплотнения между ротором и статором
- •8.7.3 - Перечень использованной литературы
- •8.8 - Материалы основных деталей турбины
- •8.8.1 - Диски и роторные детали турбины
- •8.8.2 - Сопловые и рабочие лопатки
- •8.8.3 - Покрытия лопаток
- •8.8.4 - Корпусы турбин
- •8.9.1 - Перечень использованной литературы
- •8.10.1 - Прогары и трещины лопаток ТВД
- •8.10.3 - Недостаточный циклический ресурс и поломки роторных деталей
- •8.10.4 - Устранение дефектов турбины в ходе доводки
- •8.11 - Перспективы развития конструкций и методов проектирования турбин
- •8.11.1 - 2D-аэродинамика: эффективные охлаждаемые лопатки ТВД
- •8.11.2 - 2D-аэродинамика: сокращение количества лопаток
- •8.11.3 - Противоположное вращение роторов ТВД и ТНД
- •8.11.4 - 2D-аэродинамика: эффективные решетки профилей ТНД
- •8.11.5 - 3D-аэродинамика: эффективные формы лопаточных венцов
- •8.11.6 - Новые материалы и покрытия для лопаток и дисков
- •8.11.7 - Совершенствование конструкций охлаждаемых лопаток
- •8.11.8 - Оптимизированные системы управления радиальными зазорами
- •8.11.9 - Развитие средств и методов проектирования
- •Глава 9 - Выходные устройства ГТД
- •9.1 - Нерегулируемые сопла
- •9.2 - Выходные устройства ТРДД
- •9.2.1 - Выходные устройства со смешением потоков
- •9.2.2 - Выходные устройства ТРДД с раздельным истечением потоков
- •9.3 - Регулируемые сопла
- •9.3.1 - Осесимметричные регулируемые сопла
- •9.3.1.1 - Регулируемое сопло двигателя Д30-Ф6
- •9.3.2 - Плоские сопла
- •9.4 - Выходные устройства двигателей самолетов укороченного и вертикального взлета-посадки
- •9.5 - «Малозаметные» выходные устройства
- •9.6 - Реверсивные устройства
- •9.6.1 - Реверсивные устройства ковшового типа
- •9.6.2 - Реверсивные устройства створчатого типа
- •9.6.3.1 - Гидравлический привод реверсивного устройства
- •9.6.3.3 - Механический замок фиксации положения реверсивного устройства
- •9.7 - Приводы выходных устройств
- •9.7.1 - Пневмопривод
- •9.7.2 - Пневмомеханический привод
- •9.8 - Выходные устройства диффузорного типа
- •9.8.1 - Конические диффузоры
- •9.8.2 - Осекольцевые диффузоры
- •9.8.3 - Улитки
- •9.8.4 - Соединения с выхлопными шахтами
- •9.8.5 - Выходные устройства вертолетных ГТД
- •9.12 - Перечень использованной литературы
- •Глава 10 - Привод агрегатов, редукторы, муфты ГТД
- •10.1 - Привод агрегатов ГТД
- •10.1.1 - Центральный привод
- •10.1.2 - Коробки приводов агрегатов
- •10.2 - Редукторы ГТД
- •10.2.1 - Редукторы ТВД
- •10.2.1.1 - Общие требования, кинематические схемы
- •10.2.1.2 - Конструкция редукторов ТВД
- •10.2.2 - Редукторы привода несущего и рулевого винтов вертолетов
- •10.2.2.1 - Редукторы привода несущего винта
- •10.2.2.1.1 - Кинематические схемы главных редукторов вертолетов
- •10.2.2.1.2 - Конструкция главных редукторов вертолетов
- •10.2.2.2 - Редукторы хвостовые и промежуточные
- •10.2.3 - Редукторы ГТУ
- •10.2.3.1 - Конструкция редукторов
- •10.3 - Муфты приводов ГТД и ГТУ
- •10.3.1 - Требования к муфтам
- •10.3.2 - Конструкция муфт
- •10.4 - Проектирование приводов агрегатов ГТД
- •10.4.1 - Проектирование центрального привода
- •10.4.1.1 - Конструкция центрального привода
- •10.4.2 - Проектирование коробок приводов агрегатов
- •10.4.2.1 - Конструкция коробки приводов агрегатов
- •10. 5 - Проектирование редукторов
- •10.5.1 - Особенности проектирования редукторов ТВД
- •10.5.2 - Особенности проектирования вертолетных редукторов
- •10.5.3 - Особенности проектирования редукторов ГТУ
- •10.6.1 - Требования к зубчатым передачам
- •10.6.2 - Классификация зубчатых передач
- •10.6.3 - Исходный производящий контур
- •10.6.4 - Нагруженность зубчатых передач
- •10.6.5 - Конструктивные параметры зубчатых передач
- •10.6.5.1 - Конструкции зубчатых колес
- •10.6.6 - Материалы зубчатых колес, способы упрочнения
- •Глава 11 - Пусковые устройства
- •11.1 - Общие сведения
- •11.1.1 - Основные типы пусковых устройств современных ГТД
- •11.1.2 - Технические характеристики пусковых устройств современных ГТД
- •11.2 - Электрические пусковые устройства ГТД
- •11.3 - Воздушные пусковые устройства ГТД
- •11.3.1 - Воздушно - турбинные пусковые устройства ГТД
- •11.3.2 - Регулирующие и отсечные воздушные заслонки
- •11.3.3 - Струйное пусковое устройство ГТД
- •11.4 - Турбокомпрессорные пусковые устройства ГТД
- •11.4.1 - Классификация ТКС ГТД
- •11.4.2 - Принцип действия ТКС
- •11.4.3 - Одновальный ТКС
- •11.4.4 - ТКС со свободной турбиной
- •11.4.5 - Особенности систем ТКС
- •11.5 - Гидравлические пусковые устройства ГТД
- •11.5.1 - Конструкция гидравлических стартеров
- •11.6 - Особенности пусковых устройств ГТД наземного применения
- •11.6.1 - Электрические пусковые устройства
- •11.6.2 - Газовые пусковые устройства
- •11.6.3 - Гидравлические пусковые устройства
- •11.7 - Редукторы пусковых устройств
- •11.8 - Муфты свободного хода пусковых устройств
- •11.8.1 - Муфты свободного хода роликового типа
- •11.8.2 – Муфты свободного хода храпового типа
- •11.9 – Системы смазки пусковых устройств
- •11.11 - Перечень используемой литературы
- •Глава 12 - Системы ГТД
- •12.1.1 - Системы автоматического управления и контроля авиационных ГТД
- •12.1.1.1 - Назначение САУ
- •12.1.1.2 - Состав САУ
- •12.1.1.3 - Основные характеристики САУ
- •12.1.1.5.2 - Порядок разработки САУ
- •12.1.1.5.3 - Основные принципы выбора варианта САУ в процессе проектирования
- •12.1.1.5.4 - Структурное построение САУ
- •12.1.1.5.5 - Программы управления ГТД
- •12.1.1.5.6 - Расчет и анализ показателей надежности
- •12.1.2 - САУ наземных ГТУ
- •12.1.2.1 - Назначение САУ
- •12.1.2.2 - Выбор САУ ГТУ и ее элементов
- •12.1.2.3 - Состав САУ ГТУ
- •12.1.2.4 - Основные характеристики САУ
- •12.1.2.5 - Работа САУ ГТУ
- •12.1.2.6 - Блок управления двигателем (БУД)
- •12.1.2.7 - Особенности системы контроля и диагностики наземных ГТД
- •12.1.4 – Перечень использованной литературы
- •12.2 - Топливные системы ГТД
- •12.2.1 - Топливные системы авиационных ГТД
- •12.2.1.1 - Назначение топливной системы
- •12.2.1.2 - Состав топливной системы
- •12.2.1.3 - Основные характеристики топливной системы
- •12.2.1.4 - Работа топливной системы
- •12.2.1.5 - Выбор топливной системы и ее элементов
- •12.2.1.5.1 – Выбор топливной системы
- •12.2.1.5.2 - Выбор насосов топливной системы
- •12.2.1.5.3 - Определение подогревов топлива в топливной системе
- •12.2.1.5.5 - Математическая модель топливной системы
- •12.2.1.6 - Гидроцилиндры
- •12.2.1.7 - Топливные фильтры
- •12.2.2 - Особенности топливных систем ГТУ
- •12.2.2.1 - Назначение топливной системы
- •12.2.2.2 - Выбор топливной системы и ее элементов
- •12.2.2.3 - Основные характеристики топливной системы
- •12.2.2.4 - Работа топливной системы
- •12.2.4 – Перечень использованной литературы
- •12.3 - Системы диагностики
- •12.3.1 - Общие вопросы диагностирования
- •12.3.1.1 - Задачи диагностирования ГТД
- •12.3.1.3 - Диагностируемые системы ГТД
- •12.3.1.4 - Виды наземного и бортового диагностирования ГТД
- •12.3.1.5 - Структура систем диагностики
- •12.3.1.6 - Регламент диагностирования ГТД
- •12.3.1.7 - Регистрация параметров ГТД
- •12.3.2 - Диагностирование системы механизации ГТД, САУ и ТП ГТД
- •12.3.3 - Диагностирование работы маслосистемы и состояния узлов ГТД, работающих в масле
- •12.3.3.1 - Неисправности маслосистемы и узлов ГТД, работающих в масле
- •12.3.3.2 - Диагностирование по параметрам маслосистемы
- •12.3.3.3 - Контроль содержания в масле частиц износа (трибодиагностика)
- •12.3.4 - Контроль и диагностика по параметрам вибрации ГТД
- •12.3.4.1 - Параметры вибрации и единицы изменения
- •12.3.4.2 - Статистические характеристики вибрации
- •12.3.4.3 - Причины возникновения вибрации в ГТД
- •12.3.4.4 - Датчики измерения вибрации
- •12.3.4.5 - Вибрационная диагностика ГТД
- •12.3.5 - Диагностирование ГТД по газодинамическим параметрам
- •12.3.5.1 - Неисправности проточной части ГТД
- •12.3.5.2 - Требования к перечню контролируемых параметров
- •12.3.5.3 - Алгоритмы диагностирования проточной части ГТД
- •12.3.6 - Обеспечение диагностирования ГТД инструментальными методами
- •12.3.6.1 - Виды неисправностей, выявляемых инструментальными методами
- •12.3.6.2 - Методы и аппаратура инструментальной диагностики
- •12.3.6.2.1 - Оптический осмотр проточной части ГТД
- •12.3.6.2.2 - Ультразвуковой метод диагностирования
- •12.3.6.2.3 - Вихретоковый метод диагностирования
- •12.3.6.2.4 - Капиллярный метод диагностирования с применением портативных аэрозольных наборов
- •12.3.6.2.5 - Диагностирование состояния проточной части ГТД перспективными методами
- •12.3.7 - Особенности диагностирования технического состояния ГТД наземного применения на базе авиационных двигателей
- •12.3.7.1 - Особенности режимов эксплуатации
- •12.3.7.2 - Общие особенности диагностирования наземных ГТД
- •12.3.7.3 - Особенности диагностирования маслосистемы
- •12.3.7.5 - Особенности диагностирования проточной части
- •12.4 - Пусковые системы
- •12.4.1 - Пусковые системы авиационных ГТД
- •12.4.1.1 - Назначение
- •12.4.1.2 - Общие требования
- •12.4.1.3 - Состав пусковых систем
- •12.4.1.4 - Область эксплуатации двигателя, область запуска
- •12.4.1.6 - Надежность запуска
- •12.4.1.7 - Характеристики запуска
- •12.4.1.8. - Выбор типа и параметров стартера
- •12.4.1.9 - Особенности запуска двигателей двухроторных схем
- •12.4.1.10 - Системы зажигания
- •12.4.1.11 - Обеспечение характеристик запуска на разгоне
- •12.4.1.12 - Регулирование компрессора на пусковых режимах
- •12.4.2 - Особенности пусковых систем наземных ГТУ
- •12.4.4 - Перечень использованной литературы
- •12.5 - Воздушные системы ГТД
- •12.5.1 - Функции ВС
- •12.5.2 - Основные требования к ВС
- •12.5.3 - Общие и локальные ВС ГТД
- •12.5.4 - Работа локальных ВС
- •12.5.4.1 - ВС охлаждения турбин ГТД
- •12.5.4.2 - ВС наддува и охлаждения опор
- •12.5.4.2.1 - Работа ВС наддува и охлаждения опор
- •12.5.4.2.2 - Типы ВС наддува и охлаждения опор
- •12.5.4.2.3 - Построение общей схемы ВС наддува и охлаждения опор
- •12.5.4.3 - Противообледенительная система (ПОС)
- •12.5.4.4 - Система кондиционирования воздуха
- •12.5.4.5 - Система активного управления зазорами
- •12.5.4.6 - Системы внешнего охлаждения ГТД
- •12.5.4.7 - Системы внешнего обогрева ГТД
- •12.5.5 - Подготовка воздуха для ВС ГТД
- •12.5.6 - Особенности ВС наземных ГТУ
- •12.5.7 - Агрегаты ВС
- •12.5.9 - Перечень использованной литературы
- •12.6.1 - Общие требования
- •12.6.2 - Схемы маслосистем ГТД
- •12.6.2.1 - Маслосистема с регулируемым давлением масла
- •12.6.2.2 - Маслосистема с нерегулируемым давлением масла
- •12.6.2.3 - Маслосистемы ГТД промышленного применения
- •12.6.3 - Маслосистемы редукторов
- •12.6.3.1 - Маслосистемы авиационных редукторов
- •12.6.3.2 - Маслосистемы редукторов ГТУ
- •12.6.4 - Особенности проектирование маслосистем
- •12.6.5 - Агрегаты маслосистемы
- •12.6.5.1 - Бак масляный
- •12.6.5.2 - Насосы масляные
- •12.6.5.3 - Теплообменники
- •12.6.5.4 - Фильтры и очистители
- •12.6.5.5 - Воздухоотделители и суфлеры
- •12.6.6 - Перспективы развития маслосистем
- •12.6.8 – Перечень использованной литературы
- •12.7 - Гидравлические системы ГТД
- •12.7.1 - Гидросистемы управления реверсивными устройствами
- •12.7.1.1 - Централизованная гидросистема управления реверсивным устройством
- •12.7.1.2 - Автономная гидросистема управления реверсивным устройством
- •12.7.1.3 - Порядок проектирования гидросистем
- •12.7.3 - Перечень использованной литературы
- •12.8 - Дренажные системы
- •12.8.1 - Назначение и классификация систем
- •12.8.2 - Характеристика объектов дренажа
- •12.8.3 - Основные схемы и принцип действия систем
- •12.8.4 - Основные требования к дренажным системам
- •12.8.5 - Обеспечение работоспособности дренажных систем
- •12.8.6 - Особенности конструкции дренажных баков
- •12.8.8 - Перечень использованной литературы
- •Глава 13 - Обвязка авиационных ГТД
- •13.1 - Общая характеристика обвязки
- •13.2 - Конструкция обвязки
- •13.2.1 - Трубопроводные коммуникации
- •13.2.1.1 - Основные сведения
- •13.2.1.2 - Трубы и патрубки
- •13.2.1.3 - Соединения
- •13.2.1.4 - Компенсирующие устройства
- •13.2.1.5 - Соединительная арматура
- •13.2.1.6 - Узлы крепления
- •13.2.1.7 - Неисправности трубопроводов
- •13.2.2 - Электрические коммуникации
- •13.2.2.1 - Общие сведения
- •13.2.2.2 - Конструкция элементов
- •13.2.2.2.1 - Электрические жгуты
- •13.2.2.2.2 - Электрические провода
- •13.2.2.2.3 - Электрические соединители
- •13.2.2.2.4 - Материалы для изготовления электрических жгутов
- •13.2.3 - Узлы крепления агрегатов и датчиков
- •13.2.4 - Механическая проводка управления
- •13.3 - Проектирование обвязки
- •13.3.1 - Требования к обвязке
- •13.3.2 - Основные принципы и порядок проектирования обвязки
- •13.3.3 - Методы отработки конструкции обвязки
- •13.3.3.1 - Натурное макетирование
- •13.3.3.2 - Электронное макетирование обвязки
- •13.3.5 - Проектирование трубопроводных коммуникаций
- •13.3.6 - Проектирование электрических коммуникаций
- •13.3.6.1 - Требования к электрическим коммуникациям
- •13.3.6.2 - Порядок проектирования электрических коммуникаций
- •13.3.6.3 - Разработка электрических схем
- •13.3.6.4 - Разработка монтажных схем
- •13.3.6.5 - Разработка чертежей электрических жгутов
- •13.6 - Перечень использованной литературы
- •Глава 14 - Динамика и прочность ГТД
- •14.1 - Теоретические основы динамики и прочности ГТД
- •14.1.1 - Напряженное состояние, тензор напряжений
- •14.1.2 - Уравнения равновесия
- •14.1.3 - Перемещения в деформируемом твердом теле. Тензор деформаций
- •14.1.4 - Уравнения совместности деформаций
- •14.1.5 - Обобщенный закон Гука
- •14.1.7 - Плоская задача теории упругости
- •14.1.8 - Пластическая деформация материала. Простое и сложное нагружение
- •14.1.11 - Ползучесть. Релаксация напряжений. Длительная прочность
- •14.1.12 - Усталостное разрушение элементов конструкций
- •14.1.13 - Малоцикловая усталость. Термическая усталость
- •14.1.14 - Накопление повреждений при нестационарном нагружении
- •14.1.15 - Закономерности развития трещин в элементах конструкций
- •14.1.16 - Свободные колебания системы с одной степенью свободы
- •14.1.17 - Вынужденные колебания системы с одной степенью свободы
- •14.1.18 - Колебания системы с вязким сопротивлением. Демпфирование колебаний
- •14.1.19 - Вынужденные колебания системы с одной степенью свободы под действием произвольной периодической возмущающей силы
- •14.1.21 - Колебания системы с распределенной массой
- •14.2 - Статическая прочность и циклическая долговечность лопаток
- •14.2.1 - Нагрузки, действующие на лопатки. Расчетные схемы лопаток
- •14.2.2 - Напряжения растяжения в профильной части рабочей лопатки от центробежных сил
- •14.2.3 - Изгибающие моменты и напряжения изгиба от газодинамических сил
- •14.2.5 - Суммарные напряжения растяжения и изгиба в профильной части лопатки
- •14.2.6 - Температурные напряжения в лопатках
- •14.2.7 - Особенности напряженного состояния широкохордных рабочих лопаток
- •14.2.9 - Расчет соединения рабочих лопаток с дисками
- •14.2.10 - Расчет на прочность антивибрационных (бандажных) полок и удлинительной ножки лопатки
- •14.2.11 - Особенности расчета на прочность лопаток статора
- •14.2.13 - Анализ трехмерных полей напряжений и деформаций в лопатках
- •14.3 - Статическая прочность и циклическая долговечность дисков
- •14.3.1 - Расчетные схемы дисков
- •14.3.2 - Расчет напряжений в диске в плоской оссесимметричной постановке
- •14.3.3 - Общие закономерности напряженного состояния дисков
- •14.3.7 - Подтверждение циклического ресурса дисков на основе концепции допустимых повреждений
- •14.3.8 - Расчет роторов барабанного типа
- •14.3.9 - Расчет дисков радиальных турбомашин
- •14.3.10 - Оптимальное проектирование дисков. Равнопрочный диск
- •14.4 - Колебания и вибрационная прочность лопаток осевых компрессоров и турбин
- •14.4.2 - Приближенный расчет собственных частот колебаний лопаток
- •14.4.3 - Трехмерные модели колебаний лопаток
- •14.4.4 - Влияние конструктивных и эксплуатационных факторов на собственные частоты колебаний лопатки
- •14.4.6 - Автоколебания лопаток
- •14.4.7 - Демпфирование колебаний лопаток
- •14.4.8 - Вынужденные колебания лопаток. Резонансная диаграмма
- •14.4.9 - Математическое моделирование вынужденных колебаний лопаток
- •14.4.10 - Экспериментальное исследование колебаний лопаток
- •14.4.11 - Коэффициент запаса вибрационной прочности лопаток, пути его повышения
- •14.4.12 - Колебания дисков
- •14.5 - Динамика роторов. Вибрация ГТД
- •14.5.1 - Критическая частота вращения ротора. История вопроса
- •14.5.2 - Динамика одномассового ротора. Поступательные перемещения
- •14.5.3 - Динамика одномассового ротора. Угловые перемещения
- •14.5.4 - Динамика одномассового несимметричного ротора
- •14.5.5 - Ротор с распределенными параметрами
- •14.5.6 - Особенности колебаний системы роторов и корпусов
- •14.5.7 - Демпфирование колебаний роторов
- •14.5.7.1 - Конструкция и принцип действия демпферов колебаний роторов
- •14.5.7.2 - Расчет параметров демпфирования
- •14.5.7.3 - Особенности гидромеханики реальных демпферов
- •14.5.8 - Вибрация ГТД
- •14.5.8.1 - Источники возмущающих сил и спектр вибрации
- •14.5.8.3 - Статистические характеристики вибрации
- •14.5.8.4 - Измерение и нормирование вибрации
- •14.6 - Прочность корпусов и подвески двигателя
- •14.6.1 - Силовая схема корпуса. Условия работы силовых корпусов
- •14.6.4 - Устойчивость корпусных деталей
- •14.6.5 - Расчет корпусов на непробиваемость
- •14.6.6 - Расчет элементов подвески
- •14.8 – Перечень использованной литературы
- •Глава 15 - Шум ГТД
- •15.1 - Источники шума ГТД
- •15.3 - Методы оценки акустических характеристик
- •15.4 - Снижение шума ГТД
- •15.4.1 - Методология проектирования систем шумоглушения
- •15.4.2 - Шумоглушение в выходных устройствах авиационных ГТД
- •15.4.3 - Конструкция звукопоглощающих узлов авиационных ГТД
- •15.4.4 – Глушители шума в наземных ГТУ
- •15.4.5 – Конструкция глушителей шума наземных ГТД
- •15.7 – Список использованной литературы
- •Глава 16 - Газотурбинные двигатели как силовой привод
- •16.1 - ГТД в силовом приводе ГТЭС и ГПА
- •16.2 - ГТД в силовых (энергетических) установках кораблей и судов
- •16.3 - ГТД в силовых установках танков
- •16.5 - Компоновка корабельных и судовых ГГТД
- •16.6 - Компоновка ГТД в силовой установке танка
- •16.8 – Перечень использованной литературы
- •Глава 17 - Автоматизация проектирования и поддержки жизненного цикла ГТД
- •17.1 - Проектирование и информационная поддержка жизненного цикла ГТД (идеология CALS)
- •17.2 - Жизненный цикл изделия. Обзор методов проектирования
- •17.3 - Программные средства проектирования
- •17.4 - Аппаратные средства систем проектирования
- •17.5 - PDM-системы: роль и место в организации проектирования
- •17.6 - Организация производства и ERP-системы
- •17.7 - Параллельный инжиниринг. Интеграция эскизного и технического проектирования
- •17.8 - Переход на безбумажную технологию
- •17.10 - ИПИ-технологии и эксплуатация изделий
- •17.11 - ИПИ-технологии и управление качеством
- •17.12 - Анализ и реинжиниринг бизнес-процессов
- •17.13 - Основы трехмерного проектирования
- •17.13.1 - Общие принципы трехмерного проектирования
- •17.13.1.1 - Способы создания геометрических моделей
- •17.13.1.2 - Основные термины объемной геометрической модели
- •17.13.1.3 - Принцип базового тела
- •17.13.1.4 - Основные термины при проектировании геометрической модели детали
- •17.13.2 - Управляющие структуры
- •17.13.3 - Принцип «Мастер-модели»
- •17.13.5 - Моделирование сборок
- •17.15 - Перечень использованной литературы
- •Глава 18 - Уплотнения в ГТД
- •18.1 - Уплотнение неподвижных соединений
- •18.2 - Уплотнения подвижных соединений
- •18.2.1 - Гидравлический расчет уплотнений подвижных соединений
- •18.3 - Уплотнение газового тракта между ротором и статором ГТД
- •18.3.1 - Лабиринтные уплотнения
- •18.3.2 - Щеточные уплотнения
- •18.3.3 - Скользящие сухие уплотнения газодинамические
- •18.3.4 - Скользящие сухие уплотнения газостатические
- •18.3.5 - Сравнение эффективностей уплотнений газового тракта между ротором и статором ГТД
- •18.4 - Примеры уплотнений газового тракта ГТД
- •18.4.1 - Пример 1
- •18.4.2 - Пример 2. Уплотнение статорной и роторной частей турбины
- •18.5 - Уплотнения масляных полостей опор роторов, редукторов, коробок приводов
- •18.7 - Перечень использованной литературы
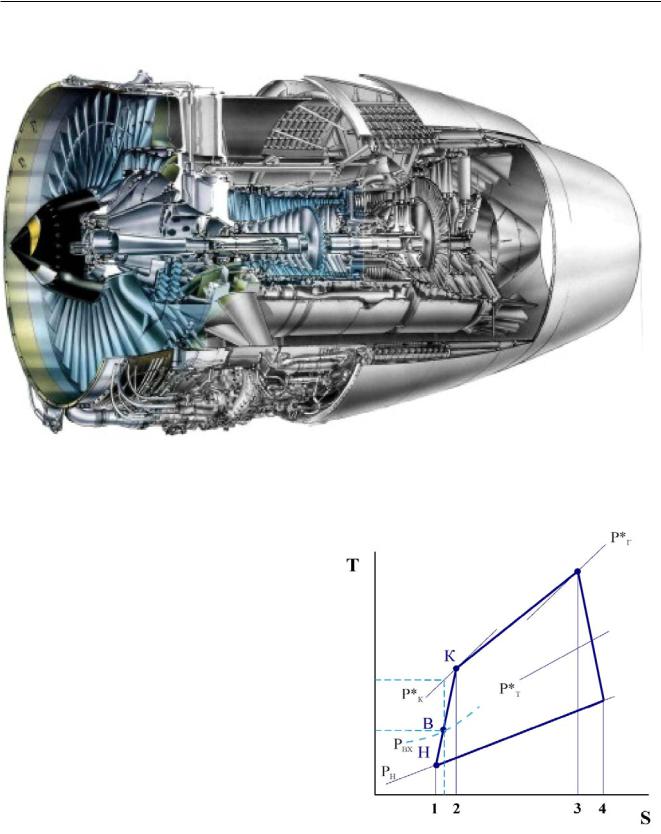
Глава 5 - Компрессоры ГТД
Глава 5 – Компрессоры ГТД
Рисунок 5_1 – Компрессор двигателя ПС-90А
ГТД – тепловая машина, работающая по известному «простому газотурбинному циклу» (см.раздел 2.1.1.1). Один из циклообразующих процессов – сжатие – представлен на диаграмме Ò-S (температура-энтропия газа) (см. Рис. 5_2).
Из диаграммы видно, что:
-идеальный процесс сжатия идет по адиабате (S = const), изображенной на диаграмме вертикальным отрезком. При этом считают, что в идеальном процессе сжатие происходит до того же давления, что и в реальном. Такое условие облегчает их сравнение;
-реальный процесс сжатия идет по политропе (с увеличением энтропии), изображ¸нной на диаграмме линией Í-Â-Ê.
Отличие реального от идеального процесса
âтом, что он протекает с потерями энергии на:
-преодоление гидравлического сопротивления при проталкивании воздуха по проточной части;
-передачу тепла воздуху в процессе сжатия;
-подвод тепла к воздуху от трения;
-потери в скачках уплотнения (возникают
âслучае превышения скорости потока скорости звука – чем выше интенсивность скачка, тем выше потери);
Рисунок 5_2 – Процесс сжатия воздуха в T-S диаграмме простого газотурбинного цикла
219

Глава 5 - Компрессоры ГТД
-вихреобразование в следе за лопатками (зависит от параметров выходной кромки, определяемой конструкцией, прочностью и технологическими возможностями производства).
Точка KÀÄ (PKÀÄ, TKÀÄ) характеризует состояние воздуха на выходе из компрессора при адиабати- ческом сжатии.
Точка Ê (ÐÊ, TÊ) характеризует состояние воздуха на выходе из компрессора.
Реальный процесс сжатия осуществляется одним из основных узлов ГТД – компрессором (см. Рис. 5_1)
Работу компрессора характеризуют следующие основные параметры:
-расход воздуха G (кг/с) - определяется коли- чеством воздуха, прошедшим через компрессор за одну секунду;
-степень повышения полного давления в ком-
прессоре πÊ* - отношение давления заторможенного потока воздуха на выходе из компрессора к давлению заторможенного потока на входе в компрессор
πÊ*= PÊ*/PÂÕ*;
- адиабатический к.п.д. ηÀÄ - определяется как отношение полезной адиабатической работы, затраченной на сжатие и проталкивание воздуха в компрессоре, к полной подведенной к компрессору
работе ηÀÄ = L*ÀÄ/ L*ÏÎË.
Адиабатический к.п.д. на расчетном режиме для отдельных ступеней осевых компрессоров составляет 0,89…0,92, а для многоступенчатых компрессоров 0,85…0,87.
Степень повышения полного давления в многоступенчатом компрессоре равна произведению степеней повышения давления отдельных его ступеней и определяется по формуле:
π*Ê=π*1π*iπ*n
Чем выше степень повышения давления в каждой ступени и чем больше число ступеней, тем выше степень повышения давления в компрессоре.
5.1 – Требования, предъявляемые к компрессорам
Компрессор - часть ГТД, степень аэродинами- ческого и конструктивного совершенства которого в значительной мере определяют мощность (тягу), экономичность, габаритные размеры, массу, надежность и ресурс двигателя. К компрессору предъявляются те же требования, что и к двигателю (см. раздел 2.3).
Помимо общих требований предъявляются
èнекоторые специфические требования:
-обеспечение заданного секундного расхода воздуха;
-обеспечение заданной степени повышения давления;
-обеспечение устойчивой, т.е. без помпажа
èпульсации, работы в широком диапазоне частоты вращения ротора.
Требования к газодинамическим параметрам компрессора (необходимые по режимам расход воздуха, степень повышения давления, коэффициент полезного действия и др.) определяются исходя из термодинамического расчета двигателя. При этом рассматривается взаимная работа узлов двигателя (камеры сгорания, турбины, выходного устройства) на различных режимах работы двигателя. Определенные таким образом основные параметры компрессора заносятся в технические условия на создание двигателя.
5.2 – Методология создания компрессоров
Создание компрессора связано с созданием двигателя в целом, поэтому этапы проектирования компрессора входят как составная часть в известные стадии разработки ГТД:
-разработка технического задания;
-разработка технического предложения;
-выполнение эскизного проекта;
-выполнение технического проекта;
-разработка конструкторской документации. Подробнее см. раздел 2.5.
5.2.1 - Типы компрессоров 5.2.1.1 – Осевые компрессоры
Осевой компрессор состоит из входного направляющего аппарата (ВНА) 5 и нескольких венцов последовательно чередующихся в осевом направлении рабочих лопаток 2, установленных на вращающемся роторе 1 и направляющих лопаток 3, закрепленных в корпусе компрессора 4 (см. Рис. 5.2.1.1_1). Совокупность одного венца рабочих лопаток и следующего за ним венца направляющих лопаток называется ступенью компрессора. Рабочие лопатки одной ступени, установленные в диске, называют рабочим колесом (РК), направляющие лопатки одной ступени, закрепленные в корпусе, называют направляющим аппаратом (НА).
В осевом компрессоре направление движения воздуха, в основном, осевое. В каналах, образованных рабочими лопатками, к воздуху подводится
220
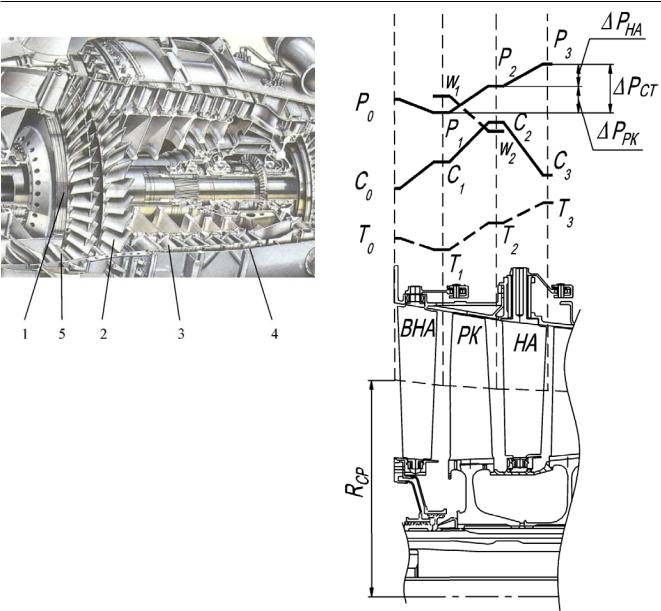
Глава 5 - Компрессоры ГТД
Рисунок 5.2.1.1_1 – Осевой компрессор двигателя Rolls-Royce Trent 700
1 – ротор; 2 - рабочие лопатки;
3 - направляющие лопатки;
4 – корпус; 5 - ВНА
механическая энергия от турбины, в результате чего давление и скорость воздуха увеличиваются. В расположенном за рабочими лопатками НА кинетическая энергия воздуха преобразуется в потенциальную, т. е. за счет снижения скорости потока воздуха повышается его давление. НА обеспечи- вает также определенное направление потока при вхождении его в следующую ступень. Принцип работы осевого многоступенчатого компрессора целесообразно рассмотреть на примере работы его отдельной ступени, так как все ступени компрессора работают аналогично.
Осевая ступень компрессора с ВНА приведена на Рис. 5.2.1.1_2. На Рис. 5.2.1.1_3 изображена элементарная ступень компрессора, представляющая собой развертку на плоскости цилиндрической поверхности, рассекающей ступень компрессора на некотором радиусе. Полная ступень компрессора складывается из бесконечного числа ее элементарных ступеней, расположенных вдоль радиуса в пределах проточной части.
Решеткой профилей называется совокупность профилей всех лопаток одного лопаточного венца, полученная рассечением его цилиндрической поверхностью.
Решетка профилей характеризуется следующими аэродинамическими и геометрическими па-
Рисунок 5.2.1.1_2 – Схема ступени и изменение параметров состояния воздуха в ступени осевого компрессора
раметрами (Рис. 5.2.1.1_4):
- ZË |
- количество лопаток; |
- b |
- хорда профиля; |
- t |
- шаг решетки профилей; |
- τ = b/t |
- густота решетки; |
- β1Ë è β2Ë |
- лопаточные углы входа и |
- θ = β2Ë - β1Ë |
выхода; |
- угол изгиба профиля; |
|
- Ñmax |
- максимальная толщина про- |
- β1 è β2 |
ôèëÿ; |
- газовые углы входа и выхода |
|
- i = β1Ë - β1 |
потока; |
- угол атаки; |
|
- δ = β2Ë - β2 |
- угол отставания. |
221
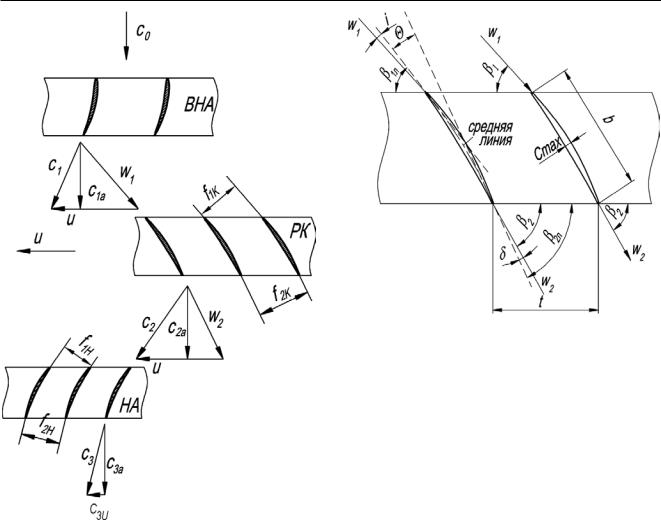
Глава 5 - Компрессоры ГТД
Рисунок 5.2.1.1_3 – Схема решеток профилей лопаток и треугольники скоростей в ступени осевого компрессора
Рассмотрим движение воздуха через элементарную ступень.
Двигаясь в осевом направлении со скоростью ÑÎ, поток воздуха поступает в ВНА. Сужающиеся межлопаточные каналы ВНА обеспечивают увели- чение скорости от ÑÎ äî Ñ1 (см. Рис. 5.2.1.1_2), сопровождающееся уменьшением статического давления и статической температуры воздуха. В ВНА воздух предварительно закручивается и поступает во вращающееся РК под некоторым углом к оси компрессора. Лопатки РК перемещаются со средней окружной скоростью U (см. Рис. 5.2.1.1_3). В результате сложения окружной скорости вращательного движения РК - U и абсолютной скорости потока на выходе из ВНА - Ñ1, получается относительная скорость потока на входе в РК - W1. Предварительная закрутка потока в ВНА позволяет уменьшить величину скорости W1, это благоприятно сказывается на уменьшении потерь в РК.
Рисунок 5.2.1.1_4 – Основные параметры решетки профилей
В результате поворота воздуха и благодаря расширяющейся форме межлопаточных каналов РК поток воздуха тормозится от скорости W1 на входе до скорости W2 на выходе из РК. Уменьшение скорости в РК приводит к повышению статического давления от P1 на входе до P2 на выходе. Работа, подводимая к воздуху в РК, идет не только на повышение статического давления, но и на увеличе- ние абсолютной скорости от значения Ñ1 äî Ñ2.
Из РК воздух со скоростью Ñ2 поступает в каналы НА. Вследствие диффузорности межлопаточ- ных каналов НА происходит уменьшение абсолютной скорости от величины Ñ2 на входе до Ñ3 на выходе, и, следовательно, повышение статического давления от P2 äî P3. Кроме того, НА осуществляет требуемый поворот воздуха перед входом в следующее РК.
Таким образом, полный прирост статического давления в ступени составляет сумму прироста давления в РК и ВНА:
∆ÐÑÒ=∆ÐÐÊ+∆ÐÂÍÀ.
В результате сжатия воздуха его температура повышается от Ò1 на входе в РК до Ò3 на выходе из ступени.
Изменение параметров состояния воздуха в ступени осевого компрессора приведено на Рис. 5.2.1.1_2.
При движении вдоль проточной части многоступенчатого компрессора воздух сжимается и его плотность возрастает. Поэтому, чтобы обеспечить
222
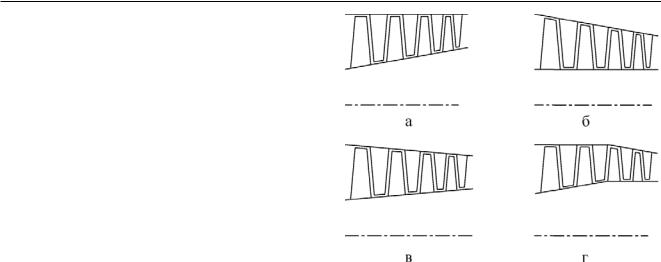
Глава 5 - Компрессоры ГТД
требуемую величину осевой скорости на выходе из компрессора, которая обычно составляет 120…180 м/с, проточную часть компрессора выполняют сужающейся к выходу.
Отношение давления на выходе из ступени
êдавлению на входе в нее называется степенью
повышения давления в ступени - π*ÑÒ. Степень повышения давления многоступенчатого компрессора тем больше, чем больше степени повышения давлений отдельных ступеней и чем больше их количество.
Степень повышения давления в ступени осевого компрессора в основном зависит от средней окружной скорости лопаток. Чем больше эта скорость, тем больше степень повышения давления. Максимальная окружная скорость лопаток из условий их прочности обычно не превышает 300…450 м/с. Например, максимальная окружная скорость рабочих лопаток первой ступени КВД двигателя ПС-90А составляет 365 м/с. Диаметр ступени компрессора определяется потребным расходом воздуха, его плотностью и осевой скоростью. Осевая скорость воздуха сохраняется по всем ступеням постоянной или несколько уменьшается
êпоследним ступеням. Так как плотность воздуха на входе в первую ступень минимальная, то наибольшую площадь проточной части имеет первая ступень, далее площадь уменьшается к последним ступеням. Площадь проточной части ограничена ее наружным и внутренним диаметрами. Для уменьшения наружного диаметра первой ступени при заданной площади проточной части уменьшают внутренний диаметр, а чтобы обеспечить размещение лопаток на роторе, внутренний диаметр выбирают обычно равным 0,35…0,4 от наружного диаметра.
На последующих ступенях может быть сохранен тот же наружный диаметр, что и на первой ступени (см. Рис. 5.2.1.1_5а), тот же внутренний диаметр (см. Рис. 5.2.1.1_5б), или тот же средний диаметр (см. Рис. 5.2.1.1_5в).
Âпервом случае потребное уменьшение площади проточной части (вследствие возрастания плотности воздуха) достигается увеличением внутреннего диаметра проточной части. При этом средние окружные скорости ступеней растут и, следовательно, увеличиваются их степени повышения давления. Но наряду с этим преимуществом указанная конструкция компрессора обладает и недостатком - меньшая длина лопаток последних ступеней. Зазор между торцом лопатки и корпусом при наличии коротких лопаток относительно больше, чем при длинных. В результате этого у компрессора с короткими лопатками увеличивается обратное
Рисунок 5.2.1.1_5 – Схемы профилей проточной части а) с постоянным наружным ди-
аметром; б) с постоянным внутренним диаметром; в) с постоянным средним диаметром; г) с переменным наружным, внутренним и средним диаметрами
перетекание воздуха в зазоре и, следовательно, уменьшается степень повышения давления компрессора.
При постоянном внутреннем или среднем диаметре лопатки последних ступеней более длинные, поэтому и перетекания меньше. Степень повышения давления ступеней остается постоянной (при постоянном среднем диаметре) или уменьшается (при постоянном внутреннем диаметре), поскольку зависит от средней окружной скорости.
В целях расширения области устойчивой работы и повышения к.п.д. применяются двухкаскадные и трехкаскадные схемы осевых компрессоров. В многокаскадном компрессоре несколько последовательно расположенных роторов автономно приводящихся во вращение отдельными турбинами (см. раздел 5.4).
5.2.1.2 – Центробежные компрессоры
В центробежном компрессоре для повышения давления газа используется центробежный эффект, который позволяет увеличить степень повышения полного давления намного больше, чем в осевом компрессоре. К числу достоинств центробежных компрессоров относятся также относительная простота конструкции (существенно меньшее число деталей), более благоприятная характеристика и меньшая чувствительность к условиям эксплуатации, чем у осевых.
223
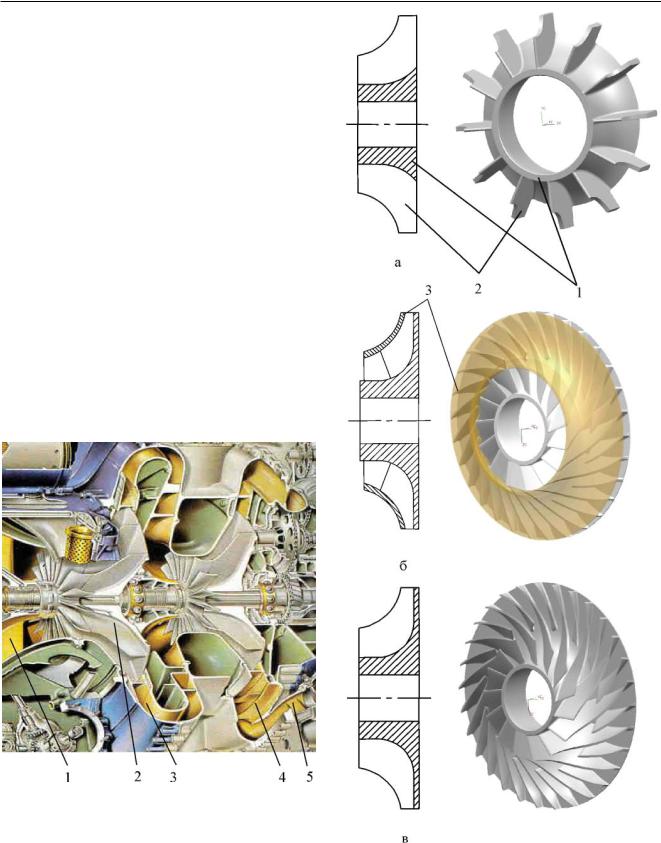
Глава 5 - Компрессоры ГТД
Ступень центробежного компрессора состоит из ВНА 1, РК 2 и выходной системы, которая вклю- чает в себя безлопаточный щелевой диффузор 3, лопаточный диффузор 4 и выходной патрубок 5 (см. Рис. 5.2.1.2_1). В РК механическая энергия, подводимая к колесу от турбины, преобразуется в потенциальную и кинетическую энергию газа. Это преобразование энергии в РК осуществляется в результате аэродинамического взаимодействия потока газа с вращающимся лопаточным аппаратом. Поток на входе обычно закручивается по вращению.
Хотя в связи с этим уменьшается напор, сообщаемый воздуху, необходимость в предварительной закрутке по вращению связана с желанием уменьшить величину относительной скорости, которая в периферийном сечении достигает значений, близких к скорости звука и даже превышающих ее.
По конструктивному выполнению рабочие колеса делятся на следующие типы:
-открытые (Рис. 5.2.1.2_2a),
-закрытые (Рис. 5.2.1.2_2б)
-полуоткрытые (Рис. 5.2.1.2_2в).
Рисунок 5.2.1.2_1 – Двухступенчатый центробежный компрессор двигателя Rolls-Royce Dart
(Печатается с разрешения RollsRoyce plc)
1 - ВНА; 2 - РК; 3 - безлопаточ- ный щелевой диффузор; 4 - лопаточный диффузор; 5 - выходной патрубок
Рисунок 5.2.1.2_2 - Типы рабочих колес а) открытого типа;
b)закрытого типа;
c)полуоткрытого типа.
1 - втулка; 2.- рабочие лопатки;
3 - покрывной диск
224
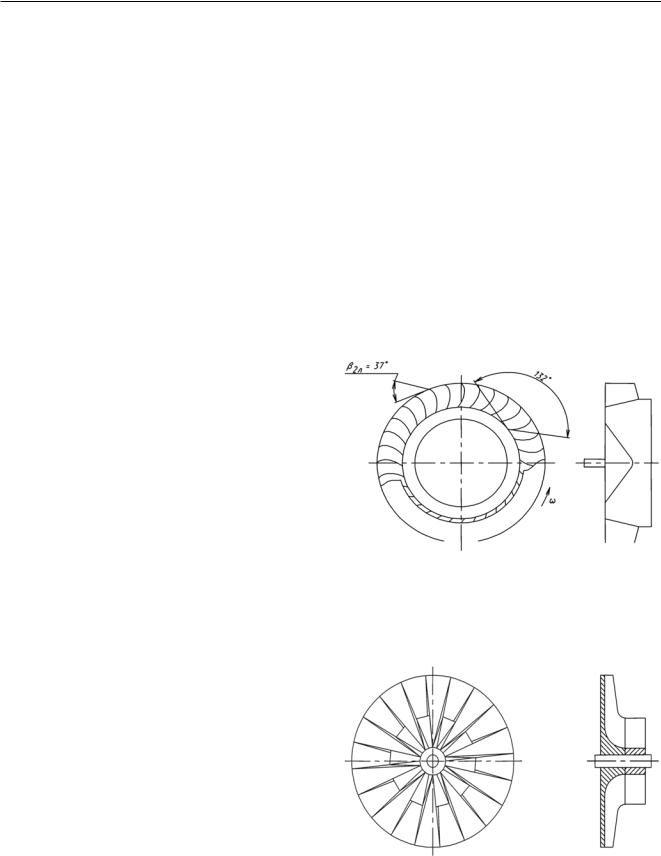
Глава 5 - Компрессоры ГТД
Рабочее колесо открытого типа состоит из втулки 1 и закрепленных на ней рабочих лопаток 2, так что межлопаточные каналы с двух торцевых сторон ограничены лишь неподвижными стенками кожуха, расположенными на небольшом расстоянии от торцов лопаток. Колесо открытого типа является малоэкономичным ввиду больших потерь от перетекания газа через торцы лопаток и из-за влияния среды в зазоре между колесами и кожухом на поток в канале колеса. Такие колеса применяются иногда в дешевых вентиляторах или дымососах.
ÓРК закрытого типа лопатки 1 с двух торцов прикрепляются к дискам 2 и 3, один из которых называется покрывным. В закрытом колесе оба торца лопаток закрыты, так что перетекания газа через торцы быть не может. Поток газа в колесе изолирован от воздействия газа, находящегося в зазоре между РК и кожухом. Ввиду этого закрытые колеса являются наиболее экономичными и применяются чаще всего в стационарных центробежных компрессорах. Лопатки закрытых колес обычно выполняют заодно с основным диском, а покрывной диск крепится к ним болтами или с помощью сварки.
Óколес полуоткрытого типа лопатки с одной стороны соединены с диском, а с другой стороны также открыты. Обычно лопатки полуоткрытых РК выполняют заодно с дисками. Полуоткрытые колеса по экономичности занимают промежуточное положение. С точки зрения механической прочности РК полуоткрытого типа имеют наибольшую прочность по сравнению с колесами закрытого типа, так как наличие покрывного диска приводит к увеличению напряжений во всех элементах основного диска.
Центробежные компрессоры могут быть с односторонним и двухсторонним входом. У компрессора с односторонним осевым входом воздух поступает на РК через неподвижный НА осевого типа.
Óкомпрессора с двухсторонним входом чаще используется кольцевой вход, а неподвижный НА представляет собой кольцевую решетку, за которой устанавливаются также направляющие тороидальные поверхности. Этот вращающийся НА иногда выполняется совместно с колесом – как одна деталь.
Недостатком центробежных компрессоров является пониженная лобовая производительность, так как сечение входа воздуха занимает лишь незначительную часть миделя (максимальной площади поперечного сечения) компрессора, особенно у компрессора с односторонним входом. Более затруднительно создание многоступенчатой конструкции, так как после выхода из предыдущей ступени
воздух может попасть на вход следующей лишь с помощью так называемого обратного канала сложной петлеобразной формы.
Использование центробежного компрессора вместо многоступенчатого осевого возможно, когда к.п.д. ступени центробежного компрессора при πK* = 6…8 достигнет η* = 0,82…0,83, т.е. приблизится к к.п.д. осевых многоступенчатых компрессоров. Более целесообразно применение осецентробежных компрессоров в двигателях малых размеров.
По аэродинамической схеме РК могут быть разделены на четыре основных группы:
-колеса низкой реактивности с лопатками, загнутыми в сторону вращения (см. Рис. 5.2.1.2_3);
-колеса со степенью реактивности, близкой
ê0,5, с радиальными лопатками (β2Ë = 90°) (ñì. Ðèñ. 5.2.1.2_4);
Рисунок 5.2.1.2_3 - Схема колеса низкой реактивности
Рисунок 5.2.1.2_4 - Колесо полуоткрытого типа с выходным углом β2Ë = 90°
225

Глава 5 - Компрессоры ГТД
-колеса средней реактивности с лопатками,
умеренно загнутыми в сторону, обратную вращению (β2Ë = 40…60°);
-колеса высокой реактивности с лопатками, загнутыми в сторону, обратную вращению
(β2Ë = 15…35°).
Колеса низкой реактивности применяют, в основном, при производстве промышленных вентиляторов. Эти колеса отличаются высоким значением коэффициента расхода и сравнительно большими значениями абсолютной скорости на выходе из колеса. Вследствие низкой степени реактивности основной процесс повышения статического давления
âмашинах с такими колесами происходит за счет диффузорного эффекта в неподвижных элементах.
Колеса со степенью реактивности, близкой к 0,5, с радиальными лопатками обычно выполняются полуоткрытого типа. В отличие от колес с изогнутыми лопатками здесь лопатки начинаются от втулки, и поворот потока из осевого направления
âрадиальное происходит в межлопаточном пространстве. Входные кромки лопаток в таких колесах обычно загибаются таким образом, чтобы их направление соответствовало направлению набегающего потока.
Вследствие отсутствия покрывного диска и благодаря прямолинейной форме и радиальному направлению лопаток напряжения в таких колесах при одних и тех же окружных скоростях значительно ниже, чем в двухдисковых колесах (с покрывным диском) с искривленными лопатками. Поэтому такие колеса пригодны для работы с большими скоростями вращения (до U = 550…600 м/с), что дает возможность получить в ступенях весьма большие напоры и расходы. Колеса этой группы нашли широкое применение в авиационных и транспортных машинах.
Колеса средней реактивности с лопатками,
умеренно загнутыми в сторону, обратную вращению
(β2Ë = 40…60°), распространены в стационарных промышленных компрессорах для нагнетания различных газов (например, азота). Такие колеса часто называют просто колесами компрессорного типа.
Колеса высокой реактивности с лопатками,
загнутыми в сторону, обратную вращению
(β2Ë = 15…35°), имеют широкое применение в насосостроении. В последнее время их стали применять также и в компрессорах. Благодаря высокой степени реактивности ступени с такими колесами имеют сравнительно высокий к.п.д. (до 86…87%).
Для колес этой группы характерны небольшие зна- чения коэффициента расходной скорости ϕ2r.
Такие колеса часто используются в последних ступенях многоступенчатых компрессоров,
где в результате сжатия в предыдущих ступенях объемный расход значительно меньше, чем в на- чальных ступенях.
Ротора центробежных компрессоров состоят из РК с лопатками, вращающихся НА, вала или передней и задней цапф.
Если конструктивно РК выполнено отдельно от вала, то передача крутящего момента производится посредством цилиндрических и торцевых шлиц. Отдельные ступени соединяются между собой промежуточными валами. Передача крутящего момента осуществляется призонными болтами или шлицевым соединением в зависимости от конструкции компрессора. Валы роторов обычно изготавливают из легированных конструкционных сталей.
5.2.1.3 – Осецентробежные компрессоры
Осецентробежные компрессоры представляют собой комбинированное устройство, в котором высокий к.п.д. (≈ 83%) осевого компрессора (первые 5…7 ступеней) сочетается с высокой степенью сжатия в единственной последней центробежной ступени (см. Рис. 5.2.1.3_1). Центробежная ступень устанавливается вместо нескольких осевых, имеющих сверхмалые высоты рабочих лопаток, у которых особенно сказывается влияние радиальных зазоров над лопатками.
Такие компрессоры, несмотря на некоторую потерю общего к.п.д. (по сравнению с осевым компрессором такой же степени сжатия), имеют зна- чительный выигрыш по длинновым размерам и массе. Это и предопределяет главную область их использования – небольшие ТРД и ТВД для региональных самолетов.
5.2.2 – Аэродинамическое проектирование компрессора
5.2.2.1 – Общие этапы
Методологию аэродинамического проектирования всех типов компрессоров можно представить в виде блок-схемы (см. Рис. 5.2.2.1_1). Все расчетные работы крупно можно разделить на три этапа:
-расчет компрессора на основе одномерной математической модели;
-расчет компрессора на основе двумерной осесимметричной математической модели;
-трехмерный расчет вязкого течения в лопаточных венцах компрессора.
226
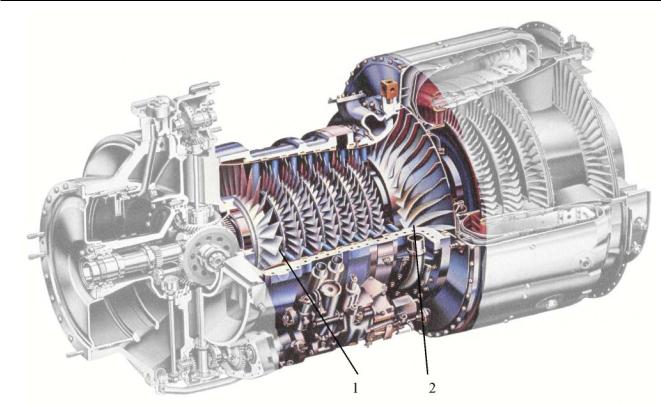
Глава 5 - Компрессоры ГТД
Рисунок 5.2.1.3_1 – Осецентробежный компрессор двигателя Honeywell Т53. Материал любезно предоставлен компанией Honeywell
1 - осевые ступени; 2 - центробежная ступень
5.2.2.2 – Расчет компрессора на основе одномерной математической
модели
Согласно блок–схеме (см. Рис. 5.2.2.1_1) на первом этапе аэродинамического проектирования определяется тип компрессора:
-осевой;
-центробежный;
-осецентробежный.
После выбора типа компрессора на основании исходных данных технического задания выполняется расчет его характеристик. На первом этапе аэродинамического проектирования компрессора расчет выполняется на основе одномерной математической модели. Исходными данными для рас- чета являются:
-полное давление и температура потока на входе в компрессор;
-расход воздуха;
-степень повышения давления;
-частота вращения ротора;
-распределение коэффициента затраченной работы по ступеням.
Расчет компрессора по параметрам на среднем радиусе выполняется на основании уравнений известных из термодинамики.
На этом этапе проектирования определяются параметры компрессора для последующего расче- та характеристик компрессора:
-размеры и форма проточной части;
-изоэнтропический коэффициент полезного действия;
-масса и длина;
-распределение параметров по ступеням;
-конструктивныепараметрылопаточныхвенцов;
-углы изгиба профиля рабочих и направляющих лопаток;
-углы атаки и отставания лопаток;
-углы лопаток на среднем радиусе.
Расчет характеристик проводится для определения параметров компрессора и запасов устойчи- вости на различных эксплуатационных режимах его работы.
Расчет каждой ступени компрессора проводится последовательно от ступени к ступени. После расчета всех ступеней вычисляется суммарная степень повышения давления компрессора
227
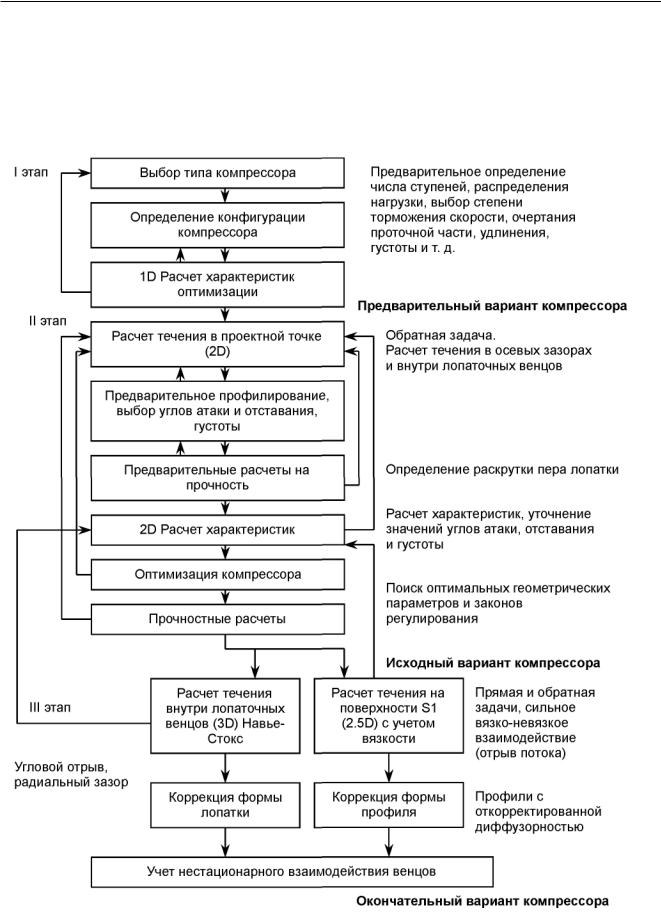
Глава 5 - Компрессоры ГТД
Z
π*K = ∏π*i
i=1
Суммарный к.п.д. компрессора определяется по методике, используемой в проектировочном расчете компрессора на среднем радиусе (см. вы-
ше). В результате выполнения первого этапа аэродинамического проектирования определяется предварительный вариант основных геометрических параметров проточной части компрессора, которые можно использовать для прорисовки его конструктивного облика.
Рисунок 5.2.2.1_1 – Методология аэродинамического проектирования компрессоров
228

Глава 5 - Компрессоры ГТД
В общем случае результаты одномерного проектирования имеют как самостоятельное значение, так и могут использоваться в качестве исходных данных для следующего этапа разработки проекта.
5.2.2.3 – Расчет компрессора на основе двумерной осесимметричной
математической модели
В основу второго этапа аэродинамического проектирования положено решение обратной зада- чи расчета осесимметричного течения в проектной точке. Смысл проектирования, в конечном счете, состоит в определении конструктивных параметров компрессора (включая координаты профилей), обеспечивающих реализацию расчетного поля те- чения.
Начальные значения геометрических параметров находятся исходя из имеющегося опыта, однако уже на этой стадии предусматриваются расчетная проверка прочности наиболее ответственных деталей (лопаток и дисков ротора). При необходимости производится коррекция их геометрии и повторный расчет течения.
Важнейшей частью работ на втором этапе проектирования компрессора является расчет его характеристик на основе осесимметричной математической модели. В основу расчета положен один из вариантов так называемого «метода кривизны линий тока». В качестве исходной информации в нем используются суммарные параметры компрессора (GÂ , π*Ê , n) и данные, полученные при одномерном расчете:
-средние параметры ступеней;
-размеры проточной части компрессора. Граничными условиями на входе в компрес-
сор являются:
- радиальное распределение полного давле-
íèÿ;
-радиальное распределение температуры торможения;
-радиальное распределение угла потока. Граничными условиями на выходе из комп-
рессора являются:
-радиальное распределение угла потока;
-постоянство статического давления;
-равенство суммарного расхода воздуха в струй-
ках тока проектному значению GÂ.
Для решения обратной задачи определения параметров потока в расчетных сечениях используется система газодинамических уравнений для идеального газа, включающая дифференциальное уравнение движения и эмпирические соотношения. Эти соотношения используются для на-
хождения потерь в лопаточных венцах и учета влияния радиальных зазоров на параметры компрессора.
В результате решения обратной задачи определяются параметры потока в межвенцовых зазорах осевого компрессора, осредненные и распределенные параметры лопаточных венцов, ступеней
èкомпрессора в целом, в том числе его суммарные параметры - степень повышения полного давления
èизоэнтропический к.п.д.
5.2.2.4 – Трехмерный расчет вязкого течения в лопаточных венцах комп-
рессора
Âсоответствии с рассматриваемой методологией на третьем этапе предусматривается дальнейшая оптимизация компрессора, основанная на совершенствовании аэродинамики трехмерного расчета вязкого течения. Для этого используются программные комплексы, в которых реализовано решение уравнений Навье-Стокса. На этом этапе может также применяться квазитрехмерный подход, базирующийся на расчете вязкого потока в межлопаточном канале в слоях переменной толщины, выделяемых на различных участках по радиусу. Для этого предварительно проводится расчет трехмерного невязкого потока.
Âкачестве граничных условий задаются:
-углы потока в окружном направлении;
-углы потока в меридиональной плоскости
âнаправлении от втулки к периферии;
-распределение по радиусу полного давления;
-распределение по радиусу температуры. На выходе должно задаваться:
-статическое давление на втулке;
-распределение давления от втулки к периферии (определяется из уравнения радиального равновесия).
Граничное условие на стенке – прилипание (скорость потока на стенке равна нулю); гранич- ные условия на периодической границе - периоди- чески повторяющиеся (параметры потока и геометрия компрессора являются периодическими – равными числу лопаток в лопаточном венце).
Расчеты с использованием трехмерного программного комплекса позволяют получать надежные качественные и количественные данные о параметрах проектируемого компрессора. Их оптимизация сводится к решению задач течения с вариацией координат профилей лопаток и проточной части в меридиональном сечении компрессора. Результат трехмерного расчета вязкого течения в лопаточных венцах проектируемого компрессора показан на Рис. 5.2.2.4_1.
229
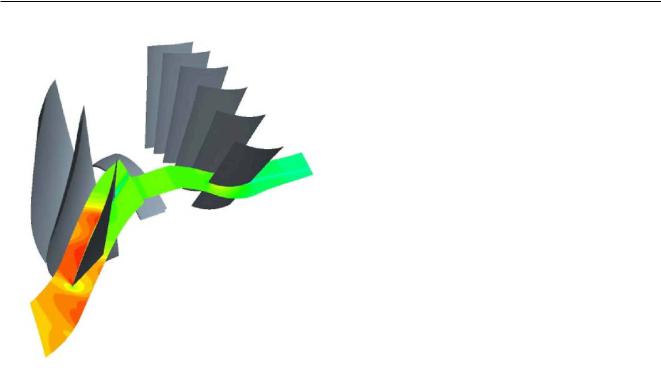
Глава 5 - Компрессоры ГТД
Рисунок 5.2.2.4_1 – Распределение скоростей потока по тракту компрессора (трехмерный расчет)
5.2.2.5 – Профилирование лопаточ- ных венцов компрессора
Задача профилирования лопаточных венцов выполняется на втором и третьем этапе проектирования компрессора, когда выполняется расчет параметров в меридиональных сечениях. Расчет профилей выполняется по тем же формулам, что и расчет одномерной модели на первом этапе. По результатам расчета определяются:
-углы атаки и отставания потока;
-профили лопаток в конических сечениях;
-профили лопаток в плоских сечениях. Определение координат профилей в плоских
сечениях лопаток, осуществляется пересчетом профилей конических сечений.
Совокупность координат всех плоских сече- ний представляет собой математическую модель поверхности пера лопатки. В таком виде модель может быть использована для изготовления лопатки на станках с числовым программным управлением.
5.2.2.6 – Обеспечение аэродинами- ческой устойчивости
Еще одной задачей второго и третьего этапа аэродинамического проектирования компрессора
является обеспечение его аэродинамической устой- чивости.
Работа осевого компрессора согласована с работой последующих узлов таким образом, что его параметры, в зависимости от частоты вращения ротора, изменяются по определенному закону, соответствующему линии, которую принято называть линией рабочих режимов (ЛРР).
Ступени компрессора проектируются и согласовываются между собой так, что на ЛРР компрессор работает близко к своему оптимуму в некоторой ограниченной области, называемой зоной расчетных режимов.
Работа компрессора на нерасчетном режиме может привести к его неустойчивой работе и возникновению помпажа. Помпаж – газодинамически неустойчивый автоколебательный режим работы компрессора и его сети, характеризующийся сильными низкочастотными колебаниями параметров:
-давления;
-температуры;
-расхода воздуха.
Характер протекания помпажа в значительной степени зависит от следующих факторов:
-тип компрессора;
-геометрические и аэродинамические характеристики компрессора;
-объем камеры сгорания;
-площадь соплового аппарата турбины. Помпаж сопровождается срывами потока зна-
чительной интенсивности в ступенях компрессора
èпериодическими выбросами сжатого в компрессоре воздуха во всасывающую систему. Встречные ударные волны и низкочастотные колебания давления могут вызвать повреждения компрессора.
Нерасчетный режим появляется из-за рассогласования в работе его первых и последних ступеней. Рассогласование может быть вызвано следующими причинами:
-отклонениями частоты вращения ротора от расчетного значения;
-изменениями температуры воздуха на входе в компрессор.
При отклонении частоты вращения ротора от расчетного значения нарушается работа крайних ступеней, когда уменьшение частоты вращения вызывает срыв потока в первых ступенях, а увели- чение - в последних.
При уменьшении частоты вращения ротора компрессора осевые составляющие скорости на первых ступенях уменьшаются сильнее, чем на последних. Так как окружные скорости на первых
èпоследних ступенях изменяются одинаково, углы атаки на первых ступенях увеличиваются, а на пос-
230
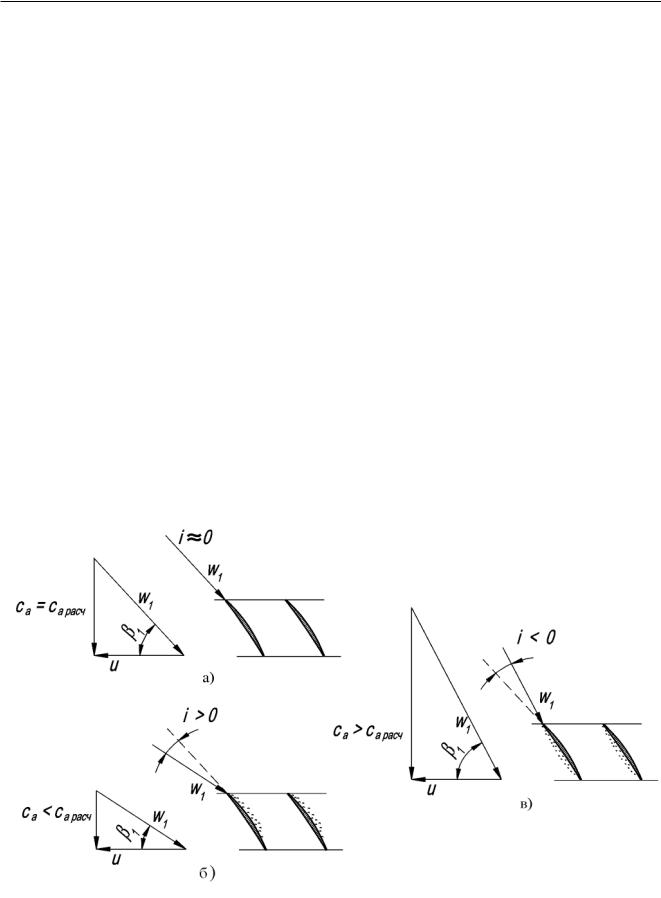
Глава 5 - Компрессоры ГТД
ледних уменьшаются. В этом случае углы атаки на первых ступенях достигают критических значений раньше, чем на последних, что обусловливает срыв потока на первых ступенях. Вследствие этого срывы на последних ступенях отсутствуют. Однако при очень больших отрицательных углах атаки на последних ступенях может наступить так называемый «турбинный» режим, при котором воздух в этих ступенях не сжимается, а расширяется. При таком режиме работы последних ступеней падает к.п.д. и напор компрессора.
Если частоты вращения ротора компрессора увеличиваются по сравнению с расчетным значе- нием, то осевая составляющая скорости на последних ступенях будет уменьшаться вследствие увеличения плотности воздуха из-за роста степени сжатия. При этом уменьшение скорости происходит таким образом, что углы атаки лопаток на последних ступенях увеличиваются значительно быстрее, чем на первых. Таким образом, срывы потока, вызывающие помпаж, будут возникать, прежде всего, на последних ступенях.
Изменение температуры воздуха на входе в компрессор также может вызвать рассогласование, вследствие того, что увеличение температуры воздуха при постоянной частоте вращения вызывает
уменьшение осевой составляющей скорости на ступенях компрессора, тем самым увеличивая углы атаки. На последних ступенях углы атаки увеличиваются быстрее, в результате чего на этих ступенях критические углы атаки достигаются раньше, чем на первых. При достижении критических углов атаки образуются срывные зоны, которые, постепенно увеличиваясь в размерах, охватывают все большее число ступеней до тех пор, пока не наступит неустойчивый режим работы всего компрессора.
Треугольники скоростей позволяют выяснить физическую сущность возникновения помпажа компрессора и применяемых мер борьбы с ним. На Рис. 5.2.2.6_1 представлена картина обтекания лопаток на трех режимах работы компрессора.
Если компрессор работает на расчетном режиме, то направление движения воздушного потока на входе в РК примерно параллельно касательной к средней линии профиля на передних кромках лопаток (см. Рис. 5.2.2.6_1а).
Уменьшение расхода воздуха по сравнению с расчетным (уменьшение осевой составляющей
абсолютной скорости - Ñà) приводит к увеличению углов атаки на лопатках (Рис. 5.2.2.6_1б). При больших положительных углах атаки, превышающих критические, возникает срыв потока, сопровожда-
Рисунок 5.2.2.6_1 – Схема обтекания лопаток РК осевого компрессора а) расчетный режим работы; б, в) нерасчетные режимы работы
231
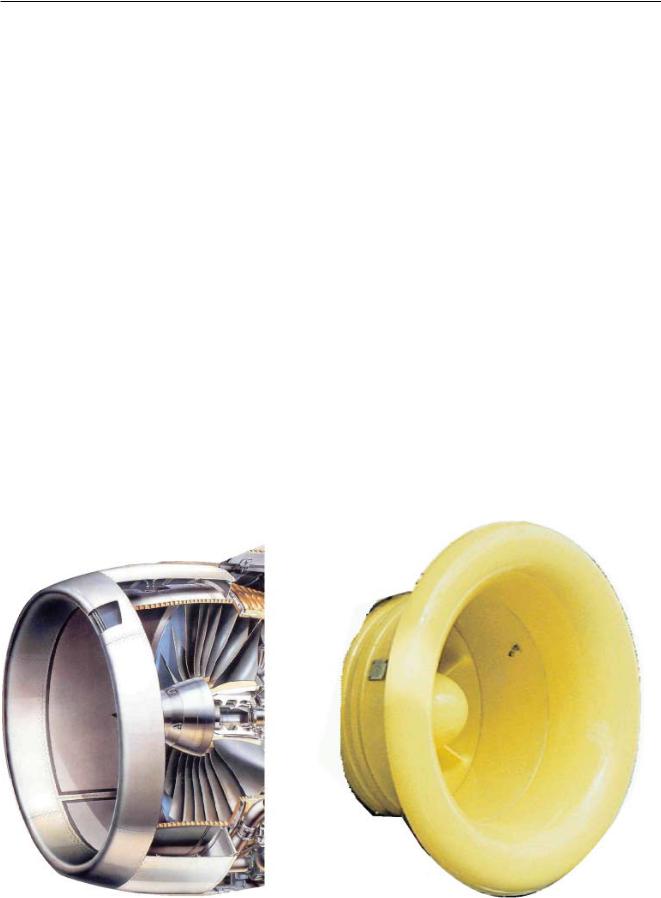
Глава 5 - Компрессоры ГТД
ющийся образованием вихревых зон с выпуклой поверхности профилей. Области этих зон нарастают и проникают внутрь компрессора, заполняя его проточную часть. Происходит периодически повторяющаяся «закупорка» проточной части компрессора вихревыми областями. Через эти области воздух из-за компрессора периодически прорывается обратно, в сторону входа. Как следствие возникают автоколебания потока, приводящие к неустой- чивой работе, т.е. к помпажу компрессора.
Увеличение расхода воздуха через ступень (увеличение осевой составляющей абсолютной скорости - Ñà) вызывает уменьшение углов атаки на лопатках (см. Рис. 5.3.2.6_1в), при этом угол атаки i становится меньше нуля. Поток воздуха ударяется в выпуклую часть лопатки, а на ее вогнутой части возникают вихри. В связи с тем, что поток воздуха под действием сил инерции прижимается к вогнутым сторонам лопаток, образовавшиеся вихри не могут распространиться по всему колесу и носят местный характер, не нарушая устойчивой работы компрессора.
Обеспечение аэродинамической устойчивости осуществляется регулированием компрессора:
- поворотом одного или нескольких венцов НА, что позволяет сохранить оптимальные углы атаки на рабочих колесах;
- перепуском воздуха из-за отдельных ступеней компрессора, что приводит к увеличению расхода воздуха через предыдущие ступени и, как следствие, к более оптимальным углам атаки на рабочие колеса.
Подробней о способах регулирования компрессора рассказано в разделе 5.7.
5.2.2.7 – Интеграция ГТД с воздухозаборником самол¸та
Входные устройства СУ (см. Рис. 5.2.2.7_1) располагаются перед входом в компрессор и предназначаются для организации равномерной пода- чи воздушного потока на вход в двигатель с сохранением высокой эффективности сжатия во всем диапазоне рабочих режимов компрессора.
Входное устройство авиационного двигателя называют воздухозаборником. В воздухозаборнике располагают коллекторы противообледенительной системы (см. Рис. 5.7_1), а внутренние обводы выполнены с панелями шумоглушения. Воздухозаборник выполняет, помимо прочего, функцию преобразования кинетической энергии набегающего потока в потенциальную.
Для нормальной работы двигателя необходимо обеспечить заданное значение скорости потока
Рисунок 5.2.2.7_1 – Входные устройства
а) авиационного дв. Rolls-Royce RR535; б) ГТУ наземного применения ПС-90ГП-1
232
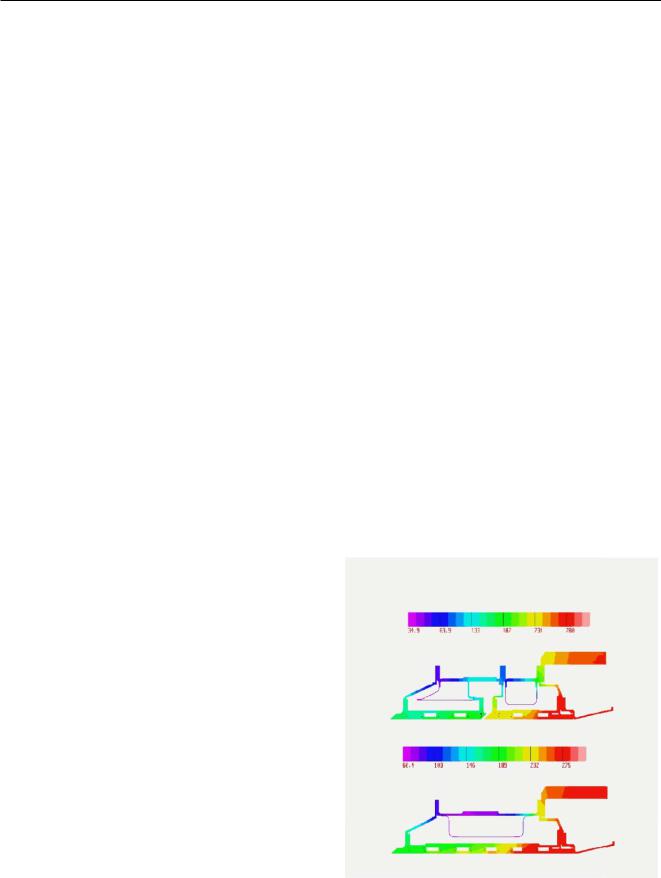
Глава 5 - Компрессоры ГТД
на входе в компрессор, в том числе и при постоянно меняющихся условиях окружающей среды. Изменение условий работы входного устройства, условия размещения его и двигателя на самолете (например, наличие обводных и криволинейных каналов) создают неравномерность поля скоростей перед компрессором.
Устойчивая работа компрессора возможна лишь при определенном значении степени неравномерности и пульсации параметров во входном устройстве.Наличие пульсаций отрицательно сказывается на работе входного устройства, что может приводить к неустойчивой работе компрессора.
Пульсация характеризуется:
-частотой;
-амплитудой.
Источниками пульсаций являются:
-неравномерность поля параметров;
-неустойчивость пограничного слоя;
-конструктивные и технологические выступы в проточной части входного устройства.
Таким образом, входное устройство должно быть спроектировано так, чтобы уровень неравномерности поля скоростей и пульсационные характеристики потока в его выходном сечении не приводили к неустойчивой работе двигателя.
Для ГТД с большой степенью двухконтурности (m ≥ 4) помимо требований, изложенных выше,
êвоздухозаборникам предъявляются специфические требования. Воздухозаборники таких силовых установок относительно короткие (l/d < 1), что обуславливает их высокую чувствительность:
-к порывам ветра;
-косому обдуву при работе на месте;
-к минимальным скоростям полета.
Для снижения чувствительности компрессора с «коротким» воздухозаборником к этим факторам вводят дополнительные эксплуатационные ограничения:
-по направлению и скорости ветра;
-введением взлета самолета с «роллинг-старта»;
-применением наземного устройства под воздухозаборником, исключающим возникновение вихревого шнура.
5.2.3 – Тепловое состояние компрессора
При создании нового двигателя особое внимание уделяется обеспечению требуемого ресурса и надежности деталей и узлов компрессора. Тепловое состояние деталей компрессора существенно влияет на их напряженно-деформированное со-
стояние (НДС) и, соответственно, на ресурс и надежность узлов. В зависимости от распределения температуры в неравномерно нагретых деталях могут возникать напряжения:
-растяжения;
-сжатия.
Оценив величину напряжений в деталях, выбирают конструкцию, которая позволит обеспе- чить назначенный ресурс. В связи с этим, получе- ние достоверного теплового состояния по циклу работы ГТД является важнейшей задачей.
5.2.3.1 – Расчет теплового состояния деталей компрессора
На Рис. 5.2.3.1_1 представлено расчетное тепловое состояние корпусов компрессора на одном из режимов работы двигателя. Расчет выполнен в осесимметричной постановке. Для определения изменения теплового состояния в процессе работы двигателя необходимо решить нестационарное уравнение теплопроводности:
(λ Т)= γ dTdτ ,
ãäå Ò - искомая температура детали; λ, γ - теплопроводность, теплоемкость детали;
τ- время.
Рисунок 5.2.3.1_1 – Расчетное тепловое состояние корпусов компрессора на одном из режимов работы двигателя
233

Глава 5 - Компрессоры ГТД
Подробно вывод данного уравнения, а так же методы его решения изложены в учебных пособиях по основам теплопередачи, см. например [5.13.1]. Поэтому здесь это не рассматривается. Отметим только, что для решения уравнения необходимо задать начальные (тепловое состояние детали в начальный момент времени) и граничные условия на поверхностях, ограничивающих рассматриваемую деталь. В [5.13.1] приведена следующая классификация граничных условий, которые могут применяться для решения уравнения нестационарной теплопроводности:
-граничные условия первого рода - на поверхностях, ограничивающих деталь, задаются значе- ния температур, которые могут зависеть от координат точек границы и времени;
-граничные условия второго рода - на гранич- ных поверхностях рассматриваемой детали, задается плотность теплового потока (производная от температуры по нормали к поверхности). Плотность теплового потока так же задается в виде функции, зависящей от времени и координат точек границы;
-граничные условия третьего рода - тепловой поток задается пропорционально разности температур на границе детали и окружающей среды:
− λ |
∂T |
|
|
=α(Ò ‹ ð −Ò f ) |
|
|
|
||||
∂n |
|||||
|
|
‹ ð |
|||
|
|
в этом условии должен быть задан коэффициент теплоотдачи a и температура окружающей среды Òf; - граничные условия четвертого рода (условия сопряжения)- одновременно задается равенство
температур и тепловых потоков на границе разделения двух соседних деталей компрессора:
Ò1 ã ð = Ò2 ã ð
−λ |
∂T1 |
|
|
|
= −λ |
|
∂Ò2 |
|
|
|
|
|
|
|
|
|
|
||||
|
|
|
||||||||
1 ∂n |
|
ã ð |
|
2 |
∂n |
|
ã ð |
|||
|
|
|
|
Эти условия допускают различные модификации. Так, например, если контакт между соседними деталями не идеален, то существует скачок температуры на границе раздела деталей, т.е.
Ò1 ã ð = kÒ2 ã ð
Необходимо отметить, что граничные условия
второго рода, в силу проблематичности получения точного значения величины плотности теплового потока, редко используются при определении теплового состояния деталей компрессора.
Могут существовать и другие важные гранич- ные условия, не рассмотренные выше. Например, при теплообмене излучением тепловой поток оказывается пропорциональным разности четвертых степеней температур источника и приемника теплоты. Однако данные граничные условия крайне редко используются при определении теплового состояния деталей компрессора, поэтому здесь не рассматриваются.
В основном, при решении уравнения теплопроводности применительно к деталям компрессора используют граничные условия третьего рода. В этом случае при определении коэффициента теплоотда- чи α используют полуэмпирические зависимости. В большинстве случаев применяют безразмерный комплекс, который называют числом Нуссельта:
Nu = α l / λ
ãäå α, λ - коэффициенты теплоотдачи, теплопроводности,
l - характерный размер.
Коэффициент теплопроводности λ относится к физическим свойствам материала. Коэффициент теплоотдачи a зависит от вида и свойств движения окружающей среды.
Разделяют два вида движения окружающей среды, влияющих на величину α:
-свободное движение, когда течение окружающей среды возникает в поле массовых сил при наличии градиентов температуры;
-вынужденное движение, когда течение окружающей среды вызвано внешними причинами.
Обобщенная зависимость для определения коэффициента теплоотдачи α имеет вид:
-для чисто вынужденного движения
Nu = f1(Re,Pr),
- для свободного движения
Nu = f2(Gr,Pr),
ãäå Re, Pr, Gr - числа Рейнольдса, Прандля и Грасгофа.
Удобной и сравнительной простой зависимостью для обобщения экспериментальных данных является следующее уравнение для вынужденного течения (Nu = ÑRemPrn) или свободного (Nu = Ñ (Gr Pr)n), ãäå Ñ, m, n - константы, которые определяются экспериментальным путем. Нахождению формул по опреде-
234

Глава 5 - Компрессоры ГТД
лению числа Нуссельта для отдельных видов и классов течений окружающей среды посвящено множество работ. Так, в [5.13.2], [5.13.3] представлены формулы, которые можно использовать при определении теплового состояния деталей компрессора.
В настоящее время появляются программные продукты, в которых не требуется задавать коэффициент теплоотдачи между деталью компрессора и окружающей средой. Данный коэффициент вычисляется при совместном решении уравнения теплопроводности, определяющего тепловое состояние детали, и уравнений Навье-Стокса, описывающих течение вязкого сжимаемого газа вокруг рассматриваемой конструкции с учетом теплообмена между газом и деталями компрессора. С развитием вычислительной техники данный способ получения совместного решения теплового состояния детали и течения среды, омывающей деталь, приобретает все более широкое распространение.
С целью быстрого получения теплового состояния при определении параметров, необходимых для задания граничных условий делают различные допущения. Так течение в деталях компрессора разбивают на два вида:
-основное течение газа в проточной части компрессора;
-вторичные (все остальные).
Зачастую, необходимые для задания гранич- ных условий в основном потоке данные получают из решения уравнений, описывающих процессы в лопаточных машинах. При этом часто вводят дополнительные допущения:
-решается уравнение течения идеального газа
ñпринятыми моделями потерь;
-при больших расходах газа по проточной части пренебрегают теплообменом от деталей компрессора в проточную часть.
При определении потоков газа во вторичных течениях обычно переходят к одномерным моделям, а при условии небольших скоростей потока полагают, что окружающая среда несжимаема. Необходимо отметить, что в данных потоках условие теплообмена между деталями и окружающей средой существенно. Поэтому данный теплообмен необходимо учитывать при определении параметров вторичных течений.
5.2.4 – Выбор радиальных и осевых зазоров
В любой конструкции, имеющей движущиеся части, между подвижными и неподвижными деталями необходим зазор для обеспечения необходимой свободы перемещения.
Компрессор ГТД состоит из двух основных частей:
-статора (неподвижного корпуса);
-ротора (вращающейся части).
Применяя цилиндрическую систему координат к двигателю (осевая координата совпадает с осью двигателя), разделим зазоры в компрессоре на два вида (см. Рис. 5.2.4_1).
-осевые зазоры (между двумя соседними лопаточными венцами);
-радиальные зазоры (между рабочими лопатками и корпусом, между лопатками НА и ротором).
При рассмотрении осевых зазоров учитывается осевое смещение статора относительно ротора, а радиальных зазоров – радиальное смещение. При рассмотрении зазоров, образованных коническими поверхностями (на поверхностях меняется как осевая, так и радиальная координата), необходимо учитывать как осевое, так и радиальное смещение статора относительно ротора. Обычно в за-
Рисунок 5.2.4_1 – Зазоры в компрессоре
235

Глава 5 - Компрессоры ГТД
висимости от вида таких зазоров, их так же называют осевыми или радиальными.
Ротор и статор компрессора являются сложными конструкциями, состоящими из большого коли- чества деталей с различными характеристиками:
-массы;
-геометрии;
-материала.
Детали ротора и статора работают в различ- ных условиях:
-имеют различное тепловое состояние;
-испытывают различные нагрузки.
Все это приводит к изменению зазоров между ротором и статором во время работы двигателя. Для предотвращения задевания деталей ротора о детали статора во всем диапазоне режимов работы компрессора и исключения возможности заклинивания ротора до и после останова двигателя зазоры выбираются с учетом вышесказанного.
Для лучшего понимания процесса изменения радиальных зазоров в компрессоре рассмотрим, как ведут себя ротор и статор при запуске и остановке наземного ГТД.
При запуске двигателя растет температура
âпроточной части компрессора и изменяется тепловое состояние деталей. Заметим, что для обеспе- чения требуемого ресурса детали ротора конструируют более массивными, т.е. они обладают большей тепловой инертностью, чем статорные детали. Изза меньшей тепловой инертности деталей корпуса радиальный зазор увеличивается относительно монтажного, существующего на холодном двигателе. В процессе работы зазор перестает увеличиваться и начинает уменьшаться по мере прогрева ротора. Стабилизация зазоров наступает, когда тепловое состояние узлов компрессора становится неизменным на установившемся режиме. Помимо теплового расширения деталей ротора и статора существует вытяжка ротора от центробежных сил, которая тоже влияет на изменение радиальных зазоров, но
âзначительно меньшей степени, поэтому в данном примере мы ее не рассматриваем. При остановке двигателя корпус компрессора остывает быстрее, чем ротор, поэтому радиальный зазор уменьшается и становится меньше монтажного. Скорость изменения зазоров пропорциональна времени, за которое происходит полный останов двигателя. При резком снижении режима двигателя радиальные зазоры продолжают уменьшаться после остановки двигателя. При неправильно выбранных монтажных зазорах в таких случаях может произойти заклинивание ротора.
При выборе величины монтажных зазоров необходимо учитывать их влияние на эффективность
работы компрессора. Зазоры в значительной степени влияют на аэродинамику. Течение газа как в осевом, так и в радиальном зазоре имеет сложную трехмерную структуру. В зависимости от величины зазора меняется характер течения и, как следствие, изменяется эффективность работы компрессора. Существует оптимальная величина осевого и радиального зазоров, при которой достигается максимальная эффективность компрессора. Но даже при оптимальных зазорах всегда существуют «паразитные течения», но их вредное влияние на параметры компрессора должно быть минимизировано.
Отрицательное влияние на эффективность компрессора оказывают:
-неравномерность потока в следе за лопатками при минимальном осевом зазоре между лопатками статора и ротора;
-потери на трение при большом осевом зазоре между лопатками статора и ротора;
-расположение скачков уплотнения при взаимодействии ротора и статора в случае неоптимального осевого зазора между лопатками статора и ротора;
-перетекание газа из области повышенного давления (за лопаткой) в область пониженного (перед лопаткой) при большом радиальном зазоре (см. Рис. 5.2.4_2), при этом с уменьшением высоты лопатки усиливается влияние обратных потоков на эффективность компрессора;
образование вихревых зон на торцах лопаток из-за отсутствия сдува вихря при перетекании,
àтак же работа части пера лопатки в пристеноч- ной области при небольшой (близкой к нулю) величине радиального зазора.
Отрицательное влияние на эффективность компрессора оказывают:
-неравномерность потока в следе за лопатками при минимальном осевом зазоре между лопатками статора и ротора;
-потери на трение при большом осевом зазоре между лопатками статора и ротора;
-расположение скачков уплотнения при взаимодействии ротора и статора в случае неоптимального осевого зазора между лопатками статора и ротора;
-перетекание газа из области повышенного давления (за лопаткой) в область пониженного (перед лопаткой) при большом радиальном зазоре (см. Рис. 5.2.4_2), при этом с уменьшением высоты лопатки усиливается влияние обратных потоков на эффективность компрессора;
-образование вихревых зон на торцах лопаток из-за отсутствия сдува вихря при перетекании,
àтак же работа части пера лопатки в пристеноч- ной области при небольшой (близкой к нулю) величине радиального зазора.
236

Глава 5 - Компрессоры ГТД
Рисунок 5.2.4_2 – Характер течения в радиальном зазоре РК компрессора
Из представленного следует, что выбор оптимальных осевых и радиальных зазоров - это компромисс между эффективностью компрессора и бездефектной работой его узлов.
Оптимальная величина радиального и осевого зазора зависит от распределения как геометри- ческих, так и газодинамических параметров в ступени. Для ее определения, на основных режимах работы компрессора при различных значениях величин зазоров проводят расчеты течения вязкого газа в трехмерной постановке с учетом взаимодействия статора и ротора. На основании выполненных расчетов выбирают оптимальное значение осевого и радиального зазоров при работе компрессора.
Как уже говорилось ранее, в процессе работы двигателя происходит изменение зазоров в компрессоре. На Рис. 5.2.4_3 представлено изменение радиального зазора в РК 11 ступени КВД по полетному циклу работы двигателя ПС-90А. В общем случае величина зазора при работе компрессора определяется по формуле:
Z = ZÌ + δZC - δZP
ãäå Z – величина зазора в рассматриваемый момент работы компрессора;
ZÌ – величина монтажного зазора;
δZC – изменение положения детали статора при работе компрессора в осевом направлении (при определении осевого зазора);
δZP – изменение положения детали ротора при работе компрессора в радиальном направлении (при определении радиального зазора) .
Из представленной формулы следует, что при работе компрессора на основных режимах полу- чить величину зазора близкую к оптимальной можно двумя способами:
-первый способ получил название пассивного регулирования зазоров. Он заключается в том,
чтобы величина монтажного зазора ZÌ была близка к оптимальному значению, а изменение смеще-
ния статора относительно ротора (δZC - δZP) на всех режимах работы компрессора не происходило.
-второй способ получил название активного регулирования зазоров. Он заключается в том, что-
бы на заданных режимах работы компрессора
обеспечить дополнительное изменение δZC èëè δZP с целью приблизить величину суммарного зазора к оптимальному значению.
При пассивном регулировании зазоров особое внимание уделяется подбору материалов, выбору геометрии деталей ротора и статора, введению дополнительных конструктивных элементов (тепло-
237

Глава 5 - Компрессоры ГТД
Рисунок 5.2.4_3 – Изменение величины радиального зазора в РК 11 ступени КВД по полетному циклу двигателя ПС-90А
изоляционные экраны, воздушные прослойки и т.д.), позволяющих выровнять тепловую инерционность (время прогрева) деталей ротора и статора.
При активном регулировании зазоров создается специальная система, которая на заданных режимах работы двигателя воздействует на детали ротора или статора. Так как, в основном, детали статора более подвержены изменению, то обычно воздействуют на их элементы.
Существует два основных типа нагрузок, от действия которых может измениться величина радиального зазора:
1) Ïðè тепловой нагрузке на детали корпуса компрессора направляется воздушный поток определенной температуры, который изменяет тепловое состояние детали, соответственно изменяется тепловое расширение статора и радиальный зазор в ступени. При этом воздействовать на корпус можно двумя способами. Первый - на основных режимах работы компрессора уменьшить радиальный зазор путем охлаждения деталей статора воздухом, отбираемым от предыдущих ступеней. Второй - на неосновных режимах работы компрессора увели-
чить радиальный зазор путем нагревания корпуса компрессора воздухом, отбираемым от последующих ступеней.
В настоящее время предпочтение отдается первому способу.
На Рис. 5.2.4_4 представлена конструкция заднего корпуса КВД двигателя ПС-90А с активным регулированием радиальных зазоров путем охлаждения воздухом, отбираемым из-за подпорных ступеней. Стрелками показаны направления течения охлаждающего воздуха. Воздух из-за подпорных ступеней по трубопроводу подается к патрубку в корпусе обдува 1. После этого воздух попадает в кольцевой коллектор, образуемый корпусом обдува и закрепленным на нем тонкостенным кожухом 2 с сетью отверстий 3. Через эти отверстия и осуществляется непосредственный обдув корпуса компрессора 4. Далее воздух сбрасывается в наружный контур через отверстия 5.
2) При регулировании с помощью газовых нагрузок над деталью корпуса компрессора создается воздушная полость, наполняемая воздухом с повышенным давлением. На основных режимах
238
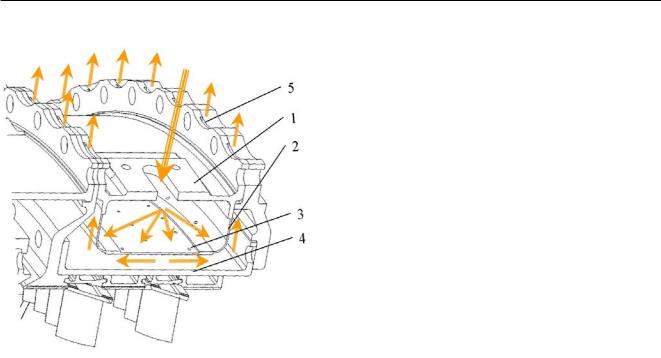
Глава 5 - Компрессоры ГТД
Рисунок 5.2.4_4 – Корпус компрессора дв. ПС-90А с каналами для активного регулирования радиальных зазоров 1 - корпус обдува; 2 – кожух; 3 -
отверстия обдува; 4 - корпус компрессора; 5 - отверстия для сброса воздуха в наружный контур
работы в эту полость подается воздух высокого давления. Это приводит к тому, что корпуса компрессора от газовых сил расширяется меньше, и величина радиального зазора в ступени компрессора уменьшается.
Описанный способ регулирования зазоров можно реализовать в конструкции, подобной представленной на Рис. 5.2.4_4, только в ней не будет кожуха 2 и выпускных отверстий 5.
Преимущество этого способа в том, что воздух, заполняющий полость над корпусом, остается в системе, а не сбрасывается в наружный колнтур, как в случае с дополнительным охлаждением корпусом. С другой стороны, эффективность способа гораздо ниже. Для увеличения эффективности, необходимо уменьшать жесткость корпуса, например, делать его более тонким, что может привести к уменьшению ресурса. Однако такой способ регулирования зазоров может получить развитие в случае создания новых жаропрочных материалов с небольшой жесткостью и высокими прочностными характеристиками.
Таким образом, выбор зазоров в компрессорах осуществляется в два этапа:
- на первом этапе, на стадии выполнения про-
ектировочных газодинамических расчетов определяются «оптимальные» величины зазоров. В дальнейшем, при доводке двигателя, размеры зазоров могут быть уточнены;
- на втором этапе монтажные зазоры, конструкция и геометрия деталей компрессора определяются таким образом, чтобы при работе на основных режимах работы величина зазора была близка к оптимальной и при этом не допускала задеваний во всем диапазоне работы компрессора. Последнее требование подразумевает, что минимальная величина зазора должна превышать величину, определяемую действием всевозможных факторов, способных ее изменить (допуск на изготовление и сборку; люфт подшипников; нагрузки от воздействия на двигатель со стороны самолета, и т.д.). При этом минимальная величина зазора определяется с учетом всех возможных циклов работы двигателя.
На изготовление и сборку деталей существуют допуски, из-за которых величина зазора в компрессоре непостоянна в окружном направлении. Кроме этого, при работе компрессора из-за неравномерности прикладываемых нагрузок происходит дополнительная овализация деталей и смещение осей деталей ротора и статора. Для уменьшения изменения радиального зазора в окружном направлении на корпусах над рабочими лопатками наносится легковырабатываемое покрытие. Кроме этого, для улучшения приработки по торцам лопаток профиль пера на торцах утончают.
Заключение о правильности назначенных зазоров делают по результатам осмотра газовоздушного тракта компрессора после проведения испытаний, а так же измерением радиальных и осевых зазоров при работе компрессора.
5.3 – Конструктивные и силовые схемы осевых компрессоров
Осевые компрессоры делятся на три группы: одно-, двухили трехкаскадные.
В однокаскадных компрессорах (см. Рис. 5.3_1) ротор 1 расположен на двух опорах – с роликовым подшипником, воспринимающим радиальные нагрузки, и радиально-упорным шариковым подшипником, фиксирующим положение ротора относительно статора 2. При этом передача усилий от передней опоры происходит через радиальные стойки 3 входного корпуса, а от задней – по корпусу КС через спрямляющий аппарат 5 последней ступени компрессора или стойки КС.
При сравнительной простоте конструкции однокаскадные компрессоры с большой степе-
239

Глава 5 - Компрессоры ГТД
Рисунок 5.3_1 – Однокаскадный компрессор двигателя Rolls-Royce (Печатается с разрешения Rolls-Royce plc)
1 - ротор компрессора; 2 - статор; 3 - входной корпус с передней опорой и неподвижным обтекателем; 4 - спрямляющий аппарат компрессора
Рисунок 5.3_2 - Двухкаскадный компрессор ТРД двигателя Rolls-Royce Tyne (Печатается с разрешения Rolls-Royce plc)
1 - КНД; 2 – КВД; 3 - разделительный корпус
240
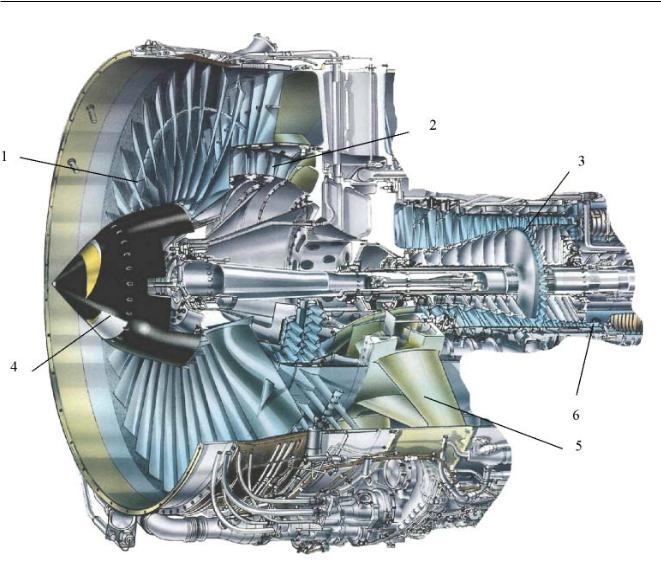
Глава 5 - Компрессоры ГТД
Рисунок 5.3_3 - Двухкаскадный компрессор ТРДД с большой степенью двухконтурности (двигатель ПС-90А) 1 – вентилятор; 2 - подпорные ступени; 3 – КВД; 4 - вращающийся обтекатель; 5 - разделительный корпус; 6 - спрямляющий аппарат КВД
нью сжатия, имеющие, соответственно, большое число ступеней, для обеспечения газодинамической устойчивости на всех режимах работы двигателя требуют сложных систем регулирования. Например, использования поворотных направляющих лопаток, систем перепуска воздуха, что в свою очередь снижает надежность и экономичность работы компрессора. Более подробно вопросы регулирования компрессора будут рассмотрены в разделе 5.6.
В настоящее время большее распространение получили двух- и трехкаскадные схемы компрессоров. Двухкаскадный компрессор состоит из двух осевых компрессоров 1 и 2 соответственно низкого давления , расположенного впереди, и высокого давления, расположенного за ним (см. Рис. 5.3_2). Двухкаскадный компрессор не имеет жесткой связи между двумя роторами, что позволяет каждому из роторов вращаться с оптимальной для них час-
тотой. Это оказывает положительное влияние на величину запасов газодинамической устойчивости компрессора.
В то же время конструктивно компрессор становится сложнее. Так длинный вал каскада низкого давления зачастую нуждается в дополнительной, межвальной, опоре. Обеспечение нормальной работы подшипника в такой опоре становится сложной инженерной задачей. В двухкаскадных компрессорах современных двигателей, спроектированных с применением новейших методов аэродинамических и прочностных трехмерных расче- тов, стало возможным уменьшить число ступеней за счет увеличения работы на каждую ступень. Это позволило уменьшить общую длину компрессора и избежать этой проблемы.
Для увеличения запасов газодинамической устойчивости ВНА, а также НА (обычно с первой
241

Глава 5 - Компрессоры ГТД
Рисунок 5.3_4 - Трехкаскадный компрессор ТРДД с большой степенью двухконтурности двигателя Rolls-Royce RB211 (Печатается с разрешения Rolls-Royce plc)
1 - вентилятор; 2 - компрессор среднего давления; 3 - компрессор высокого давления; 4 - силовые стойки разделительного корпуса, совмещенные с лопатками спрямляющего аппарата вентилятора; 5 - вал ротора низкого давления; 6 - вал ротора среднего давления; 7 - вал ротора высокого давления; 8 - опора вентилятора (межвальная); 9 - опора компрессора среднего давления; 10 - опора компрессора высокого давления
по четвертую ступени) КВД делают с поворотны- |
компрессоров - через радиальные стойки входного |
ми НА. В двигателях, работающих в широком ди- |
корпуса. Иногда для уменьшения габаритов и мас- |
апазоне скоростей на входе, может применяться по- |
сы эту функцию могут выполнять лопатки непод- |
воротный ВНА КНД (см. Рис. 5.5.1.1_1). |
вижного ВНА или неподвижной части поворотно- |
В двухкаскадных компрессорах ТРД (см. |
го ВНА. Передача усилий от задней опоры |
Рис. 5.3_2) и ТРДД с малой степенью двухконтур- |
осуществляется по корпусу промежуточному (раз- |
ности (m = 0,2…2) КНД обычно состоит из трех - |
делительному) 3 через профилированные силовые |
пяти ступеней. Передача усилий от передней опо- |
стойки. |
ры чаще всего происходит, как у однокаскадных |
|
242

Глава 5 - Компрессоры ГТД
Разделительный корпус ТРДД является силовым элементом двигателя, который разделяет потоки наружного и внутреннего контуров. Кроме того, на нем располагают узлы крепления двигателя к самолету.
Âдвухкаскадных компрессорах ТРДД с большой степенью двухконтурности (m > 4) (см. Рис. 5.3_3) КНД состоит из одной вентиляторной ступени 1. В КНД могут быть включены от одной до четырех (редко – до семи) так называемых подпорных ступеней 2 для повышения суммарной степени сжатия внутреннего контура компрессора.
Поскольку от ВНА в данном случае отказываются из-за его громоздкости, усилия от обеих опор передаются по корпусу разделительному че- рез профилированные силовые стойки. В некоторых случаях целесообразно силовые стойки разделительного корпуса совместить с лопатками спрямляющего аппарата вентилятора. Обычно эту схему применяют в двигателях с коротким наружным контуром или в трехкаскадных двигателях (см. Рис. 5.3_4).
Âсвязи с тем, что ВНА отсутствует, обтекатель 4 крепят непосредственно к диску вентилятора. КВД 3 (см. Рис. 5.3_3) состоит обычно из пяти…десяти ступеней. В редких случаях их число достигает двенадцать…четырнадцать. Усилия от передней опоры передаются через профилированные стойки разделительного корпуса 5, а от задней – по корпусу КС через спрямляющий аппарат 6 последней ступени компрессора или стойки КС.
Конструктивно трехкаскадный компрессор ТРДД представлена на Рис. 5.3_4. Она представляет собой три отдельных компрессора работающих с собственными частотами вращения и находящихся на отдельных валах и опорах:
- вентилятор 1 (КНД для ТРДД с малой степенью двухконтурности);
- ÊÑÄ 2; - ÊÂÄ 3.
Такая конструкция позволяет повысить запасы устойчивой работы компрессора. Количество ступеней вентилятора – одна, КНД – три…пять, КСД – четыре…шесть, КВД – четыре…восемь.
Конструктивно трехкаскадный компрессор еще сложнее, чем двухкаскадный. Для дополнительного увеличения запасов газодинамической устойчивости ВНА КСД, ВНА КВД, а также НА первой…третьей (обычно) ступеней КВД делают поворотными.
5.4 – Роторы осевых компрессоров
Основными деталями ротора являются рабо- чие лопатки 1 (см. Рис. 5.4_1), диски (или барабан) 2, цапфы (или вал) 3 и 4 и подшипники 5 и 6. Ротор осевого компрессора является подвижным узлом, совершающим вращательное движение. Частота вращения роторов современных осевых компрессоров может достигать 15000 об/мин, а окружные скорости на наружном диаметре - 400 м/с. На таких оборотах ротор испытывает высокие нагрузки, которые и определяют тип его конструкции.
5.4.1 – Типы роторов осевых компрессоров
По конструктивному исполнению роторы осевых компрессоров могут быть следующих типов:
-барабанного;
-дискового;
-смешанного.
Рисунок 5.4_1 - Ротор компрессора двигателя Honeywell TFE731-60 (Материал любезно предоставлен компанией Honeywell)
1 - рабочая лопатка; 2 - диск компрессора; 3 - цапфа передней опоры; 4 - цапфа задней опоры; 5 - шарикоподшипник; 6 – роликоподшипник; 7 - торцевые треугольные шлицы; 8 - центральный стяжной болт; 9 - гайка стяжного болта
243
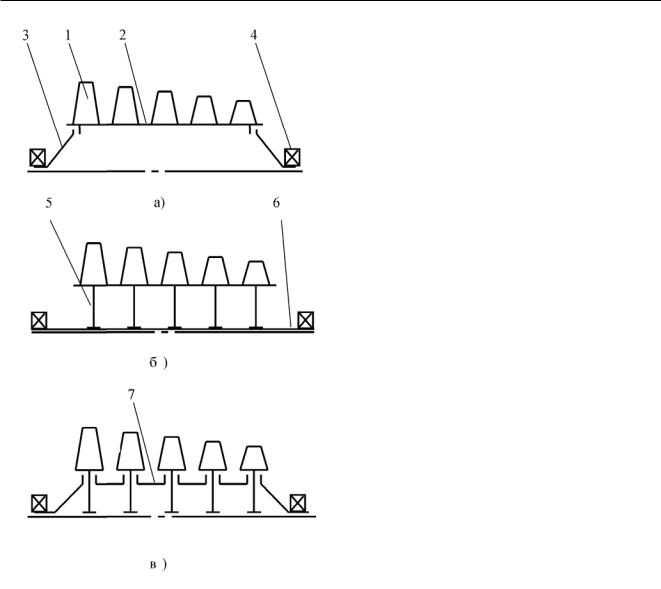
Глава 5 - Компрессоры ГТД
Рисунок 5.4.1_1 – Типы роторов осевых компрессоров:
а) барабанный; б) дисковый; в) смешанный
1 - рабочая лопатка; 2 - барабан компрессора; 3 - крышки барабана с цапфами опор; 4 – подшипники; 5 - диск компрессора; 6 - вал компрессора; 7 - барабанные секции
Схема ротора барабанного типа показана на Рис. 5.4.1_1а. Несколько рядов рабочих лопаток 1 закрепляются на цилиндрическом или коническом барабане 2, представляющем собой механически обработанную поковку из алюминиевого сплава, титана или стали. Две крышки 3 закрывают барабан с торцев и имеют цапфы, которыми ротор опирается на подшипники 4. Крутящий момент к каждой ступени передается через стенку барабана.
Достоинствами ротора барабанного типа являются:
-простота конструкции;
-низкая удельная масса;
-большая изгибная жесткость;
-высокая критическая частота вращения;
-высокая вибрационная стойкость.
Примечание: Критической частотой враще-
ния называют частоту вращения, при которой прогибы ротора становятся бесконечно большими, о чем свидетельствует резкий рост вибрации в опорах ротора.:
ωÊÐ2 = k / mÄ,
ãäå ωÊÐ – критическая частота вращения; k – изгибная жесткость вала;
mÄ, – масса диска.
Остаточный дисбаланс, неизбежный даже после тщательной балансировки, неравномерный прогрев и вытяжка дисков и лопаток, а также некоторые другие причины вызывают смещение центра массы рабочего колеса (колес) относительно геометрической оси во время работы двигателя. Роторы барабанного типа получают сваркой отдельных секций, или механической обработкой из цельной заготовки.
К недостаткам ротора барабанного типа следует отнести:
-сравнительно невысокую несущую способность барабана;
-низкую рабочую окружную скорость – не более 200 м/с.
Роторы барабанного типа для авиационных двигателей были заимствованы из конструкций компрессоров для паровых турбин.
Ротор дискового типа (см. Рис. 5.4.1_1б) имеет соединенные с валом 6 диски 5, на периферии которых крепятся рабочие лопатки 1. Диски стянуты в единый пакет гайками, которые накручены на вал. Достоинствами ротора дискового типа являются:
-большая несущая способность дисков;
-высокая рабочая окружная скорость - до 400 м/с.
Ступени компрессора с дисковыми роторами являются высоконапорными и применяются в ГТД
ñбольшими степенями повышения давления воздуха. Крутящий момент к каждой ступени передается через вал. Недостатками ротора дискового типа являются:
-сравнительно небольшая изгибная жест-
кость;
244

Глава 5 - Компрессоры ГТД
Рисунок 5.4.1_2 – Ротор осевого компрессора смешанного (барабанно-дискового) типа двигателя Rolls-Royce RB162-86 (Печатается с разрешения Rolls-Royce plc)
-невысокая критическая частота вращения;
-высокая удельная масса;
-сложность конструкции.
Снижение изгибной жесткости ротора дискового типа в сравнении с ротором барабанного типа приводит к снижению критической частоты. Для повышения критического числа оборотов увеличи- вают потребное сечение вала ротора, но при этом увеличивается и масса компрессора.
Конструкцией, сочетающей в себе достоинства роторов барабанного и дискового типа, является ротор смешанного типа (см. Рис. 5.4.1_1в и 5.4.1_2).
В данном случае отдельные секции, имеющие диски 5 и барабанные секции 7, соединяются между собой. Причем соединение делается на таком радиусе, где окружная скорость невелика и допускается по условиям прочности барабана.
Достоинствами ротора барабанно-дискового типа являются:
-сравнительно большая жесткость;
-высокая критическая частота вращения;
-большая несущая способность дисков;
-высокая рабочая окружная скорость - до 400 м/с.
Диапазоны рабочих частот вращения роторов всех типов могут лежать ниже критической частоты - такой ротор называется «жестким». Если же рабочие частоты больше критического значения - такой ротор называют «гибким». Представленные типы роторов бывают как жесткие, так и гибкие.
5.4.2 – Конструкция роторов осевых компрессоров
Конструкция ротора должна обеспечить выполнение трех основных функций:
-передачу крутящего момента;
-передачу осевых усилий;
-взаимное центрирование элементов конструкции ротора.
В зависимости от типа конструкции ротора выполнение этих функций может осуществляться различными способами. Рассмотрим типовые решения, применяемые в конструкциях роторов многоступенчатых осевых компрессоров.
На Рис. 5.4.2_1 показан ротор барабанно-дис- кового типа, состоящий из вала 1 и расположенных на нем тринадцати рабочих колес 2. Между рабочими колесами установлены промежуточные
Рисунок 5.4.2_1 - Ротор барабанно-дискового типа со шлицевым валом двигателя ПС-90А 1 - вал компрессора; 2 - рабочее колесо; 3 - промежуточное кольцо; 4 - гайка ротора компрессора
245
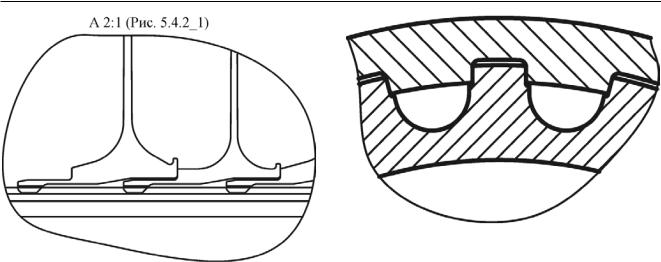
Глава 5 - Компрессоры ГТД
Рисунок 5.4.2_3 - Соединение дисков с валом прямоРисунок 5.4.2_2 - Диски со шлицами на выносных угольными шлицами
элементах
кольца 3, образующие барабан, стянутый гайкой 4. Передача крутящего момента от вала к дискам и центрирование дисков осуществляется шлицами. Для этого, в основном, используются шлицы двух типов:
-эвольвентные;
-трапециевидные.
Применение эвольвентных шлицев менее распространено, т. к. лучшее центрирование обеспе- чивают прямоугольные шлицы (см. Рис. 5.4.2_3), где центрирование осуществляется по радиальным (боковым) поверхностям. В таких шлицах центровка будет сохраняться независимо от тепловых и силовых деформаций ступицы.
Шлицы являются концентраторами напряжений. Для выведения из зоны действия растягивающих усилий от центробежных сил, шлицевое соединение вала с диском выносят на некоторое расстояние от ступицы диска. Такие конструкции получили название - конструкции на выносных элементах (см. Рис. 5.4.2_2).
Пакет дисков стянут на шлицевом участке вала с двух сторон гайками 4 (см. Рис. 5.4.2_1). При этом монтажное усилие стяжки пакета дисков выбирается таким образом, чтобы при нагреве ротора в рабо- чих условиях не происходило снижение усилия затяжки до нулевого значения (не происходило «раскрытие» ротора).
Для дополнительного демпфирования дисков и организации проточной части между ободами дисков устанавливают промежуточные кольца. Это существенно повышает изгибную жесткость ротора. Конструкция промежуточных колец или иных проставных элементов ободной части ротора зави-
сит от принятой при проектировании формы проточной части.
Проточная часть по типу образующих ее поверхностей может быть двух видов:
-«гладкой»;
-«негладкой».
Проточная часть называется «гладкой», если наружные поверхности промежуточных колец
èдисков образуют в меридиональном сечении плавные линии без уступов (см. Рис. 5.4.2_1). Проточная часть называется «негладкой» если на наружной поверхности промежуточных колец имеются выступающие или утопающих элементы воздушных уплотнений (см. Рис. 5.4.2_4).
Возможны варианты конструкции ротора без центрального шлицевого вала. На Рис. 5.4.2_4 показан ротор того же, что и на Рис. 5.4.2_1 компрессора, но другого типа - без внутреннего шлицевого вала. Передние десять дисков из титанового сплава объединены в сварную секцию. Центрирование дисков 1 при сборке обеспечивается с помощью цилиндрических посадочных участков 2, которые после сварки срезаются. Сварной шов 3 должен контролироваться, а вся сварная секция дисков должна быть термообработана для снятия внутренних напряжений.
Êсварной титановой секции 4 призонными болтами 7 крепятся стальные диски последних ступеней 5 с цапфами 6. Такой ротор имеет меньшую массу и большую поперечную жесткость, чем ротор на Рис. 5.4.2_1. На практике применяются и другие конструкции роторов компрессоров:
- Рис. 5.4_1 - передача крутящего момента
èцентрирование дисков с помощью торцовых тре-
246
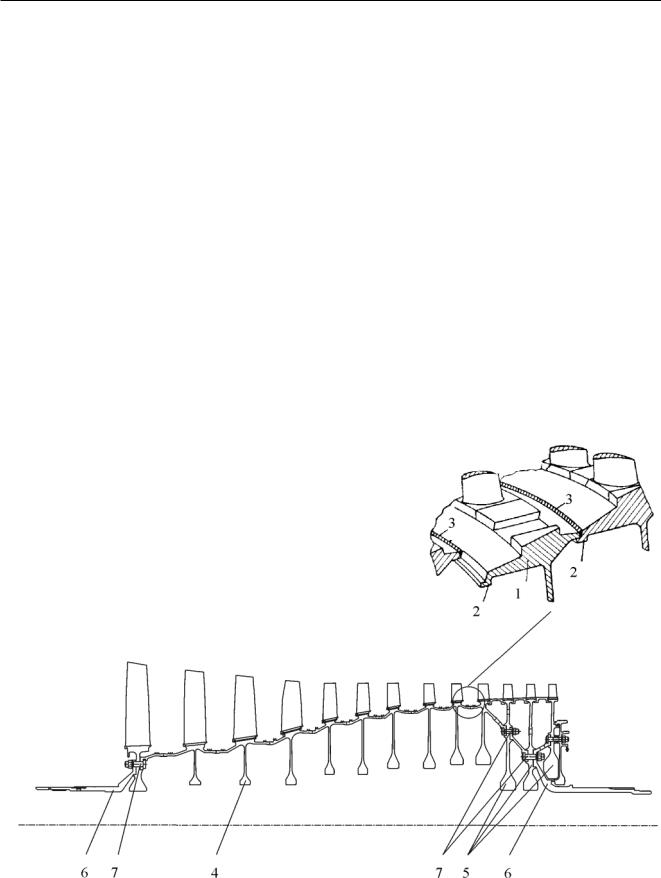
Глава 5 - Компрессоры ГТД
угольных шлицев 7, стяжка секций ротора цент- |
новые пути в решении этой непростой задачи. Так, |
ральным стяжным болтом 8; |
например, использование в роторе любого типа |
- Рис. 5.4.2_5 - передача крутящего момента |
моноколес (блисков) (см. Рис. 5.4.2_6) позволяет |
длинными стяжными болтами 2, скрепляющими па- |
добиться снижения массы конструкции до 25% от |
кет дисков ротора 1; центрирование дисков и прос- |
исходного и повысить критическое число оборотов. |
тавок 3 осуществляется с помощью цилиндрических |
Моноколесо - это рабочее колесо, в котором лопат- |
призонных участков на болтах и отверстий, выпол- |
ки выполнены с диском за одно целое. |
ненных в дисках и проставках, развернутых совме- |
Дальнейшим развитием этой идеи являются |
стно. Одновременное прижатие по стыкам осуществ- |
роторы, изготовленные с применением техноло- |
ляется с помощью распорных втулок 4, надетых на |
гии «блинг». «Блинг» - это рабочее кольцо, в ко- |
болты. |
тором лопатки выполнены с диском за одно целое |
Одной из главных задач при проектировании |
(см. Рис. 5.4.2_7). По внутренней поверхности та- |
роторов является сочетание минимальной массы |
кое кольцо армировано металлокомпозитной мат- |
конструкции с максимальным ресурсом и надеж- |
рицей, которая повышает его несущую способность. |
ностью. Традиционные конструкции роторов на |
Армирование производится методом диффузионной |
современном этапе практически исчерпали свой |
сварки. Подобная схема изготовления рабочих колес |
ресурс в области снижения массы. Единственным |
позволит на новом этапе развития вернуться к кон- |
путем остается использование новых легких мате- |
струкции ротора барабанного типа, избежав при этом |
риалов, включая интерметаллиды. |
таких его недостатков, как низкая допустимая рабо- |
В то же время современное развитие техноло- |
чая окружная скорость и сравнительно невысокая |
гий резания, диффузионной сварки и т.п. открыло |
несущая способность барабана. |
Рисунок 5.4.2_4 - Ротор барабанно-дискового типа со сварной титановой секцией 1 - титановый диск компрессора; 2 - цилиндрический посадочный участок; 3 - сварной
шов; 4 - сварная титановая секция; 5 - стальной диск компрессора; 6 – цапфа вала; 7 - призонные болты
247
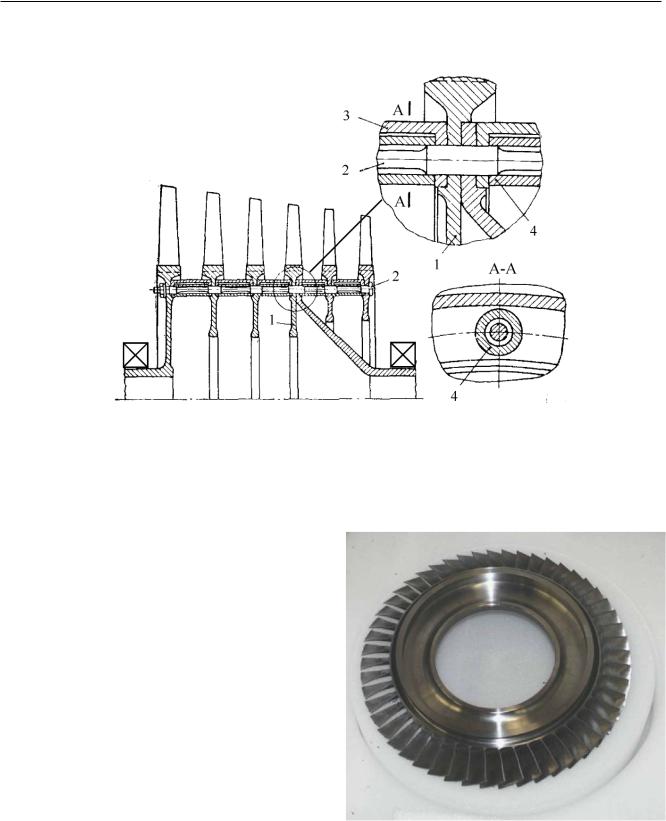
Глава 5 - Компрессоры ГТД
Рисунок 5.4.2_5 - Передача крутящего момента в роторе длинными стяжными болтами 1 - диск компрессора; 2 - стяжной болт; 3 - кольцевые проставки; 4 - распорная втулка
Отдельно следует остановиться на отличиях, присущих роторам КНД ТРДД с большой степенью двухконтурности или, как их ещ¸ называют, роторам подпорных ступеней (см. Рис. 5.4.2_8).
Такие роторы преимущественно барабанного типа. Отдельные диски соединяют между собой болтами (см. Рис. 5.4.2_8a). Болтовое соединение дисков между собой используется обычно при двухступенчатой конструкции. При увеличении количества ступеней ротор выполняют сварным (см. Рис. 5.4.2_8б) или из цельной кольцевой заготовки (см. Рис. 5.4.2_8в). В последнем случае для установки рабочих лопаток чаще всего применяют кольцевой замок, поскольку выполнение лопаточных пазов других типов связано с технологи- ческими сложностями.
Крутящий момент на ротор подпорных ступеней передают как непосредственно с вала НД (см. Рис. 5.4.2_9a), так и через рабочее колесо вентилятора (см. Рис. 5.4.2_9б). В последнем случае рабочие лопатки вентилятора необходимо монтировать в колесо после установки ротора КНД, что создает определенные неудобства при сборке вентилятора и при замене модуля КНД в эксплуатации в случае необходимости.
Рисунок 5.4.2_6 – Моноколесо (блиск) осевого компрессора
248
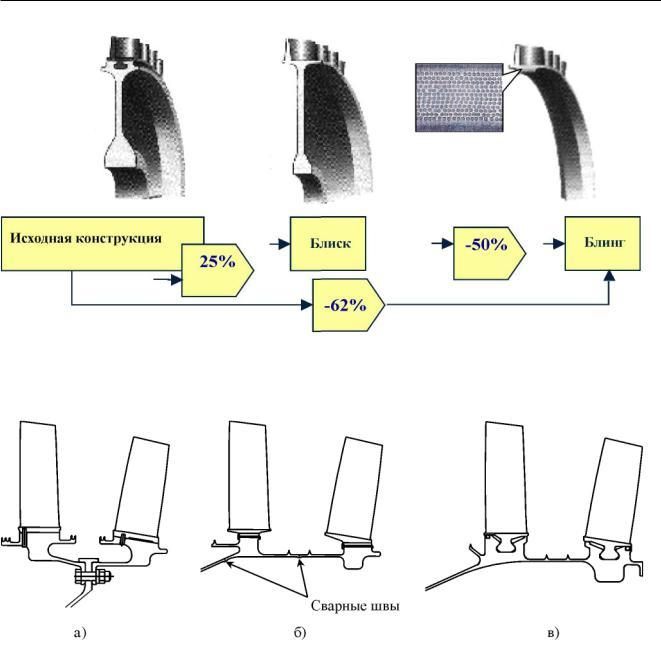
Глава 5 - Компрессоры ГТД
Рисунок 5.4.2_ 7 – Снижение массы рабочих колес оптимизацией их конструкции (Материал любезно предоставлен компанией Snecma Moteurs)
Рисунок 5.4.2_8 - Варианты изготовления роторов подпорных ступеней а) с болтовым соединением; б) сварной; в) из цельной заготовки
5.4.3 – Рабочие лопатки компрессора
Рабочие лопатки - одни из самых ответственных и массовых деталей двигателя, работающие в сложных условиях. В процессе работы на них действуют инерционные и аэродинамические силы, вызывающие напряжения растяжения, изгиба и кручения при высокой температуре (для компрессора 300…800°С). Кроме того, лопатки испытывают переменные напряжения от вибрационных нагрузок, амплитуда и частота которых изменяется в широких пределах.
Лопатки подвержены значительному износу в процессе эксплуатации - по торцу пера от задевания о прирабатываемое покрытие рабочих колец, по кромкам - вследствие попадания посторонних предметов. Поломка лопаток приводит к отказу двигателя в целом, поэтому в процессе эксплуатации их периодическим осматривают.
Надежность лопаток зависит не только от их конструктивной прочности, но и от применяемой технологии их изготовления, которая влияет на качество поверхностного слоя.
249

Глава 5 - Компрессоры ГТД
Рисунок 5.4.2_9 - Передача крутящего момента на ротор подпорных ступеней
а) непосредственно с вала НД в двигателе International Aero Engine (I.A.E) V2500-D5; б) через рабочее колесо вентилятора в дв. Pratt&Witney PW6000
1 - вал НД; 2 - ротор подпорных ступеней; 3 - рабочее колесо вентилятора
5.4.3.1 – Требования к рабочим лопаткам
При проектировании и изготовлении рабочих лопаток должны быть обеспечены, помимо общих требований к компрессору (см. раздел 5.1), ряд специфических требований:
-относительно высокая точность исполнения линейных и угловых размеров профиля и замка для обеспечения одинаковых скоростей течения воздушного потока, давлений и температур в каждом лопаточном канале;
-относительно низкая шероховатость обработки пера (Ra = 0,08…1,6 мкм) для уменьшения потерь трения воздуха при обтекании пера лопатки и увеличения усталостной прочности;
-отсутствие концентраторов напряжений, особенно в переходе пера к хвостовику;
Конструкции лопаток компрессора разнообразны. Их параметры (например, размеры профиля и качество поверхности) могут изменяться
âшироком диапазоне в зависимости от конкретного двигателя и его назначения. В то же время любая рабочая лопатка (см. Рис. 5.4.3.1_1) имеет профильную часть (перо) 1, находящуюся в потоке воздуха и замковую часть (хвостовик) 2, предназначенную для ее крепления и передачи усилий от лопатки к ротору. Форма и размеры пера определяются на основании аэродинамического расчета с учетом обеспечения статической
èдинамической прочности. Условия работы лопаток компрессоров определяют требования к материалам, из которых они изготавливаются. Для изготовления лопаток компрессора, в основном, используются коррозионно-стойкие и теплостойкие хромистые стали и сплавы, жаропрочные сплавы. Широко применяются титановые сплавы, обладающие малой удельной массой, однако сфера их применения ограничена невысокими по сравнению со сталями рабочими температурами. Возможно применение алюминиевых сплавов
èкомпозиционных материалов на первых ступенях компрессора.
5.4.3.2 – Требования, предъявляемые к соединениям
Соединения лопаток 3 с дисками 4 (см. Рис. 5.4.3.1_1) должны удовлетворять следующим требованиям:
-обеспечивать размещение необходимого количества лопаток в диске;
-обеспечивать необходимую прочность и одинаковую жесткость крепления всех лопаток в колесе при минимальной массе хвостовика;
-обеспечивать необходимую точность установки в диске и неизменность их положения при работе;
-обеспечивать простоту монтажа и демонтажа лопаток.
250
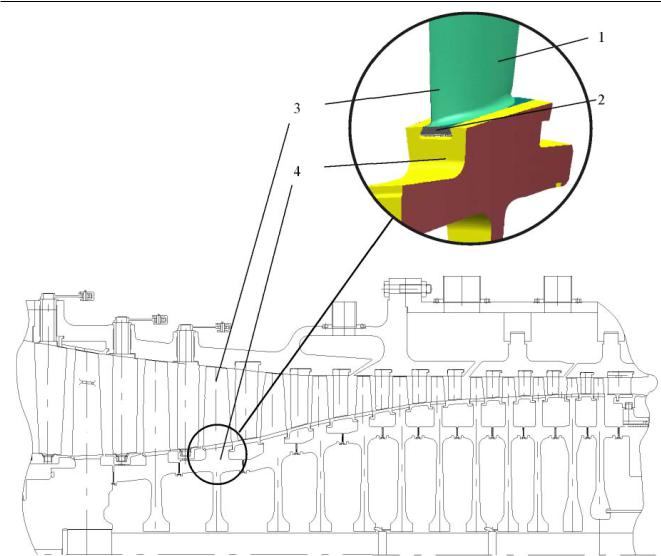
Глава 5 - Компрессоры ГТД
Рисунок 5.4.3.1_1 – Cоединение лопатки с диском
1 – перо; 2 – хвостовик; 3 - лопатка рабочая компрессора; 4 - диск
Хвостовики лопаток и пазы в диске изготавливают протяжкой, фрезерованием или точением.
5.4.3.3 – Конструкции соединения лопаток с дисками
В компрессоре наиболее распространено соединение лопаток с дисками типа «ласточкин хвост» (см. Рис. 5.4.3.3_1). В данной конструкции хвостовик лопатки и паз в диске в сечении, перпендикулярном оси паза, имеют трапециевидный профиль (форму равнобедренной трапеции). Хвостовики типа «ласточкин хвост» могут иметь плоские (см. Рис. 5.4.3.3_1а) и кольцевые рабочие поверхности (см. Рис. 5.4.3.3_1б).
Переход от профильной части лопатки к замку может осуществляться напрямую, и тогда проточная часть формируется совокупностью лопаток и наружной поверхности обода диска.
В том случае, когда угол наклона линии проточной части превышает 5…10°, хвостовик лопатки располагают горизонтально, а перо соединяют с хвостовиком через промежуточный элемент (см. Рис. 5.4.3.3_2) – ножку 1. Ножка позволяет значительно разгрузить хвостовик лопатки. Между ножкой и пером размещают полку 2, совокупность которых и формирует проточную часть.
Для широкохордных рабочих лопаток вентилятора могут применяться вставки между лопатками (см. Рис. 5.4.3.3_3).
На Рис. 5.4.3.3_4 показаны основные геометри- ческие параметры хвостовика типа «ласточкин хвост» с плоскими рабочими поверхностями. Шероховатость рабочих поверхностей Ra = 0,8…1,6 мкм. Посадка в замковом соединении может быть с зазором 0,01…0,04 мм или жесткой с натягом до 0,015 мм.
Посадка лопаток в диск с зазором применяет-
251
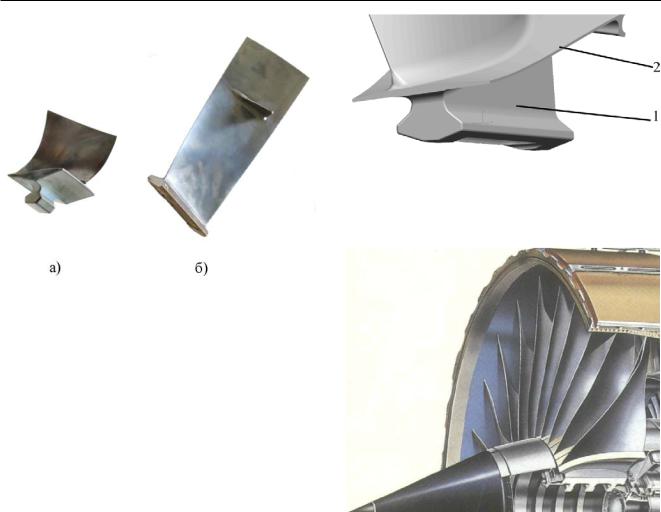
Глава 5 - Компрессоры ГТД
Рисунок 5.4.3.3_1 – Лопатки с хвостовиками типа «ласточкин хвост» а) с кольцевыми рабочими по-
верхностями; б) с плоскими рабочими поверхностями
ся наиболее часто. Она позволяет осуществлять легкий монтаж и демонтаж лопаток. Посадка с зазором допускает небольшую качку лопаток в окружном направлении и тем самым демпфирует колебания лопаток силами трения, возникающими в соединении.
Для демпфирования колебаний лопаток и облегчения сборки - разборки также применяют покрытие рабочих поверхностей хвостовика серебром или медью толщиной 0,003…0,005 мм.
Для отстройки от резонансов применяется посадка с натягом. Это повышает собственные ча- стоты колебаний лопаток. Набольшая величина натяга в соединении выбирается из условия непревышения допустимых напряжений.
Для предотвращения перемещений лопатки вдоль паза в диске при работе двигателя ее необходимо фиксировать. Фиксация лопаток осуществляется несколькими способами:
-радиальными штифтами (см.Рис. 5.4.3.3_5а). Для фиксации радиальными штифтами отверстия
âрабочих лопатках 1 и диске 2 выполняются отдельно в каждой детали. После сборки в рабочее колесо, совместив отверстия в лопатках и в диске,
âних вставляют втулку 4 со штифтом 3. После чего загибают усик контровочной втулки, фиксируя тем самым штифт от выпадывания.
-осевыми штифтами (см. Рис. 5.4.3.3_5б). Для фиксации осевыми штифтами после сборки рабо- чего колеса на границе между хвостовиком рабо- чей лопатки 1 и дном паза в диске 2 выполняют резьбовое отверстие, в которое устанавливают резьбовой штифт 5, который фиксируется от вы-
Рисунок 5.4.3.3_2 – Хвостовик широкохордной лопатки 1 - хвостовик; 2 - лопатка
Рисунок 5.4.3.3_3 – Вставки между лопатками вентилятора двигателя Rolls-Royce Trent700
падывания следующим рабочим колесом. Этот способ не ремонтопригоден и, кроме того, резьбовое отверстие является концентратором напряжений, что отрицательно сказывается на усталостной прочности лопатки и диска.
-контровочными пластинами или проволокой (см. Рис. 5.4.3.3_6). В дне лопаточного паза диска 2 заранее выполняют специально спрофилированные пазы 5 (или отверстие 6) для постановки контровочной пластины 3 (контровочной проволоки 4).
Âпроцессе сборки рабочего колеса контровочную пластину 3 или контровочную проволоку 4 устанавливают в подготовленное место, а над ними помещают рабочую лопатку 1, после чего выступающие концы загибают.
-сплошными кольцами (см. Рис. 5.4.3.3_7). При использовании сплошного кольца его устанавливают по пояску, выполненному в диске 1 с переходной посадкой. В хвостовиках лопаток 2 имеются проточки для предотвращения их продольных перемещений. От перемещения в окружном направ-
252

Глава 5 - Компрессоры ГТД
Рисунок 5.4.3.3_4 – Хвостовик типа «ласточкин хвост» с плоскими рабочими поверхностями
* - Размеры расчетные
Рисунок 5.4.3.3_5 – Фиксация лопаток от перемещений штифтами
a) радиальным штифтом; б) осевым резьбовым штифтом; 1 – лопатка рабочая; 2 – диск;
3 – радиальный штифт; 4 - контровочная втулка; 5 - резьбовой штифт
лении кольцо 4 фиксируется радиальным штифтом 3 за обод диска 1.
- разрезными кольцами (см. Рис. 5.4.3.3_8). Разрезное контровочное кольцо 3 устанавливают в канавку, проточенную в диске 1 и лопатках 2. При работе двигателя оно прижимается к лопаткам центробежной силой, а от перемещения в окружном направлении фиксируется стопором 5 за обод диска. Для сжатия кольца при демонтаже лопаток из колеса в диске выполнены специальные отверстия 4.
В роторах с гладкой проточной частью фиксацию лопаток от осевого перемещения в пазу можно осуществить с помощью рядом стоящих деталей, как показано на Рис. 5.4.3.1_1.
Для предотвращения перемещений в окружном направлении лопатки 2, устанавливаемой в кольцевом пазе 4 диска 1 (см. Рис. 5.4.3.3_9), ее фиксация осуществляется контровочными замками 3 че- рез поперечные пазы 5 в диске 1. Крайние лопатки имеют пазы 6 в полках под замки. Замок фиксируется в кольцевом пазе диска при помощи винта.
253
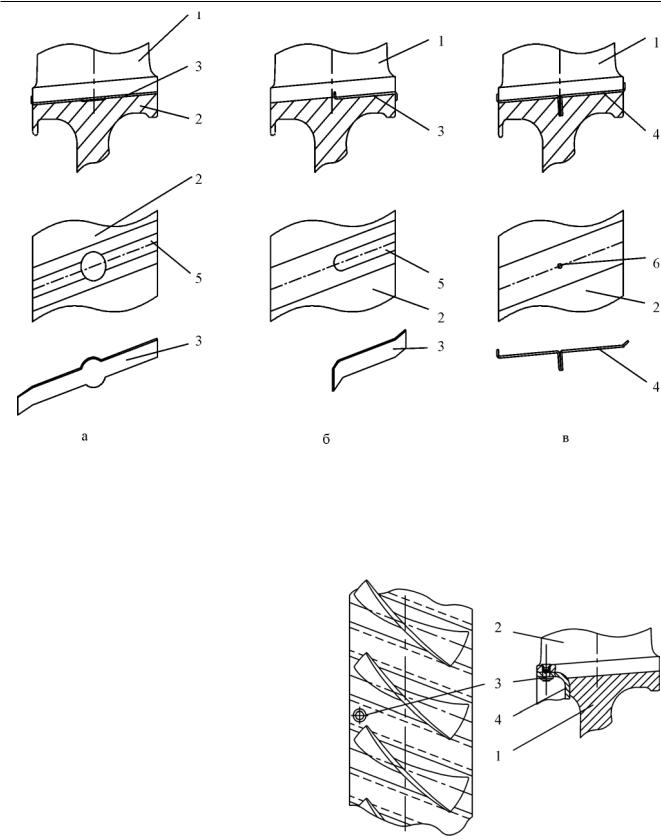
Глава 5 - Компрессоры ГТД
Рисунок 5.4.3.3_6 - Фиксация лопаток от перемещений контровочными пластинами и проволокой а, б) контровочными пластинами; в) контровочной проволокой;
1 – лопатка рабочая; 2 – диск; 3 – контровочная пластина; 4 - контровочная проволока; 5 – паз; 6 – отверстие
Еще одним способом крепления лопаток в диск является так называемый шарнирный замок (см. Рис. 5.4.3.3_10). В данной конструкции лопатки 2 своими проушинами 7 устанавливаются в кольцевые пазы 6 обода диска 1 (между ребордами 5) и фиксируется штифтами 3, которые в свою оче- редь контрятся стопорами 4.
При этом лопатка имеет зазор как относительно диска 1, так и относительно штифта 3, и поэтому сохраняет возможность поворота относительно оси штифта, закрепленного в ребордах. Такое крепление благоприятно сказывается на вибрационном состоянии лопатки, поскольку большая подвижность соединения по сравнению с соединением «ласточкин хвост» позволяет значительно лучше демпфировать возникающие в работе колебания. Однако та же самая подвижность соединения может привести к повышенному износу или ôðåò- тинг-коррозии лопаток, диска и фиксирующих штифтов. (Примечание - фреттинг-коррозией называется явление износа материала, возникающего на контактных поверхностях в результате посто-
Рисунок 5.4.3.3_7 - Фиксация лопаток от перемещений сплошным кольцом 1 – диск; 2 – лопатка рабочая; 3 – контровочный штифт; 4 – сплошное кольцо
254

Глава 5 - Компрессоры ГТД
Рисунок 5.4.3.3_8 - Фиксация лопаток от перемещений разрезным кольцом 1- диск; 2 - лопатка рабочая;
3 - разрезное кольцо; 4 - отверстия под съемник; 5 - стопор кольца
янных взаимных перемещений деталей). Чтобы это предотвратить, необходимо принимать специальные меры, например, наносить твердую смазку или износостойкие покрытия.
Определенным недостатком подобного соединения является то, что в собранном РК невозможно обработать торцы лопаток с целью обеспечения минимального радиального зазора. Лопатки с шарнирным замком имеют самую большую массу из рассмотренных в этом разделе. Поэтому шарнирное соединение возможно использовать только в рабо- чих колесах, имеющих сравнительно небольшие окружные скорости (не более 300 м/с) на периферии. В противном случае не удается удовлетворить требования прочности как к ребордам диска, так и к самому штифту. Исходя из указанных причин, такое соединение, в основном, получило распространение в КНД ТРД и ТРДД с малой степенью двухконтурности и в современных двигателях используется редко.
Рисунок 5.4.3.3_9 - Фиксация от перемещений лопаток с кольцевыми рабочими поверхностями (Печатается с разрешения Rolls-Royce plc.)
1 - диск; 2 - рабочая лопатка; 3 - контровочный замок ; 4 - кольцевой паз в диске; 5 - паз для ввода замка в кольцевой паз диска; 6 - паз в лопатке под контровочный замок
5.4.3.4 – Особенности крупногабаритных рабочих лопаток вентилятора
При проектировании крупногабаритных лопаток вентилятора необходимо решить следующие проблемы.
Первая проблема заключается в том, что из-за малой величины отношения диаметра диска к длине лопаток трудно разместить необходимое количе- ство лопаток. Обычно для вентилятора используют соединение типа «ласточкин хвост». Для крупногабаритных же лопаток при возникновении проблем с размещением необходимого количества пазов иногда применяют замок елочного типа с двумя зу-
255

Глава 5 - Компрессоры ГТД
Рисунок 5.4.3.3_10 - Шарнирное соединение лопатки с диском 1 - рабочая лопатка; 2 - проушины лопатки; 3 - кольцевые пазы; 4 - диск; 5 - реборды
диска; 6 - фиксирующий штифт; 7 - стопоры штифта
бьями, который меньше ослабляет ободную часть диска.
Следующая проблема связана с обеспечением допустимых вибронапряжений в лопатках. Для демпфирования колебаний и снижения вибронапряжений лопатки вентилятора с большим удлинением выполняют с антивибрационными полками на одном или нескольких уровнях (см. Рис. 5.4.3.4_1).
В современных авиационных двигателях, особенно в ТРДД с большой степенью двухконтурности, наибольшее применение нашли широкохордные лопатки без антивибрационных полок (см. Рис. 5.4.3.4_2).
Основные цели введения широкохордных лопаток:
-уменьшение потерь, связанных с закромоч- ными следами от антивибрационных полок;
-уменьшение влияния следов от полок на характеристики спрямляющей решетки;
-обеспечения максимального расхода воздуха на единицу площади, что позволяет свести к минимуму поперечные габариты двигателя;
-повышение аэродинамической эффективности вентилятора;
-снижение уровня шума вентилятора;
Рисунок 5.4.3.4_1 – Вентилятор с антивибрационными полками на двух уровнях двигателя Pratt&Whitney PW4000
-повышение стойкости двигателя к попаданию в него посторонних предметов;
-уменьшение общего количества лопаток вентилятора;
-уменьшение массы.
256
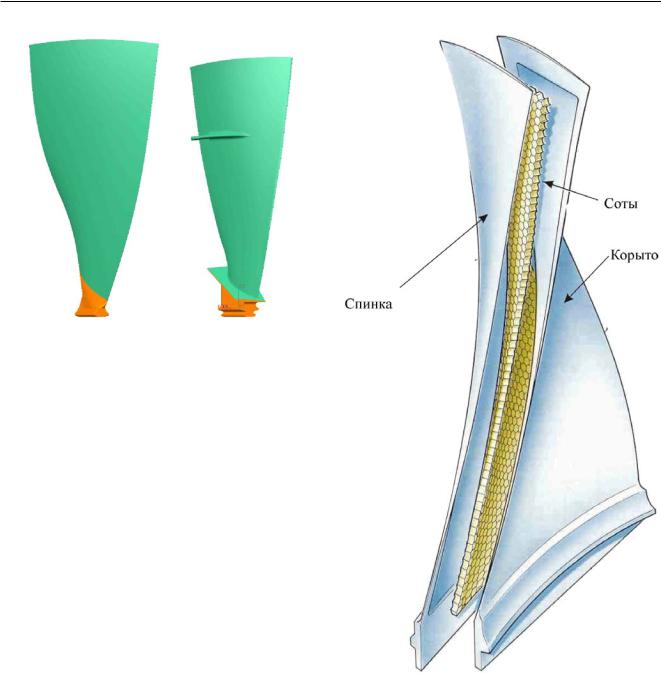
Глава 5 - Компрессоры ГТД
Рисунок 5.4.3.4_2 – Сравнение современной широкохордной и полочной лопаток вентиляторов одинакового диаметра
Проведенные исследования показывают, что только отказ от антивибрационных полок дает несколько преимуществ:
-газодинамическая эффективность вентилятора повышается до 6%;
-удельноый расход топлива на крейсерских режимах снижается на 4%;
-увеличивается расход воздуха через венти-
лятор.
Последнее обстоятельство оказывается чрезвычайно важным, так как проходящий по наружному контуру воздушный поток создает около 75% общей тяги. При заданной площади проходного сечения широкохордная лопатка без антивибрационных полок предоставляет большие возможности по выбору, повышению и оптимизации тяги.
Применение новых конструкторских и технологических решений позволяет снизить массу каждой лопатки в отдельности. Это пустотелые титановые лопатки с сотовым заполнителем или с гофрированным листом, пустотелые титановые лопатки с соединением двух половин по средней линии методом диффузионной сварки, лопатки из полимерных композиционных материалов (ПКМ), лопатки из неполимерных композиционных материалов (например, лопатки из материала на основе борного волокна
âалюминиевой матрице с титановой обшивкой). На Рис. 5.4.3.4_3 показана стреловидная широкохордная титановая лопатка вентилятора с сотовым заполнителем двигателя Rolls-Royce RB-211.
Рисунок 5.4.3.4_3 – Пустотелая титановая лопатка двигателя Rolls-Royce RB211 (Печатается с разрешения Rolls-Royce plc)
5.5 – Статоры осевых компрессоров
Статор компрессора обычно состоит из нескольких основных частей, которые в зависимости от назначения и выполняемой функции могут называться:
257
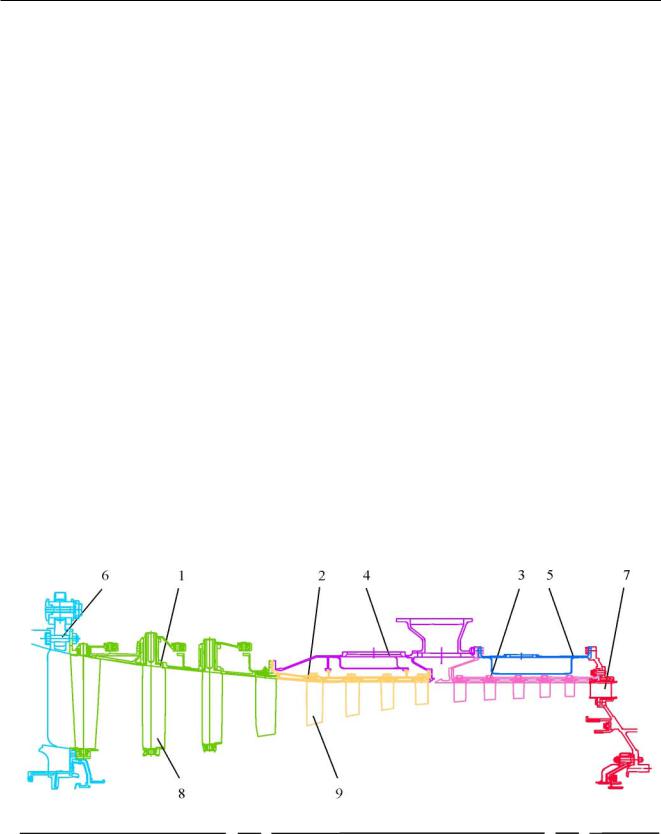
Глава 5 - Компрессоры ГТД
-корпус входной;
-корпус с регулируемыми и неподвижными НА;
-корпус отборов;
-корпус задней опоры.
В двух- и трехкаскадных компрессорах роль входных корпусов выполняет разделительный корпус. Пример статора компрессора представлен на Рис. 5.5_1.
Внутри корпуса крепятся опоры ротора, НА. Снаружи на обечайке и фланцах монтируются агрегаты (топливные и масляные насосы и т.п.), трубопроводные и электрические коммуникации, приводы механизации компрессора, узлы подвески двигателя к самолету. На корпусе выполнены специальные отверстия для отбора воздуха на различные нужды и смотровые люки для периодического контроля в эксплуатации рабочих и направляющих лопаток.
Статор воспринимает разнообразные нагрузки:
-осевые силы;
-гироскопические усилия;
-силы давления;
-массу и силы инерции ротора;
-изгибные и крутящие моменты от сопрягаемых деталей;
-тепловые деформации.
К статору предъявляются ряд специфических требований:
- герметичность;
-локализация возможного разрушения роторных деталей;
-простота изготовления и монтажа НА и различных агрегатов;
-обеспечение минимальных радиальных зазоров на всех режимах работы двигателя.
5.5.1 – Конструкции корпусов
Корпусы компрессора обычно представляют собой кольцевые цилиндрические или конические детали с фланцами на переднем и заднем торцах для крепления корпусов между собой (см. Рис. 5.5_1). Корпусы (см. Рис. 5.5.1_1) могут быть неразъемными и разъемными.
Корпус без продольного разъема обладает меньшей массой и большей жесткостью, но его изготовление более трудоемко, а сборка и разборка более сложная - такой корпус требует последовательную, поэтапную сборку и разборку ротора и статора.
Корпус с продольным разъемом также имеет свои недостатки. Неравномерная жесткость корпуса по окружности (большая в плоскости разъема и меньшая – в перпендикулярной к нему плоскости) приводит к неравномерному расширению корпуса и, следовательно, к дополнительной овализации в процессе работы. Параметры компрессора ухудшены из-за увеличенных зазоров - зазоры приходится увеличивать из-за большей овализации корпуса. Через разъемы происходят дополнительные
Рисунок 5.5_1 – Статор КВД двигателя ПС-90А 1 - корпус с регулируемыми НА; 2, 3 - корпус с неподвижными НА; 4 - корпус перепуска и от-
боров; 5 - корпус обдува; 6 - разделительный корпус с деталями передней опоры; 7 - корпус КС со спрямляющим аппаратом компрессора и деталями задней опоры; 8 - подвижные лопатки НА; 9 - неподвижные лопатки НА
258
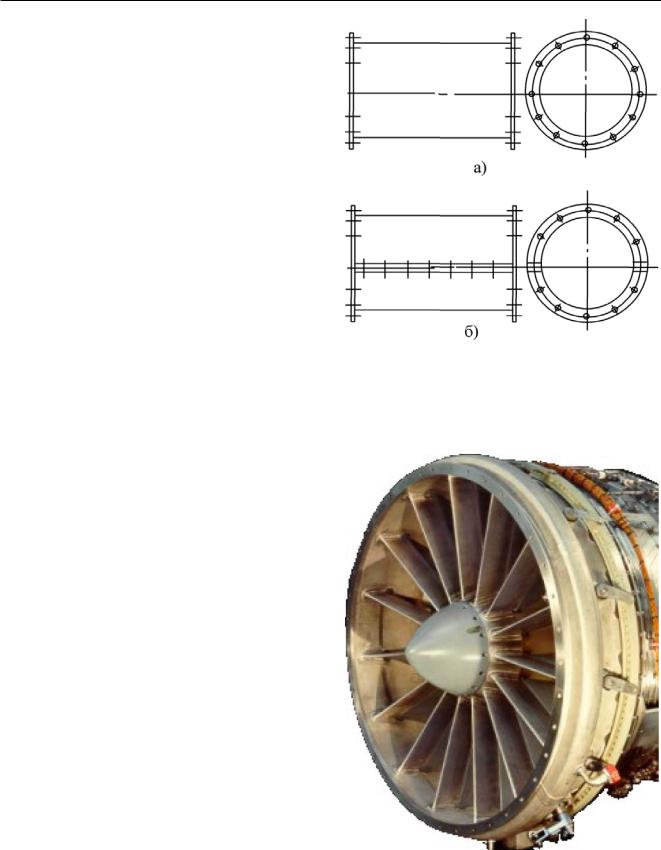
Глава 5 - Компрессоры ГТД
утечки воздуха. Худшая центровка статора с ротором. Основным преимуществом корпуса с продольным разъемом является удобство сборки, а на одноконтурных двигателях, особенно промышленного применения, возможность разборки корпуса и ремонта без разборки двигателя.
В современных авиационных двигателях предпочтение отдают комбинированным корпусам, в которых используются продольные и поперечные разъемы. Это, помимо прочего, позволяет изменять марку материала корпуса в зависимости от рабо- чей температуры от первой ступени к последней. Например для первых ступеней - алюминиевый корпус, затем - титановый, а последние ступени могут иметь корпус из жаропрочного сплава.
5.5.1.1 – Корпус входной
Корпус входной представляет собой силовой неразъемный корпус, предназначенный для передачи усилий от передней опоры компрессора. Может применяться конструкция, когда в силовую схему включаются лопатки ВНА, что уменьшает габариты и массу компрессора. Для увеличения запасов газодинамической устойчивости может применяться конструкция с регулируемой выходной кромкой ВНА (см. Рис 5.5.1.1_1).
Внутри стоек размещают коммуникации подвода к деталям опоры и отвода от них масла, а также воздуха на наддув уплотнений и обогрев обтекателя.
5.5.1.2 – Корпусы с направляющими аппаратами
Корпусы с НА (см. Рис. 5.5_1) представляют собой кольцевые детали, в которых закреплены лопатки НА подвижные и неподвижные. Эти корпусы формируют проточную часть компрессора и реализуют силовую связь между разделительным (входным) корпусом и корпусом камеры сгорания. В передней части корпуса компрессора для увели- чения запасов газодинамической устойчивости применяют НА, регулируемые по специальной программе (см. Рис. 5.5.1.2_1).
Корпус 1 с регулируемыми НА чаще всего выполняют с продольным разъ¸мом 3 для облегчения сборки компрессора. Лопатки 2 связаны друг с другом кольцами 4, которые в свою очередь соединены механизмом привода 5. Работа поворотных НА будет подробнее описана в разделе 5.6.
Корпус с неподвижными НА представляет собой тело вращения с закрепленными в нем отдельными лопатками НА, либо объединенным в сектора лопатками НА. Лопатки или сектора с лопатками
Рисунок 5.5.1_1 - Схема корпусов
a) без продольного разъема; б) с продольным разъемом
Рисунок 5.5.1.1_1 – Входной корпус со стойками, совмещенными с лопатками НА, двигатель Snecma M88
(Фотография любезно предоставлена компанией Snecma Moteurs)
259
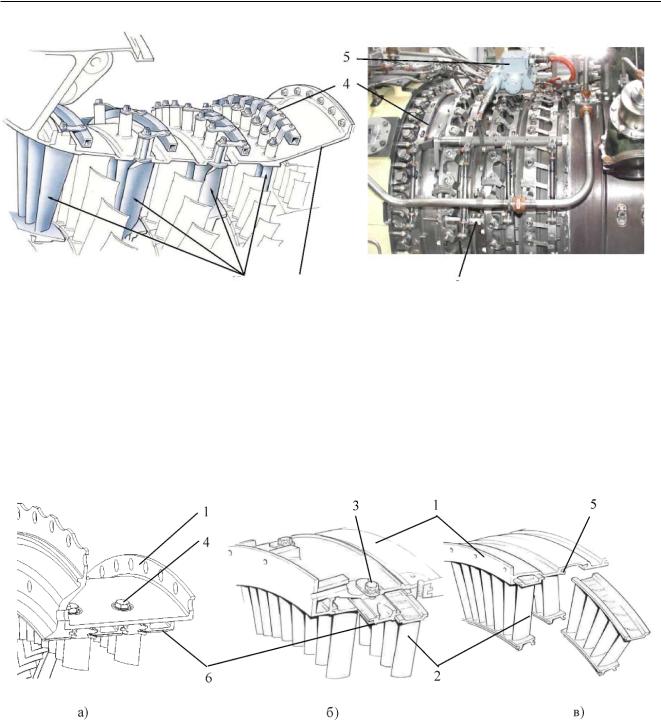
Глава 5 - Компрессоры ГТД
Рисунок 5.5.1.2_1 – Корпус с регулируемыми лопатками НА
a) двигатель International Aero Engine (I.A.E) V2500 (Печатается с разрешения Rolls-Royce plc); б) двигатель ПС-90ГП2
1 - корпус; 2 - лопатки НА; 3 - продольный разъем корпуса; 4 - кольца привода НА; 5 - Механизм привода НА
Рисунок 5.5.1.2_2 – Корпус с неподвижными лопатками НА
a) с консольными лопатками с замком типа «ласточкин хвост» в секторном кольце НА; б) с консольными лопатками с кольцевым замком; в) с секторами двухопорных лопаток; 1 - корпус; 2 - секторы НА; 3 - винт крепления рабочего кольца; 4 - винт крепления сектора НА; 5 - прирабатывемое покрытие на корпусе; 6 - рабочее кольцо c прирабатываемым покрытием
могут устанавливаться в специально выточенные |
ние 3 можно применять и для секторов НА. На кор- |
пазы в корпусе или последовательно друг за дру- |
пус между НА и на рабочие кольца наносится спе- |
гом по схеме «НА - рабочее кольцо – НА» (см. |
циальное мягкое прирабатываемое покрытие для |
Рис. 5.5.1.2_2). Рабочее кольцо 6 крепится к кор- |
предотвращения износа лопаток ротора при их за- |
пусу 1 радиальными винтами 4. Такое же крепле- |
девании о поверхность корпуса. |
260
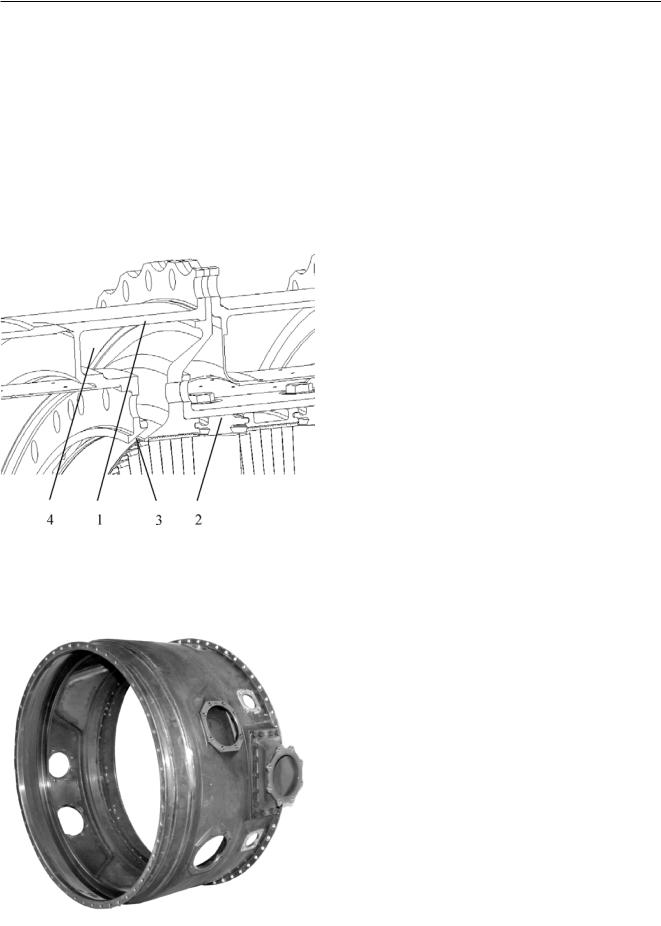
Глава 5 - Компрессоры ГТД
5.5.1.3 – Корпус отборов
Корпус отборов1 (см. Рис. 5.5.1.3_1) представляет собой деталь, расположенную над корпусом 2 с НА и образующая с ним кольцевую полость 4 со щелью отбора 3. На корпусе выполняются отверстия (см. Рис. 5.5.1.3_2) для отбора сжатого воздуха. Воздух расходуется на различные нужды - кондиционирование пассажирского салона самолета, наддув опор двигателя, охлаждение или обогрев различных узлов. Воздух отбирается из проточной части компрессора через отверстия в корпусе с НА
Рисунок 5.5.1.3_1 – Корпус отборов 1 - корпус отборов; 2 - корпус с
НА; 3 - щель отбора воздуха; 4 - кольцевая полость
Рисунок 5.5.1.3_2 - Корпус отборов КВД двигателя ПС-90А
или из кольцевой щели, образованной двумя последовательными корпусами с НА.
5.5.1.4 – Корпус задней опоры
Корпус задней опоры компрессора обеспечи- вает силовую связь между компрессором 1 и камерой сгорания 2 (см. Рис. 5.5.1.4_1). Внутри корпуса размещена задняя опора 3 компрессора. Корпус представляет собой два кольца, соединенные между собой радиальными связями, которыми являются либо лопатки спрямляющего аппарата 4 последней ступени компрессора, либо специально спрофилированные стойки на входе в КС. В последнем случае корпус чаще называют «корпусом камеры сгорания». Внутреннее кольцо корпуса задней опоры 5 с опорой компрессора соединяет силовая диафрагма 6. К наружному кольцу корпуса могут монтироваться узлы крепления двигателя к самолету.
Температура воздуха в районе корпуса задней опоры компрессора может достигать 550…600îС. На корпус действует высокое избыточное давление, от опоры передаются значительные радиальные и осевые (в случае, если установлен радиаль- но-упорный подшипник) усилия. Таким образом, корпус задней опоры компрессора является одним из самых нагруженных узлов всего двигателя.
5.5.2 – Корпус вентилятора. Удержание лопаток при обрыве
Согласно требованиям Авиационных Правил корпусы в ГТД должны быть спроектированы таким образом, чтобы обеспечить локализацию повреждений. Локализация - это удержание внутри корпуса двигателя фрагментов его конструкции, образовавшихся вследствие поломок лопаток роторов, а также вызванных ими вторичных явлений. При этом не должно происходить значительных разрывов и опасной деформации наружного корпуса или защитного экрана, но фрагменты могут выходить через воздухозаборник или выходное устройство двигателя.
Лопатка вентилятора ТРДД с большой степенью двухконтурности является самой тяжелой лопаткой двигателя. Поэтому задача локализации повреждений при обрыве лопатки вентилятора приобретает особое значение. Решается эта задача конструкцией корпуса вентилятора.
Корпус 1 вентилятора (см. Рис. 5.5.2_1) является силовым элементом двигателя. Он образует проточную часть от входа в двигатель до входа в спрямляющий аппарат 2 вентилятора. На внут-
261
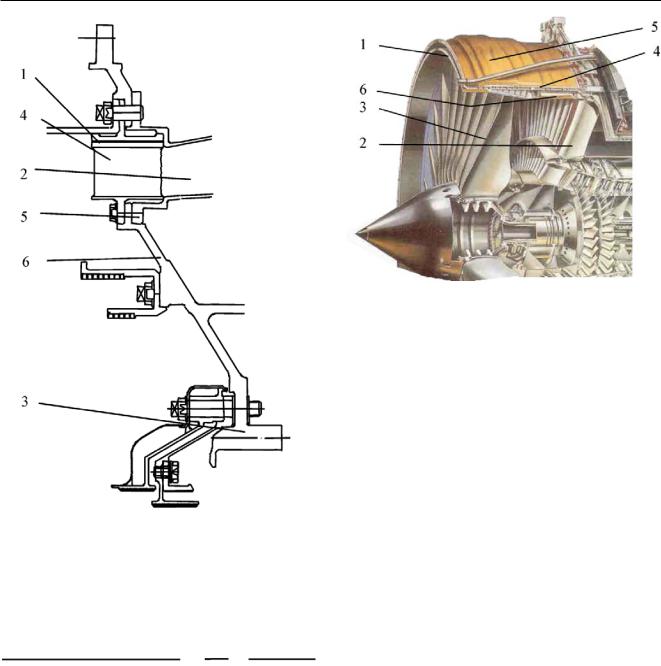
Глава 5 - Компрессоры ГТД
Рисунок 5.5.1.4_1 – Корпус задней опоры в КВД двигателя ПС-90А.
1 - КВД; 2 - КС; 3 - задняя опора компрессора; 4 - спрямляющий аппарат компрессора; 5 - внутреннее кольцо корпуса задней опоры компрессора; 6 - силовая диафрагма
реннюю часть корпуса вентилятора наносится прирабатываемое покрытие для обеспечения минимального радиального зазора над рабочими лопатками вентилятора.
На Рис. 5.5.2_1 представлен корпус вентилятора с мероприятиями по локализации повреждений при обрыве рабочей лопатки 3. Корпус вентилято-
Рисунок 5.5.2_1 – Корпус вентилятора двигателя Trent 800
1 - корпус вентилятора; 2 - спрямляющий аппарат вентилятора; 3 - рабочая лопатка вентилятора; 4 - алюминиевый корпус-мат- рица; 5 - кевларовая оболочка; 6 - панели с ЗПК
ра состоит из корпуса-матрицы 4, изготовленного из алюминиевого сплава, и удерживающего кольца 5 из кевлара (композиционного материала с высокой прочностью). Назначение корпуса-матрицы
– сохранение формы корпуса при обрыве лопатки, а назначение намотки из кевлара – удержать лопатку и предотвратить разрушение удерживающего кольца. Как правило, в корпус также встраиваются шумоглушащие панели 6.
5.5.3 – Направляющие аппараты (НА)
НА представляют собой набор лопаток закрепленных в корпусе неподвижно или имеющих возможность поворота профиля вокруг оси. Направляющие лопатки могут заранее помещаться в кольцевую деталь, после чего собранный НА устанавливается в корпус компрессора. Последний НА компрессора чаще называют спрямляющим аппаратом. Спрямляющий аппарат разворачивает воздушный поток на выходе из компрессора до осевого направления перед его входом в КС.
Условия работы направляющих лопаток аналогичны рабочим, поэтому к направляющим лопаткам предъявляют требования, подобные требованиям к рабочим лопаткам (см. раздел 5.4.3.1). Отличиями в работе является то, что направляющие лопатки не испытывают растягивающих напряжений от центробежных сил.
262

Глава 5 - Компрессоры ГТД
5.5.3.1 – Конструкция НА
Лопатки НА по способу закрепления в корпусе делятся на консольные и двухопорные.
Неподвижные консольные лопатки крепятся к корпусу или кольцу НА чаще всего хвостовиками типа «ласточкин хвост» (см. Рис. 5.5.3.1_1). Установка НА с хвостовиками такого типа показано на Рис. 5.5.1.2_2а. Еще один способ крепления направляющих лопаток в корпусе представлен на рисунке 5.5.1.2_2б,в. В этом случае лопатки или группы лопаток, соединенные в сектор, имеют специальные заплечики. Лопатки заводятся в специально спрофилированный кольцевой паз в корпусе. В этом случае корпус (или кольцо НА) обычно имеет разъемы для облегчения сборки узла. Очень редко каждую лопатку соединяют с корпусом сваркой или пайкой.
Двухопорные неподвижные НА собирают следующим образом. В корпус лопатки 1 устанавливаются любым из описанных для консольных лопаток способов, но дополнительно крепятся на внутреннем кольце 2, например, гайками 3, навинчивающимися на специально нарезанную резьбу на внутренних цапфах лопаток (см. Рис. 5.5.3.1_2а). Возможно крепление кольца внутреннего к лопаткам посредством заклепок 4 (см. Рис. 5.5.3.1_2б) или через отверстия 5 с помощью болтового соединения с сопряженным корпусом (см. Рис. 5.5.3.1_2в). На внутреннюю поверхность этих колец наносят прирабатываемое покрытие 5 для организации уплот-
Рисунок 5.5.3.1_1 – Лопатка НА с хвостовиком типа «ласточкин хвост» 1 - перо; 2 - хвостовик
нения, предотвращающего перетекание воздуха между ступенями.
Поворотные направляющие лопатки обеспе- чивают запас газодинамической устойчивости.
Поворотные консольные лопатки имеют в периферийной части пера 1 цилиндрический хвостовик 2 (см. Рис. 5.5.3.1_3). Лопатка устанавливается в корпус изнутри до упора в торец 4. С наружной части корпуса на лопатку устанавливается рычаг, фиксирующий ее от выпадения и осуществляющий поворот лопатки (см. Рис. 5.5.1.2_1).
Двухопорные поворотные НА конструктивно аналогичны консольным. Но на втулочной части
Рисунок 5.5.3.1_2 – Двухопорная неподвижная лопатка НА
a) с креплением внутреннего кольца гайками; б) с креплением внутреннего кольца заклепками; в) с внутренним кольцом, сформированным полками лопаток; 1 - лопатка НА; 2 - кольцо внутреннее; 3 - гайка; 4 - заклепка; 5 - прирабатываемое покрытие; 6 - отверстия для болтового соединения с сопряженным корпусом
263

Глава 5 - Компрессоры ГТД
Рисунок 5.5.3.1_3 – Поворотная лопатка НА
a) консольная; б) двухопорная; 1 - перо; 2 - наружный цилиндрический хвостовик; 3- внутренний цилиндрический хвостовик; 4 - упорный торец
пера лопаток этих НА имеется второй цилиндри- ческий хвостовик (см. Рис. 5.5.3.1_3), который позволяет закрепить лопатку во внутреннем закрепленном (для лопаток ВНА) или незакрепленном (для остальных поворотных НА) кольце (см. Рис. 5.5_1). Для компенсации несоосности цилиндрических отверстий в корпусе и внутреннем кольце на хвостовики лопаток устанавливают сферические подшипники, значительно снижающие усилия поворота лопатки.
Âслучае использования НА с консольным креплением лопаток ротор компрессора должен иметь «гладкую» (см. раздел 5.4.2) проточную часть. Поэтому двухопорные лопатки в первую очередь применяют в поворотных и неподвижных НА первых ступеней компрессора, где лопатки имеют большое относительное удлинение.
Âгорячей части компрессора лопатки могут устанавливаться с жесткой связью только по одному (наружному или внутреннему) кольцу. Соответственно в другом кольце лопатки имеют возможность перемещения вдоль своей радиальной оси. Это делается с целью обеспечения возможности дополнительных температурных расширений.
5.6– Регулирование компрессоров
ГТД являются по характеру использования многорежимными, широкодиапазонными машинами. Например, авиационный ГТД должен обеспе-
чивать необходимые параметры как в условиях старта на земле, так и в условиях полета на больших высотах с различными, в том числе и сверхзвуковыми скоростями полета. При определенных условиях работы ГТД возможно существенное снижение к.п.д. компрессора на отдельных режимах, несмотря на его высокое значение на расчетном режиме. Кроме того, на некоторых режимах возможно появление признаков неустойчивой работы компрессоров, что недопустимо для работы двигателя.
Необходимые характеристики удается полу- чить рациональным выбором расчетного режима
ñпомощью регулирования компрессора:
-перепуском воздуха;
-поворотом направляющих лопаток. Целями регулирования являются:
-обеспечение запасов газодинамической устойчивости;
-обеспечение к.п.д. компрессора;
-изменение соотношений между расходом воздуха, частотой вращения и степенью повышения полного давления для улучшения характеристик двигателя;
-обеспечение допустимого предела вибрационных напряжений в лопатках.
Основными способами регулирования компрессора являются поворот направляющих лопаток и перепуск воздуха на низких частотах вращения.
5.6.1 – Поворот направляющих лопаток компрессора
Поворот направляющих лопаток компрессора позволяет достичь высоких характеристик двигателя на разных режимах работы путем подстройки геометрических углов лопаток под направление воздушного потока в соответствии с условиями работы компрессора. Количество ступеней поворотных аппаратов и диапазоны углов поворота лопаток выбираются при проектировании компрессора.
Существует множество различных конструкций механизмов поворота лопаток направляющих аппаратов. Привод механизма выбирается, исходя из потребного усилия и времени перекладки, диапазона регулирования. В конструкции механизма поворота может быть один или два привода. Привод может быть гидравлическим (рабочее тело – жидкость), пневматическим (рабочее тело – воздух) или электрическим.
Перекладка поворотных лопаток НА может осуществляться:
- из одного крайнего положения в другое крайнее положение за короткий промежуток времени (десятые доли секунды),
264
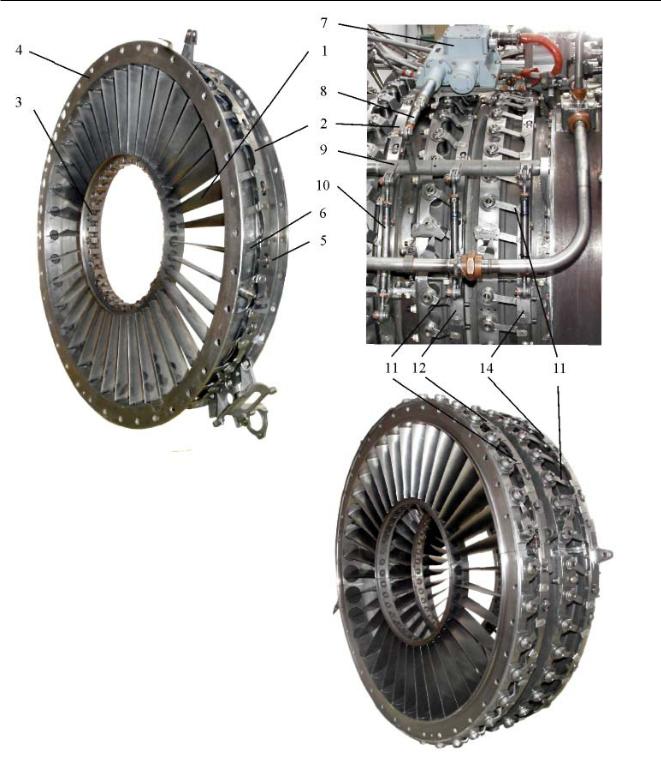
Глава 5 - Компрессоры ГТД
à)
Рисунок 5.6.1_1 - Привод поворотных НА двигателя ПС-90ГП-1 а) ВНА; б) корпус с поворотными
НА 1 и 2 ступеней; 1 - лопатка ВНА; 2 - кольцо приво
да ВНА; 3 - кольцо внутреннее; 4 - кольцо наружное; 5 – ролик; 6 - рычаги ВНА; 7 - электричес-
кий привод; 8 - шток привода; 9 - ведущий вал; 10 – тяга; 11 - рычаг НА 1 ступени; 12 - кольцо привода НА 1 ступени; 13 - рычаг НА 2 ступени; 14 - кольцо привода НА 2 ступени
|
á) |
- по программе в зависимости от изменения |
ковых по конструкции ведущих вала 9, располо- |
приведенных оборотов КВД. |
женных диаметрально противоположно. Рычаг ве- |
На Рис. 5.6.1_1а представлена конструкция |
дущего вала через тягу 10 передает усилие к рыча- |
механизма поворота лопаток НА двигателя |
гу привода ВНА, соединенного со скобой кольца |
ПС-90ГП-1. Поворот лопаток 1 ВНА осуществля- |
привода ВНА 2. Лопатки ВНА 1 закреплены в на- |
ется по заданной программе в зависимости от при- |
ружном 4 и внутреннем 3 кольцах с зазором в сфе- |
веденной частоты вращения ротора КВД двумя |
рических опорах и поворачиваются вокруг про- |
электрическими приводами 7, расположенными ди- |
дольной оси с помощью кольца привода ВНА, |
аметрально противоположно. Поступательное дви- |
соединенного шарнирно с рычагами, жестко укреп- |
жение штоков привода 8 передается на два одина- |
ленных на лопатках. |
265

Глава 5 - Компрессоры ГТД
Если для обеспечения параметров компрессора одного поворотного аппарата недостаточно, то за ним устанавливают аналогичные поворотные аппараты последующих ступеней. На Рис. 5.6.1_1б представлен корпус с поворотными НА 1 и 2 ступеней двигателя ПС-90ГП-1. Привод осуществляется теми же ведущими валами 9. Лопатки НА 1
è2 ступеней поворачиваются относительно своих продольных осей с помощью подвижных колец 12
è14 привода НА 1 и 2 ступеней, соединенных шарнирно с рычагами 11 и 13, жестко укрепленных на лопатках.
При повороте рычагов ведущих валов происходит перемещение колец привода ВНА, НА 1 и 2 ступеней относительно корпусов в окружном направлении, что и осуществляет поворот лопаток на заданный законом управления угол.
Датчик, установленный около одного из приводов, измеряет фактический угол и передает эти данные в систему автоматического регулирования (САР), которая сравнивает их с заданными по программе управления значениями и выдает команду в привод на корректировку положения.
5.6.2 – Перепуск воздуха из проточ- ной части компрессора
Перепуск воздуха в группе средних ступеней компрессора позволяет увеличить расход воздуха через передние ступени на низких частотах вращения, тем самым выводя их на расчетный режим работы. С помощью перепуска снижается линия рабочих режимов двигателя, за счет чего удается повысить запас устойчивой работы компрессора. Необходимо отметить, что этот метод регулирования экономически не выгоден, так как ведет к снижению тяги двигателя и увеличению удельного расхода топлива на режимах перепуска. Поэтому перепуск воздуха используется на кратковременных режимах работы двигателя, а на вновь проектируемых двигателях чаще всего не применяется.
Перепуск воздуха осуществляют через отверстия в корпусе, которые закрываются и открываются по программе регулирования компрессора. Открытие отверстий осуществляется разными способами:
-лентами;
-заслонками;
-клапанами.
Воздух, отобранный из проточной части компрессора, сбрасывается в атмосферу (для одноконтурных двигателей) или в проточную часть наружного контура (для двухконтурных двигателей).
На Рис. 5.6.2_1 показан способ регулирования перепусков стальными лентами. С внешней сторо-
ны корпуса перепуска 1 отверстия 2 закрыты двумя стальными лентами 3, которые при помощи механизмов 4 управления открывают или закрывают одновременно оба ряда отверстий. На концах ленты имеются петли 5, которыми она при помощи звеньев 6 шарнирно соединена с поршнем 7 механизма управления. Отверстия закрываются лентой при перемещении поршня в цилиндре 8 под действием сжатого воздуха, подводимого через штуцер 9, а открываются отверстия под действием пружин 10 при выключении подачи сжатого воздуха.
На рисунке изображено положение деталей механизма и лент перепуска при закрытых отверстиях.
Другим способом осуществления перепуска воздуха является перепуск посредством открытия заслонок 1 (см. Рис. 5.6.2_2). На осях 2 заслонок 1 крепят рычаги, связанные с гидроцилиндром управления.
Существуют конструкции компрессоров, в которых перепуск воздуха осуществляется при срабатывании клапанов 2 перепуска воздуха (см. Рис. 5.6.2_3). В корпусе 1 выполняют необходимое количество отверстий 3. Над отверстиями имеется кольцевой коллектор 4, на который установлены клапаны перепуска. Клапаны перепуска открываются и закрываются по заданному закону или в случае возникновения угрозы неустойчивой работы компрессора.
5.7 – Противообледенительные устройства
В некоторых условиях эксплуатации авиационных двигателей и двигателей наземного использования (например, минусовые температуры окружающего воздуха, высокая влажность) возможно образование льда на элементах входного устройства и деталях компрессора. Накопление льда на деталях двигателя неблагоприятно влияет на его работу и вызывает недопустимое снижение мощности или тяги. При этом возможно ухудшение управляемости двигателя, повышение температуры газа выше допустимой. Образование льда на деталях двигателя, особенно на роторных деталях компрессора, может привести к значительному увеличению вибраций двигателя вследствие разбалансирования ротора. В конечном итоге оторвавшиеся куски льда, попадая в газовоздушный тракт двигателя, могут привести к недопустимым механическим повреждениям двигателя
Для обеспечения надежной работы двигателей в этих условиях необходимо предусматривать
266
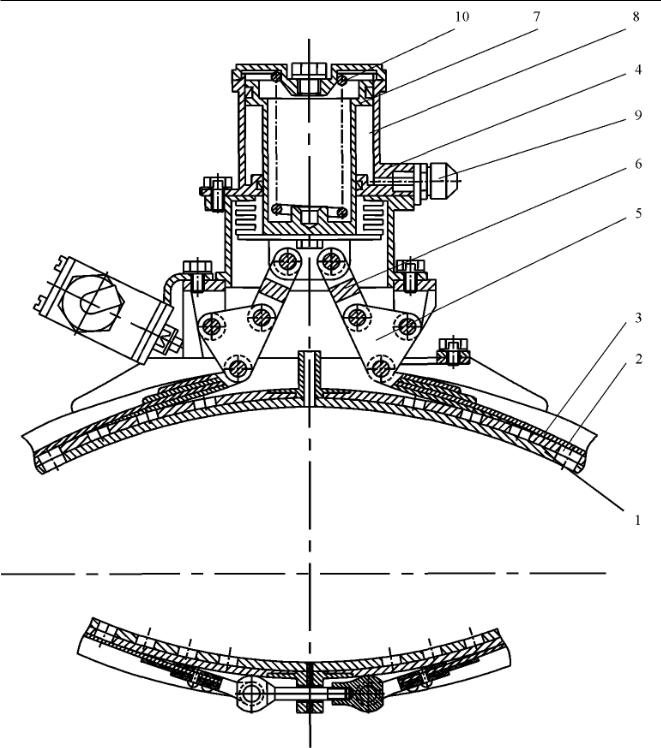
Глава 5 - Компрессоры ГТД
Рисунок 5.6.2_1 – Перепуск с лентами 1 - корпус перепуска; 2 - отверстия; 3 - стальная лента; 4 - механизм управления; 5 – пет-
ля; 6 – звено; 7 – поршень; 8 – цилиндр; 9 – штуцер; 10 - пружина
специальные противообледенительные системы |
В большинстве случаев лед образуется на не- |
(ПОС). ПОС включают в себя: |
подвижных деталях двигателя, но в неблагоприят- |
- противооблединительные устройства (ПУ); |
ных условиях работы возможно образование льда |
- систему управления ПОС (см. главу 12 «Си- |
даже на поверхности вращающегося обтекателя. |
стемы») |
Для предотвращения обледенения использу- |
ПУ должны обеспечивать работу двигателя во |
ются следующие способы: |
всем диапазоне полетных режимов. |
- подогрев стенок элементов входного устрой- |
267
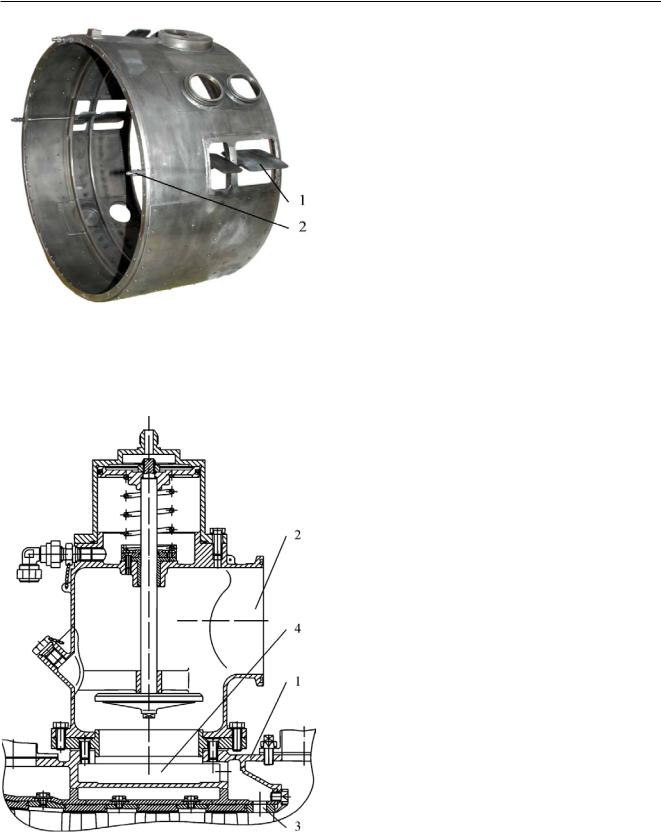
Глава 5 - Компрессоры ГТД
Рисунок 5.6.2_2 – Корпус перепуска с поворотными дроссельными заслонками двигателя Д-30 1- заслонки; 2 - ось заслонки
Рисунок 5.6.2_3 – Перепуск в компрессоре двигателя ПС-90ГП-1 с пневматическим клапаном перепуска 1 - корпус перепуска; 2 - клапан
пе репуска; 3 - отверстия перепуска;4 - кольцевой коллектор
ства, а также лопаток первых ступеней компрессора;
-впрыскивание во входное устройство двигателя противообледенительной жидкости;
нанесение специальных покрытий и материалов, препятствующих накоплению льда на элементах двигателя.
Для авиационных двигателей и двигателей наземного применения в настоящее время наибольшее применение нашел первый способ – подогрев элементов входного устройства и деталей компрессора (воздухозаборник, приемники давления и температуры на входе в двигатель, конус-обтекатель, стойки, лопатки ВНА).
Источникамитепладляподогреваэлементоввходного устройства и деталей компрессора могут быть:
-воздух, отбираемый из-за одной из ступеней компрессора;
-масло, откачиваемое из маслоотстойников;
-газы, отбираемые из камеры сгорания или изза турбины двигателя;
-газы, вырабатываемые в специальной вспомогательной камере сгорания;
-электрический подогрев.
Обогрев теплым воздухом, отбираемым от компрессора, является наиболее простым, и поэтому он получил наибольшее распространение. Воздух подводится к обогреваемым деталям только при условиях обледенения. Расход воздуха, его давление и температура должны обеспечить достаточный обогрев деталей во всем диапазоне рабочих режимов и условий эксплуатации двигателя. Чрезмерный равно как и неравномерный подогрев может приводить к короблению обогреваемых деталей. Поэтому на практике применяют системы отбора обогревающего воздуха с переключением места отбора – в зависимости от режимов работы двигателя воздух на обогрев отбирается от различных ступеней компрессора.
Пройдя систему подогрева, теплый воздух обычно выбрасывается в проточную часть наружного контура двигателя. В одноконтурных двигателях этот воздух сбрасывается в атмосферу.
На Рис. 5.7_1 представлен пример обогрева деталей воздухозаборника и входного корпуса воздухом, отбираемым от компрессора.
Тепло отработанного масла может использоваться для обогрева силовых стоек входного корпуса компрессора. Обогрев горячими газами не получил распространения из-за вызываемой ими коррозии деталей ПОС и сравнительно высокой пожароопасности. При электрическом подогреве источники тепла – нагревательные элементы – размещаются в обогреваемых деталях. Для электри- ческой системы обогрева необходимо сравнитель-
268

Глава 5 - Компрессоры ГТД
Рисунок 5.7_1 – ПОС на входе в двигатель RollsRoyce RB183 MK 555 (Печатается с разрешения Rolls-Royce plc)
1 - обогреваемый воздухозаборник;
2 - обогреваемый обтекатель;
3 - обогреваемые лопатки ВНА;
4 - регулятор давления; 5 - воздушный коллектор; 6 - трубопровод подвода воздуха
но большое количество электрической энергии - 80…120 Вт на 1 дм2 обогреваемой поверхности, что является существенным недостатком.
5.8 – Защита от попадания посторонних предметов
Большое количество двигателей снимается с самолетов до выработки ими гарантийного ресурса из-за повреждения компрессора посторонними предметами, попавшими на вход двигателя при эксплуатации. Досрочный съем двигателей нарушает регулярность рейсов самолетов и приводит к большой дополнительной загрузке завода-изго- товителя и ремонтных предприятий внеплановым ремонтом двигателей. Повреждение компрессоров двигателей снижает эксплуатационную надежность и безопасность полетов.
Повреждения газовоздушного тракта в основном происходят от попадания в двигатель частиц износа с ВПП, пыли, льда, воды, проволоки щеток снегоочистителей, града, птиц и т.д. В зимнее время уровень съема двигателей по забоинам на лопатках превышает уровень съема в летнее время.
Это объясняется ухудшенным состоянием ВПП
èрулежных дорожек зимой из-за образования на них льда и внедрения в него твердых частиц.
Преимущественно попадание посторонних предметов и частиц в газовоздушный тракт компрессора происходит:
во время рулежки, разбега и пробега из-под передних и основных колес шасси;
-èç-ïîä струй газов при позднем закрытии створок реверса тяги при посадке самолета;
-при работе двигателя на стоянке из-за возникновения вихревого жгута под воздухозаборником на поверхности ВПП.
В настоящее время определены основные направления защиты двигателя от повреждений:
-предотвращение попадания посторонних предметов в воздухозаборник;
-очистка воздуха на входе в двигатель от посторонних предметов;
-создание «самозащищенных» двигателей, приспособленных к сохранению работоспособности в условиях попадания на вход посторонних предметов.
Предотвращение попадания посторонних предметов в воздухозаборник осуществляется следующим комплексом мероприятий:
-применение на колесах шасси щитков;
-отработка методики взлета и реверсирова-
íèÿ;
-струйная защита от образования вихря;
-совершенствование покрытий аэродромов
èкачества ухода за ними.
Очистка воздуха на входе в двигатель от посторонних предметов осуществляется:
-применением управляемых сеток, перекрывающих вход в двигатель на соответствующих режимах;
-использованием искривлений воздухоподводящих каналов для организации инерционной очи- стки воздуха путем установки в местах поворота потока окон-ловушек;
применением роторных систем защиты, в которых очистка воздуха от посторонних предметов осуществляется специальной ступенью, установленной перед входом в двигатель.
Создание «самозащищенных» двигателей требует разработки:
-методики расчета полей скоростей, индуцируемых воздухозаборником двигателя;
-математических моделей движения посторонних предметов вне воздухозаборника и в его канале с учетом динамического взаимодействия
ñэлементами летательного аппарата и силовой установки.
269
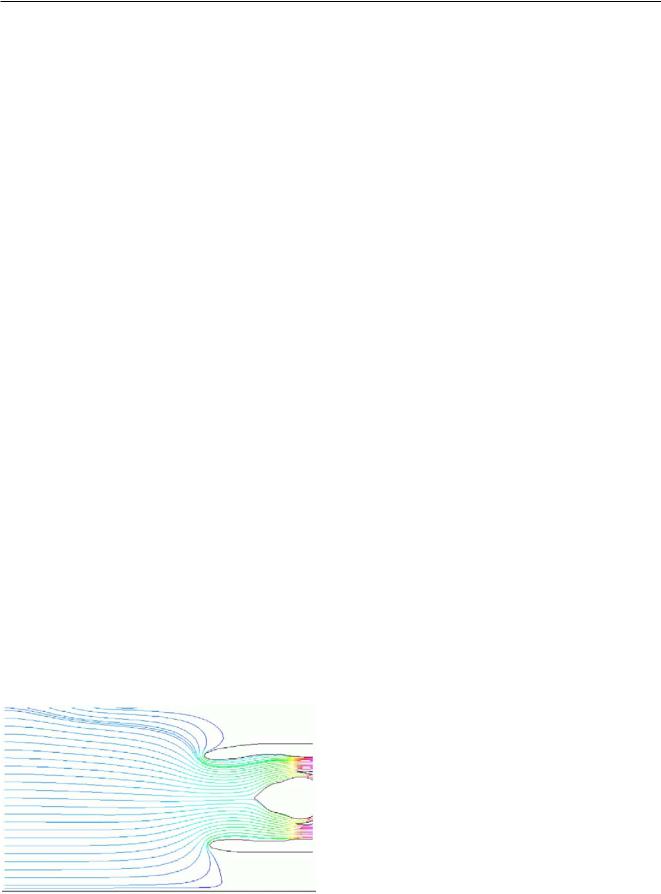
Глава 5 - Компрессоры ГТД
Конструкции современных двигателей позволяют ремонтировать поврежденные лопатки вентиляторов и КНД вплоть до замены модулей без съема двигателя с самолета. В то же время повреждения КВД ведут к досрочному съему двигателей и их полной переборке. Анализ повреждений проточной части компрессоров показывает, что соответствующей компоновкой компрессоров, профилированием лопаток и проточной части, использованием систем сдува вихря и ПОС, можно существенно снизить вероятность повреждения лопаток КВД.
Для разработки мероприятий по предотвращению попадания постороннего предмета в газовоздушный тракт необходимо ясно представлять себе процессы, вызывающие вихревое засасывание предметов, и влияние конструктивных и эксплуатационных параметров на интенсивность засасывания. Для этого рассматривается кинематическая структура потока около воздухозаборника двигателя при его работе над поверхностью аэродрома (см. Рис. 5.8_1).
Анализ векторного поля скоростей показывает, что по мере приближения к воздухозаборнику происходит сближение линий тока, причем на поверхности аэродрома существует точка, радиальные составляющие скорости в которой равны нулю. Как показывают экспериментальные исследования [5.13.17], именно возле таких точек торможения формируется ядро вихревого шнура. Положение точки торможения зависит от скорости и направления ветра, скорости движения самолета по аэродрому. При увеличении скорости движения самолета точка торможения сдувается, и, следовательно, исчезает предпосылка возникновения вихревого шнура. Результаты расчетных и экспериментальных данных свидетельствуют, что течение на входе в воздухозаборник при наличии вихревого за-
Рисунок 5.8_1 – Структура воздушного потока при размещении двигателя ПС-90А на высоте H=2 м (условия M=0, H=0)
сасывания, не является равномерным, и при определенных условиях может привести к нарушению устойчивой работы двигателя.
Однако наличие вихревого течения под воздухозаборником не всегда приводит к забросу в двигатель посторонних предметов, находящихся на поверхности аэродрома. Для этого вихрь должен обладать определенной интенсивностью. Интенсивность вихревого течения можно оценить вели- чиной горизонтальной составляющей скорости воздушного потока в приземном слое под воздухозаборником Vгmax [5.4.18].
Vmax = Gmax / (20,1 - H20)
ãäå Gmax – максимальный расход воздуха;
H0 – расстояние от поверхности аэродрома до оси воздухозаборника.
Граничными значениями, установленными на основании экспериментальных данных, являются:
Vmax < 1,0 м/с – отсутствие вихревых шнуров или весьма слабое вихреобразование;
1,0 ì/ñ < Vmax < 1,5 м/с – вихреобразование недостаточно интенсивное, чтобы подбросить части-
цу опасного размера на уровень воздухозаборника; Vmax > 1,5 м/с – интенсивное вихреобразование. Согласно предложенной ЛИИ им М.М. Громова методике определения интенсивности вихрево-
го течения, все самолеты, с точки зрения вероятности заброса посторонних предметов в двигатель, можно разделить на «вихревые» и «невихревые» (см. Рис. 5.8_2).
Из рисунка следует, что защита двигателя обеспечивается, когда величина горизонтальной составляющей скорости воздушного потока в приземном слое под воздухозаборником не превышает значения VÃmax = 1,5 м/с. При этом относительная высота расположения воздухозаборника должна быть не ниже Íîòí = 2.
Таким образом, можно сделать следующие выводы.
1.Для защиты двигателя необходимо обеспечи- вать такую компоновку силовой установки на самолете, при которой высота расположения воздухозаборника должна быть заведомо большей, чем Íîòí = 2.
2.Если обеспечить такую высоту расположения воздухозаборника не удается, то необходимо рассматривать применение специальных средств защиты, например, струйных.
Таким образом, схема размещения СУ на самолете, широко применяемая в настоящее время (см. Рис. 5.8_3) – наиболее удачная с точки зрения летных качеств самолета - не позволяет в то же время избежать возможности появления вихрево-
270
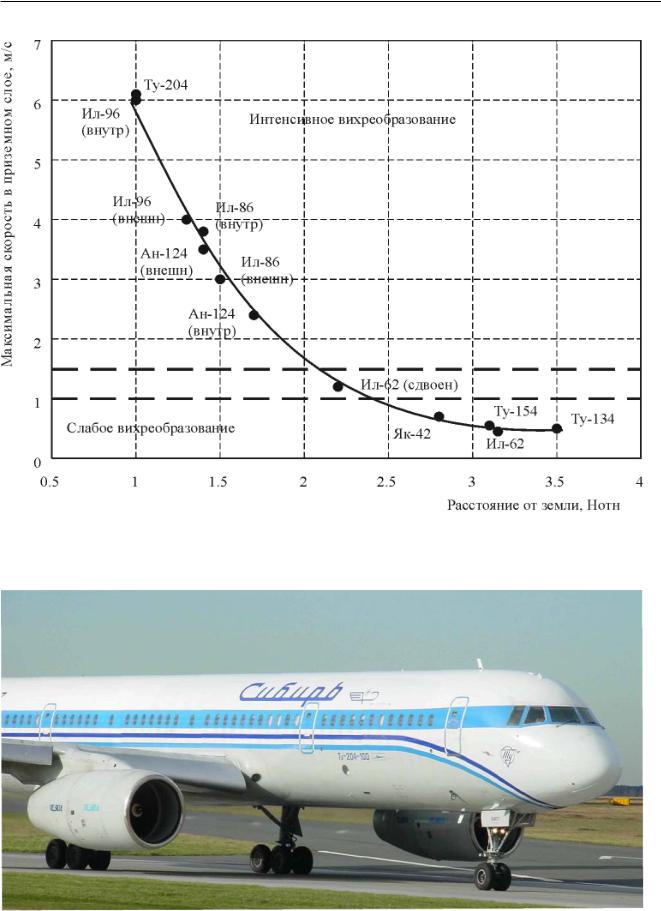
Глава 5 - Компрессоры ГТД
Рисунок 5.8_2 – Значение параметра защищенности ГТД от вихревого шнура компоновочной схемой самолета
Рисунок 5.8_3 – Размещение двигателя на самолете Ту-204-100
271
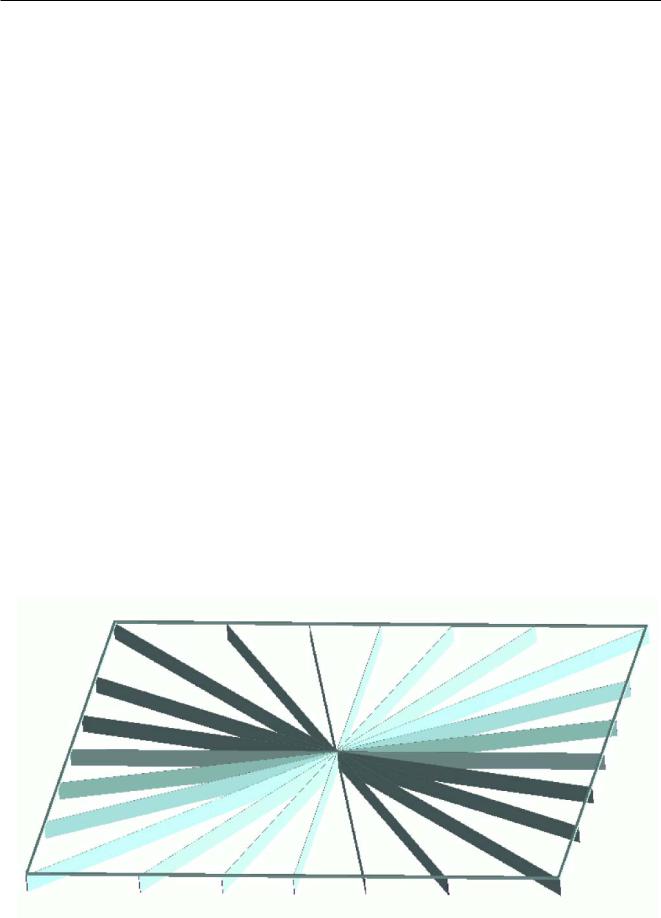
Глава 5 - Компрессоры ГТД
го течения при работе двигателей в наземных условиях.
Из вышесказанного можно сделать вывод, что для снижения вероятности попадания в двигатель посторонних предметов вихревым течением необходима защита хотя бы от одного из двух следующих условий:
-существование вихревого течения, что обуславливается наличием точки торможения линий тока на поверхности земли;
-существование в приземном слое воздушного потока достаточной интенсивности (VÃmax > 1,5 ì/ñ).
5.8.1 – Эксплуатационные мероприятия по предотвращению появления вихревого шнура
Одним из эксплуатационных методов защиты двигателя является специальный метод разбега самолета на стартовом участке ВПП со свободными тормозами – «роллинг-старт». Суть такого метода в том, что самолет начинает разбег при работе двигателя на пониженном режиме (режиме страгивания), а затем в процессе разбега режим работы двигателей увеличивается до максимального.
Другим эксплуатационным мероприятием, исключающим возникновение вихревого шнура под воздухозаборником при отладке двигателей на гоночной площадке, является применение наземного устройства (Рис. 5.8.1_1), разрушающего вихревой шнур. Такое наземное устройство представляет со-
бой звездообразную конструкцию, состоящую из ряда пластин, равномерно расходящихся из центра. Размеры пластин могут быть следующими: толщина 2-2,5 мм, длина, равная радиусу зоны вихреобразования, высота, равная 0,07 диаметра воздухозаборника. Располагается данное устройство на поверхности аэродрома под воздухозаборником, при этом центр устройства совмещается с эпицентром вихря.
5.8.2 – Конструктивные мероприятия для защиты внутреннего контура от попадания посторонних предметов
На примере двигателя ПС-90А рассмотрим мероприятия для защиты внутреннего контура от попадания посторонних предметов:
-обтекатель спроектирован вращающимся
ñуглом конуса 90°;
-на обтекатель нанесена отпугивающая окраска для защиты двигателя от попадания птиц;
-втулка рабочего колеса имеет крутой подъем
≈25°;
-разделитель потока максимально отодвинут от рабочего колеса;
-осуществляется сепарирование посторонних предметов (прошедших через тракт подпорных ступеней) в полость наружного контура через кольцевую щель перепуска воздуха из КНД;
-спроектирован искривленный канал внутреннего контура вентилятора с малым шагом решеток ВНА и спрямляющего аппарата подпорных ступеней;
Рисунок 5.8.1 _1 – Наземное защитное устройство типа антивихревого рассекателя
272
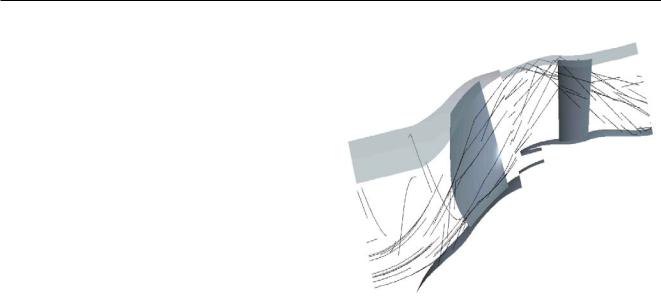
Глава 5 - Компрессоры ГТД
-предусмотрена ПОС обтекателя двигателя
èвоздухозаборника самолета.
Для увеличения устойчивости двигателя к попаданию посторонних предметов применяют широкохордные лопатки вентилятора с упрочненной входной кромкой.
Лопатки широкохордного вентилятора по сравнению с традиционным в большей степени защищают двигатель от попадания посторонних предметов, поскольку они имеют большую ширину и толщину корневого сечения и поэтому более устойчивы и к попаданию птиц. Кроме этого под действием центробежных сил, а также из-за переноса передней кромки ближе к входу такие лопатки позволяют отбрасывать посторонние предметы в наружный контур.
Применение указанных мероприятий, а также возможность зачистки забоин на лопатках вентилятора и их замены без разборки двигателя позволяют уменьшить количество двигателей, снимаемых с самолета в эксплуатации по повреждениям лопаток.
Проведенные с целью определения места
èстепени концентрации посторонних предметов в воздухозаборнике самолета расчетные исследования показывают, что отчетливо видна концентрация частиц в центре канала, которая достигает наибольшей величины на начальном участке (см. Рис. 5.8.2_1). Затем поток частиц начинает расширяться, смещаться вверх и в дальнейшем испытывает соударение, достигая верхней стенки канала.
Полученные результаты по степени концентрации частиц, в частности, по величине площади пучка в области повышенной концентрации, е¸ протяженности по длине канала дают все основания полагать, что элементы вентилятора, в том числе обтекатель, при наличии короткого воздухозаборника, могут быть использованы для эффективной сепарации частиц из воздушного потока.
Установлено, что на движение частиц после соударения с обтекателем существенное влияние оказывает величина коэффициента отражения, которая зависит от отношения диаметра частицы к толщине стенки обтекателя.
Проведенные расчеты траекторий движения
посторонних предметов для двух значений углов
конуса (βÊ) входного обтекателя двигателя показали, что после отражения от обтекателя при βÊ = 1180 большая часть посторонних предметов попадает на лопатку вентилятора в зону больших скоростей
èмалых относительных толщин передней кромки
èтела лопатки, что увеличивает вероятность их повреждения, чего не наблюдается при угле βÊ = 710.
Рисунок 5.8.2_1 – Расчетные траектории движения посторонних предметов в потоке воздуха перед воздухозабор ником и в его канале
Данным примером иллюстрируется взаимосвязь геометрии вентилятора с величиной вероятности попадания посторонних предметов в компрессор высокого давления, показывается необходимость тщательного (оптимального) выбора геометрических параметров (величина угла конуса обтекателя, угол наклона втулки рабочего колеса, расположение антивибрационной полки рабочего колеса и разделителя потока) при проектировании входных элементов газотурбинных двигателей.
Так, например, обтекатель двигателя ПС-90А имеет угол конуса βÊ = 900, который находится ближе к минимальному из рассматриваемого диапазона (710 <βÊ < 1180). Следовательно, отражение посторонних предметов обтекателем будет осуществляться в зону относительно небольших окружных скоростей. При этом максимально отодвинутый от рабочего колеса вентилятора разделитель потока и крутой подъем втулки рабочего колеса обеспечи- вают направление посторонних предметов в наружный контур. Вращение обтекателя позволяет уменьшить относительную составляющую скорости соударения посторонних предметов с рабочим колесом.
Вероятность соударения посторонних предметов с обтекателем двигателя превосходит 90 %. После соударения с обтекателем частицы движутся к концам лопаток вентилятора, распределяясь по сечению, близко к равномерному. Из сравнения типов траекторий, реализующихся после отраже-
273

Глава 5 - Компрессоры ГТД
ния частиц от обтекателя, установлено, что их попадание во внутренний контур маловероятно. При- чем не столкнувшиеся с обтекателем частицы имеют преимущественно осевое движение, и их траектории слабо меняются при соударении с лопатками.
Для защиты КВД от посторонних предметов, прошедших через тракт подпорных ступеней, предусмотрено их сепарирование (инерционная очистка воздуха) в полость наружного контура через кольцевую щель перепуска. Для защиты компрессора от попадания большеразмерных посторонних предметов (куски льда, птицы и т.д.) перед подпорными ступенями установлен ВНА с большой густотой и числом лопаток z = 77. Кроме того, средний поперечный линейный размер спрямляющего аппарата подпорных ступеней составляет менее 20 мм. Воздухозаборник и обтекатель двигателя в условиях обледенения обогреваются воздухом, отбираемым из КВД, что исключает образование на них льда.
Применение этих мероприятий, а также имеющиеся возможности зачистки забоин на лопатках вентилятора, замены отдельных лопаток вентилятора, модулей вентилятора и КНД позволяют уменьшить количество двигателей, снимаемых с самолета в эксплуатации по повреждениям лопаток.
Мероприятия, вводимые в конструкцию двигателя и летательного аппарата, обеспечивают достаточно высокий уровень защиты КВД от попадания посторонних предметов.
5.8.3 – Особенности конструкций систем защиты ГТД наземного применения от попадания посторонних
предметов
Для ГТУ наземного применения в отличие от авиационных ГТД, в силу менее жестких ограниче- ний по габаритам и массе, применяются стационарные воздухоприемные устройства со ступенчатой системой очистки воздуха.
Типовая схема воздухоочистки состоит из двухступенчатой системы:
-первая ступень очистки воздуха для улавливания частиц размером до 10 мкмциклонные блоки или щелевые инерционные воздухоочистители;
-вторая ступень очистки воздуха для улавливания более мелких частиц - фильтры тонкой очистки.
На период пуско-наладочных работ (первые 500-1000 ч работы) на лемнискатный воздухозаборник ГТУ устанавливается мелкоячеистая сетка для защиты компрессора от попадания элементов конструкции входного устройства.
5.9 – Особенности конструкции компрессоров ГТД наземного применения
Цикл работы промышленного двигателя существенно отличается от цикла работы авиационного - он характеризуется меньшей нагруженностью и большей продолжительностью. Таким образом, появляется возможность использовать отработавшие на авиационном двигателе детали на промышленном двигателе – дать им «вторую жизнь». Этот путь наиболее быстр и наименее затратен, однако не позволяет в полной мере использовать потенциал конструкции компрессора.
Оптимальным с точки зрения затрат и ожидаемой эффективности является второй путь – создание компрессора на базе высокоэффективного компрессора авиационного двигателя, прошедшего доводку и всеобъемлющие испытания. Подобное решение настолько привлекательно, что даже при необходимости создания компрессора другой производительности выгоднее моделировать (масштабировать) существующий компрессор, чем проектировать новый. Тем не менее, специфика использования компрессора в стационарной ГТУ определяет некоторые особенности конструкции и подходы к проектированию.
При создании компрессора для двигателя летательного аппарата очень остро стоит вопрос минимизации массы конструкции. Этим обуславливается необходимость применения материалов с возможно низкой удельной массой и высокими механическими свойствами: титановых сплавов, высоколегированных сталей и специальных сплавов. Такие материалы довольно дороги и, зачастую, труднообрабатываемы. Дополнительно для снижения массы в конструкции узлов авиационных двигателей применяют облегчающие проточки, фрезеровки, используют детали сложной пространственной конфигурации.
Для компрессора стационарного двигателя требование минимальной массы отходит на второй план. В связи с этим применение дорогих труднообрабатываемых материалов для снижения массы нецелесообразно. Желательно применение деталей простых форм с необходимым минимумом механической обработки. Требуемые запасы прочности обеспечиваются увеличением сечения деталей. На Рис. 5.9_1 показаны части корпуса компрессора авиационного двигателя и созданного на его базе корпуса компрессора двигателя наземного применения.
Ñбольшой осторожностью следует подходить
êвопросу замены марки материала особо ответ-
274
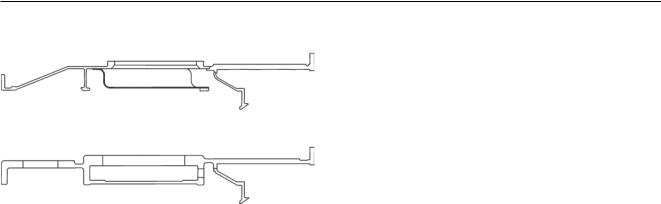
Глава 5 - Компрессоры ГТД
Рисунок 5.9_1 - Часть корпуса компрессора авиационного двигателя (вверху) и созданный на его базе корпус компрессора наземного двигателя
ственных и сложных в доводке деталей (валов, дисков, лопаток). Изменение материала этих деталей может потребовать проведения дорогостоящих экспериментальных работ - тензометрирования и ча- стотной отстройки лопаток, эквивалентно-цикли- ческих испытаний дисков и валов и т.п.
В качестве исполнительных механизмов поворота лопаток ВНА и НА могут применяться как традиционные для авиационных двигателей гидро-
èпневмоцилиндры, так и электропроводы. В слу- чае использования гидроприводов приходится предусматривать специальный гидронасос, поскольку в отличие от авиационного двигателя, где в качестве рабочего тела используется давление топлива основного топливного насоса, промышленные двигатели чаще всего используют газовое топливо.
Как известно, на величину требуемых монтажных и рабочих радиальных зазоров между рабочи- ми лопатками и корпусом, между лопатками НА
èротором влияют предполагаемые условия работы двигателя. Цикл работы промышленного двигателя по сравнению с авиационным характеризуется меньшей напряженностью, более узким диапазоном рабочих режимов, большей длительностью переходных режимов – запуска приемистости и сброса. Это позволяет в компрессоре промышленного двигателя иметь меньшие монтажные
èрабочие радиальные зазоры. Уменьшение радиальных зазоров положительно сказывается на параметрах компрессора – компрессоры промышленых двигателей, созданные на базе авиационных, имеют, как правило, более высокий, чем у прототипа КПД.
5.10 – Особенности работы компрессора в парогазовом цикле
Для эффективного использования ГТЭС в составе ПГУ необходимо поддержание максимально возможной температуры газа за турбиной (Òт*) при снижении температуры наружного воздуха (tн)
èпри дросселировании ГТД. Основной особенностью работы компрессора в парогазовом цикле является то, что поддержание Òт* обеспечивается прикрытием лопаток ВНА и НА компрессора для снижения расхода воздуха при постоянной частоте вращения.
Особенности работы компрессора в парогазовом цикле рассмотрим на примере компрессора ГТЭ-180.
Компрессор ГТЭ-180 является моделью
(ÊÌ = 3,477) КВД авиационного двигателя ПС-90А. Основными особенностями его работы в парогазовом цикле, связанными с изменением угла установки лопаток ВНА и НА от основной программы управления, являются:
-изменение запасов устойчивой работы компрессора;
-изменение максимального момента, действующего на вал механизации управления ВНА.
В связи с тем, что компрессор ГТЭ-180 находится на одном валу с электрогенератором, физи- ческие обороты компрессора всегда постоянны
èравны 3000 об/мин. При изменении температу-
ры окружающей среды tÍ изменяются приведенные обороты компрессора. Рассмотрим особенности работы компрессора в парогазовом цикле при
tÍ = +15°Ñ.
На Рис. 5.10_1 приведены зависимости температуры газа за турбиной ÒÒ* от мощности ГТУ при фиксированном положении ВНА и при прикрытии ВНА. На Рис. 5.10_2 приведена зависимость относительной мощности ГТУ от прикрытия ВНА. Как видно из рисунков, для поддержания постоянной ÒÒ* необходимо прикрытие лопаток ВНА. Но при снижении мощности ГТУ ниже 0,5NÍÎÌ поддержание постоянной ÒÒ* невозможно из-за ограничения величины прикрытия ВНА.
Прикрытие ВНА при фиксированной частоте вращения ротора приводит к изменению запасов устойчивой работы компрессора из-за рассогласования в работе отдельных ступеней. Максимальная величина прикрытия ВНА определяется исходя из условия, что запасы устойчивой работы компрессора должны быть не ниже минимально допустимого уровня.
275

Глава 5 - Компрессоры ГТД
Рисунок 5.10_1 – Зависимость температуры газа за турбиной от относительной мощности ГТУ при tÂÕ*= +15°Ñ
Рисунок 5.10_2 – Зависимость относительной мощности ГТУ от прикрытия ВНА от исходной программы регулирования
276
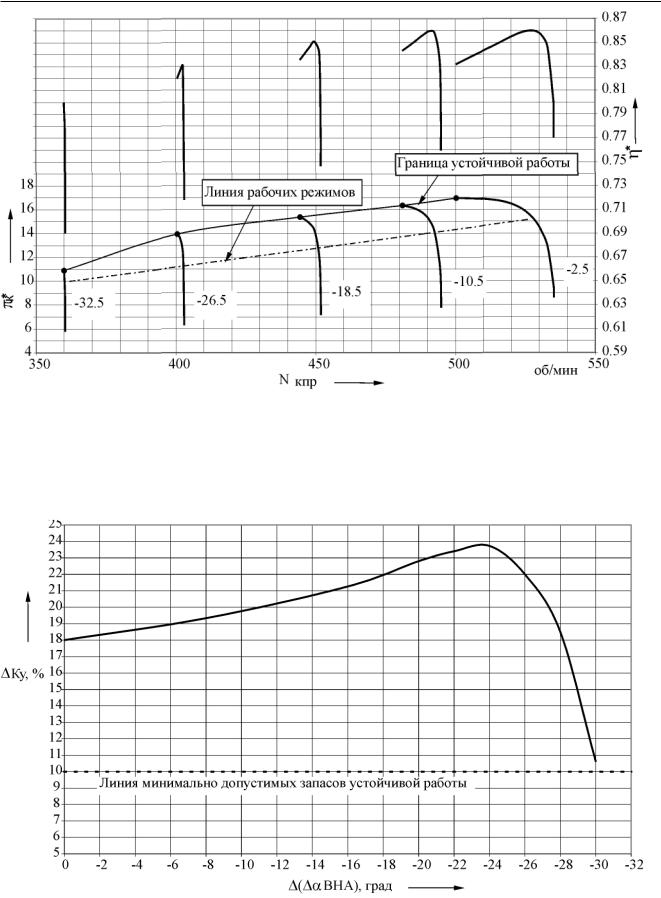
Глава 5 - Компрессоры ГТД
Рисунок 5.10_3 – Характеристики компрессора ГТЭ-180 на режиме nпр=3000 об/мин (tвх*=+15°С) при различных углах ВНА
Рисунок 5.10_4 - Зависимость запасов устойчивой работы компрессора в парогазовом цикле
(nÏÐ=3000 îá/ìèí, tÂÕ=+15°С) от прикрытия ВНА от исходной программы регулирования
277
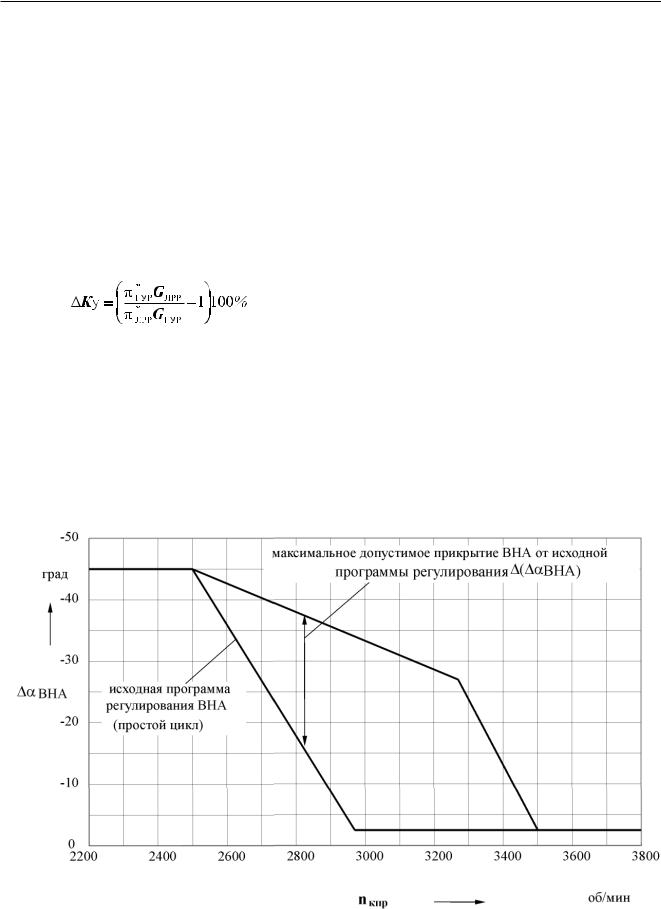
Глава 5 - Компрессоры ГТД
Для определения максимальной величины прикрытия ВНА проведены расчетно-эксперимен- тальные работы по определению напорных характеристик компрессора при различных значениях прикрытия ВНА от исходной программы регулирования.
На Рис. 5.10_3 приведены расчетно-экспери- ментальные напорные характеристики компрессора при различных значениях прикрытия ВНА от исходной программы регулирования компрессора и расчетная линия рабочих режимов. На Рис. 5.10_4 представлены фактические и минимально допустимые запасы устойчивой работы компрессора по критерию:
Из рисунка видно, что прикрытие ВНА от исходной программы регулирования более чем на 30° приводит к снижению запасов устойчивости ниже допустимого уровня. Поэтому максимальная вели- чина прикрытия ВНА от исходной программы регулирования при tÂÕ* = +15°С равна 30°.
На Рис. 5.10_5 представлена зависимость максимального допустимого прикрытия лопаток ВНА от исходной программы регулирования ∆(∆αÂÍÀ)
от температуры воздуха на входе в компрессор. На Рис. 5.10_6 приведена зависимость максимального допустимого прикрытия ВНА от приведенной частоты вращения компрессора.
Прикрытие лопаток ВНА и НА при постоянной частоте вращения приводит к изменению максимального момента, действующего на вал механизма управления ВНА и НА. Это изменение в основном связано с увеличением аэродинамических сил, действующих на лопатки ВНА и НА.
По данным расчета прикрытие ВНА от исходной программы регулирования на 24 градуса (при nÏÐ = 3000 об/мин) приводит к изменению аэродинамического момента от минус 21,5 кгс·м до 208 кгс·м. Так как на данном режиме работы компрессора крутящий момент от аэродинамических сил составляет не менее 25% от суммарного момента (с учетом момента от сил трения в механизме управления), то работа компрессора в парогазовом цикле требует учета увеличения усилия на штоке механизма управления ВНА и НА.
5.11 – Материалы, применяемые для деталей компрессоров
Выбор материалов компрессора осуществляется исходя из свойств материала в рабочих усло-
Рисунок 5.10_5 - Зависимость максимального допустимого прикрытия ВНА от приведенной частоты вращения компрессора
278

Глава 5 - Компрессоры ГТД
Рисунок 5.10_6 – Максимальное допустимое прикрытие ВНА от исходной программы регулирования в зависимости от температуры воздуха на входе в компрессор
виях эксплуатации. Деталь, изготовленная из выбранного материала, должна удовлетворять нормам прочности при заданных надежности и ресурсе.
5.11.1 – Характеристики применяемых материалов
В компрессоре применяются четыре основные группы материалов:
-алюминиевые сплавы - в диапазоне температур, не превышающих 250îÑ;
-титановые сплавы –в диапазоне температур, не превышающих 500îÑ;
-стали и жаропрочные сплавы - в диапазоне температур, превышающих 450…500îÑ;
-полимерные композиционные материалы -
âдиапазоне температур, не превышающих 150…250îÑ.
Некоторые свойства перечисленных материалов приведены в таблице 5.11.4_1
5.11.1.1 – Титановые сплавы
В настоящее время наиболее широко в мировой практике применяются в конструкции компрессоров титановые сплавы. Титановые сплавы при сравнительно небольшой плотности 4,5 г/см3 против 7,8…8,3 г/см3 у сталей) обладают соизме-
римым со сталями пределом прочности. Поэтому, заменяя стальные детали на титановые, можно полу- чить заметное снижение массы компрессора, а зна- чит и всего двигателя в целом.
В то же время необходимо учитывать, что с увеличением рабочей температуры механические свойства титановых сплавов заметно падают. Кроме этого, титановые сплавы чувствительны к концентраторам напряжений, как заложенным в конструкции детали, так и появившимся в результате нарушения технологического процесса при изготовлении. Немаловажным фактором является также возможное нарушение температурного режима при изготовлении и эксплуатации деталей из титановых сплавов. Все перечисленное может привести к заметному снижению сопротивления усталости.
Еще одним фактором, который необходимо учитывать при проектировании деталей из титановых сплавов, является так называемый «титановый пожар». Это явление возникает при продолжительном непрерывном контакте двух взаимно подвижных поверхностей из титановых сплавов. При этом детали разогреваются и происходит их сварка и даже возгорание. Для того, чтобы освободиться от такого явления, на одну из деталей, находящихся в зоне вероятного контакта, следует нанести прирабатываемое покрытие. В некоторых
279

Глава 5 - Компрессоры ГТД
случаях даже принимают решение изготовить одну из деталей из другого материала, в том числе из стали, хотя это и ведет к увеличению массы конструкции.
5.11.1.2 – Алюминиевые сплавы
Алюминиевые сплавы обладают еще меньшей массой - 2,65…2,85 г/см3. Однако их механические свойства и диапазон рабочих температур значительно ниже, чем сталей и титановых сплавов и сталей, что резко снижает область их применения. Препятствием для применения таких сплавов также является сравнительно низкая коррозионная стойкость. Материал требует применения специальных эмалевых или других покрытий для предотвращения коррозии.
5.11.1.3 – Стали и жаропрочные никелевые сплавы
Эти материалы являлись бы оптимальными для изготовления деталей компрессора, поскольку они обладают наилучшими механическими свойствами, самым широким среди рассматриваемых материалов диапазоном рабочих температур, высокими эрозионными и коррозионными свойствами. Все это обусловило их полное доминирование на раннем этапе существования ГТД. Однако зада- ча обеспечения минимальной массы может решаться только применением более легких материалов.
5.11.1.4 – Полимерные композиционные материалы
В настоящее время в авиадвигателестроении все шире применяются ПКМ, обладающие относительно высокими механическими свойствами при сравнительно низкой удельной массе (см. таблицу 5.13.4_1). До недавнего времени главным ограничением их применения являлись невысокие рабочие температуры - до 100îС, но за последний годы этот предел достиг 250îС (для стеклопластиков), а для отдельных новых материалов и 350îÑ.
ПКМ состоит из двух основных компонентов: связующего (синтетической смолы) и волокнистого наполнителя (ткань или однонаправленный жгут из угле-, органоили стекловолокна). Наполнитель воспринимает основные нагрузки, а связующее формирует из отдельных частей наполнителя (ткани, жгута, ленты) единое целое и обеспечивает распределение нагрузки. Узлы из ПКМ можно армировать металлическими элементами. Таким образом, готовый узел можно получить практически не применяя механическую обработку, и иметь при этом коэффициент использования материала близким к 100%. Однако стоимость отдельных компонентов материала и трудоемкость изготовления таких узлов, по сравнению с аналогичным металлическим, в несколько раз выше, что пока ограни- чивает сферу применения ПКМ в серийных двигателях.
|
Свойства материалов, применяемых компрессорах ГТД |
Таблица 5.11.4_1 |
|||||
|
|
||||||
|
|
|
|
|
|
|
|
|
|
|
|
|
Предел |
|
|
|
Плотность |
Коэф. линейного расширения α, |
прочности |
|
|||
Материал |
при |
Модуль упругости Е |
|||||
ρ ,г/см3 |
|
|
|
||||
|
|
|
|
|
растяжении |
|
|
|
|
|
|
|
σ В, МПа |
|
|
|
|
100oС |
200oС |
400оС |
|
||
ÏÊÌ |
1,4…1,9 |
|
|
|
900…1100 |
100000…130000 |
|
|
|
|
|
|
|
|
|
Алюминиевые |
2,65…2,85 |
1,0016 |
1,0039 |
1,0087 |
360…380 |
|
|
сплавы |
|
||||||
|
|
|
|
|
|
||
|
|
|
|
|
|
|
|
Титановые |
4,4…4,55 |
1,0007 |
1,0016 |
1,0037 |
950…1200 |
|
|
сплавы |
|
||||||
|
|
|
|
|
|
||
Стали |
7,8…8,3 |
1,0012 |
1,0031 |
1,0068 |
900…1000 |
|
|
Жаропрочные |
8,2…8,35 |
1,0010 |
1,0024 |
1,0054 |
1000…1200 |
110000…160000 |
|
сплавы |
|||||||
|
|
|
|
|
|
||
|
|
|
|
|
|
|
280

Глава 5 - Компрессоры ГТД
5.12 – Англо-русский словарьминимум
adiabatic – адиабатический aerodynamic – аэродинамика air bleed cavity – полость отбора airflow – воздушный поток airfoil – профиль (лопатки) analysis – расчет
aspiration – всасывание axial – осевой
axisymmetric – осесимметричный bearing – подшипник
blade – рабочая лопатка bleed – отбор (воздуха)
boundary layer – пограничный слой booster – подпорные ступени centrifugal – центробежный
chord – хорда clearance – зазор coating – покрытие cooling – охлаждение
compressor – компрессор core – газогенератор cover – крышка, кожух disc – диск
distribution – распределение downstream – вниз по потоку eddy – вихрь
edge – кромка fan – вентилятор
flowpath – проточная часть hatch – люк
heating – нагрев
HPC (high pressure compressor) – КВД (компрессор высокого давления)
honeycomb lining – сотовое уплотнение incidence angle – угол атаки
inlet – âõîä
IGV (inlet guide vane) – входная направляющая лопатка
isentropic – изоэнтропический leakage – перетекание
ledge – выступ lid – крышка
lip – выступ, фланец load – нагрузка
loss – потери
LPC (low pressure compressor) – КНД (компрессор низкого давления)
Mach number – число Маха noise – шум
nut - гайка
operating line – линия рабочих режимов
parameter – параметр performance – характеристика piece –деталь
pin -штифт
radial – радиальный
ratio – отношение, коэффициент repair – ремонт
Reynolds number – критерий Рейнольдса rib – ребро
ring – кольцо
rod – стержень, тяга, шток roll – ролик
root – корень (хвостовик) лопатки rotation – вращение
rotor – ротор screw – винт, болт seal – уплотнение
secondary flows – вторичное течение section – сечение
shaft – вал shape – форма
shock – удар, скачок уплотнения shroud – бандаж
simulation – моделирование slot – щель, канавка
snubber – демпфирующее устройство span – размах, хорда
spull – барабан
splitter – разделитель, рассекатель stability – устойчивость
stage – ступень stagnation – торможение stall – срыв
stator – статор stream – поток
streamline – линия тока strut – стойка
surge – помпаж thickness – толщина thread – резьба throat – горло thrust – тяга
trailing edge – выходная кромка
tip speed – окружная скорость на периферии РК unit – элемент, единица измерения
valve – клапан velocity – скорость viscosity – вязкость wall – стенка
wave – волна
281

Глава 5 - Компрессоры ГТД
5.13 – Перечень использованной литературы
5.13.1.Б.Н.Юдаев. Техническая термодинамика. Теплопередача. Учебное пособие для втузов. – М.: Высшая школа, 1988г.
5.13.2.В.И.Локай, М.Н.Бодунов, В.В.Жуйков, А.В.Щукин. Теплопередача в охлаждаемых деталях газотурбинных двигателях летательных аппаратов. - М.: Машиностроение, 1985г.
5.13.3.Основы теплопередачи в авиационной и ра- кетно-космической технике. -М.: Машиностроение, 1975г.
5.13.4.Аэродинамика компрессоров: Пер. с англ./ Н.Кампсти.– М.: Мир, 2000г.
5.13.5.Конструкция и проектирование авиационных газотурбинных двигателей. Под общей редакцией Д.В.Хронина - М.: Машиностроение, 1989 г.
5.13.6.Авиационные правила. Часть 33. Нормы летной годности двигателей воздушных судов./ Межгосударственный Авиационный Комитет
5.13.7.Техническая справка. Влияние компоновки самолета на защищенность двигателей от посторонних предметов, забрасываемых с поверхности ВПП. ГосНИИ ГА - Москва, 2001 г.
5.13.8.Техническая справка ¹ 25602. Силовая установка ПС-90А-12. Защита от попадания посторонних предметов в двигатель.
5.13.9.К.В.Холщевников, О.Н.Емин, В.Т.Митрохин. Теория и расчет авиационных лопаточных машин. – М.: Машиностроение, 1986г.
5.13.10.Ю.С. Подубуев, К.П. Селезнев. Теория и расчет осевых и центробежных компрессоров. – М.: Машгиз1957
5.13.11.Технический отчет ¹ 39155. Двигатель ГТЭ-180. Расчетно-экспериментальные характеристики компрессора ГТЭ-180, уточненные по результатам испытаний на установке К-2-180.
5.13.12.Технический отчет ¹ 39224. Двигатель ГТЭ-180. Испытание модели компрессора в составе установки К-2-180 (053).
5.13.13.Методология проектирования осевого компрессора. Ф.Ш.Гельмедов, В.И.Милешин и др. ЦИАМ - Теплоэнергетика. 2002. ¹9. С.19 —28.
5.13.14.Применение метода установления для рас- чета низкочастотных течений. Д.Чой, Ч.М.Меркл - Аэрокосмическая техника. 1986. ¹ 7. С. 29 — 40.
5.13.15.THE JET ENGINE – Rolls-Royce plc
282
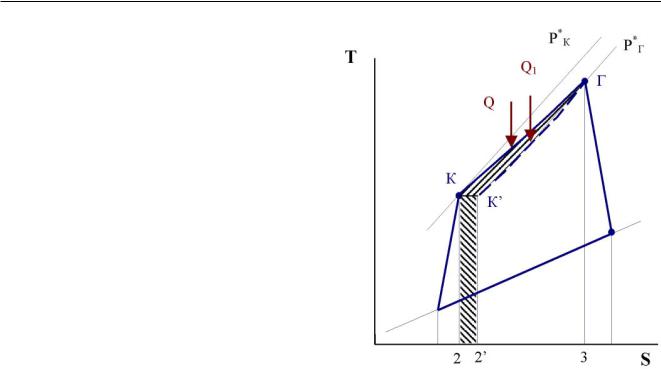
Глава 6 - Камеры сгорания
Глава 6 – Камеры сгорания ГТД
«простом» термодинамическом цикле ГТД (см.главу 2) на участке К-Г (см. Рис. 6_1) к потоку рабочего тела подводится тепло.
ÂГТД этот процесс осуществляется в камере сгорания (КС) (см. Рис. 6_2). Тепло подводится за счет сгорания топлива, то есть преобразования химической энергии топлива в тепловую, при этом температура рабочего тела возрастает от значения
ÒÊ* (за компрессором) до ÒÃ* (на входе в турбину). Реальный процесс в КС отличается от идеаль-
ного наличием потерь давления от Ð*Ê äî Ð*Ã . Потери давления в КС складываются из гидравли- ческих потерь (потерь трения) и потерь от подвода тепла к потоку рабочего тела. Гидравилические потери в свою очередь можно разделить на составляющие потери:
- в диффузоре, - в кольцевых каналах,
- на втекание воздуха в отверстия жаровой трубы и элементы фронтового устройства (ФУ),
- на смешение струй.
Как видно из диаграммы, приведенной на Рис. 6_1, гидравлические потери частично компенсируются, т.к. работа трения преобразуется в тепло, которое возвращается в работу термодинами- ческого цикла. Однако потери давления в КС приводят к уменьшению степени понижения давления газа в турбине и сопле и, соответственно,
êуменьшению полезной работы и к.п.д. цикла. Кроме потерь давления процессы в КС сопро-
вождаются потерями тепла за счет его рассеивания в окружающее пространство и за счет неполного сгорания топлива.
Потери тепла в окружающее пространство по сравнению с количеством тепла, подводимым к рабочему телу в, КС ТРД составляют 0,005…0,01%. А в ТРДД эти потери отсутствуют, т.к. тепло от корпуса КС подводится к воздуху наружного контура, и, таким образом, участвует в работе цикла.
Экономичность двигателя находится в прямой зависимости от полноты сгорания топлива. В современных ГТД процесс сгорания топлива в КС достаточно хорошо организован, поэтому полнота сгорания топлива в них достигает величины ηà = 0,995…0,999. При термодинамических расче- тах двигателя тепло, подведенное к рабочему телу, вычисляется сразу с учетом полноты сгорания топлива в КС. Для увеличения эффективности двигателя и КС, в частности, на стадии проектирования решаются задачи по минимизации потерь.
Рисунок 6_1 - Подвод тепла в цикле ГТД
-площадь 2КГ32 – сумма внешнего тепла и тепла трения, лежащая под линией КГ реального подвода тепла в КС (Q);
-площадь 2’К’Г32’ – внешнее тепло (Q1), определенное тем же интервалом температур (Тг – Тк) с учетом полноты сгорания;
-площадь 2КГК’2’ – тепло трения
âреальном процессе подвода тепла
âÊÑ
Особенностью узла КС является то, что происходящие в нем процессы распыла топлива, перемешивания топлива с воздухом, горения топливовоздушной смеси, теплообмена - сложны. Даже новейшее программное обеспечение, позволяющее в настоящее время рассчитывать до тысячи протекающих при работе КС химических реакций, описывает эти процессы не в полной мере. Как следствие - результаты расчетов недостаточно точны. Здесь следует заметить, что в расчетах КС используется большое число эмпирических зависимостей и коэффициентов, которые определены для конкретной конструкции и требуют корректировки при расчете другой. В связи с этим для получения требуемых характеристик КС требуется большой объем дорогих экспериментально-доводочных работ. Рабочий проект формируется в результате нескольких этапов расчетов и экспериментально-до- водочных работ, в том числе - по подтверждению работоспособности смежных узлов, например, турбины.
283

Глава 6 - Камеры сгорания
Рисунок 6_2 – КС Двигателя ПС-90А
6.1 – Требования к КС
КС – часть ГТД, и к ней предъявляются те же общетехнические требования, что и ко всему двигателю и другим его узлам. Это требования по массе, надежности, технологичности и т.д. (см. раздел 2.3).
К КС кроме общих требований предъявляются специфические требования. Рассмотрим их подробнее.
Минимальные габаритные размеры КС. Они влияют на продольные и поперечные размеры двигателя, и следовательно - на его массу. Обычно габариты КС (т.е. е¸ объем) характеризуются вели- чиной удельной теплонапряженности QV, которая равна отношению количества тепла, выделившегося в единицу времени, к объему жаровой трубы и давлению на входе в КС:
Q |
= |
|
|
Q |
= 3600 |
HU GT |
η |
à |
(6.1-1) |
V |
P* |
|
|||||||
V |
|
|
V P* |
||||||
|
|
|
|
Ж Ê |
|
Ж K |
|
|
ãäå ÍU - низшая теплотворная способность топлива (Дж/кг);
GT - секундный расход топлива (кг/с); VÆ - объем жаровой трубы (ì3);
ÐÊ* - давление воздуха (Па).
Чем больше теплонапряженность при заданном расходе топлива, тем меньше объем КС. Теплонапряженность КС современных ГТД составляет (3,5…6,5)106 (Äæ/÷ ì3 Ïà).
Высокая полнота сгорания топлива на всех режимах работы двигателя. Полнота сгорания топлива характеризуется коэффициентом полноты сгорания ηÃ, под которым обычно понимают отношение количества тепла, выделившегося при сгорании единицы массы топлива, к его теплотворной способности.
Минимальные потери полного давления в КС. Потери характеризуются коэффициентом восстановления полного давления:
σÊÑ = Ð*à / Ð*Ê |
(6.1-2) |
В современных КС коэффициент восстановления полного давления составляет 0,94…0.96.
284

Глава 6 - Камеры сгорания
Широкие пределы устойчивого горения. Пределы устойчивого горения определяются условиями эксплуатации самолета. Пламя не должно погасать в заданном диапазоне изменения отношения топлива/воздух, давления, скорости и при попадании на вход двигателя воды, льда и посторонних предметов.
Надежный розжиг топлива в земных и высотных условиях. В земных условиях розжиг должен быть обеспечен в диапазоне температур от минус 40° до плюс 40°С. Должен быть обеспечен розжиг топлива в условиях высокогорного аэродрома – до высоты 4,5 км. Высотность розжига для гражданских самолетов – 9 км.
Отсутствие пульсаций давления (вибрационного горения).
Поле температур на выходе из КС. Поле температур должно в радиальном направлении иметь эпюру, определяемую предельно допустимыми напряжениями в рабочих лопатках турбины и соплового аппарата. Конкретный характер эпюры температур по радиусу лопатки выбирают в зависимости от конструктивных особенностей турбины (величины и формы рабочей лопатки, ее материала, способа охлаждения и т.д.).
Рабочая лопатка турбины при своем вращении воспринимает среднюю температуру за КС. Поэтому для оценки неравномерности поля температур, воздействующих на рабочие лопатки, необходимы температуры, осредн¸нные на i-м радиусе. Такая неравномерность задается радиальной эпюрой относительных средних избыточных температур (определения даны в соответствии с отраслевым стандартом [6.9.1]):
θiCP = (Ò*Ãi - Ò*Ê) / (Ò*Ã - Ò*Ê) |
(6.1-3) |
ãäå θiCP - относительная средняя избыточная температура газа на i-м радиусе выходного сечения КС;
Ò*Ãi- средняя температура на i радиусе;
Ò*Ã - средняя температура газа на выходеиз КС; Ò*Ê- температура воздуха на входе в КС.
Кроме того, для обеспечения работы лопаток соплового аппарата турбины задается радиальная эпюра максимальных относительных избыточных температур газа на выходе из КС, которая определяется как:
|
θimax= (Ò*Ãimax - Ò*Ê) / (Ò*Ã - Ò*Ê) (6.1- 4) |
ãäå θimax |
- максимальная относительная избыточ- |
|
ная температура газа на i-м радиусе |
|
выходного сечения КС; |
Ò* |
Ãimax |
- максимальное значение температуры |
|
газа на i-м радиусе выходного |
|
|
|
|
|
|
сечения КС. |
Максимальная неравномерность поля температуры газа за КС характеризуется величиной, называемой максимальной относительной избыточ- ной температурой газа θmax, и определяется выражением:
θmax= (Ò*Ãmax - Ò*Ê) / (Ò*Ã - Ò*Ê) (6.1-5)
ãäå Ò*Ãmax- максимальное значение температуры газа за КС
Уровень выбросов. Уровень выбросов дыма (SN (Smoke number)), несгоревшего топлива и газообразных веществ, загрязняющих атмосферу - оксидов азота (NOx), оксидов углерода (СО), несгоревших углеводородов (НС) - должен соответствовать международным нормам ИКАО [6.9.2] и Авиационным правилам [6.9.3].
На элементах конструкции КС не должен откладываться нагар.
Способность работать на различных топливах как отечественных, так и зарубежных.
Рисунок 6.1_1 – Радиальные эпюры температур газа за КС
6.2 – Схемы КС
При всем разнообразии конструкций КС е¸ схему и происходящие в ней процессы можно представить следующим образом (см. Рис. 6.2_1 и 6.2_2). Воздух поступает из компрессора в КС с большой скоростью - в современных двигателях до 150 м/с. Потери полного давления в КС при подводе тепла к потоку, движущемуся с такой скоростью, были бы недопустимыми и достигали бы четвертой
285
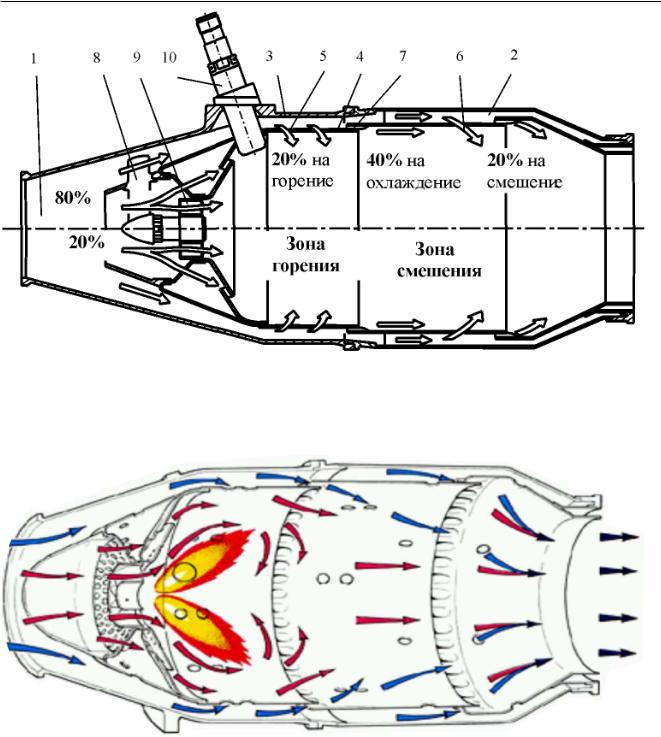
Глава 6 - Камеры сгорания
Рисунок 6.2_1 – Общая схема и распределение воздуха в КС (Печатается с разрешения Rolls-Royce plc.) 1 – диффузор; 2 – кольцевые каналы; 3 – корпус КС; 4 – жаровая труба;
5 – отверстия первичной зоны; 6 - отверстия зоны смешения; 7 - отверстия охлаждения; 8 - топливная форсунка; 9 – фронтовое устройство; 10 – свеча зажигания
Рисунок 6.2_2 – Модель воздушного потока и стабилизации пламени в КС (Печатается с разрешения Rolls-Royce plc.)
части повышения давления воздуха в компрессоре. |
Далее воздух поступает в кольцевые каналы |
Для снижения потерь давления и преобразования |
2 между корпусом 3 и жаровой трубой 4, а затем |
части кинетической энергии в прирост статическо- |
в жаровую трубу. В жаровой трубе воздух распре- |
го давления скорость воздушного потока после ком- |
деляется по отверстиям двух условных зон – зоны |
прессора должна быть значительно снижена. Поэто- |
горения 5 (первичная зона) и зоны смешения 6. Кро- |
му на всех ГТД после компрессора располагается |
ме этого, воздух также поступает в отверстия 7 для |
диффузор 1 (см. Рис. 6.2_1) [6.9.4]. |
охлаждения горячих стенок жаровой трубы. Топ- |
286

Глава 6 - Камеры сгорания
ливо подается в жаровую трубу через форсунки 8. В первичной зоне с помощью фронтового устройства (ФУ) 9 организуется зона с малыми скоростями. В этой зоне процесс горения поддерживается за счет циркуляционного течения продуктов сгорания, непрерывно поджигающих свежую топливовоздушную смесь (ТВС). При запуске двигателя воспламенение ТВС в КС осуществляется с помощью электрической свечи 10 или воспламенителя (см. раздел 6.4.5).
Циркуляционное течение в первичной зоне обеспечивает стабильность и эффективность горения. Отношение расхода топлива и воздуха в первичной зоне является важнейшим фактором, влияющим на процесс горения и рабочие характеристики КС. Для обеспечения устойчивого процесса горения на всех режимах работы двигателя в первичную зону подается только часть воздуха. В зависимости от способа сжигания топлива это количество воздуха может меняться (см. раздел 6.3.2.). На Рис. 6.2_1 приведено распределение воздуха в жаровой трубе для типичной КС, где 20% воздуха поступает во ФУ, а 80% в жаровую трубу(20% в зону горения, 20% в зону смешения и 40% на охлаждение стенок). Иногда первичную зону (зону горения) разделяют на две зоны - зону циркуляции и зону догорания топлива (промежуточную зону).
В зоне смешения продукты сгорания разбавляются воздухом до требуемой температуры, тем самым на выходе из КС формируется стабильное и оптимальное поля температур для обеспечения работоспособности турбины.
6.2.1 – Основные схемы КС
Наибольшее распространение в ГТД получи- ли три схемы КС - трубчатые, трубчато-кольцевые
èкольцевые.
Âтрубчатой КС каждая жаровая труба имеет отдельный корпус и образует индивидуальную трубчатую КС (см. Рис. 6.2.1_1). В авиационных ГТД КС такой схемы выполняют в виде блока из
нескольких индивидуальных трубчатых КС. На Рис. 6.2.1_1 показана трубчатая КС с восемью индивидуальными трубчатыми КС, расположенными вокруг внутреннего корпуса 1 двигателя. Корпуса 2 каждой индивидуальной КС соединяются с выходом компрессора при помощи фланца 3. Между собой корпуса индивидуальных КС и жаровые трубы соединены муфтами 4 для переброса пламени при розжиге ТВС и выравнивания давления между жаровыми трубами. Кроме того, корпуса КС соединены между собой дренажными трубами 5 для слива топлива при неудавшемся запуске
двигателя. Холодная передняя часть КС, в которой расположена система подачи топлива, отделена от горячей задней части и горячих корпусов турбины, при соприкосновении с которыми может воспламениться топливо, противопожарной перегородкой 6.
Топливо в КС подается через форсунки 7. Топливо к форсункам подается через коллектор 8 первого контура и коллектор 9 второго контура. На входе в КС расположен диффузор 10. Жаровые трубы 1 (см. Рис. 6.2.1_2) для фиксации от перемещения
âрадиальном направлении опираются в передней части на форсунку 2, вставленную в завихритель 3, а в осевом направлении фиксируются подвесками 4. Воздух через воздухозаборник 5 поступает в первичную зону жаровых труб и далее через перфорацию - во ФУ 6 и завихритель. Для обеспечения необходимого соотношения между расходом воздуха и топлива через отверстия 7 дополнительно подводится воздух. Воздух в зону смешения поступает через отверстия 8. Стенки жаровых труб охлаждаются воздухом, проходящим через гофрированные щели 9. Выходная часть жаровых труб 10 телескопически входит в индивидуальные газосборники 1 (см. Рис. 6.2.1_3), образующие кольцевой вход в первый сопловой аппарат 2 турбины.
Трубчатые КС применялись на ранних ГТД фирмы Rolls-Royce (Nene), Allison (J-33), General Electric (J-47), ФГУП «Завод им. В.Я. Климова» (ВК-1) и др.
Трубчато-кольцевая КС также состоит из нескольких отдельных жаровых труб и газосборников, но располагаются они в общем кольцевом канале между корпусами. На Рис. 6.2.1_4 показана трубчато-кольцевая КС двигателя ÏÑ-90À. КС комбинированного типа с двенадцатью жаровыми трубами и кольцевым газосборником. Применение кольцевого газосборника отличает представленную КС от обычных схем трубчато-кольцевых КС с индивидуальными газосборниками.
Рассмотрим конструкцию КС двигателя ПС90А более подробно.
Наружный 1 и внутренний 2 корпусы образуют кольцевой канал, в котором располагаются жаровые трубы 3 и кольцевой газосборник, состоящий из наружного 4 и внутреннего 5 колец. Кроме того, наружный и внутренний корпусы вместе со скрепляющими их двенадцатью силовыми стойками 6 входят в силовую схему двигателя. На входе
âКС наружное кольцо 7 и внутреннее 8 диффузора образуют кольцевой диффузорный канал с безотрывным течением в начальном участке и с внезапным расширением потока на выходном участке (см. раздел 6.4.1). Наружное кольцо 7 диффузора
287
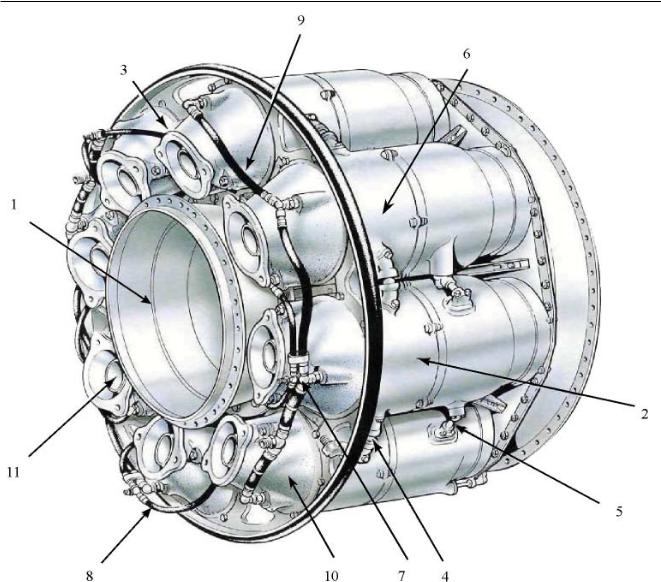
Глава 6 - Камеры сгорания
Рисунок 6.2.1_1 – Трубчатая КС (Печатается с разрешения Rolls-Royce plc.)
1 – внутренний корпус двигателя; 2 – корпус; 3 – фланец, соединения с компрессором; 4 - пламеперебрасывающая муфта; 5 – дренажная труба; 6 – противопожарная перего-
родка; 7 - форсунка; 8 – коллектор первого контура; 9 – коллектор второго контура; 10 – диффузор; 11 – заборник первичного воздуха
образует вместе с наружным корпусом полость 9, |
Жаровые трубы фиксируются от перемещения |
из которой через фланцы 10 осуществляется отбор |
в радиальном направлении в передней части при по- |
воздуха на самолетные нужды и агрегаты системы |
мощи форсунок, а в задней - опираются на кольца |
автоматического регулирования двигателя. |
газосборника. В осевом направлении десять из две- |
На корпус КС устанавливается двенадцать |
надцати жаровых труб фиксируются при помощи |
топливных форсунок 11, коллекторы первого 12 |
подвесок 18, а две жаровые трубы - при помощи све- |
и второго 13 контуров с двадцатью четырьмя тру- |
чей зажигания. В стенках жаровых труб выполне- |
бопроводами 14 подвода топлива к форсункам. Для |
но два ряда отверстий 19 и 20 для подвода воздуха |
розжига ТВС в КС в двух жаровых трубах установ- |
в первичную зону и зону смешения, соответственно. |
лены по одной свече зажигания 15. Воспламене- |
По боковым поверхностям фланцев 21 жаровые тру- |
ние топлива в других жаровых трубах происходит |
бы стыкуются между собой, а по верхним и нижним |
через пламеперебрасывающие патрубки 16, соеди- |
поверхностям телескопически сопрягаются с коль- |
ненные пламеперебрасывающими муфтами 17. |
цами газосборника. Кольца газосборника образуют |
288
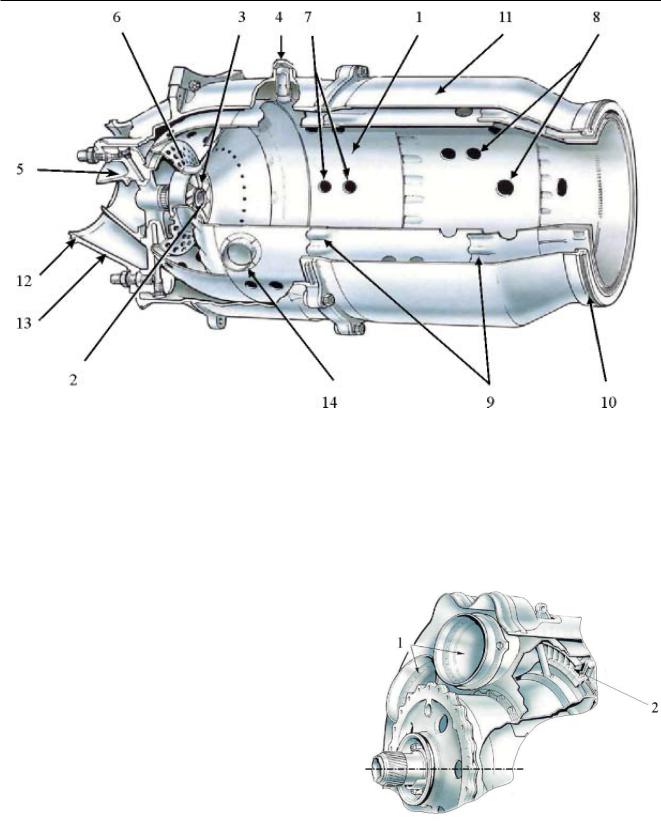
Глава 6 - Камеры сгорания
Рисунок 6.2.1_2 – Индивидуальная трубчатая КС (Печатается с разрешения Rolls-Royce plc.)
1 – жаровая труба; 2 – форсунка; 3 – завихритель; 4 – подвеска жаровой трубы; 5 - заборник первичного воздуха; 6 – фронтовое устройство; 7 – отверстия первичной зоны; 8 - отверстия зоны смешения; 9 – гофрированные щели системы охлаждения; 10 - уплотнительное кольцо; 11 - корпус; 12 – выход из компрессора присоединительный фланец; 13 – диффузор; 14 - пламеперебрасывающий патрубок
кольцевой канал, в котором происходит формирование на выходе из КС газового потока с наименьшей неравномерностью температур и давлений по окружности и необходимой радиальной эпюрой. Задняя часть кольца газосборника наружного является корпусом соплового аппарата 22 ТВД.
На фланцы наружного корпуса установлены двенадцать перепускных труб 23, которые проходят через проточную часть КС и вставляются во втулки на корпусе внутреннем. Через перепускные трубы проходят трубопроводы масляной, воздушной и суфлирующей систем двигателя, а также сообщается с наружным контуром полость, расположенная под корпусом внутренним. Для эндоскопического контроля КС на наружном корпусе расположены двенадцать лючков 24.
Трубчато-кольцевые КС получили широкое распространение в ГТД. Наиболее известные двигатели с трубчато-кольцевыми КС – зарубежные RR-Spay, Konway, Tay, JT-8D Pratt&Whitney и оте- чественные Р-11Ф-300, Р-15Б-300, Д-30, Д-30КУ
èего модификации, Ä-30Ô6, ÏÑ-90À è äð.
Âкольцевой КС (см. Рис. 6.2.1_5) между образующими кольцевой канал наружным 1 и внут-
Рисунок 6.2.1_3 – Газосборник трубчатой КС (Печатается с разрешения RollsRoyce plc.)
1 – индивидуальные газосборники;
2 – первый сопловой аппарат турбины.
289
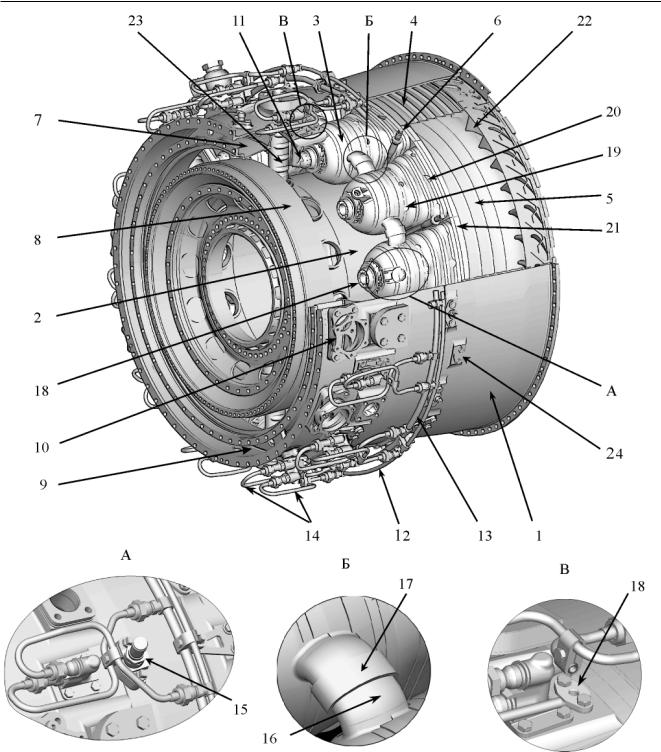
Глава 6 - Камеры сгорания
Рисунок 6.2.1_4 – Трубчато-кольцевая камера сгорания двигателя ПС-90А 1 – наружный корпус КС; 2 - внутренний корпус КС; 3 - жаровая труба; 4 – наружное коль-
цо газосборника; 5 – внутреннее кольцо газосборника; 6 - силовая стойка; 7 - наружное кольцо диффузора; 8 – внутреннее кольцо диффузора; 9 - полость отборов воздуха; 10 - фланцы отбора воздуха; 11 – форсунка; 12 – топливный коллектор первого контура;
13 - топливный коллектор второго контура; 14 – трубопроводы подвода топлива к форсунке; 15 – свечи зажигания; 16 – пламеперебрасывающий патрубок; 17 - пламеперебрасывающая муфта; 18 - подвеска жаровой трубы; 19 – отверстия первичной зоны; 20 – отверстия зоны смешения; 21 - рамочный фланец жаровой трубы; 22 - сопловой аппарат ТВД; 23 – перепускная труба; 24 - лючок осмотра.
290
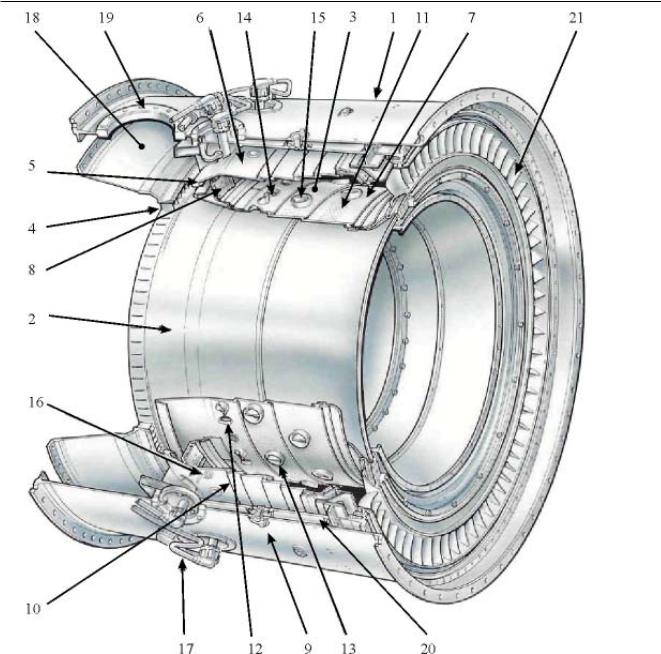
Глава 6 - Камеры сгорания
Рисунок 6.2.1_5 – Кольцевая КС двигателя RB-211 (Печатается с разрешения Rolls-Royce plc.)
1 – наружный корпус; 2 – внутренний корпус; 3 – жаровая труба; 4 - направляющий аппарат компрессора; 5 – кольцо диффузора наружное; 6 – наружная стенка жаровой трубы; 7 - внутренняя стенка жаровой трубы; 8 – фронтовая плита; 9 – подвеска жаровой трубы; 10 - пояс системы охлаждения; 11 – отверстия перфорации; 12 – отверстия подвода воздуха в первичную зону; 13 – отверстия зоны смешения; 14 – козырек; 15 – втулка; 16 - топливная форсунка; 17 – топливный коллектор; 18 – полость отборов воздуха;
19 - фланец отбора воздуха; 20 – внутренняя стенка наружного корпуса; 21 – сопловой аппарат турбины
ренним 2 корпусами устанавливается одна жаровая труба 3. На Рис. 6.2.1_5 представлен разрез кольцевой камеры сгорания двигателя RB-211.
Корпуса КС вместе с направляющим аппаратом 4 компрессора входят в силовую схему двигателя. На выходе из направляющего аппарата комп-
рессора установлено кольцо диффузора наружное 5, которое вместе со стенкой внутреннего корпуса образует кольцевой диффузор.
Рабочий объем жаровой трубы представляет собой кольцевое пространство между наружной 6, внутренней 7 стенками и фронтовой плитой 8. От
291

Глава 6 - Камеры сгорания
перемещения вдоль оси двигателя жаровая труба зафиксирована подвесками 9. Стенки жаровой трубы изготовлены точением. Воздух на охлаждение стенок подается через несколько поясов отверстий 10. Кроме того, для местного охлаждения в стенках имеется перфорация 11 из мелких отверстий. Для организации горения воздух в жаровую трубу поступает во ФУ, в отверстия 12 первичной зоны и отверстия 13 зоны смешения. Для увеличения пробивной способности струй воздуха в отверстия установлены козырьки 14 и втулки 15. Топливо в КС подается через форсунки 16 с воздушным распылом. Топливо к форсункам поступает по коллекторам 17.
Рисунок 6.2.1_6 – Испарительная кольцевая КС (Печатается с разрешения RollsRoyce plc.)
1 – испарительное устройство;
2 – жаровая труба; 3 – форсунка
Наружное кольцо диффузора образует вместе с наружным корпусом полость 18, из которой че- рез фланцы 19 отбирается воздух на самолетные нужды.
Наружный корпус КС имеет двойную стенку. Внутренняя стенка 20 образует проточную часть КС и предохраняет наружную стенку от потока тепла от горячей жаровой трубы. Наружная стенка корпуса – силовая. Она воспринимает усилия от внутреннего давления и осевых сил. Между стенками корпуса проходит воздух, отбираемый из КС на охлаждение турбины.
Кроме рассмотренных основных схем существует большое количество КС, которые имеют особенности конструкции для удовлетворения требований, предъявляемых к конкретной КС. Так, по конструкции ФУ жаровых труб различают КС испарительные (см. Рис. 6.2.1_6) и многофорсуночные (см. Рис. 6.3.4.1_2). Испарительные КС отличаются от обычных только наличием специального испарительного устройства 1 (см. Рис. 6.2.1_6), в которое форсункой 2 подается топливо и небольшое количество воздуха (α = 0,25…0,3), чтобы ТВС не воспламенилась в испарительном устройстве. При попадании топлива на горячие стенки испарительного устройства топливо испаряется, перемешивается с воздухом, и подготовленная ТВС поступает в жаровую трубу 3. Такие КС не получили широкого распространения из-за проблем с коксованием топлива в испарительном устройстве и проскоком в него пламени.
Рисунок 6.2.1_7 – Противоточная индивидуальная КС (Печатается с разрешения Rolls-Royce plc.)
1 – выход из компрессора присоединительный патрубок; 2 – корпус КС; 3 - жаровая труба; 4 - фронтовое устройство; 5 – завихритель; 6 – патрубки; 7 - отверстия зоны смешения; 8 - форсунка; 9 – труба подвода продуктов сгорания к турбине
292

Глава 6 - Камеры сгорания
Рисунок 6.2.1_8 – Противоточная КС двигателя Т-55 (Иллюстраци любезно предоставлена компанией Honeywell International Inc.)
В зависимости от направления проходящего через КС потока, они делятся на прямоточные, (все рассмотренные выше) и противоточные, в которых поток меняет свое направление. На Рис. 6.2.1_7 представлена одна из ранних разработок противоточной КС фирмы Rolls-Royce. Воздух поступает из компрессора через патрубок 1 в пространство между корпусом 2 и жаровой трубой 3, затем входит через ФУ 4, завихритель 5, патрубки 6 и отверстия 7 в жаровую трубу. Топливо подается в жаровую трубу форсункой 8. Происходит сгорание топлива по обычной схеме, и горячие газы через трубу 9 поступают на вход турбины. Противоточ- ные КС из-за смены направления пока имеют повышенные потери давления и применяются в основном на двигателях имеющих ограничения по габаритам в длину. Пример противоточной КС приведен на Рис. 6.2.1_8.
К особой группе относятся двухзонные КС, созданные для обеспечения низкой эмиссии вредных веществ. Они будут рассмотрены в разделе 6.3.4.
6.2.2 – Выбор схемы КС
Выбор схемы КС зависит от назначения двигателя и от предъявляемых к нему специальных требований. Спроектированные для одного и того же двигателя трубчато-кольцевая и кольцевая КС имеют практически одинаковые характеристики, хотя каждая схема имеет свои индивидуальные достоинства и недостатки.
В трубчато-кольцевой КС имеется возможность равномерного подвода воздуха к подаваемому топливу. Это важное обстоятельство позволяет хорошо организовать процесс горения и смешения
âжаровой трубе. Благодаря этому камера имеет высокую полноту сгорания, низкую неравномерность поля температур газа на выходе, хорошие эмиссионные характеристики. Важным достоинством этой схемы является возможность испытания и доводки КС на установках с умеренными расходами воздуха.
Кольцевая КС более компактна, имеет несколько меньшие потери полного давления (хотя
âсовременных ГТД минимально допустимые по-
293

Глава 6 - Камеры сгорания
тери полного давления диктуются охлаждаемым сопловым аппаратом турбины). Жаровая труба кольцевой КС, в силу простой формы, более технологична в изготовлении. Меньшая поверхность жаровой трубы требует меньших расходов воздуха на охлаждение ее стенок. Однако сравнительно небольшая поверхность не приводит к снижению массы жаровой трубы, как можно было бы ожидать, поскольку обеспечение необходимой прочности наружной обечайки требует увеличения е¸ толщины, что соответственно увеличивает массу. Вследствие сильного влияния полей скоростей воздуха на входе в КС на поля температур газа на выходе и трудностей согласования потоков воздуха с подачей топлива в жаровую трубу, поля температур газа в кольцевой КС менее стабильны, чем в труб- чато-кольцевой. Большую трудность в стендовой доводке кольцевой КС представляет необходимость иметь установки с большим расходом воздуха. Несмотря на это в настоящее время кольцевые КС получили наибольшее распространение в авиационных ГТД.
В промышленных ГТД широкое применение находят трубчато-кольцевые КС, поскольку в данном случае одно из первых мест занимает требование по эксплуатационной технологичности (возможности замены узлов КС в эксплуатации вплоть до замены жаровых труб).
6.3 – Проектирование КС
Процесс создания КС, как и любого другого основного узла ГТД состоит из определенных этапов (см. раздел 2.5.1). В данной главе рассматриваются особенности проектирования КС, выбор ее облика, определение требований к составляющим узлам.
Облик КС выбирается, как правило, на базе имеющегося прототипа с учетом традиций и накопленного опыта предприятия, его технологи- ческой и производственной базы, сроков создания. За прототип может быть выбрана ранее спроектированная КС с известными характеристиками, наиболее близко отвечающая предъявляемым требованиям. Следует отметить, что создание КС с нужными характеристиками, надежно работающей в течение заданного ресурса, требует проведения значительного объема эксперимен- тально-доводочных работ, как на установках, так и в системе двигателя. Это также заставляет при проектировании новых КС стремиться в максимальной степени использовать опыт создания и доводки предшествующих образцов.
6.3.1– Исходные данные для проектирования КС
Âперечень исходных данных для выполнения проекта входят:
–общие требования к двигателю и его узлам (см. раздел 2.3);
- специальные требования к КС (см. раздел 6.1);
- результаты термодинамического расчета двигателя на режимах условного цикла взлетно-поса- дочных операций в соответствии со стандартом ИКАО;
- характеристики воздушного потока на входе в КС (интенсивность и масштаб турбулентности, распределение давления, температуры и вектора скорости в окружном и радиальном направлениях); - максимальное располагаемое давление
и температура топлива на входе в КС; - экстремальные соотношения «топливо/воз-
дух» на режимах приемистости и сброса газа; - требования к величине отборов воздуха из
КС: на охлаждение турбины, противообледенительную систему, систему кондиционирования воздуха и перепусков на запуске;
- требования к количеству, расположению и проходным сечениям воздушных, масляных и суфлирующих магистралей, если они проходят через КС.
6.3.2– Определение основных размеров КС
Для определения основных размеров КС выполняется проектировочный расчет, который базируется на основных положениях теории рабоче- го процесса и практическом опыте, накопленном при создании КС авиационных ГТД.
6.3.2.1 – Объем жаровой трубы
Объем жаровой трубы рассчитывается из условия обеспечения заданной полноты сгорания с помощью обобщенной зависимости полноты сгорания топлива от критерия форсирования ηà = f(ÊV). Расчет обычно выполняется для максимального режима работы ГТД.
Параметр форсирования ÊV по своему физи- ческому смыслу характеризует отношение времени химической реакции ко времени пребывания топлива в КС:
Ê |
V |
= const (G |
Ê |
/ T* |
K |
V |
Æ |
(P* |
K |
)1,25) (6.3.2-1) |
|
|
|
|
|
|
294

Глава 6 - Камеры сгорания
ãäå VÆ |
- объем жаровой трубы; |
GÊ, P*K, T*K |
- расход, давление и температура |
|
воздуха на входе в КС. |
При выборе объема жаровой трубы необходимо учесть следующее.
Во-первых - объем жаровой трубы определяет время пребывания продуктов сгорания при высоких температурах в КС, что в свою очередь влияет на выбросы вредных веществ. С целью уменьшения выбросов NOx необходимо уменьшать время пребывания продуктов сгорания при высоких температурах на взлетном режиме, т.е. уменьшать объем жаровой трубы.
Во-вторых - для обеспечения работы КС на режиме малого газа, низких выбросов СО и НС и обеспечения высотного розжига требуется увеличение объема жаровой трубы, т.к. на этих режимах резко снижается полнота сгорания и увеличи- вается критерий форсирования ÊV.
Окончательный объем жаровой трубы определяется путем нескольких последовательных рас- четов, конструкторских проработок и проведения экспериментов на модельных установках, включа- ющих имитацию высотных режимов.
6.3.2.2 – Распределение воздуха в жаровой трубе
После определения объема жаровой трубы выполняется «аэродинамическое проектирование», цель которого – обеспечить:
-безотрывность течения воздуха в преддиффузоре;
-оптимальное распределение воздуха в межтрубном пространстве или кольцевых каналах;
-заданные потери давления;
-оптимальное распределение подвода воздуха в жаровую трубу по ее длине с точки зрения организации процесса горения для обеспечения высокой полноты сгорания топлива, норм на выбросы вредных веществ и формирования требуемой радиальной эпюры температур газа на выходе.
Весь воздух, поступающий в жаровую трубу, можно условно разделить на отдельные характерные составляющие: на систему охлаждения, в ФУ,
âзону горения и в зону смешения.
Для распределения расхода воздуха между зонами жаровой трубы часто поступают следующим образом. Вначале выбирается режим сжигания топлива в расчетных условиях и определяется количество воздуха, поступающего в зону горения. Например, при общем коэффициенте избытка воздуха на выходе из КС αÊÑ = 3 при сжигании обедненной ТВС в зоне горения с αÃÎÐ = 1,5 â íå¸ íåîá-
ходимо подать 50% от общего количества воздуха, поступившего в КС. Если выбрана концепция низкотемпературного сжигания обогащенной ТВС
ñ αÃÎÐ = 1,5 в не¸ необходимо подать 50% от общего количества воздуха, поступившего в КС. Если
выбрана концепция низкотемпературного сжигания обогащенной ТВС с αÃÎÐ = 0,6, то в зону горения необходимо подать 20% воздуха, здесь:
α = GÂ / GÒL0
ãäå GÂ – расход воздуха через КС (или зону горения) (кг/с);
GÒ – расход топлива (кг/c);
L0 – стехиометрический коэффициент для воздуха и данного вида топлива (керосина).
Для используемых видов керосина (РТ, Т-6, ТС-1, Т-1) стехиометрический коэффициент для воздуха находится в диапазоне от 14,70 до 14,94.
Решение задачи по распределению воздуха между ФУ и основными отверстиями зоны горения сводится к отысканию компромиссного варианта, при котором обеспечивается максимальная однородность ТВС, надежность запуска и устой- чивость горения во всем диапазоне работы двигателя. Противоречие между этими требованиям заключается в том, что с одной стороны увеличение расхода воздуха через ФУ способствует образованию более однородной ТВС, с другой стороны - это приводит к росту скорости потока в головной части жаровой трубы, что ухудшает условия розжига
èсужает область устойчивого горения. В каждом конкретном случае распределение воздуха между ФУ и основными отверстиями выбирается либо по аналогии с ближайшим прототипом, либо на основании имеющихся литературных данных или собственного опыта предприятия и окончательно подтверждается экспериментом.
Оставшийся воздух делится между системой охлаждения и зоной смешения. В связи с тем, что воздух системы охлаждения практически не вовлекается в организацию рабочего процесса в жаровой трубе, его количество стараются ограничить. Особенно это актуально для современных ГТД с высокими термодинамическими параметрами цикла
èнизкими значениями коэффициента избытка воз-
äóõà çà ÊÑ (αÊÑ ≈ 2,2). Òàê, â ÊÑ ñ αÊÑ = 2,2, при организации процесса сжигания обедненной ТВС
ñ α= 1,8 в зоне горения объем воздуха, оставшегося на зону смешения и охлаждение стенок, будет составлять всего около 18%.
В условиях дефицита воздуха для охлаждения стенок жаровых труб требуется применять высокоэффективные системы охлаждения и теплоза-
295

Глава 6 - Камеры сгорания
щитные покрытия (см. раздел 6.4.2.2). В каждом конкретном случае величину потребного расхода охлаждающего воздуха предварительно находят из теплового расчета стенки жаровой трубы и затем уточняют по результатам термометрирования на двигателе.
На начальном этапе проектирования геометрические размеры отверстий в стенке жаровой трубы и ФУ можно определить по следующей схеме:
–определяется суммарная эффективная площадь отверстий в стенке жаровой трубы;
–распределяется суммарная эффективная площадь по зонам жаровой трубы в соответствии
ñвыбранным распределением расхода воздуха;
–определяется геометрическая площадь и фактические размеры отверстий.
Суммарная эффективная площадь отверстий (м2) в стенке жаровой трубы находим по формуле:
F Σ = |
G |
ÂÆ |
/ (2ρ∆Ð |
Æ |
)0,5 |
(6.3.2 - 3) |
ÝÔ |
|
|
|
|
ãäå GÂÆ - расход воздуха через жаровую трубу (кг/с);
ρ - плотность воздуха в межтрубном канале (кг/м3);
∆ÐÆ - перепад давления на стенке жаровой трубы (Па).
Величина перепада давления на стенке жаровой трубы на практике колеблется в достаточно узких пределах (3…5% от давления за компрессором). Это связано с тем, что при низких значениях перепада ухудшается эффективность системы охлаждения первого соплового аппарата ТВД и протекание рабочего процесса в самой жаровой трубе. При более высоких значениях необоснованно завышаются общие потери в КС. Поэтому, величи- ной перепада давления на стенке жаровой трубы можно предварительно задаться, принимая ее постоянной по всей длине жаровой трубы.
Если известны потери давления в диффузоре, то среднюю величину перепада давления на стенке жаровой трубы можно определить путем вычи- тания из общих потерь давления в КС (которые, как правило, являются заданной величиной), потерь в диффузоре.
На основании принятого допущения о постоянной величине перепада давления вдоль стенки жаровой трубы, эффективная площадь отверстий должна соответствовать ранее выбранному распределению расхода воздуха по зонам жаровой трубы. Тогда геометрическая площадь отдельных отверстий определится как отношение эффективной площади к коэффициенту расхода воздуха:
Рисунок 6.3.2_1 – Схема распространения струи в сносящем потоке
Рисунок 6.3.2_2 – Коэффициент расхода воздуха через основные отверстия
FÃÅÎÌ = FÝÔÔ / µ0 |
(6.3.2 - 4) |
Для лопаточных завихрителей коэффициент расхода воздуха бер¸тся по справочным или экспериментальным данным, а за геометрическую площадью принимается площадь самого узкого места в межлопаточном канале. Размеры отверстий системы охлаждения находятся по результатам теплового расчета жаровой трубы.
При определении размеров основных отверстий зоны горения и зоны разбавления конструктору приходится подбирать оптимальное соотношение между количеством отверстий, их размерами и формой с тем, чтобы обеспечить лучшее перемешивание воздуха с топливом или продуктами сгорания (см. Рис. 6.4.2_3). Важной характеристикой в этом выборе является глубина проникновения
296
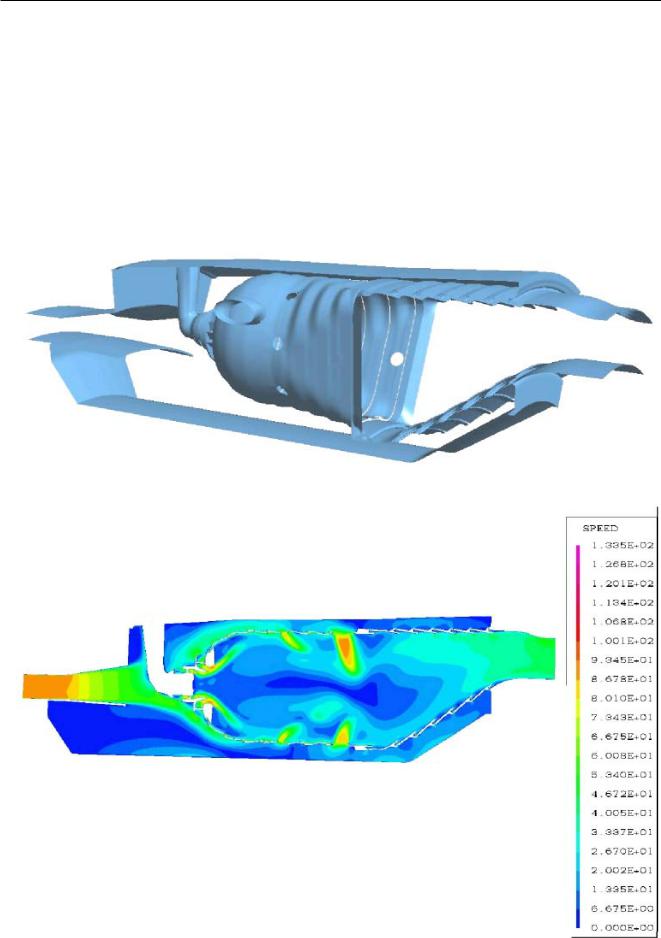
Глава 6 - Камеры сгорания
струи воздуха в поток газов. В общем случае она зависит от располагаемого перепада статического давления на стенке жаровой трубы (или скорости воздушной струи), формы отверстия, профиля кромок, толщины стенки, угла наклона оси отверстия к направлению сносящего потока, скорости воздуха в межтрубном канале и скорости газа в жаровой трубе. Для струи воздуха, втекающей через круглое отверстие перпендикулярно к сносящему потоку (см. Рис. 6.3.2_1), глубину проникновения можно определить по эмпирической формуле:
H=d0[0,3+0,415(W0/ WÆ)] (L/d0)0,63 (6.3.2 - 5)
ãäå L - длина, на которой глубина проникновения струи равна Í (ì);
W0 - скорость струи в отверстии (м/с);
WÆ - скорость потока газов в жаровой трубе (м/с).
Скорость струи воздуха в отверстии определяется через эффективную площадь отверстия по формуле:
Рисунок 6.3.2_3 – Расчетная область КС двигателя ПС-90А
Рисунок 6.3.2._4 – Поле модуля скорости в КС двигателя ПС-90А
297
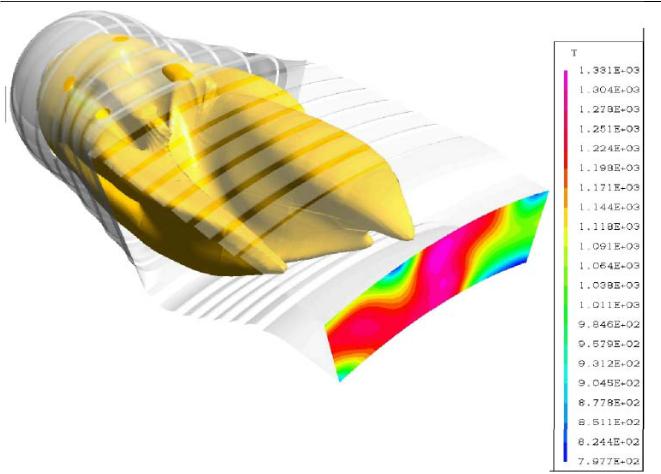
Глава 6 - Камеры сгорания
Рисунок 6.3.2_5 – Изоповерхность температуры Т=1350 К и профиль температуры на выходе КС двигателя ПС-90А
W0 = GÎÒÂ / (ρµ0 FÃÅÎÌ) (6.3.2 - 6)
Желательно, чтобы глубина проникновения струй воздуха (или отдельных струй), втекающих через основные отверстия зон горения и разбавления доходила как минимум до центра жаровой трубы, где происходит основной процесс горения и обыч- но наблюдается максимальная температура газов. Для повышения пробивной способности струй воздуха иногда используют направляющие втулки или патрубки (см. Рис. 6.4.2_3). Коэффициент расхода воздуха через основные отверстия µ0 при попутном движении воздуха и газа вдоль стенки толщиной d можно определить по графику на Рис. 6.3.2_2.
После того, как будут определены размеры отверстий жаровой трубы, производится уточненный расчет аэродинамических характеристик КС с учетом горения и расчет теплового состояния стенки жаровой трубы.
С целью повышения точности расчетов в последнее время все большее распространение стали получать специальные программные пакеты, моделирующие трехмерное течение. На Рис. 6.3.2_3
показана расчетная область КС двигателя ПС-90А. Сеточная модель этой области составляет более 1 млн. ячеек. На Рис. 6.3.2_4 и 6.3.2_5 приведены результаты расчета распределения скорости и температуры газа внутри жаровой трубы.
6.3.3 – Расчет температур элементов КС
Тепловые расчеты позволяют определить необходимый уровень температур стенки жаровой части для заданного временного и циклического ресурсов с учетом критериев эффективности и экономичности охлаждения при наиболее неблагоприятном сочетании внешних факторов (ухудшение параметров, экземплярный разброс, максимальная неравномерность температур и т.д.). Как правило, ресурсные и другие нерасчетные факторы учитываются запасом температуры ∆ÒÑÒ над предельно допустимой для выбранной марки материала стенки жаровой части:
ÒÑÒ = [ÒÑÒ] - ∆ÒÑÒ |
(6.3.3 - 1) |
298
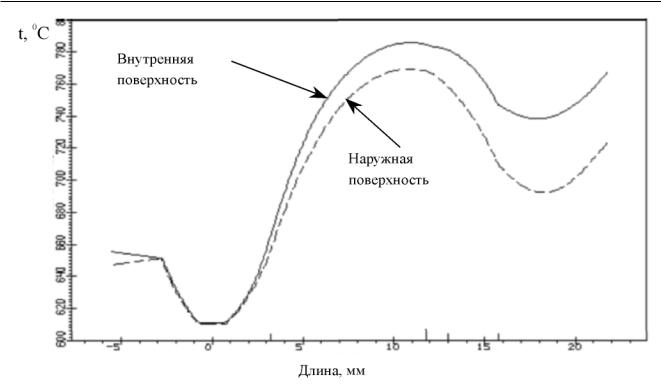
Глава 6 - Камеры сгорания
Рисунок 6.3.3_1 – Изменение температуры стенки вдоль секции системы охлаждения жаровой трубы
Из опыта эксплуатации КС величина запаса |
Кроме этого предусмотрено два способа за- |
|
температуры ∆ÒÑÒ составляет 50…150°С. |
дания величины лучистого потока - либо устанав- |
|
В общем случае задача по определению тем- |
ливается конкретное значение, либо программа |
|
пературы стенки жаровой трубы сводится к реше- |
«сама» определяет величину лучистого потока по |
|
нию уравнения баланса тепловых потоков через |
заложенным в ней результатам измерений на дви- |
|
стенку: |
|
гателе. Если конструкция жаровой трубы и расп- |
QÃÊÎÍ + QÃË = QÕÊÎÍ + QÕË = Qδ, (6.3.3 - 2) |
ределение в ней топлива существенно отличаются |
|
от применяемых на двигателе, а также при исполь- |
||
ãäå QÃÊÎÍ, QÕÊÎÍ |
|
зовании других видов топлива, то интенсивность |
- тепловые потоки от горячих |
лучистого потока целесообразно задать конкретной |
|
|
газов к стенке и от стенки к хо- |
величиной, определяемой экспертным или расчет- |
|
лодному воздуху за счет конвек- |
ным путем. На Рис. 6.3.3_1 приведено характерное |
QÃË , QÕË |
тивного теплообмена; |
распределение температуры вдоль стенки одной |
- лучистые тепловые со стороны |
секции пленочной системы охлаждения, показан- |
|
|
горячих газов и со стороны хо- |
íîé íà Ðèñ. 6.4.2.2_5à. |
Qδ |
лодного воздуха; |
Для других типов конструкций системы охлаж- |
- тепловой поток через стенку |
дения тепловой расчет выполняется по общим ме- |
|
|
за счет теплопроводности. |
тодикам расчета, изложенным в специальной лите- |
Для расчета теплового и напряженного состо- |
ратуре [6.9.6] или с помощью универсальных |
|
яний конвективно-пленочной и ударно-пленочной |
программ. Так, результаты аэродинамического рас- |
|
систем охлаждения может быть использована про- |
чета КС с учетом горения, выполненные с помощью |
|
грамма, созданная в ЦИАМ на основе результатов |
программного пакета моделирующего трехмерное |
|
аналитических и экспериментальных исследова- |
течение, могут быть использованы в качестве гра- |
|
ний, приведенных в работе [6.9.5]. Исходными дан- |
ничных условий для расчета температуры стенки жа- |
|
ными для расчета являются геометрические пара- |
ровой трубы. На Рис. 6.3.3_2 и 6.3.3_3 приведено |
|
метры, марка материала секции охлаждения, |
расчетное температурное поле, воздействующее на |
|
температура и давление охлаждающего воздуха |
стенку и распределение температуры вдоль стенки. |
|
и продуктов сгорания, коэффициент избытка воз- |
Другой важной задачей при проектировании |
|
духа и скорости потоков в районе секции. |
КС является определение теплового состояния ее |
299

Глава 6 - Камеры сгорания
Рисунок 6.3.3_2 – Температурное поле, воздействующее на стенку жаровой трубы
Рисунок 6.3.3_3 – Температура стенки жаровой трубы
300
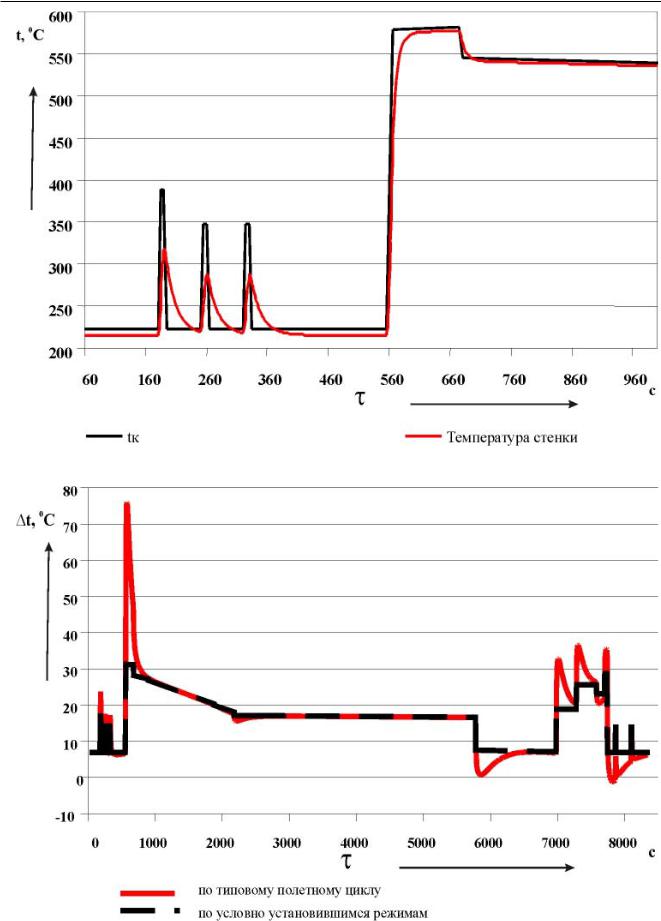
Глава 6 - Камеры сгорания
Рисунок 6.3.3_4 – Изменение максимальной температуры стенки корпуса по типовому полетному циклу
Рисунок 6.3.3_5 - Изменение перепада температур на фланце под свечу зажигания корпуса КС по полетному циклу
301
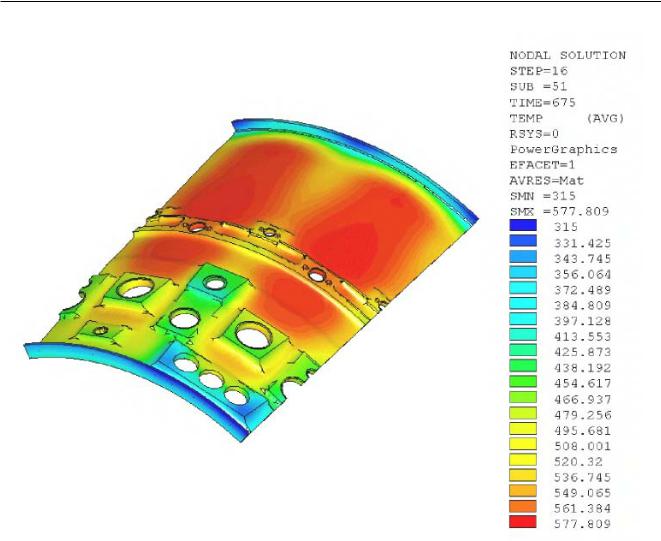
Глава 6 - Камеры сгорания
Рисунок 6.3.3_6 – Температура на наружной поверхности корпуса КС двигателя ПС-90А на взлетном режиме
наружного корпуса, который относится к основным силовым элементам двигателя.
Результаты тепловой оценки используются при расчете НДС, оценке запасов прочности и прогнозировании ресурса корпуса по циклической долговечности. В связи с тем, что температура корпуса является инерционным параметром, для повышения качества прочностного расчета необходимо оценивать тепловое состояние корпуса с учетом нестационарности режима работы двигателя по полетному циклу.
На графиках на Рис. 6.3.3_4 и 6.3.3_5 виден инерционный характер изменения максимальной температуры корпуса по полетному циклу и отличие в перепаде температур между внутренней и наружной поверхностями (в районе фланца свечи зажигания) в стационарных и нестационарных условиях. Общая картина распределения температуры в расчетной области корпуса КС приведена на Рис. 6.3.3_6.
6.3.4 – Проектирование на заданную эмиссию
Âсвязи с большим вниманием, уделяемым
âпоследнее время проблеме экологической чистоты авиационных и наземных ГТД, одним из главных критериев, на который необходимо ориентироваться при проектировании КС, является требование по обеспечению заданных норм на эмиссию вредных веществ. В соответствии с международным стандартами и отечественными правилами в настоящее время для авиационных ГТД нормируется эмиссия HC, СО, NОx и дыма. Нормируемым параметром эмиссии газообразных вредных веществ является условный валовый выброс каждого вещества, отнесенный к тяге двигателя на взлетном режиме (г/кН):
DNOx,CO,HC = MNOx,CO,HC / R00, (6.3.4 - 1)
302

Глава 6 - Камеры сгорания
Эмиссия дыма нормируется по максимальному измеренному значению условного числа дымности SN.
Валовый выброс каждого из вредных веществ определяется как сумма выбросов на режимах стандартного условного цикла взлетно-посадочных операций:
Ì = ΣEI GÒτ |
(6.3.4 - 2) |
ãäå EI - индекс эмиссии (Emission Index) - масса вредного вещества, приходящаяся на 1 кг топлива (г/кг);
GÒ - расход топлива (кг/мин);
τ - время работы на i-ом режиме (мин). Стандартный условный цикл взлетно-поса-
дочных операций включает в себя следующие режимы:
-взлет - 100 % расчетной мощности, время работы на режиме 0,7 мин.;
-набор высоты - 85 % расчетной мощности, время работы 2,2 мин.;
-заход на посадку -30 % расчетной мощности, время работы 4,0 мин.;
-руление, малый газ – 7 % расчетной мощности, время работы 26 мин.
Первые нормы на эмиссию вредных веществ, согласно стандарту ИКАО, распространялись на авиационные ГТД с датой создания после 31 декабря 1985 г. и имели следующие величины:
DCO |
= 118 ã/êÍ; |
|
|
|
DHC |
= 19,6 ã/êÍ; |
|
||
DNÎx |
= 40+2πÊ ã/êÍ; |
(6.3.4 - 3) |
||
SN |
= 83,6 (R |
00 |
)-0,274, но не более 50 |
|
|
|
|
(6.3.4 - 4) |
|
|
|
|
|
ãäå πÊ – степень повышения давления в двигателе; R00 – тяга на взлетном режиме.
После этого нормы на эмиссию СО, НС и SN не менялись, а норма на эмиссию NОx дважды пересматривалась в сторону ужесточения. Сначала она была снижена на 20 % для двигателей с датой создания после 31.12. 1995г., а затем примерно еще на 16 % (зависит от πÊ è R00) для двигателей с датой создания после 31.12.2003г. Точные значения норм 2004 года на эмиссию NОx определяются по формулам:
DNÎx = 19+1,6πÊ |
(6.3.4 - 5) |
ïðè πÊ ≤ 30 è R00 > 89 êÍ (9075 êãñ); |
|
DNÎx = 37,572 +1,6πÊ - 0,2087R00 |
(6.3.4 - 6) |
ïðè πÊ ≤ 30 è 26,7< R00 ≤ 89 êÍ (9075 êãñ);
DNÎx = 7+2πÊ |
(6.3.4 - 7) |
ïðè 30< πÊ ≤ 62,5 è R00 > 89 êÍ (9075 êãñ);
DNÎx = 42,71+1,4286πÊ - 0,4013R00 (6.3.4 - 8)
ïðè 30< πÊ < 62,5 è 26,7< R00 ≤ 89 (9075 êãñ);
DNÎx = 32+1,6πÊ |
(6.3.4 - 9) |
ïðè πÊ ≥ 30.
Графическая интерпретация изменения норм ИКАО на эмиссию NОx приведена на Рис. 6.3.4_1.
Следующим шагом в плане ужесточения норм на эмиссию вредных веществ является планируемое введение в 2008 году поправки к стандарту ИКАО, согласно которой будут ужесточены нормы на эмиссию NОx примерно на 12% [6.9.7]. Кроме того, некоторые страны Евросоюза, например Швеция, Норвегия, Финляндия и Франция, взимают штрафы за превышение эмиссии вредных веществ над нормами ИКАО 2004 года.
Для того, чтобы иметь более четкое представление о возможных путях снижения эмиссии вредных веществ, рассмотрим механизмы их образования.
Окись углерода в большом количестве может образовываться вследствие нехватки кислорода для завершения реакции окисления углерода до СО2 (забогащенная топливовоздушная смесь в первичной зоне), либо вследствие диссоциации СО2 при высокой температуре (стехиометрическая или умеренно забедненная топливовоздушная смесь).
Значительную добавку к термодинамически равновесному СО дает неполное сгорание топлива. Именно этим можно объяснить тот факт, что максимальные концентрации СО образуются на режимах малой тяги, где температура газа в зоне горения относительно невелика. Таким образом, основными причинами высокого содержания СО
âвыхлопных газах могут быть:
-низкая скорость горения в первичной зоне вследствие недостатка топлива и (или) нехватки времени пребывания;
-недостаточно однородная топливовоздушная смесь, в результате чего образуются локальные забедненные зоны с низкой полнотой сгорания, а также зоны с большим избытком топлива;
-«замораживание» продуктов горения воздухом, участвующим в охлаждении стенки жаровой трубы.
303

Глава 6 - Камеры сгорания
Повышенное содержание несгоревших углеводородов, к которым относят топливо в виде капель или пара, а также продукты разложения исходного топлива на углеводороды меньшей молекулярной массы (метан, ацетилен), обычно связывают с плохим распыливанием топлива, недостаточной скоростью горения и «замораживанием» продуктов неполного сгорания в охлаждающем воздухе вблизи стенок жаровой трубы. С увеличе- нием режима работы двигателя выбросы несгоревших углеводородов уменьшаются. Связано это как с улучшением распыливания топлива, так и с ростом скорости химических реакций в первичной зоне вследствие повышения давления и температуры воздуха на входе в КС.
Устранение причин образования СО и НС сводится, как правило, к повышению полноты сгорания топлива на режимах вблизи малого газа. Связь между полнотой сгорания и уровнями выбросов СО и НС описывается следующим аналитическим выражением:
1-η |
à |
=(EI |
HC |
+ 0,232EI |
CO |
)10-3 |
(6.3.4 - 10) |
|
|
|
|
|
|
|
|||
ãäå ηà |
|
|
- коэффициент полноты сгорания |
|||||
EIHC , EICO |
топлива; |
|
|
|
||||
- удельные выбросы СО и НС |
||||||||
|
|
|
(г/кг топлива). |
|
|
NOx образуются в результате окисления азота, находящегося в атмосферном воздухе и в топливе. Легкие дистиллятные топлива содержат небольшие количества органического азота (менее 0,06 %), в то время как тяжелые продукты перегонки могут содержать до 1,8 %. В последнем случае
доля NO из топлива может составлять значи- тельную долю в общем выбросе окиси азота.
Основную часть в окислах азота обычно составляет окись азота NO. Образование NO происходит в соответствии с цепным механизмом Зель-
довича [6.9.8]: |
|
|
Î2 |
' 2Î, |
|
Î + N2 |
' NO + N, |
(6.3.4 - 11) |
N + O2 |
' NO + O. |
|
Процесс образования окиси азота эндотерми- чен и идет с заметной скоростью только при температурах выше 1800 К, поэтому NO образуется только в горячих зонах и достигает максимальной концентрации на режиме наибольшей тяги. Окисление NO до NO2 происходит при снижении температуры газа. Практический диапазон температуры газа, при которой образуется двуокись азота - от 400 до 900 К. На режимах большой тяги доля
Рисунок 6.3.4_1 – Нормы ИКАО на эмиссию NOx
NO2 в окислах азота NOx (NOx = NO+NO2) очень мала, но на режиме малого газа она может достигать 50 %.
Установлено, что выброс NOx экспоненциально возрастает с повышением температуры пламени согласно соотношению NOx ∞ exp(0,009ÒÏË) и линейно возрастает с повышением времени пребывания продуктов сгорания в высокотемпературных зонах. Изменение давления от 0,5 до 3 МПа практически не влияет на уровень выброса NOx.
Сажа (или дым) может образовываться в любой части зоны горения, где имеется избыток топлива и скорость смешения недостаточна. Например, в случае центробежных форсунок основная сажеобразующая область располагается внутри факела распыливания. В этой области существует возвратное течение продуктов сгорания и локальные порции паров топлива оказываются окруженными высокотемпературными газами с дефицитом кислорода. Большая часть сажи, образовавшейся в первичной зоне горения, сгорает затем в высокотемпературных областях ниже по потоку. Экспериментально установлено, что на образование сажи оказывают влияние свойства топлива, давление и температура воздуха в КС, коэффициент избытка воздуха, качество распыливания топлива и способ подачи топлива в КС. Так, склонность к сажеобразованию возрастает при уменьшении содержания в топливе водорода, а также при повышении концентрации в топливе полициклических аромати- ческих углеводородов.
С увеличением давления в КС сажеобразование существенно возрастает. Связано это с тем, что расширяются пределы горения и сажа начинает образовываться в тех областях, где при низких давлениях эти области были бы слишком забогащен-
304
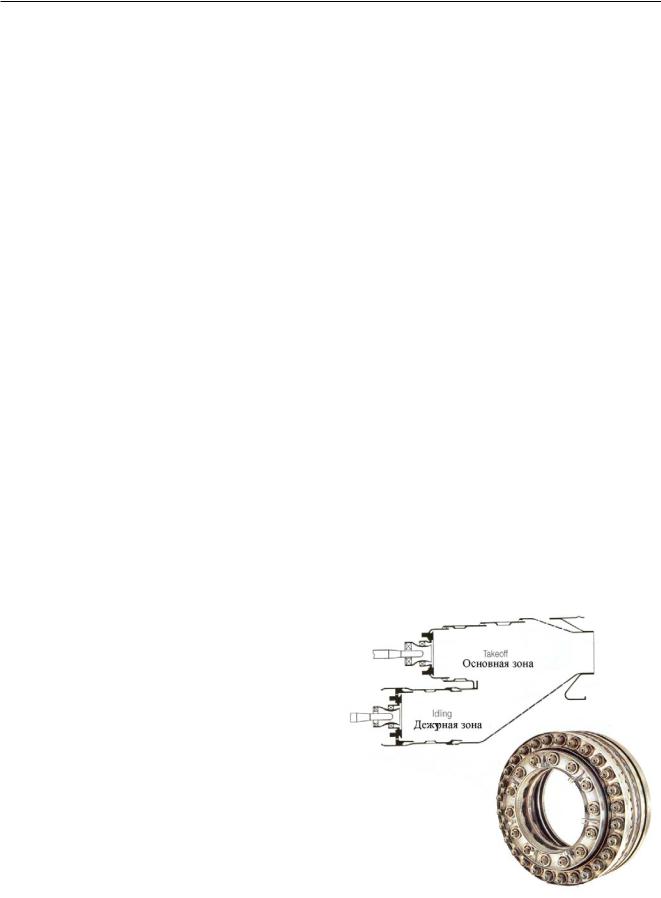
Глава 6 - Камеры сгорания
ными для горения. Кроме этого, повышенное давление ускоряет химические реакции и тем самым приводит к более раннему инициированию горения и к увеличению доли топлива, сгорающего в переобогащенных областях.
Увеличение температуры воздуха на входе в КС чаще всего приводит к усилению сажеобразования, особенно при наличии забогащенных зон. Повышение температуры газа на выходе из камеры уменьшает сажеобразование благодаря увели- чению области выгорания сажи в зоне смешения.
6.3.4.1 – Способы снижения эмиссии вредных веществ
Для обеспечения минимального уровня эмиссии вредных веществ при организации процесса горения в КС любого типа необходимо обеспечить следующие условия:
- достаточно мелкое дробление частиц топ-
ëèâà;
- высокую однородность смеси перед подачей
âÊÑ;
-максимально возможную скорость реакции;
-температуры в зоне горения 700…1500 °С;
-отсутствие локальных высокотемпературных
çîí;
-постоянного во всем диапазоне работы двигателя состава смеси (α = const) в зоне горения;
-оптимальное распределение вторичного воз-
äóõà;
-оптимальный состав смеси в смесительных устройствах или в первичной зоне КС.
Большинство способов снижения вредных выбросов в КС традиционных схем по существу являются компромиссом между выбросом СО и НС с одной стороны и выбросом NOx – с другой. В то же время, для обеспечения перспективных норм на эмиссию вредных веществ, необходимо создание КС, которые бы позволили одновременно снизить все виды вредных компонентов. К основным конструктивным схемам низкоэмиссионных КС можно отнести следующие схемы:
-двухзонные;
-изменяемой геометрии;
-многофорсуночные;
-с гомогенизацией топливовоздушной смеси;
-каталитические.
Принцип действия всех низкоэмиссионных КС так или иначе основан на поддержании температуры в зоне (зонах) горения в достаточно узком интервале на всех эксплуатационных режимах двигателя.
Пример двухзонной КС с параллельным расположением зон показан на Рис. 6.3.4.1_1. Дежур-
ная зона этой КС (внутренняя зона) оптимизирована в отношении высокой полноты сгорания и низких выбросов СО и НС на режимах близких к малому газу, тогда как основная зона создает бедную смесь, оптимальную в отношении выброса NOx на режимах большой мощности. Дежурная зона обеспечивает также устойчивость горения основной зоны при ее подключении. К недостаткам двухзонной КС можно отнести сложность обеспечения ее надежной работы на переменных режимах работы двигателя, когда требуется быстрое отключение или подключение основной зоны.
В конструкции КС изменяемой геометрии постоянство коэффициента избытка воздуха в первич- ной зоне обеспечивается применением элементов, позволяющих регулировать распределение воздуха в жаровой трубе. На режимах максимальной тяги значительная часть воздуха подается в первичную зону для того, чтобы минимизировать образование сажи и NOx. При снижении тяги двигателя все увеличивающаяся доля воздуха направляется в зону разбавления, тем самым удерживается высокая температура в первичной зоне и обеспечивается низкий уровень выбросов СО и НС. КС с изменяемой геометрией, ввиду сложности конструкции, не нашли широкого распространения.
Снижение эмиссии вредных веществ в многофорсуночных КС достигается за счет уменьшения размеров локальных зон с высокой температурой горения. Пример многофорсуночной КС, приведен на Рис. 6.3.4.1_2. В этой КС форсуноч- ные модули 1 расположены в два ряда – по 36 модулей в каждом ряду. Для компенсации тепловых
Рисунок 6.3.4.1_1 – Двухзонная КС фирмы SNECMA [6.9.9]
305
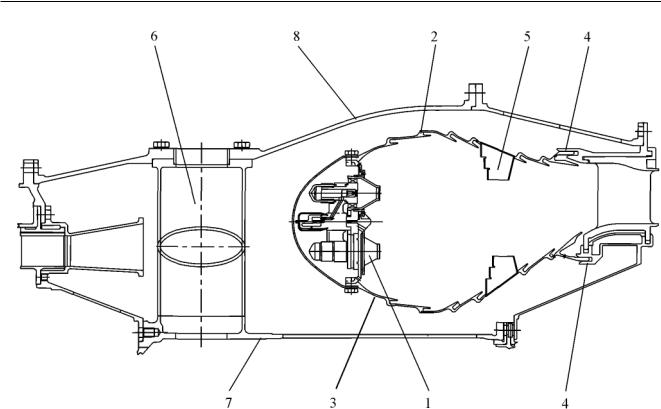
Глава 6 - Камеры сгорания
Рисунок 6.3.4.1_2 – Многофорсуночная КС [6.9.10, 6.9.11] 1 - форсуночный модуль (72 шт.); 2 - наружная стенка жаровой трубы; 3 - внутренняя
стенка жаровой трубы; 4 - телескопическое соединение жаровой трубы с первым сопловым аппаратом турбины; 5 - патрубки для подвода воздуха в зону разбавления; 6 - силовая стойка; 7 - корпус внутренний КС; 8 - корпус наружный КС
расширений наружная 2 и внутренняя 3 стенки жаровой трубы имеют телескопическое соединение 4 с первым сопловым аппаратом. Высокая однородность поля температур газа перед турбиной обеспечивается благодаря применению смесительных патрубков 5 в зоне разбавления. Усилия от расположенной под КС опоры ротора ВД передаются на наружную подвеску двигателя с помощью пустотелых силовых стоек 6, связывающих внутренний 7 и наружный 8 корпусы КС.
В КС с гомогенизацией рабочей смеси в первичную зону подается топливо, предварительно испаренное и полностью перемешанное с воздухом. При этом существенно сокращается время, необходимое для полного сгорания топлива. Низкую температуру пламени поддерживают за счет забеднения топливовоздушной смеси. В то же время на режимах малой мощности смесь может оказаться слишком забедненной для устойчивого горения. Поэтому данный подход, как правило, требует организации дежурного пламени и (или) регулирования распределения воздуха. Другим не-
достатком такой КС является вероятность самовоспламенения топлива в устройствах подготовки смеси или проскок пламени на режимах с высокими параметрами воздуха на входе в КС. Тем не менее, ввиду больших потенциальных возможностей по снижению эмиссии NОx такие КС находят все большее применение как в авиационных, так и промышленных ГТД.
Другим способом снижения температуры пламени при сжигании гомогенной топливовоздушной смеси является ее забогащение. При этом практи- чески исключается проскок пламени в устройство подготовки смеси. К недостаткам этого способа можно отнести то, что он, во-первых, требует организации в зоне разбавления быстрого перевода продуктов сгорания с избытком топлива в забедненную смесь, что на практике реализовать довольно сложно. Во-вторых, забогащенная первичная зона склонна к нагарообразованию.
В каталитических КС для повышения скорости горения и снижения температуры продуктов сгорания используются катализаторы. Схема ката-
306
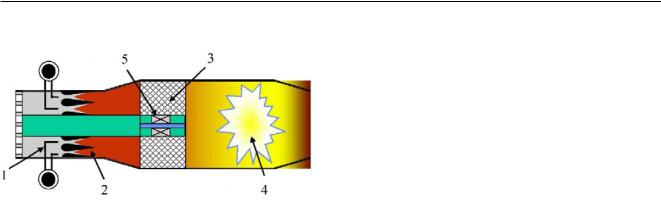
Глава 6 - Камеры сгорания
Рисунок 6.3.4.1_3 – Схема каталитической КС [6.9.12] 1 – топливная форсунка;
2 – зона предварительного смешения; 3 – катализатор; 4 - зона горения за катализато-
ром; 5 – впрыск топлива минуя катализатор
литической КС приведена на Рис. 6.3.4.1_3. Здесь одна часть топлива поступает через форсунки 1 и предварительно смешивается с воздухом в зоне 2. Подготовленная однородная топливовоздушная смесь с заданным соотношением топлива к воздуху проходит через катализатор 3. Проходя через катализатор, топливовоздушная смесь конвертируется в синтез-газ, который имеет повышенную температуру и включает в себя такие горючие компоненты как Н2 и СО. Синтез-газ догорает в зоне горения 4 за катализатором вместе с другой частью топлива 5, подаваемой в эту зону, минуя катализатор.
В присутствии катализатора реакция окисления топлива является специфическим квантохими- ческим процессом получения тепла в виде излуче- ния инфракрасных квантов. Реакция протекает через несколько последовательных стадий по более выгодному пути, что позволяет проводить процесс с большей скоростью. Важнейшим фактором каталитической технологии беспламенного сжигания топлива является то, что она позволяет проводить реакцию без вовлечения в реакцию нейтрального N2. Эффект обосновывается наличием в процессе каталитических реакций магнитно-газо- селективной адсорбции О2 и выталкиванием N2 из зоны реакции. Область применения каталитических реакторов в настоящее время ограничена по причине сложности создания катализаторов с большой мощностью тепловыделения и работающих при высоких термических нагрузках.
6.4 – Основные конструктивные элементы КС
КС состоит из следующих основных конструктивных и функциональных элементов: диффузора, жаровых труб, форсунок, корпусов, системы зажигания. Несмотря на общность функций, существует большое разнообразие конструктивных исполнений КС и составляющих элементов. Каждое техническое решение имеет объективные обоснования. Немаловажное значение имеют традиции и опыт фирм–разработчиков.
Конструкцию КС разрабатывают на основе выбранной схемы и исходных данных. К исходным данным относятся:
-данные, определенные проектировочным расчетом КС:
-параметры диффузора;
-размеры жаровой трубы и воздушных каналов;
-количество форсунок;
-расположение основных отверстий для подвода воздуха в жаровую трубу;
-распределение воздуха по жаровой трубе;
-присоединительные размеры проточной ча- сти и корпусов компрессора и турбины;
-силовая схема двигателя (расположение подшипниковых опор);
-схема вторичных потоков двигателя (прохождение через КС трубопроводов, обеспечивающих работу опор двигателя, системы охлаждения и др.);
-требования к креплению двигательных агрегатов и узлов на корпусе КС.
Ниже рассмотрены некоторые конструктивные решения и расчеты основных и элементов КС ГТД.
6.4.1 – Диффузор
Диффузор представляет собой расширяющийся канал, в котором скорость потока снижается
èчасть кинетической энергии преобразуется в потенциальную, что выражается приростом статического давления.
Диффузоры должны удовлетворять следующим требованиям:
-иметь минимальные гидравлические потери;
-иметь минимальную длину;
-обеспечивать устойчивое поле скоростей
èдавлений перед входом в жаровую трубу (т.е. отсутствие отрыва потока).
В трубчатых КС диффузоры выполняются в виде индивидуальных для каждой жаровой трубы патрубков (см. Рис. 6.2.1_2) с изоградиентным увели- чением площади проходного сечения.
307

Глава 6 - Камеры сгорания
à) |
á) |
â) |
Рисунок 6.4.1_1 – Диффузоры КС |
|
|
а) с изоградиентным изменением площади; б) с разделителем потока; в) двухканальный |
||
с фиксированным отрывом потока. |
|
|
1 – диффузор; 2 – корпус наружный; 3 – корпус внутренний; 4 – жаровая труба; 5 – обте- |
||
катель; 6 – разделитель потока |
|
|
В трубчато-кольцевых и кольцевых КС ранее |
имеет два характерных участка (см. Рис. 6.4.1_3): |
применялись диффузоры 1 в виде профилирован- |
относительно короткий участок с плавным расши- |
ных кольцевых каналов, образованных наружным |
рением проточной части – преддиффузор 1 (учас- |
2 и внутренним 3 корпусами КС, также с изогра- |
ток с безотрывным течением) и участок с внезапным |
диентным изменением площади (см. Рис. 6.4.1_1а). |
расширением 2 (участок со стабилизированным |
Такие диффузоры обеспечивают наименьшие поте- |
отрывом потока). К преимуществам ступенчатого |
ри полного давления, наиболее равномерное поле |
диффузора по сравнению с обычным плавным |
скоростей на выходе, но имеют достаточно большую |
диффузором можно отнести его небольшую дли- |
длину. Еще одним недостатком таких диффузоров |
ну и слабую чувствительность к изменению струк- |
является то, что они не могут работать без отрыва |
туры потока на входе. При этом, однако, он имеет |
потока на всех режимах работы двигателя. Причем |
несколько повышенные потери. Разновидностью |
на разных режимах отрыв происходит в разных се- |
таких диффузоров являются диффузоры с фикси- |
чениях по длине диффузора, что неблагоприятно |
рованным отрывом, в которых для уменьшения ве- |
сказывается на режимах горения в жаровой трубе. |
личины вихревых течений размер ступени ограни- |
Для обеспечения требуемых расходов воздуха в ка- |
чивается (см. Рис. 6.4.1_1в). |
налах кольцевых КС и одинакового перепада дав- |
В некоторых случаях для улучшения аэродина- |
ления на наружной и внутренней стенках жаровой |
мических характеристик диффузоров, имеющих от- |
трубы перед входом в жаровую трубу 4 в диффу- |
рыв потока, используют управляемую систему отсо- |
зорах кольцевых КС устанавливают обтекатели 5, |
са воздуха или сдув пограничного слоя. Однако такие |
которые разделяют поток по наружному и внутрен- |
диффузоры не имеют широкого применения. |
нему кольцевым каналам (см. Рис. 6.4.1_1á), èëè |
В зависимости от расположения подшипни- |
выполняют двухканальные диффузоры с раздели- |
ковых опор на двигателе через КС могут прохо- |
телем 6 потока (см. Рис. 6.4.1_1в). В трубчато- |
дить полые стойки (см. Рис. 6.4.1_2). Через стойки |
кольцевых КС потребность в разделителях пото- |
прокладываются воздушные и масляные трубопро- |
ка отсутствует, так как воздух после диффузора |
воды к опорам. В кольцевых КС с целью сокраще- |
попадает в общую полость, образованную наруж- |
ния длины диффузора стойки располагают в сече- |
ным 2 и внутренним 3 корпусами КС, и растека- |
нии начального (профилированного) участка. |
ется между отдельными жаровыми трубами (см. |
Размещение стоек и других загромождающих эле- |
Ðèñ. 6.4.1_1à). |
ментов в диффузоре приводит к повышению по- |
В современных конструкциях КС все большее |
терь давления и дополнительной неравномернос- |
предпочтение стали отдавать ступенчатым диффу- |
ти полей скоростей и давлений перед жаровыми |
зорам (см. Рис. 6.4.1_2 и 6.4.1_3). Такой диффузор |
трубами, что может привести к повышенной нерав- |
308

Глава 6 - Камеры сгорания
Рисунок 6.4.1_2 – Пример диффузора со стойками в проточной части 1 - полая стойка; 2 – наружное кольцо диффузора; 3 – внутреннее кольцо диффузора
номерности поля температур газа на выходе из КС. При профилировании стоек необходимо учитывать возможную крутку потока за спрямляющим аппаратом компрессора. В трубчато-кольцевых КС для снижения потерь в диффузоре стойки (перепускные трубы) могут быть расположены за плавной частью диффузора между жаровыми трубами (см. Рис. 6.2.1_4).
При конструировании диффузоров следует обратить внимание на точность соблюдения размеров его проточной части (для обеспечения тече- ния без отрыва потока), а также задавать низкую шероховатость поверхности элементов проточной части, с целью снижения потерь. Пример задания шероховатости поверхности и точности размеров приведен на см. Рис. 6.4.1_2.
- относительная длина преддиффузора - отношение длины преддиффузора к высоте канала на входе:
; (6.4.1 - 1)
- степень расширения преддиффузора - отношение площади на выходе к площади на входе:
n =F |
2 |
/ F ; |
(6.4.1 - 2) |
Ä |
1 |
|
- угол раскрытия преддиффузора - связан с относительной длиной и степенью расширения соотношением:
; (6.4.1 - 3)
6.4.1.1 – Расчет диффузора
Кратко рассмотрим главные расчетные параметры наиболее часто встречающегося в современных конструкциях КС ступенчатого диффузора (см. Рис. 6.4.1_3).
Основными геометрическими параметрами диффузора, на которые следует обращать внимание при его проектировании, являются:
- расстояние между преддиффузором и головной частью жаровой трубы L1.
При проектировании диффузора необходимо стремиться к получению безотрывного течения в плавной его части и минимальных потерь давления. На Рис. 6.4.1_4 показаны граничные условия, при которых начинается отрыв потока от стенок
309

Глава 6 - Камеры сгорания
Рисунок 6.4.1_3 – Основные геометрические параметры диффузора 1 – преддиффузор; 2 – участок с в-
незапным расширением
различных типов диффузоров. Здесь же приведена граница рекомендуемых соотношений между nÄ è для обеспечения безотрывного течения.
Участок стабилизированного отрыва потока так же играет большую роль в организации процессов в КС. Назначение этого участка сводится к созданию стабильных (по режимам двигателя) условий для обтекания жаровой трубы с минимальными потерями давления, отсутствием автоколебаний и равномерной скоростью вдоль стенок жаровой трубы. Последнее условие необходимо для обеспечения нормальной работы системы охлаждения и оптимального втекания воздуха в жаровую трубу.
Эффективность работы диффузора чаще всего оценивают по величине коэффициента восстановления полного давления σÄ, который определяется по формуле:
σÄ = ∆P*P / π*Ê = (P*Ê - P*ÊÀÍ) / π*Ê (6.4.1 - 4)
ãäå P*Ê |
- полное давление на входе в диффузор |
P*ÊÀÍ |
(на выходе из компрессора); |
- полное давление в межтрубном канале |
|
|
КС (среднее давление между наруж- |
|
ным и внутренним каналами при |
|
кольцевой КС). |
На Рис. 6.4.1_5 показана зависимость σÄ от расстояний между диффузором и головной частью жаровой трубы L1, диффузором и основными отверстиями зоны горения L, от высоты канала h2 и диаметра головной части жаровой трубы DÆ (обозначения см. Рис. 6.4.1_3). Из рисунка следует, что уменьшение этого расстояния приводит к росту потерь давления.
Рисунок 6.4.1_4 - Границы начала отрывв потока для различных типов дифузоров
Рисунок 6.4.1_5 – Зависимость потерь давления в диффузоре от расстояния до жаровой трубы и основных отверстий зоны горения
310
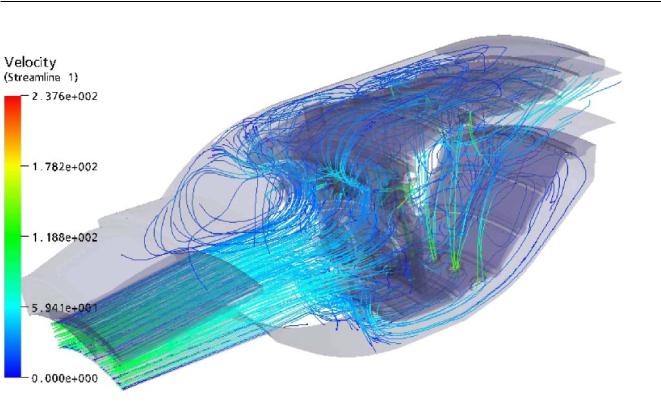
Глава 6 - Камеры сгорания
Рисунок 6.4.1_6 – Линии тока в диффузоре и КС
В современных КС коэффициент восстановления полного давления в диффузоре составляет 0,980…0,985.
Более подробно аэродинамические характеристики диффузоров исследуются с помощью программных пакетов в трехмерной постановке (см. Рис. 6.4.1_6) и при продувке моделей диффузоров на установках.
6.4.2 – Жаровая труба
После выбора схемы КС при выполнении проектировочных расчетов определяются основные параметры жаровой трубы, которые служат исходными данными для разработки е¸ конструкции. К ним относятся:
–объем жаровой трубы (см. раздел 6.3.2);
–распределение воздуха по длине жаровой трубы (площади проходных сечений фронтового устройства, количество и размеры отверстий зоны горения и смешения, количество поясов охлаждения и количество отверстий по поясам) (см. разделы 6.3.2 и 6.3.3);
–количество форсунок и фронтовых устройств;
–тип фронтового устройства; - тип системы охлаждения.
Жаровая труба в трубчатых и трубчато-коль- цевых КС как правило состоит из двух частей - собственно жаровой трубы и газосборника (см. Рис. 6.2.1_2, 6.2.1_3 и 6.2.1_4).
Пример конструкции жаровой трубы двигателя ПС-90А приведен на Рис. 6.4.2_1. В передней части жаровой трубы расположено ФУ 1. Далее по длине жаровой трубы располагается обтекаемая головка 2, за ней стенка, состоящая из секций 3 и гофрированных колец 4, сваренных между собой точечной сваркой. В конструкции жаровой трубы применена пленочная система охлаждения (см. Рис. 6.4.2.2_4). На поверхности жаровой трубы выполняют отверстия 5 для подвода воздуха в зону горения и 6 - в зону смешения. От осевых перемещений жаровая труба фиксируется за корпус КС с помощью кронштейна 7. Кронштейн расположен в передней части рядом с ФУ и форсункой, чтобы уменьшить влияние тепловых перемещений жаровой трубы относительно форсунки для обеспече- ния стабильных параметров распыла и перемешивания топлива с воздухом во ФУ. Для переброса пламени из одной жаровой трубы в другую в момент розжига трубы соединены между собой пламеперебрасывающими патрубками 8 и муфтами 17 (см. Рис. 6.2.1_4).
311
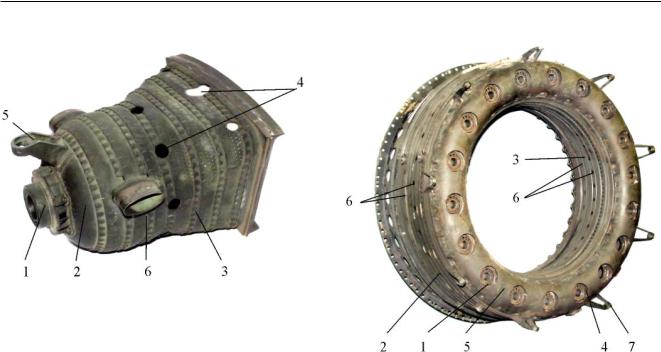
Глава 6 - Камеры сгорания
Рисунок 6.4.2_1 – Жаровая труба двигателя ПС-90А 1 - фронтовое устройство; 2 - обтекаемая головка; 3 - система охлаждения; 4 - отверстия подвода воздуха в зону горения и смешения; 5 - кронштейн; 6 - пламеперебрасывающий патрубок
Газосборники в трубчатых КС выполняют для каждой жаровой трубы отдельно, а в трубчато-коль- цевых КС они могут быть как отдельными (см. Рис. 6.2.1_3), так и кольцевыми, в которые вставляются все жаровые трубы двигателя по кольцу. Для компенсации температурных расширений жаровые трубы соединяются с газосборником с помощью телескопического соединения. Задним фланцем газосборники обычно крепятся за корпус первого соплового аппарата турбины. Стенки газосборника оснащают системой охлаждения. На Рис. 6.2.1_4 приведен пример конструкции кольцевых газосборников двигателя ПС-90А, где наружное и внутреннее кольца газосборника - точе- ные. В них выполнено по семь поясов подвода охлаждающего воздуха. Шесть поясов используются для охлаждения самих колец, а седьмой пояс
– для охлаждения наружной и внутренней полок соплового аппарата ТВД. Задняя часть кольца газосборника наружного является корпусом соплового аппарата ТВД.
Пример жаровой трубы кольцевой КС приведен на Рис. 6.4.2_2. Жаровая труба состоит из фронтового устройства 1, наружной 2 и внутренней 3 кольцевых стенок, фронтовой плиты 4. Для снижения гидравлического сопротивления и необходимого распределения воздуха по кольцевым каналам
Рисунок 6.4.2_2 – Жаровая труба кольцевой КС двигателя ПС-90А 1 - фронтовое устройство; 2 - на-
ружная кольцевая стенка; 3 - внутренняя кольцевая стенка;
4 - фронтовая плита; 5 - обтекатель; 6 - отверстия подвода воздуха в зону горения и смешения; 7 - кронштейн
в передней части жаровой трубы, расположен обтекатель 5. На стенках выполнена система охлаждения по типу, представленному на Рис. 6.4.2.2_5а.
На наружной и внутренней стенках выполнены отверстия 6 для подвода воздуха в зоны горения и смешения. От осевых и радиальных перемещений жаровая труба закрепляется за корпус КС с помощью нескольких кронштейнов 7. Соединение с корпусом первого соплового аппарата выполняется телескопическим для компенсации тепловых расширений (см. Рис. 6.3.4.1_2).
Отверстия для подвода воздуха в зоны горения и смешения могут быть круглой или овальной формы 1, с отбортовками 2 или с патрубками 3 (см. Рис. 6.4.2_3). Форма отверстий, их размеры и количество должны выбираться из условий минимальных потерь при втекании воздуха в жаровую трубу, обеспечения стабильного расхода воздуха, достаточной глубины проникновения в газовоздушный поток и интенсивного перемешивания вводимого воздуха с газовоздушным потоком на минимальной длине жаровой трубы. Механически
312
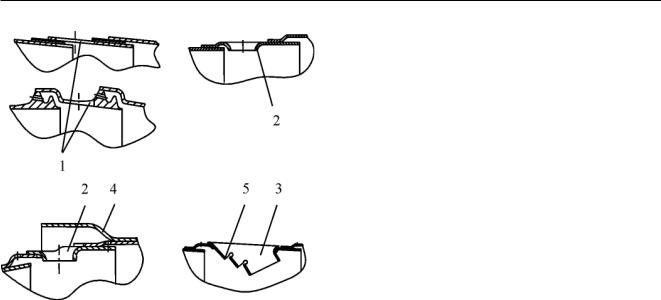
Глава 6 - Камеры сгорания
Рисунок 6.4.2_3 – Способы подвода воздуха 1 – круглые механически обрабо-
танные отверстия; 2 - отверстия с отбортовкой; 3 - смесительный патрубок; 4 – воздухозаборник; 5 – система
охлаждения патрубка
обработанные отверстия круглого сечения имеют более высокую стабильность расхода воздуха.
В некоторых случаях для увеличения пробивной способности воздушной струи используют скоростной напор воздуха – над отверстием с наружной стороны жаровой трубы устанавливают воздухозаборник 4. Применение смесительных патрубков для подвода вторичного воздуха, в основном, в кольцевых КС, вызвано необходимостью пробивать большую толщину газового потока для обеспечения более равномерного поля температур на выходе из КС. Установка патрубков в потоке газа с высокой температурой требует применения охлаждения патрубков, особенно в их передней части, например, через щели 5.
Для изготовления жаровых труб и газосборников применяют следующие материалы:
-нержавеющую сталь - до температуры 800°С;
-жаростойкие сплавы на никелевой и хромистой основе - до температуры 900…1100°С.
Новыми материалами для изготовления жаровых труб являются структуростабильные жаропрочные сплавы на никелевой и хромистой основе, отличающиеся повышенной кратковременной
èдлительной прочностью, термостойкостью и технологичностью. Их рабочая температура составляет 1100…1200°С. Применение этих материалов
может повысить ресурс жаровой трубы в полтора - два раза.
Перспективными материалами для изготовления жаровых труб также являются порошковые сплавы на основе интерметаллидов Ni3Al, NiAl, FeCrAl, предназначенные для теплонапряженных конструкций, работающих до температуры 1200…1300°С. Высокая жаростойкость, стойкость к карбидообразованию, водородному и сульфидному растрескиванию при высоких температурах, жаропрочность и относительно низкая плотность обуславливают их преимущество по сравнению с традиционными материалами.
Отраслевыми институтами ведутся работы над керамическими материалами рабочая температура, которых будет 1500°С и выше.
6.4.2.1 – Фронтовые устройства
Практически все известные КС имеют свои, отличающиеся по конструкции ФУ. Классическими примерами ФУ в виде плохо обтекаемых тел являются щелевая головка жаровой трубы 1 и конические насадки 2, устанавливаемые в передней части жаровой трубы (см. Рис. 6.4.2.1_1). Такие ФУ имеют повышенные гидравлические сопротивления, в них недостаточно полно происходит смесеобразование, вследствие чего получается сравнительно невысокая полнота сгорания и высокий уровень эмиссии.
Одним из способов получения в первичной зоне КС однородной ТВС является использование испарительных ФУ (см. Рис. 6.2.1_6).
ÂФУ с осевым 4 или радиальным 5 лопаточными завихрителями (см. Рис. 6.4.2.1_1) размеры зоны обратных токов определяются степенью крутки потока. Степень крутки потока зависит от скорости истечения воздуха из завихрителя и угла установки лопаток. Гидравлические потери в завихрительных ФУ значительно ниже, чем в щелевых и конусных.
Âнастоящее время в КС, в основном, применяются комбинированные 6 завихрительные ФУ.
Âних помимо функции стабилизации пламени обеспечивается предварительная подготовка ТВС (распыливание, смешение до нужной концентрации и степени однородности). Современные завихрительные ФУ состоят из двух и более осевых, струйных 7 и (или) радиальных завихрителей и сопловых насадков 8 различной конфигурации (см. Рис. 6.4.2.1_1). С помощью таких ФУ можно обеспечить практически все предъявляемые в настоящее время требования.
313
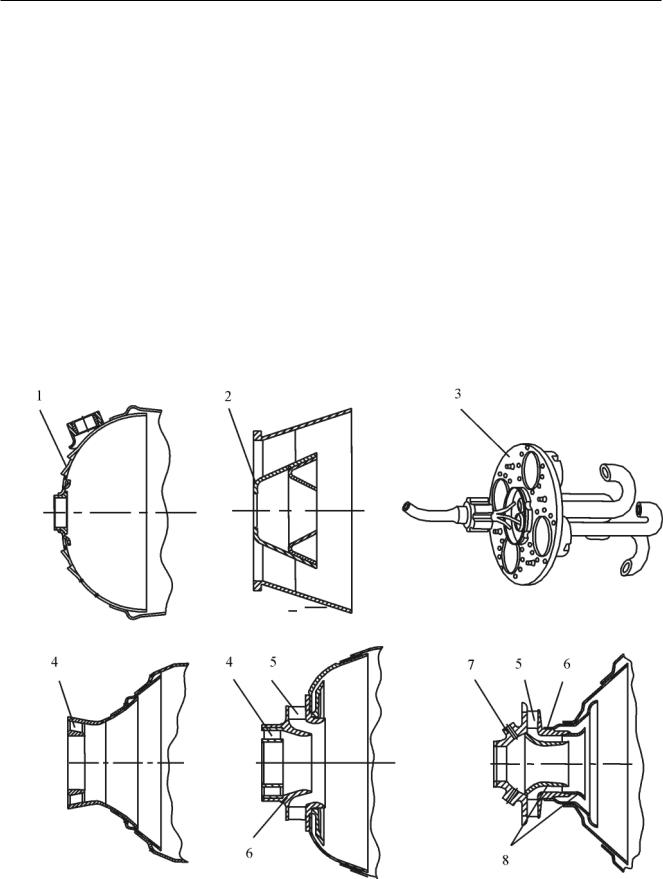
Глава 6 - Камеры сгорания
ФУ обычно изготавливают методами точного литья с последующей механической обработкой некоторых поверхностей для обеспечения необходимой точности и шероховатости обработки поверхности. Материалы для изготовления ФУ - никелевые сплавы.
ФУ крепятся на жаровых трубах трубчатых и трубчато-кольцевых КС при помощи сварки или клепки. В кольцевых КС ФУ крепятся с помощью подвижных соединений, которые компенсируют температурные расширения и неточности монтажа форсунок.
Разработка современных ФУ, состоящих из каскада осевых и (или) тангенциальных завихрителей, струйных смесителей и нескольких сопловых насадков различной конфигурации является сложной задачей. Она решается за несколько последовательных расчетных, конструкторских, исследовательских и экспериментальных шагов, в ре-
зультате которых должны быть обеспечены заданные характеристики и требования к КС, изложенные в разделе 6.1.
Во время экспериментов исследуются практически все характеристики КС:
–тонкость распыла топлива (вместе с форсункой);
–расход воздуха через ФУ;
–структура течения за ФУ, величина зоны обратных токов;
–отсутствие проскока пламени на всех режимах двигателя;
–отсутствие нагарообразования на всех режимах двигателя;
–отсутствие пульсационного горения;
–полнота сгорания;
–характеристики розжига и область устойчи- вого горения;
–влияние на поля температур;
Рисунок 6.4.2.1_1 – Фронтовые устройства КС 1 – щелевая головка; 2 – конический насадок; 3 – испарительное ФУ; 4 – осевой лопаточ-
ный завихритель; 5 - радиальный лопаточный завихритель; 6 - комбинированное завихрительное ФУ; 7 – струйный завихритель; 8 - сопловой насадок
314
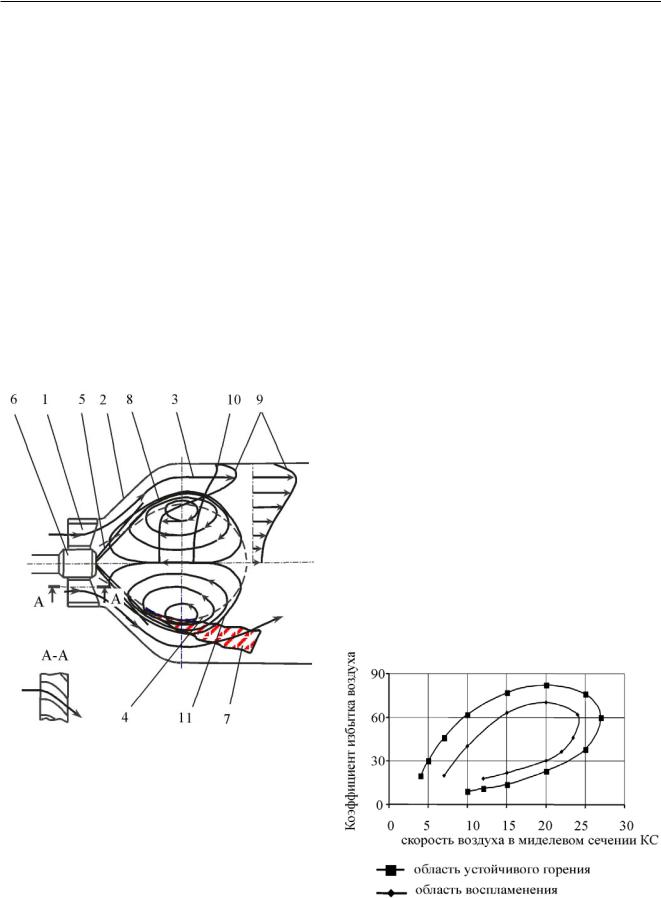
Глава 6 - Камеры сгорания
–температурное состояние стенок жаровых труб.
ФУ это именно тот узел, который конструкторы КС, создав однажды, стараются не менять, если он обеспечивает требуемые характеристики.
Принцип работы ФУ рассмотрим на примере работы типичного ФУ, образованного лопаточным завихрителем 1 и переходным конусом 2 между завихрителем и цилиндрической частью жаровой трубы. Схематично структура потока, образующаяся за подобным ФУ, показана на Рис. 6.4.2.1_2.
Физическая основа стабилизации пламени заключается в создании в головной части жаровой трубы зоны пониженного давления, которая образуется за счет эжекции газа конической струей воздуха 3, созданной завихрителем. Отток газа изнутри конической струи компенсируется его добавлением из участков, расположенных несколько дальше от
ФУ. Вследствие этого образуется зона обратных токов 4, в которой часть горячих газов движется навстречу основному потоку воздуха. Распыленное топливо 5 подается форсункой 6 в зону обратных токов. Если смесь в КС воспламенить, то стабилизация пламени 7 осуществляется вблизи внешней границы зоны обратных токов 8.
Структура потока в головной части жаровой трубы, представленная на Рис. 6.4.2.1_2 с помощью эпюры скоростей 9, эпюры давлений 10 и линий токов 11, как при холодной продувке, так и на работающей КС качественно одинакова. Но зона обратных токов на работающей КС имеет меньшие размеры. Тепловыделение в активном потоке приводит к расширению газа, но при наличии стенок газ может расширяться только в направлении к оси КС и основного движения, что и приводит к поджатию и укорочению зоны обратных токов.
Одно из основных требований к КС, которое обеспечивается в основном с помощью ФУ - широкие пределы устойчивого горения. Пределы устой- чивого горения обычно представляют в форме границ стабилизации пламени, которые разделяют область устойчивого и неустойчивого горения. Область стабилизации пламени изображается в координатах коэффициента избытка воздуха α и скорости в миделевом сечении КС. Таким образом, на каждой скорости в КС существуют значения a, при которых происходит срыв пламени: «богатый» срыв при αmin и «бедный» срыв при αmax. Границы области стабильного горения называют бедной и богатой границей. Существует максимальная скорость, при которой наступает прекращение горения при любом значении α (ñì. Ðèñ. 6.4.2.1_3).
Рисунок 6.4.2.1_2 – Структура потока и стабилизация пламени за фронтовым устройством камеры ГТД 1 - лопаточный завихритель;
2 - переходный конус; 3 - кони- ческая струя воздуха; 4 – зона обратных токов; 5 – топливный конус; 6 - форсунка; 7 – зона стабилизации пламени;
8 – граница зоны обратных то-
ков; 9 - эпюра осевых скоростей; |
Рис.6.4.2.1_3 - Область устойчивого горения и |
|
10 – эпюра давлений;11 – линии |
||
воспламенения |
||
токов |
||
|
315

Глава 6 - Камеры сгорания
6.4.2.2 – Системы охлаждения жаровой трубы
Âпроцессе горения в КС стенки жаровой трубы нагреваются конвекцией и тепловым излучением от горячих газов (в основном углекислого газа
èводяного пара) и твердых частиц (в основном сажи). Если стенки жаровой трубы не охлаждать специальным образом, то их охлаждение происходит только за счет конвективного отвода тепла к воздуху, обтекающему жаровые трубы снаружи, и путем излучения на корпуса КС.
При высоких параметрах современных двигателей без специального охлаждения стенки жаровой трубы могут разогреваться до предельных температур и прогорать. Кроме того в этих условиях нагрев и теплосъем происходит неравномерно, и на поверхности стенок образуется большой градиент температур, что приводит к их короблению. Для обеспечения заданного ресурса жаровой трубы необходимо, чтобы температура и градиент температур на ее стенке не превышали предельных значений характеристик применяемых материалов. Например, для никелевых сплавов максимальная температура составляет 850…900°С при длительной работе, 1000…1100°С при кратковременном нагреве, градиент температур - не более 50°С/мм. Для выполнения этого условия стенки жаровых труб оснащают системами охлаждения.
С помощью систем охлаждения увеличивается конвективный отвода тепла к обтекающему воздуху. Кроме этого на внутренней поверхности жаровой трубы (в большинстве систем охлаждения) создается завеса охлаждающего воздуха, которая предотвращает нагрев стенок от конвективного тепла горячих газов. В зоне интенсивного теплового излучения, где воздушная завеса не предохраняет стенки от нагрева, воздушная пелена охлаждающего воздуха конвекцией снимает тепло со стенок жаровой трубы. Для направления потока воздуха вдоль внутренней поверхности выполняют разделение стенок по длине на секции, в соединениях которых выполняют отверстия или щели для прохода охлаждающего воздуха.
Различают системы охлаждения конвективные, пленочные, конвективно-пленочные. Однако, практически любая из перечисленных систем в различ- ной степени является комбинированной в зависимости от преобладающего способа теплосъема.
Âнастоящее время чаще встречаются в конструкциях жаровых труб две разновидности конвективной системы охлаждения.
Первая - однослойная (см. Рис. 6.4.2.2_1), где охлаждение стенки жаровой трубы происходит за
счет съема тепла потоком воздуха, обтекающего жаровую трубу снаружи. При применении такого охлаждения с внешней стороны стенки жаровых труб выполняют продольные или поперечные ребра (относительно потока охлаждающего воздуха) для увеличения теплосъема. Внутреннюю поверхность выполняют гладкой, как правило, с нанесением теплозащитного покрытия.
Вторая - двухслойная (см. Рис. 6.4.2.2_2). Здесь наружная стенка 1 выполняется с мелкими отверстиями 2, через которые охлаждающий воздух 3 струйками натекает и ударяется о внутреннюю стенку 4. Ударное натекание воздуха увеличивает эффективность охлаждения. Часто при использова-
Рисунок 6.4.2.2_1 – Однослойная конвективная система охлаждения 1 – охлаждающий воздух; 2 – ребро
Рисунок 6.4.2.2_2 – Двухслойная конвективная система охлаждения 1 – наружная стенка; 2 - отвер-
стия подвода охлаждающего воздуха; 3 – охлаждающий воздух; 4 – внутренняя стенка; 5 – ребро
316

Глава 6 - Камеры сгорания
Рисунок 6.4.2.2_3 – Пленочная система охлаждения из сварных секций 1 – секция; 2 – кольцевые ребра;
3 - контактная сварка; 4 – кольцевая щель; 5 – охлаждающий воздух; 6 - заградительная пленка; 7 - компенсирующие прорези, 8 – упор
нии такой схемы охлаждения для снижения трудоемкости изготовления обе стенки делают гладкими. Но иногда для повышения эффективности теплосъема на внешней стороне внутренней стенки выполняют продольные или поперечные ребра 5.
Âконструкции жаровых труб пленочная система охлаждения получила широкое распространение. Исполнение этих систем охлаждения различно. Остановимся на нескольких конструкциях.
Âранних разработках ГТД на жаровых трубах применялась пленочная система охлаждения сварной конструкции, которая (см. Рис. 6.4.2.2_3) состоит из набора отдельных секций 1, штампованных или выкатанных из листового материала толщиной 0,8…1,5мм с кольцевыми ребрами 2. Секции сварены между собой контактной сваркой 3 с образованием в местах соединения кольцевой щели 4. Охлаждающий воздух 5 сквозь отверстия
âсекции попадает в кольцевую щель и далее направляется вдоль стенки жаровой трубы (со стороны процесса горения), образуя заградительную пленку 6. Эта пленка защищает стенку жаровой трубы от горячих продуктов сгорания. По мере удаления от щели защитная пленка постепенно перемешивается с горячими газами и размывается. Ее защитные свойства падают, поэтому секции жаровой трубы с такой системой охлаждения име-
ют большую неравномерность температур стенки по длине - это основной недостаток данной системы охлаждения. Для уменьшения термических напряжений внешние и внутренние части секций имеют продольные компенсирующие прорези 7, завершенные отверстием. Для сохранения постоянного зазора в щелях на секциях выштамповываются упоры 8. Ещ¸ один недостаток такой системы охлаждения - наличие зазора между секциями в местах контактной сварки. Зазор создает большое температурное сопротивление, что затрудняет передачу тепла от внутренней поверхности конструкции к внешней.
Более рациональной является система охлаждения, изготовленная из листовых секций 1, между стыками которых вставлены гофрированные кольца 2, приваренные контактной точечной сваркой 3 к секциям (см. Рис. 6.4.2.2_4). Гофрированные кольца закрыты от воздействия продуктов сгорания, поэтому могут быть изготовлены из ленты толщиной 0,5-0,8мм, что делает эту систему охлаждения предельно малой толщины, податливой, исключающей возникновение существенных терми- ческих напряжений. Охлаждающий воздух 4 проходит в щели гофрированного кольца и образует заградительную пленку 5. Однако такая система охлаждения может быть использована только на жаровых трубах небольшого диаметра, когда стенка малой толщины еще способна работать на устойчивость под действием перепада давления.
Конструкция пленочной системы охлаждения из точеных секций представлена на Рис. 6.4.2.2_5. Механически обработанные секции позволяют
Рисунок 6.4.2.2_4 – Пленочная система охлаждения с гофрированным кольцом [6.9.13] 1 – секция; 2 – гофрированное
кольцо; 3 - контактная точечная сварка; 4 - охлаждающий воздух; 5 - заградительная пленка
317

Глава 6 - Камеры сгорания
Рисунок 6.4.2.2_5 – Пленочные системы охлаждения, изготовленные механической обработкой а) ПС-90А ОАО«Авиадвигатель»;
á) PW2037 Pratt&Whitney; â) CF6-80 General Electric
1 – кольцевой канал; 2 – лазерная сварка; 3 – кольцевые ребра
Рисунок 6.4.2.2_6 – Транспирационная система охлаждения 1 – подвод охлаждающего возду-
ха; 2 - отверстия во внешней стенке; 3 - каналы внутреннего охлаждения; 4 - отверстия во внутренней стенке; 5 - воздушная заградительная пленка
повысить точность изготовления кольцевых каналов 1, обеспечивают точное дозирование охлаждающего воздуха, отличаются повышенной прочностью и повышенной теплопроводностью от внутренней поверхности к внешней, что в конеч- ном итоге повышает их ресурс. Система охлаждения из точеных секций применена на газосборниках двигателя ПС-90А (см. Рис.6.4.2.2_5а).
Разновидностями механически обработанных систем охлаждения являются система охлаждения «double pass» фирмы Pratt&Whitney , которая изготавливается путем пластической деформации, механической обработки и лазерной сварки 2 (см. Рис. 6.4.2.2_5б). Другой вариант стенки жаровых труб, выполненной механической обработкой - это система охлаждения фирмы General Electric (см. Рис. 6.4.2.2_5в). Ребра 3 относительно большой толщины делают эти системы охлаждения проч- ными и жесткими, что позволяет им работать на устойчивость при больших диаметрах кольцевых КС. Недостатком этих систем охлаждения является то, что при большой толщине стенок возникает большой градиент температур и соответственно повышенные термические напряжения, приводящие к образованию продольных трещин.
При высоких значениях термодинамического цикла, ограниченном расходе охлаждающего воздуха для повышения эффективности охлаждения требуется повышать роль конвективного теплосъема. Наиболее прогрессивными в этом отношении являются конвективно-пленочные системы охлаждения с двойной стенкой. Примером такой конструкции является транспирационная система охлаждения, приведенная на Рис. 6.4.2.2_6. В этой системе охлаждения воздух 1 проходит через множество мелких отверстий 2 во внешней стенке и далее внутри и вдоль стенки по специальным перекрещивающимся каналам 3. После этого воздух выходит внутрь жаровой трубы также через множество мелких отверстий 4, образуя воздушную завесу 5. Главным недостатком, сдерживающим применение транспирационной системы охлаждения, является быстрое засорение внутренних каналов.
Другим примером конвективно-пленочной системы охлаждения с двойной стенкой является конструкция, приведенная на Рис. 6.4.2.2_7. В этой конструкции эффективность охлаждения увеличена за счет повышенного конвективного теплообмена при течении воздуха между стенками. С внешней стороны внутренней стенки для увеличения поверхности теплосъема и увеличения турбулентности течения охлаждающего воздуха выполнены ребра 1 (или штырьки). Обратное течение воздуха меж-
318
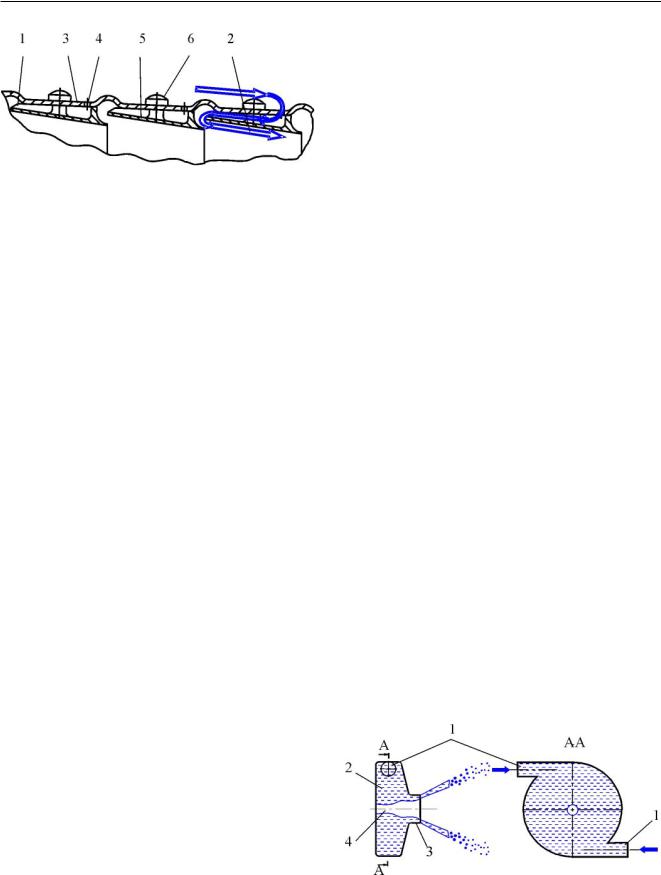
Глава 6 - Камеры сгорания
Рисунок 6.4.2.2_7 - Система охлаждения с накладными панелями [6.9.14] 1 – ребра; 2 – воздушная загради-
тельная пленка; 3 – внешняя стенка; 4 - отверстия охлаждения; 5 – накладная панель; 6 - крепление панелей.
ду стенками снижает градиент температур по длине секций. Вытекая в зазор между накладными панелями, охлаждающий воздух создает заградительную пленку 2. Такие системы охлаждения состоят из цельной внешней стенки 3 с отверстиями 4 для подвода охлаждающего воздуха и накладных панелей 5. Крепление 6 панелей выполняют с зазорами для компенсации тепловых расширений, а сами панели изготовлены из материала с малым коэффициентом линейных расширений и высокой жаростойкостью. Применение накладных панелей повышает ремонтопригодность конструкции.
В КС современных ГТД, отличающихся высокой степенью повышения давления за компрессором, с одной стороны происходит увеличение лучистых потоков тепла от газов внутри жаровой трубы к ее стенкам, с другой стороны - на входе в КС растет температура воздуха, что снижает его хладоресурс. Все это усложняет проблему охлаждения стенок жаровой трубы, и на их охлаждение расходуется более одной трети общего расхода воздуха, проходящего через КС.
Увеличение доли воздуха, подаваемого вдоль внутренней стенки жаровой трубы в сочетании с неизбежным уменьшением воздуха, подаваемого в зону смешения, ухудшает неравномерность поля температур газа за КС. Более того, охлаждающий воздух вызывает «замораживание» хими- ческих реакций при горении вблизи стенки. Это приводит к понижению полноты сгорания и увеличению выброса окиси углерода и несгоревшего углеводорода.
Вышеперечисленные причины требуют повышения эффективности системы охлаждения жаровых труб и применения специальных теплозащит-
ных покрытий. Так, для повышения стойкости материалов к газовой коррозии контактирующие с горячими газами поверхности жаровых труб покрывают жаростойкой стеклокристаллической эмалью. Широкое распространение находит применение керамических теплозащитных покрытий ZrO2 + Y2O3 толщиной 0,2…1 мм напыляемых на поверхности деталей КС, соприкасающиеся с горячими газами. Эти покрытия обладают малой степенью черноты и низкой теплопроводностью, что обеспечивает снижение температуры поверхности детали на 30…100°С в зависимости от толщины покрытия и интенсивности охлаждения.
6.4.3 – Топливные форсунки
Среди большого многообразия конструкций форсунок наибольшее распространение в основных КС ГТД получили центробежные форсунки.
Схема простейшей центробежной форсунки приведена на Рис. 6.4.3_1.
Топливо в такой форсунке поступает в тангенциальные каналы 1 камеры закручивания 2 и приобретает начальную закрутку. В камере закручивания при уменьшении диаметра крутки увеличивается окружная составляющая скорости, возникают значи- тельные центробежные силы. В выходном сопле 3 образуется тонкая пленка кольцевого сечения, которая на выходе из форсунки распадается на мельчайшие капли, создающие коническую пелену распыленного топлива. Вдоль оси форсунки при этом образуется воздушный (газовый) вихрь 4. Чем выше скорость топлива на выходе из сопла форсунки, тем более мелкими получаются капли и, тем самым, достигаются более выгодные условия для создания однородной ТВС. Величина скорости топлива на выходе из сопла определяется перепадом давления на форсунке. В общем виде перепад давления и расход топлива через форсунку связаны соотношением:
Рисунок 6.4.3_1 – Схема центробежной форсунки 1 – тангенциальные каналы; 2 – камера закручивания; 3 – сопло; 4 - воздушный вихрь
319

Глава 6 - Камеры сгорания
GÒ = Ê (∆P)0,5 |
(6.4.3.1 - 1) |
ãäå Ê– коэффициент расхода, учитывающий геометрические параметры форсунки и размерность величин GÒ è ∆P.
Форсунки должны обеспечивать распыливание топлива до капель требуемого размера с требуемой формой топливного конуса на всех режимах работы двигателя. Так, например, при переходе двигателя с режима максимальной тяги у земли на режим сильного дросселирования на большой высоте полета расход топлива уменьшается в 20…30 раз. В простой центробежной форсунке расход топлива изменяется по зависимости (6.4.3.1_1), так что для увеличения расхода топлива в 30 раз требуется увеличить перепад давления в 900 раз.
Применяемые в настоящее время топливные насосы обеспечивают максимальное давление перед форсунками примерно равное 75…80 кг/см2. Это давление не может быть существенно повышено без значительного усложнения и утяжеления топливной аппаратуры и уменьшения ее надежности. Если максимальное давление подачи составляет 75…80 кг/см2, то для уменьшения расхода в 30 раз необходимо снизить давление до 0,08…0,09 кг/см2. Но при столь низком давлении топливная струя, вытекающая из форсунки, уже практически не распадается на капли и образует «пузырь». Удовлетворительное распыливание достигается при использовании керосина лишь при избыточном давлении перед форсункой, равном 3…4 кг/см2.
Обеспечение качества распыливания на всех режимах работы двигателя в настоящее время решается тремя путями.
Первый - соединяют в одной форсунке две или несколько центробежных форсунок с концентрич- но расположенными соплами и раздельными камерами закручивания - двухсопловые форсунки 1 (см. Рис. 6.4.3_1). В первый контур 3 двухконтурных форсунок топливо подается на запуске двигателя, во второй контур 4 топливо поступает до выхода на режим малого газа, на всех остальных режимах работают оба контура.
Второй - в современных конструкциях КС применяют пневматические форсунки 2 (см. Рис. 6.4.3_1). Топливная пленка в такой форсунке расположена между двумя воздушными закрученными потоками 5 и распадается на мелкие капли за счет энергии воздуха. При использовании пневматических низконапорных форсунок снижается вес топливных агрегатов и повышается их надежность. При этом несколько усложняется конструкция самой форсунки и возникают проблемы с за-
пуском КС, так как трудно обеспечить качество распыливания топлива на низких режимах работы двигателя из-за малых скоростей воздуха.
Третий - при применении одноконтурных центробежных форсунок необходимый диапазон изменения расхода топлива получают за счет последовательного включения в работу нескольких форсунок или групп форсунок, поэтому одноконтурные форсунки находят применение во многофорсуночных КС.
Двухконтурные форсунки по типу распылителей подразделяются на двухсопловые и двухступенчатые. Двухсопловая форсунка показана на Рис. 6.4.3_2. Двухступенчатая форсунка (см. Рис. 6.4.3_3) имеет одно сопло 1 и две камеры закручивания первого 2 и второго 3 контура.
В топливных форсунках применяются различ- ные типы распылителей топлива. Конструкция некоторых распылителей, таких как «грибковый» 1, шнековый 2, неразборный 3 и разборный 4, приведены на Рис. 6.4.3_4. Каждая конструкция обладает определенными достоинствами и недостатками.
Так, например, разборный распылитель прост в изготовлении, но изготовление камеры закручи- вания и сопла как отдельных деталей приводит к их некоторой несоосности, что повышает неравномерность распыливания топлива в топливном конусе. Неразборный распылитель сложнее в изготовлении, но расточка камеры закручивания и сопла за одну установку на станке приводит к практически полному отсутствию их несоосности. Применение того или иного типа распылителей зависит от опыта
èтрадиций фирмы-разработчика. Например, шнековые распылители встречаются в форсунках фирмы General Electric, а неразборные распылители использованы в конструкции форсунок ОАО «Авиадвигатель».
Распылители изготавливают из сталей с высокой твердостью HRC = 50…56 и износоустойчи- востью, работающая до температуры 400°С. Перспективными материалами для изготовления распылителей являются твердые сплавы на основе карбида вольфрама и карбонитрадов, обладающие устойчивостью против эрозии, истирания, стойкостью к коррозии.
Топливные форсунки КС расположены в высокотемпературном воздушном потоке за КВД, а распыливающая часть – в среде горячих продуктов сгорания. Это создает дополнительные трудности связанные с термическим разложением
èкоксованием топлива в топливных каналах форсунок. Для исключения проблем, связанных с коксованием, к форсункам предъявляются следующие требования:
320
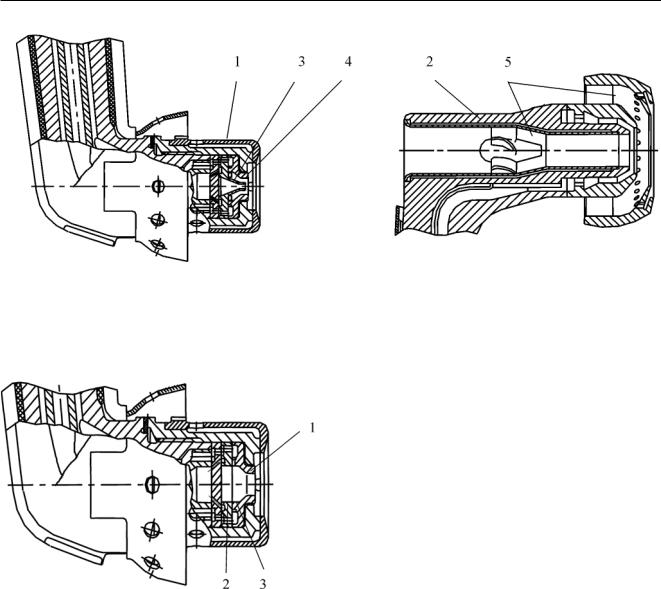
Глава 6 - Камеры сгорания
Рисунок 6.4.3_2 – Топливные форсунки
1 – центробежная двухконтурная двухсопловая; 2 – одноконтурная пневматическая; 3 - первый контур; 4 – второй контур; 5 – воздушные каналы
Рисунок 6.4.3_3 – Двухступенчатая форсунка
1 – сопло; 2 – камера закручивания первого контура; 3 - камера закручивания второго контура
-наличие теплозащиты каналов и распылителей;
-отсутствие застойных и непроточных зон;
-наличие топливных фильтров на входе;
-отсутствие топлива в каналах форсунок во время останова двигателя;
-возможность демонтажа с двигателя во время технического обслуживания;
-практически абсолютная герметичность корпуса, соединений и отсутствие перетекания топлива между контурами в холодном состоянии и при рабочей температуре.
Перечисленные требования могут быть реализованы в форсунках, корпуса которых изготовлены из цельной штампованной или высококаче- ственной литой заготовки. Разъемные резьбовые
соединения герметизируются сваркой. Неразъемные соединения выполняют пайкой высокотемпературным припоем или сваркой, как правило элек- тронно-лучевой или лазерной.
Пример конструкции центробежной двухконтурной двухсопловой форсунки двигателя ПС-90А приведен на Рис. 6.4.3_5. Форсунка состоит из корпуса 1, стакана 2, сваренного с кожухом 3, который направляет воздух для обдува торцев распылителей. Стакан с помощью резьбы прижимает к корпусу с большим моментом затяжки (5…6 кг·м) пакет элементов подачи топлива: распылитель 4 второго контура, распылитель 5 первого контура, переходник-распределитель 6 топлива и уплотнительное кольцо 7. Резьбовое соединение загерметизировано электронно-лучевой сваркой. Разделение топливных каналов внутри корпуса выполнено при помощи трубки 8 и втулок 9 и 10. Уплотнение трубки 8 и втулки 9 с корпусом сделано высокотемпературной пайкой 11, а втулки 10 - аргоннодуговой сваркой и уплотнительным кольцом 12 из терморасширенного графита. Корпус форсунки снаружи теплоизолирован стеклотканью 13, которая защищена от воздушного потока кожухом 14. В штуцерах 15 и 16 соответственно первого и второго контура установлены фильтры 17. Для исклю- чения коксования топлива в малорасходном первом контуре его канал 18 практически на всем протяжении выполнен внутри канала 19 большерасходного второго контура.
При конструировании системы подачи топлива решаются вопросы, касающиеся выбора ко-
321