
- •Содержание
- •Глава 1 - Общие сведения о газотурбинных двигателях
- •1.1 — Введение
- •1.2.1.2 — Турбовинтовые двигатели и вертолетные ГТД
- •1.2.1.3 — Двухконтурные турбореактивные двигатели (ТРДД)
- •1.2.1.4 — Двигатели для самолетов вертикального взлета и посадки
- •1.2.1.5 - Комбинированные двигатели для больших высот и скоростей полета
- •1.2.1.6 - Вспомогательные авиационные ГТД и СУ
- •1.2.2 - Авиационные СУ
- •1.2.3 - История развития авиационных ГТД
- •1.2.3.1 - Россия
- •1.2.3.2 - Германия
- •1.2.3.3 – Англия
- •1.3 - ГТД наземного и морского применения
- •1.3.1 - Области применения наземных и морских ГТД
- •1.3.1.1 -Механический привод промышленного оборудования
- •1.3.1.2 - Привод электрогенераторов
- •1.3.1.3 - Морское применение
- •1.3.2 - Основные типы наземных и морских ГТД
- •1.3.2.1 - Стационарные ГТД
- •1.3.2.2 - Наземные и морские ГТД, конвертированные из авиадвигателей
- •1.3.2.3 - Микротурбины
- •1.4 - Основные мировые производители ГТД
- •1.4.1 - Основные зарубежные производители ГТД
- •1.4.2 - Основные российские производители ГТД
- •1.6 - Перечень использованной литературы
- •Глава 2 - Основные параметры и требования к ГТД
- •2.1 - Основы рабочего процесса ГТД
- •2.1.1 - ГТД как тепловая машина
- •2.1.1.1 – Простой газотурбинный цикл
- •2.1.1.2 - Применение сложных циклов в ГТД
- •2.1.2 - Авиационный ГТД как движитель
- •2.1.3 - Полный к.п.д. и топливная эффективность (экономичность) ГТД
- •2.2 - Параметры ГТД
- •2.2.1 - Основные параметры авиационных ГТД
- •2.2.2 - Основные параметры наземных и морских приводных ГТД
- •2.3 - Требования к авиационным ГТД
- •2.3.1 - Требования к тяге (мощности)
- •2.3.2 – Требования к габаритным и массовым характеристикам
- •2.3.3 - Возможность развития ГТД по тяге (мощности)
- •2.3.4 - Требования к используемым горюче-смазочным материалам
- •2.3.4.1 - Топлива авиационных ГТД
- •2.3.4.2 – Авиационные масла
- •2.3.4.3 - Авиационные гидравлические жидкости
- •2.3.5 – Надежность авиационных ГТД
- •2.3.5.1 – Основные показатели
- •2.3.5.1.1 – Показатели безотказности, непосредственно влияющие на безопасность работы двигателя
- •2.3.5.2 – Методология обеспечения надежности
- •2.3.5.2.1 – Этап проектирования
- •2.3.6 - Ресурс авиационных ГТД
- •2.3.6.1 - Методология обеспечения ресурса
- •2.3.6.2 - Количественные показатели ресурса
- •2.3.7 - Требования производственной технологичности
- •2.3.8 - Требования эксплуатационной технологичности
- •2.3.8.1 - Эксплуатационная технологичность - показатель совершенства ГТД
- •2.3.8.2 - Основные качественные характеристики ЭТ
- •2.3.8.3 - Количественные показатели ЭТ
- •2.3.9 - Экономические требования к авиационным ГТД
- •2.3.9.1 - Себестоимость производства
- •2.3.9.2 - Стоимость ЖЦ двигателя
- •2.3.10 - Экологические требования
- •2.3.10.2 - Ограничения по шуму
- •2.3.12 - Соответствие требованиям летной годности
- •2.4 - Особенности требований к ГТД наземного применения
- •2.4.1 - Особенности требований к приводным ГТД для ГПА
- •2.4.1.1 - Требования к характеристикам ГТД
- •2.4.1.2 - Требования к ресурсам и надежности
- •2.4.1.4 - Используемые ГСМ
- •2.4.1.5 - Требования экологии и безопасности
- •2.4.1.6 - Требования производственной и эксплуатационной технологичности
- •2.4.2 - Особенности требований к ГТД энергетических установок
- •2.4.2.1 - Требования к характеристикам ГТД
- •2.4.2.2 - Используемые ГСМ
- •2.4.2.3 - Требования к ресурсам и надежности
- •2.4.2.4 - Требования к экологии и безопасности
- •2.4.2.5 - Требования к контролепригодности, ремонтопригодности и др.
- •2.5 - Методология проектирования
- •2.5.1 - Основные этапы проектирования ГТД
- •2.5.1.1 - Техническое задание
- •2.5.1.2 – Техническое предложение
- •2.5.1.3 – Эскизный проект
- •2.5.1.4 – Технический проект
- •2.5.1.5 – Разработка конструкторской документации
- •2.5.2 - Разработка конструкций ГТД на основе базовых газогенераторов
- •2.5.2.1 - Газогенератор – базовый узел ГТД
- •2.5.2.2 – Основные параметры и конструктивные схемы газогенераторов ГТД
- •2.5.2.3 – Создание ГТД различного назначения на базе единого газогенератора
- •2.6.1.1 — Общие положения по авиационным ГТД
- •2.6.1.2 — Общие положения по сертификации наземной техники
- •2.6.1.3 — Общие положения по сертификации производства и СМК
- •2.6.1.4 — Органы регулирования деятельности
- •2.6.1.4.1 — Авиационная техника
- •2.6.1.4.2 — Органы регулирования деятельности по сертификации производства и СМК
- •2.6.2.1 — Авиационная техника
- •2.6.2.2 — Наземная техника
- •2.6.2.3 Производство и СМК
- •2.6.2.4 — Принятые сокращения и обозначения
- •2.6.3.1 — Основные этапы создания авиационных ГТД
- •2.6.3.2 — Этапы процесса сертификации авиационных ГТД
- •Глава 3 - Конструктивные схемы ГТД
- •3.1 - Конструктивные схемы авиационных ГТД
- •3.1.1 - Турбореактивные двигатели
- •3.1.2 - Двухконтурные турбореактивные двигатели
- •3.1.3 - Турбовинтовые и вертолетные ГТД
- •3.2 - Конструктивные схемы наземных и морских ГТД
- •3.2.1 - Одновальные ГТД
- •3.2.2 - ГТД со свободной силовой турбиной
- •3.2.3 - ГТД со «связанным» КНД
- •3.2.4 - Конструктивные особенности наземных ГТД различного назначения
- •3.2.5 - Конструктивные особенности ГТД сложных циклов
- •3.4 - Перечень использованной литературы
- •Глава 4 - Силовые схемы ГТД
- •4.1 - Усилия, действующие в ГТД
- •4.1.2 - Крутящие моменты от газовых сил
- •Глава 5 - Компрессоры ГТД
- •6.4.4 - Корпуса КС
- •6.4.4.1 - Наружный корпус КС
- •6.4.4.2 - Внутренний корпус КС
- •6.4.4.3 - Разработка конструкции корпусов
- •6.4.5 - Системы зажигания ГТД
- •6.5 - Экспериментальная доводка КС
- •6.6 - Особенности КС двигателей наземного применения
- •6.7 - Перспективы развития камер сгорания ГТД
- •Глава 7 - Форсажные камеры
- •7.1 - Характеристики ФК
- •7.2 - Работа ФК
- •7.3 - Требования к ФК
- •7.4 - Схемы ФК
- •7.4.2 - Вихревые ФК
- •7.4.3 - ФК с аэродинамической стабилизацией
- •7.5 - Основные элементы ФК
- •7.5.1 - Смеситель
- •7.5.2 - Диффузоры
- •7.5.3 - Фронтовые устройства
- •7.5.4 - Корпусы и экраны
- •7.6 - Управление работой ФК
- •7.6.1 - Розжиг ФК
- •7.6.2 - Управление ФК на режимах приемистости и сброса
- •7.6.3 - Управление ФК на стационарных режимах
- •Глава 8 - Турбины ГТД
- •8.2 - Аэродинамическое проектирование турбины
- •8.2.2 - Технология одномерного проектирования турбины
- •8.2.4 - 2D/3D-моделирование невязкого потока в проточной части турбины
- •8.2.5 - 2D/3D-моделирование вязкого потока в турбине
- •8.2.6 - Синтез геометрии профилей и лопаточных венцов
- •8.2.7 - Одномерное проектирование турбины
- •8.2.7.1 - Выбор количества ступеней ТВД
- •8.2.7.2 - Выбор количества ступеней ТНД
- •8.2.7.3 - Аэродинамическое проектирование и к.п.д. турбины
- •8.2.9 - Методы управления пространственным потоком в турбине
- •8.2.10 - Экспериментальное обеспечение аэродинамического проектирования
- •8.2.11 - Перечень использованной литературы
- •8.3 - Охлаждение деталей турбины
- •8.3.1 - Тепловое состояние элементов турбин
- •8.3.1.1 - Принципы охлаждения
- •8.3.2 - Конвективное, пленочное и пористое охлаждение
- •8.3.3 - Гидравлический расчет систем охлаждения
- •8.3.4 - Методология расчета температур основных деталей турбин
- •8.3.5 - Расчет полей температур в лопатках
- •8.3.6 - Перечень использованной литературы
- •8.4 - Роторы турбин
- •8.4.1 - Конструкции роторов
- •8.4.1.1 - Диски турбин
- •8.4.1.2 - Роторы ТВД
- •8.4.1.3 - Роторы ТНД и СТ
- •8.4.1.4 - Примеры доводки и совершенствования роторов
- •8.4.1.5 - Предотвращение раскрутки и разрушения дисков
- •8.4.2 - Рабочие лопатки турбин
- •8.4.2.1 - Соединение рабочих лопаток с диском
- •8.4.3 - Охлаждение рабочих лопаток
- •8.4.4 - Перечень использованной литературы
- •8.5 - Статоры турбин
- •8.5.1 - Корпусы турбин
- •8.5.2 - Сопловые аппараты
- •8.5.3 - Аппараты закрутки
- •8.5.4 – Перечень использованной литературы
- •8.6 - Радиальные зазоры в турбинах
- •8.6.1 - Влияние радиального зазора на к.п.д. турбины
- •8.6.2 - Изменение радиальных зазоров турбины в работе
- •8.6.3 - Управление радиальными зазорами
- •8.6.4 - Выбор радиального зазора при проектировании
- •8.6.5 - Перечень использованной литературы
- •8.7 - Герметизация проточной части
- •8.7.1 - Герметизация ротора и статора от утечек охлаждающего воздуха
- •8.7.2 - Уплотнения между ротором и статором
- •8.7.3 - Перечень использованной литературы
- •8.8 - Материалы основных деталей турбины
- •8.8.1 - Диски и роторные детали турбины
- •8.8.2 - Сопловые и рабочие лопатки
- •8.8.3 - Покрытия лопаток
- •8.8.4 - Корпусы турбин
- •8.9.1 - Перечень использованной литературы
- •8.10.1 - Прогары и трещины лопаток ТВД
- •8.10.3 - Недостаточный циклический ресурс и поломки роторных деталей
- •8.10.4 - Устранение дефектов турбины в ходе доводки
- •8.11 - Перспективы развития конструкций и методов проектирования турбин
- •8.11.1 - 2D-аэродинамика: эффективные охлаждаемые лопатки ТВД
- •8.11.2 - 2D-аэродинамика: сокращение количества лопаток
- •8.11.3 - Противоположное вращение роторов ТВД и ТНД
- •8.11.4 - 2D-аэродинамика: эффективные решетки профилей ТНД
- •8.11.5 - 3D-аэродинамика: эффективные формы лопаточных венцов
- •8.11.6 - Новые материалы и покрытия для лопаток и дисков
- •8.11.7 - Совершенствование конструкций охлаждаемых лопаток
- •8.11.8 - Оптимизированные системы управления радиальными зазорами
- •8.11.9 - Развитие средств и методов проектирования
- •Глава 9 - Выходные устройства ГТД
- •9.1 - Нерегулируемые сопла
- •9.2 - Выходные устройства ТРДД
- •9.2.1 - Выходные устройства со смешением потоков
- •9.2.2 - Выходные устройства ТРДД с раздельным истечением потоков
- •9.3 - Регулируемые сопла
- •9.3.1 - Осесимметричные регулируемые сопла
- •9.3.1.1 - Регулируемое сопло двигателя Д30-Ф6
- •9.3.2 - Плоские сопла
- •9.4 - Выходные устройства двигателей самолетов укороченного и вертикального взлета-посадки
- •9.5 - «Малозаметные» выходные устройства
- •9.6 - Реверсивные устройства
- •9.6.1 - Реверсивные устройства ковшового типа
- •9.6.2 - Реверсивные устройства створчатого типа
- •9.6.3.1 - Гидравлический привод реверсивного устройства
- •9.6.3.3 - Механический замок фиксации положения реверсивного устройства
- •9.7 - Приводы выходных устройств
- •9.7.1 - Пневмопривод
- •9.7.2 - Пневмомеханический привод
- •9.8 - Выходные устройства диффузорного типа
- •9.8.1 - Конические диффузоры
- •9.8.2 - Осекольцевые диффузоры
- •9.8.3 - Улитки
- •9.8.4 - Соединения с выхлопными шахтами
- •9.8.5 - Выходные устройства вертолетных ГТД
- •9.12 - Перечень использованной литературы
- •Глава 10 - Привод агрегатов, редукторы, муфты ГТД
- •10.1 - Привод агрегатов ГТД
- •10.1.1 - Центральный привод
- •10.1.2 - Коробки приводов агрегатов
- •10.2 - Редукторы ГТД
- •10.2.1 - Редукторы ТВД
- •10.2.1.1 - Общие требования, кинематические схемы
- •10.2.1.2 - Конструкция редукторов ТВД
- •10.2.2 - Редукторы привода несущего и рулевого винтов вертолетов
- •10.2.2.1 - Редукторы привода несущего винта
- •10.2.2.1.1 - Кинематические схемы главных редукторов вертолетов
- •10.2.2.1.2 - Конструкция главных редукторов вертолетов
- •10.2.2.2 - Редукторы хвостовые и промежуточные
- •10.2.3 - Редукторы ГТУ
- •10.2.3.1 - Конструкция редукторов
- •10.3 - Муфты приводов ГТД и ГТУ
- •10.3.1 - Требования к муфтам
- •10.3.2 - Конструкция муфт
- •10.4 - Проектирование приводов агрегатов ГТД
- •10.4.1 - Проектирование центрального привода
- •10.4.1.1 - Конструкция центрального привода
- •10.4.2 - Проектирование коробок приводов агрегатов
- •10.4.2.1 - Конструкция коробки приводов агрегатов
- •10. 5 - Проектирование редукторов
- •10.5.1 - Особенности проектирования редукторов ТВД
- •10.5.2 - Особенности проектирования вертолетных редукторов
- •10.5.3 - Особенности проектирования редукторов ГТУ
- •10.6.1 - Требования к зубчатым передачам
- •10.6.2 - Классификация зубчатых передач
- •10.6.3 - Исходный производящий контур
- •10.6.4 - Нагруженность зубчатых передач
- •10.6.5 - Конструктивные параметры зубчатых передач
- •10.6.5.1 - Конструкции зубчатых колес
- •10.6.6 - Материалы зубчатых колес, способы упрочнения
- •Глава 11 - Пусковые устройства
- •11.1 - Общие сведения
- •11.1.1 - Основные типы пусковых устройств современных ГТД
- •11.1.2 - Технические характеристики пусковых устройств современных ГТД
- •11.2 - Электрические пусковые устройства ГТД
- •11.3 - Воздушные пусковые устройства ГТД
- •11.3.1 - Воздушно - турбинные пусковые устройства ГТД
- •11.3.2 - Регулирующие и отсечные воздушные заслонки
- •11.3.3 - Струйное пусковое устройство ГТД
- •11.4 - Турбокомпрессорные пусковые устройства ГТД
- •11.4.1 - Классификация ТКС ГТД
- •11.4.2 - Принцип действия ТКС
- •11.4.3 - Одновальный ТКС
- •11.4.4 - ТКС со свободной турбиной
- •11.4.5 - Особенности систем ТКС
- •11.5 - Гидравлические пусковые устройства ГТД
- •11.5.1 - Конструкция гидравлических стартеров
- •11.6 - Особенности пусковых устройств ГТД наземного применения
- •11.6.1 - Электрические пусковые устройства
- •11.6.2 - Газовые пусковые устройства
- •11.6.3 - Гидравлические пусковые устройства
- •11.7 - Редукторы пусковых устройств
- •11.8 - Муфты свободного хода пусковых устройств
- •11.8.1 - Муфты свободного хода роликового типа
- •11.8.2 – Муфты свободного хода храпового типа
- •11.9 – Системы смазки пусковых устройств
- •11.11 - Перечень используемой литературы
- •Глава 12 - Системы ГТД
- •12.1.1 - Системы автоматического управления и контроля авиационных ГТД
- •12.1.1.1 - Назначение САУ
- •12.1.1.2 - Состав САУ
- •12.1.1.3 - Основные характеристики САУ
- •12.1.1.5.2 - Порядок разработки САУ
- •12.1.1.5.3 - Основные принципы выбора варианта САУ в процессе проектирования
- •12.1.1.5.4 - Структурное построение САУ
- •12.1.1.5.5 - Программы управления ГТД
- •12.1.1.5.6 - Расчет и анализ показателей надежности
- •12.1.2 - САУ наземных ГТУ
- •12.1.2.1 - Назначение САУ
- •12.1.2.2 - Выбор САУ ГТУ и ее элементов
- •12.1.2.3 - Состав САУ ГТУ
- •12.1.2.4 - Основные характеристики САУ
- •12.1.2.5 - Работа САУ ГТУ
- •12.1.2.6 - Блок управления двигателем (БУД)
- •12.1.2.7 - Особенности системы контроля и диагностики наземных ГТД
- •12.1.4 – Перечень использованной литературы
- •12.2 - Топливные системы ГТД
- •12.2.1 - Топливные системы авиационных ГТД
- •12.2.1.1 - Назначение топливной системы
- •12.2.1.2 - Состав топливной системы
- •12.2.1.3 - Основные характеристики топливной системы
- •12.2.1.4 - Работа топливной системы
- •12.2.1.5 - Выбор топливной системы и ее элементов
- •12.2.1.5.1 – Выбор топливной системы
- •12.2.1.5.2 - Выбор насосов топливной системы
- •12.2.1.5.3 - Определение подогревов топлива в топливной системе
- •12.2.1.5.5 - Математическая модель топливной системы
- •12.2.1.6 - Гидроцилиндры
- •12.2.1.7 - Топливные фильтры
- •12.2.2 - Особенности топливных систем ГТУ
- •12.2.2.1 - Назначение топливной системы
- •12.2.2.2 - Выбор топливной системы и ее элементов
- •12.2.2.3 - Основные характеристики топливной системы
- •12.2.2.4 - Работа топливной системы
- •12.2.4 – Перечень использованной литературы
- •12.3 - Системы диагностики
- •12.3.1 - Общие вопросы диагностирования
- •12.3.1.1 - Задачи диагностирования ГТД
- •12.3.1.3 - Диагностируемые системы ГТД
- •12.3.1.4 - Виды наземного и бортового диагностирования ГТД
- •12.3.1.5 - Структура систем диагностики
- •12.3.1.6 - Регламент диагностирования ГТД
- •12.3.1.7 - Регистрация параметров ГТД
- •12.3.2 - Диагностирование системы механизации ГТД, САУ и ТП ГТД
- •12.3.3 - Диагностирование работы маслосистемы и состояния узлов ГТД, работающих в масле
- •12.3.3.1 - Неисправности маслосистемы и узлов ГТД, работающих в масле
- •12.3.3.2 - Диагностирование по параметрам маслосистемы
- •12.3.3.3 - Контроль содержания в масле частиц износа (трибодиагностика)
- •12.3.4 - Контроль и диагностика по параметрам вибрации ГТД
- •12.3.4.1 - Параметры вибрации и единицы изменения
- •12.3.4.2 - Статистические характеристики вибрации
- •12.3.4.3 - Причины возникновения вибрации в ГТД
- •12.3.4.4 - Датчики измерения вибрации
- •12.3.4.5 - Вибрационная диагностика ГТД
- •12.3.5 - Диагностирование ГТД по газодинамическим параметрам
- •12.3.5.1 - Неисправности проточной части ГТД
- •12.3.5.2 - Требования к перечню контролируемых параметров
- •12.3.5.3 - Алгоритмы диагностирования проточной части ГТД
- •12.3.6 - Обеспечение диагностирования ГТД инструментальными методами
- •12.3.6.1 - Виды неисправностей, выявляемых инструментальными методами
- •12.3.6.2 - Методы и аппаратура инструментальной диагностики
- •12.3.6.2.1 - Оптический осмотр проточной части ГТД
- •12.3.6.2.2 - Ультразвуковой метод диагностирования
- •12.3.6.2.3 - Вихретоковый метод диагностирования
- •12.3.6.2.4 - Капиллярный метод диагностирования с применением портативных аэрозольных наборов
- •12.3.6.2.5 - Диагностирование состояния проточной части ГТД перспективными методами
- •12.3.7 - Особенности диагностирования технического состояния ГТД наземного применения на базе авиационных двигателей
- •12.3.7.1 - Особенности режимов эксплуатации
- •12.3.7.2 - Общие особенности диагностирования наземных ГТД
- •12.3.7.3 - Особенности диагностирования маслосистемы
- •12.3.7.5 - Особенности диагностирования проточной части
- •12.4 - Пусковые системы
- •12.4.1 - Пусковые системы авиационных ГТД
- •12.4.1.1 - Назначение
- •12.4.1.2 - Общие требования
- •12.4.1.3 - Состав пусковых систем
- •12.4.1.4 - Область эксплуатации двигателя, область запуска
- •12.4.1.6 - Надежность запуска
- •12.4.1.7 - Характеристики запуска
- •12.4.1.8. - Выбор типа и параметров стартера
- •12.4.1.9 - Особенности запуска двигателей двухроторных схем
- •12.4.1.10 - Системы зажигания
- •12.4.1.11 - Обеспечение характеристик запуска на разгоне
- •12.4.1.12 - Регулирование компрессора на пусковых режимах
- •12.4.2 - Особенности пусковых систем наземных ГТУ
- •12.4.4 - Перечень использованной литературы
- •12.5 - Воздушные системы ГТД
- •12.5.1 - Функции ВС
- •12.5.2 - Основные требования к ВС
- •12.5.3 - Общие и локальные ВС ГТД
- •12.5.4 - Работа локальных ВС
- •12.5.4.1 - ВС охлаждения турбин ГТД
- •12.5.4.2 - ВС наддува и охлаждения опор
- •12.5.4.2.1 - Работа ВС наддува и охлаждения опор
- •12.5.4.2.2 - Типы ВС наддува и охлаждения опор
- •12.5.4.2.3 - Построение общей схемы ВС наддува и охлаждения опор
- •12.5.4.3 - Противообледенительная система (ПОС)
- •12.5.4.4 - Система кондиционирования воздуха
- •12.5.4.5 - Система активного управления зазорами
- •12.5.4.6 - Системы внешнего охлаждения ГТД
- •12.5.4.7 - Системы внешнего обогрева ГТД
- •12.5.5 - Подготовка воздуха для ВС ГТД
- •12.5.6 - Особенности ВС наземных ГТУ
- •12.5.7 - Агрегаты ВС
- •12.5.9 - Перечень использованной литературы
- •12.6.1 - Общие требования
- •12.6.2 - Схемы маслосистем ГТД
- •12.6.2.1 - Маслосистема с регулируемым давлением масла
- •12.6.2.2 - Маслосистема с нерегулируемым давлением масла
- •12.6.2.3 - Маслосистемы ГТД промышленного применения
- •12.6.3 - Маслосистемы редукторов
- •12.6.3.1 - Маслосистемы авиационных редукторов
- •12.6.3.2 - Маслосистемы редукторов ГТУ
- •12.6.4 - Особенности проектирование маслосистем
- •12.6.5 - Агрегаты маслосистемы
- •12.6.5.1 - Бак масляный
- •12.6.5.2 - Насосы масляные
- •12.6.5.3 - Теплообменники
- •12.6.5.4 - Фильтры и очистители
- •12.6.5.5 - Воздухоотделители и суфлеры
- •12.6.6 - Перспективы развития маслосистем
- •12.6.8 – Перечень использованной литературы
- •12.7 - Гидравлические системы ГТД
- •12.7.1 - Гидросистемы управления реверсивными устройствами
- •12.7.1.1 - Централизованная гидросистема управления реверсивным устройством
- •12.7.1.2 - Автономная гидросистема управления реверсивным устройством
- •12.7.1.3 - Порядок проектирования гидросистем
- •12.7.3 - Перечень использованной литературы
- •12.8 - Дренажные системы
- •12.8.1 - Назначение и классификация систем
- •12.8.2 - Характеристика объектов дренажа
- •12.8.3 - Основные схемы и принцип действия систем
- •12.8.4 - Основные требования к дренажным системам
- •12.8.5 - Обеспечение работоспособности дренажных систем
- •12.8.6 - Особенности конструкции дренажных баков
- •12.8.8 - Перечень использованной литературы
- •Глава 13 - Обвязка авиационных ГТД
- •13.1 - Общая характеристика обвязки
- •13.2 - Конструкция обвязки
- •13.2.1 - Трубопроводные коммуникации
- •13.2.1.1 - Основные сведения
- •13.2.1.2 - Трубы и патрубки
- •13.2.1.3 - Соединения
- •13.2.1.4 - Компенсирующие устройства
- •13.2.1.5 - Соединительная арматура
- •13.2.1.6 - Узлы крепления
- •13.2.1.7 - Неисправности трубопроводов
- •13.2.2 - Электрические коммуникации
- •13.2.2.1 - Общие сведения
- •13.2.2.2 - Конструкция элементов
- •13.2.2.2.1 - Электрические жгуты
- •13.2.2.2.2 - Электрические провода
- •13.2.2.2.3 - Электрические соединители
- •13.2.2.2.4 - Материалы для изготовления электрических жгутов
- •13.2.3 - Узлы крепления агрегатов и датчиков
- •13.2.4 - Механическая проводка управления
- •13.3 - Проектирование обвязки
- •13.3.1 - Требования к обвязке
- •13.3.2 - Основные принципы и порядок проектирования обвязки
- •13.3.3 - Методы отработки конструкции обвязки
- •13.3.3.1 - Натурное макетирование
- •13.3.3.2 - Электронное макетирование обвязки
- •13.3.5 - Проектирование трубопроводных коммуникаций
- •13.3.6 - Проектирование электрических коммуникаций
- •13.3.6.1 - Требования к электрическим коммуникациям
- •13.3.6.2 - Порядок проектирования электрических коммуникаций
- •13.3.6.3 - Разработка электрических схем
- •13.3.6.4 - Разработка монтажных схем
- •13.3.6.5 - Разработка чертежей электрических жгутов
- •13.6 - Перечень использованной литературы
- •Глава 14 - Динамика и прочность ГТД
- •14.1 - Теоретические основы динамики и прочности ГТД
- •14.1.1 - Напряженное состояние, тензор напряжений
- •14.1.2 - Уравнения равновесия
- •14.1.3 - Перемещения в деформируемом твердом теле. Тензор деформаций
- •14.1.4 - Уравнения совместности деформаций
- •14.1.5 - Обобщенный закон Гука
- •14.1.7 - Плоская задача теории упругости
- •14.1.8 - Пластическая деформация материала. Простое и сложное нагружение
- •14.1.11 - Ползучесть. Релаксация напряжений. Длительная прочность
- •14.1.12 - Усталостное разрушение элементов конструкций
- •14.1.13 - Малоцикловая усталость. Термическая усталость
- •14.1.14 - Накопление повреждений при нестационарном нагружении
- •14.1.15 - Закономерности развития трещин в элементах конструкций
- •14.1.16 - Свободные колебания системы с одной степенью свободы
- •14.1.17 - Вынужденные колебания системы с одной степенью свободы
- •14.1.18 - Колебания системы с вязким сопротивлением. Демпфирование колебаний
- •14.1.19 - Вынужденные колебания системы с одной степенью свободы под действием произвольной периодической возмущающей силы
- •14.1.21 - Колебания системы с распределенной массой
- •14.2 - Статическая прочность и циклическая долговечность лопаток
- •14.2.1 - Нагрузки, действующие на лопатки. Расчетные схемы лопаток
- •14.2.2 - Напряжения растяжения в профильной части рабочей лопатки от центробежных сил
- •14.2.3 - Изгибающие моменты и напряжения изгиба от газодинамических сил
- •14.2.5 - Суммарные напряжения растяжения и изгиба в профильной части лопатки
- •14.2.6 - Температурные напряжения в лопатках
- •14.2.7 - Особенности напряженного состояния широкохордных рабочих лопаток
- •14.2.9 - Расчет соединения рабочих лопаток с дисками
- •14.2.10 - Расчет на прочность антивибрационных (бандажных) полок и удлинительной ножки лопатки
- •14.2.11 - Особенности расчета на прочность лопаток статора
- •14.2.13 - Анализ трехмерных полей напряжений и деформаций в лопатках
- •14.3 - Статическая прочность и циклическая долговечность дисков
- •14.3.1 - Расчетные схемы дисков
- •14.3.2 - Расчет напряжений в диске в плоской оссесимметричной постановке
- •14.3.3 - Общие закономерности напряженного состояния дисков
- •14.3.7 - Подтверждение циклического ресурса дисков на основе концепции допустимых повреждений
- •14.3.8 - Расчет роторов барабанного типа
- •14.3.9 - Расчет дисков радиальных турбомашин
- •14.3.10 - Оптимальное проектирование дисков. Равнопрочный диск
- •14.4 - Колебания и вибрационная прочность лопаток осевых компрессоров и турбин
- •14.4.2 - Приближенный расчет собственных частот колебаний лопаток
- •14.4.3 - Трехмерные модели колебаний лопаток
- •14.4.4 - Влияние конструктивных и эксплуатационных факторов на собственные частоты колебаний лопатки
- •14.4.6 - Автоколебания лопаток
- •14.4.7 - Демпфирование колебаний лопаток
- •14.4.8 - Вынужденные колебания лопаток. Резонансная диаграмма
- •14.4.9 - Математическое моделирование вынужденных колебаний лопаток
- •14.4.10 - Экспериментальное исследование колебаний лопаток
- •14.4.11 - Коэффициент запаса вибрационной прочности лопаток, пути его повышения
- •14.4.12 - Колебания дисков
- •14.5 - Динамика роторов. Вибрация ГТД
- •14.5.1 - Критическая частота вращения ротора. История вопроса
- •14.5.2 - Динамика одномассового ротора. Поступательные перемещения
- •14.5.3 - Динамика одномассового ротора. Угловые перемещения
- •14.5.4 - Динамика одномассового несимметричного ротора
- •14.5.5 - Ротор с распределенными параметрами
- •14.5.6 - Особенности колебаний системы роторов и корпусов
- •14.5.7 - Демпфирование колебаний роторов
- •14.5.7.1 - Конструкция и принцип действия демпферов колебаний роторов
- •14.5.7.2 - Расчет параметров демпфирования
- •14.5.7.3 - Особенности гидромеханики реальных демпферов
- •14.5.8 - Вибрация ГТД
- •14.5.8.1 - Источники возмущающих сил и спектр вибрации
- •14.5.8.3 - Статистические характеристики вибрации
- •14.5.8.4 - Измерение и нормирование вибрации
- •14.6 - Прочность корпусов и подвески двигателя
- •14.6.1 - Силовая схема корпуса. Условия работы силовых корпусов
- •14.6.4 - Устойчивость корпусных деталей
- •14.6.5 - Расчет корпусов на непробиваемость
- •14.6.6 - Расчет элементов подвески
- •14.8 – Перечень использованной литературы
- •Глава 15 - Шум ГТД
- •15.1 - Источники шума ГТД
- •15.3 - Методы оценки акустических характеристик
- •15.4 - Снижение шума ГТД
- •15.4.1 - Методология проектирования систем шумоглушения
- •15.4.2 - Шумоглушение в выходных устройствах авиационных ГТД
- •15.4.3 - Конструкция звукопоглощающих узлов авиационных ГТД
- •15.4.4 – Глушители шума в наземных ГТУ
- •15.4.5 – Конструкция глушителей шума наземных ГТД
- •15.7 – Список использованной литературы
- •Глава 16 - Газотурбинные двигатели как силовой привод
- •16.1 - ГТД в силовом приводе ГТЭС и ГПА
- •16.2 - ГТД в силовых (энергетических) установках кораблей и судов
- •16.3 - ГТД в силовых установках танков
- •16.5 - Компоновка корабельных и судовых ГГТД
- •16.6 - Компоновка ГТД в силовой установке танка
- •16.8 – Перечень использованной литературы
- •Глава 17 - Автоматизация проектирования и поддержки жизненного цикла ГТД
- •17.1 - Проектирование и информационная поддержка жизненного цикла ГТД (идеология CALS)
- •17.2 - Жизненный цикл изделия. Обзор методов проектирования
- •17.3 - Программные средства проектирования
- •17.4 - Аппаратные средства систем проектирования
- •17.5 - PDM-системы: роль и место в организации проектирования
- •17.6 - Организация производства и ERP-системы
- •17.7 - Параллельный инжиниринг. Интеграция эскизного и технического проектирования
- •17.8 - Переход на безбумажную технологию
- •17.10 - ИПИ-технологии и эксплуатация изделий
- •17.11 - ИПИ-технологии и управление качеством
- •17.12 - Анализ и реинжиниринг бизнес-процессов
- •17.13 - Основы трехмерного проектирования
- •17.13.1 - Общие принципы трехмерного проектирования
- •17.13.1.1 - Способы создания геометрических моделей
- •17.13.1.2 - Основные термины объемной геометрической модели
- •17.13.1.3 - Принцип базового тела
- •17.13.1.4 - Основные термины при проектировании геометрической модели детали
- •17.13.2 - Управляющие структуры
- •17.13.3 - Принцип «Мастер-модели»
- •17.13.5 - Моделирование сборок
- •17.15 - Перечень использованной литературы
- •Глава 18 - Уплотнения в ГТД
- •18.1 - Уплотнение неподвижных соединений
- •18.2 - Уплотнения подвижных соединений
- •18.2.1 - Гидравлический расчет уплотнений подвижных соединений
- •18.3 - Уплотнение газового тракта между ротором и статором ГТД
- •18.3.1 - Лабиринтные уплотнения
- •18.3.2 - Щеточные уплотнения
- •18.3.3 - Скользящие сухие уплотнения газодинамические
- •18.3.4 - Скользящие сухие уплотнения газостатические
- •18.3.5 - Сравнение эффективностей уплотнений газового тракта между ротором и статором ГТД
- •18.4 - Примеры уплотнений газового тракта ГТД
- •18.4.1 - Пример 1
- •18.4.2 - Пример 2. Уплотнение статорной и роторной частей турбины
- •18.5 - Уплотнения масляных полостей опор роторов, редукторов, коробок приводов
- •18.7 - Перечень использованной литературы

Глава 12 - Системы ГТД
12.3.3 - Диагностирование работы маслосистемы и состояния узлов ГТД, работающих в масле
Оценка технического состояния узлов и деталей ГТД, омываемых маслом, выполняется по измеряемым параметрам и методами трибодиагностики. При параметрическом анализе оценивается влияние неисправностей ГТД на параметры маслосистемы, измеряемые с помощью штатных чувствительных элементов – датчиков и сигнализаторов. С помощью методов трибодиагностики оценивается состояние узлов и деталей ГТД по продуктам износа, содержащимся в масле.
12.3.3.1 - Неисправности маслосистемы и узлов ГТД, работающих в масле
Неисправности узлов и деталей ГТД, выявляемые методами трибодиагностики и параметрической диагностики маслосистемы, делятся на следующие группы:
а) неисправности системы измерения параметров маслосистемы (датчиков, сигнализаторов, разъ¸мов, линий связи);
б) неисправности элементов маслосистемы:
–неисправность, засорение маслофильтров;
–негерметичность масляных уплотнений
èтрубопроводов;
–неисправность маслоагрегатов (маслонасосов, маслобака, воздухоотделителей, теплообменников);
в) неисправности деталей и узлов двигателя, омываемых маслом:
–неисправность подшипников опор роторов
ÃÒÄ;
–неисправность лабиринтных уплотнений опор ГТД;
–неисправность деталей коробки приводов
èцентрального привода;
г) неисправности двигателя, влияющие на параметры маслосистемы, например, чрезмерный нагрев горячими газами из газовоздушного тракта деталей, омываемых маслом, вследствие неисправности деталей газовоздушного тракта или системы перепуска воздуха;
д) неисправности приводных агрегатов, вклю- ч¸нных в маслосистему ГТД (электрогенераторы, гидронасосы и т.д.).
12.3.3.2 - Диагностирование по параметрам маслосистемы
Требования к перечню измеряемых параметров
Поскольку параметры маслосистемы не уча- ствуют в регулировании ГТД, то решение об измерении того или иного параметра принимается в зависимости от требований к контролю технического состояния ГТД и требований соответствующих нормативных документов.
Действующий стандарт [12.3.9.8] устанавливает минимальный перечень измеряемых параметров маслосистемы ГТД для самол¸тов:
–давление масла на входе в двигатель;
–температура масла на входе в двигатель;
–количество масла в баке;
–максимальный перепад давления на масляном фильтре;
–стружка в масле.
Для увеличения контролепригодности ГТД используют следующие измерения:
–температура масла на выходе из двигателя (из опор подшипников и коробки приводов),
–давление в полости суфлирования. Раздельное измерение температуры масла в ма-
гистралях откачки от опор подшипников позволяет существенно упростить процесс поиска неисправности и увеличить количество выявляемых неисправностей.
Электрические сигналы от датчиков и сигнализаторов маслосистемы преобразуются в цифровой вид, обрабатываются в САУ ГТД, затем поступают
âинформационную систему самол¸та и записываются бортовым регистратором параметров.
Алгоритмы диагностирования по параметрам маслосистемы
Диагностирование параметров маслосистемы может осуществляться бортовыми и наземными средствами контроля по измеренным значениям параметров, по значениям параметров, приведенным к стандартным атмосферным условиям и к режиму.
Во время пол¸та воздушного судна применяется оперативный контроль, который предназначен для выявления быстроразвивающихся неисправностей и принятия решения о дальнейших действиях экипажем во время пол¸та. Оперативный контроль параметров маслосистемы осуществляется
âпроцессе работы ГТД, как правило, средствами бортовой системы контроля и визуально экипажем по отображаемым в кабине самол¸та параметрам. При оперативном контроле измеренные значения параметров сравниваются c предельно допустимыми значениями, и при выходе за допуск система кон-
765

Глава 12 - Системы ГТД
троля ГТД выда¸т соответствующий сигнал в информационную систему самол¸та.
Для выявления неисправностей ГТД на ранней стадии их развития существуют наземные комплексы диагностирования параметров ГТД, включающие диагностирование по параметрам маслосистемы. Такие системы отслеживают изменение параметров каждого ГТД в отдельности, как в те- чение каждого цикла (пол¸та), так и за весь период его эксплуатации. Такой подход является более тонким инструментом для оценки параметров и диагностирования ГТД, так как каждый конкретный экземпляр двигателя обладает своими характерными особенностями, которые не всегда возможно учитывать при оперативном контроле.
Для оценки изменения параметров двигателя в течение всего периода его эксплуатации, как правило, применяется многопол¸тный контроль параметров, при котором анализируется их изменение по мере увеличения наработки двигателя. Поскольку значения параметров маслосистемы зависят от ряда факторов, корректное сравнение их возможно только после приведения к стандартным условиям с учетом режима работы ГТД и внешних условий. Приведение параметров маслосистемы производится по температуре воздуха на входе в двигатель, по частоте вращения ротора ГТД, по температуре топлива (если масло охлаждается топливом), по давлению масла на входе в двигатель по эмпирическим формулам. Для уменьшения погрешности оценки параметров для многопол¸тного контроля целесообразно использовать установившиеся режимы работы маслосистемы. Такими режимами могут быть: режим малого газа, режим, на котором выполняется взл¸т, режим набора высоты, крейсерский режим пол¸та. При многопол¸тном анализе оценивается величина изменения контролируемого параметра по сравнению с начальным периодом эксплуатации и скорость изменения параметра по наработке за выбранный фиксированный интервал наработки, например, за 10...20 циклов (полетов). Увеличение интервала оценки повышает достоверность оценки при отсутствии неисправностей, но вызывает задержку срабатывания допуска. Рассчитывая скорость изменения параметра можно спрогнозировать, когда он достигнет предельных значений, когда и где следует ожидать появление неисправности. На основании многопол¸тного анализа прогнозируется выработка ресурса парка двигателей, осуществляется планирование закупки запчастей, работ при регламентном обслуживании, ремонта двигателей, внедрение мероприятий по увеличению срока службы двигателей.
Ñувеличением над¸жности, компактности
èпроизводительности компьютеров и с развитием средств связи в последнее время просматриваются тенденции к применению алгоритмов многопо- л¸тного анализа во время пол¸та, как на борту самол¸та, так и с помощью средств телеметрии наземными комплексами.
Используя алгоритмы многопол¸тного анализа параметров маслосистемы можно выявить неисправности ГТД и устранить их до того, когда они войдут в свою критическую стадию, когда может произойти выключение двигателя в пол¸те или его отказ в транзитном аэропорту.
По давлению масла на входе в двигатель можно определить правильность регулировки давления масла, исправность нагнетающего маслонасоса
èдругих элементов маслосистемы (маслофильтров, редукционных клапанов и т.д.), расположенных в нагнетающей магистрали.
По изменению количества масла в баке рас- считывается часовой расход масла в двигателе (безвозвратные потери), характеризующий герметич- ность маслосистемы.
По изменению температуры масла можно оценить изменение теплоотдачи от омываемых маслом деталей ГТД или эффективность работы масляных теплообменников.
По величине перепада давления на маслофильтре определяется момент, когда засор¸н маслофильтр. Сигнализаторы стружки в масле позволяют определить, когда содержание металлических частиц в масле достигает опасного уровня. В слу- чае измерения перепада давления на маслофильтре и количества стружки в масле датчиками появляется возможность контролировать процесс изменения содержания металлической стружки
èкокса в масле во времени, что позволит выявить неисправность на более ранней стадии. Кроме того, в случае поломки сигнализатора она может быть не выявлена, а при использовании датчика его неисправность может быть выявлена при наличии отклонений от нормы.
По величине давления в системе суфлирования можно определить герметичность масляных полостей двигателя, исправность агрегатов, отделяющих воздух от масла.
При экспертном анализе по характеру изменения параметров маслосистемы в комплексе с другими параметрами двигателя можно определить наиболее вероятные неисправности двигателя, что существенно облегчает их обнаружение на ранней стадии развития и поиск визуальными методами.
766
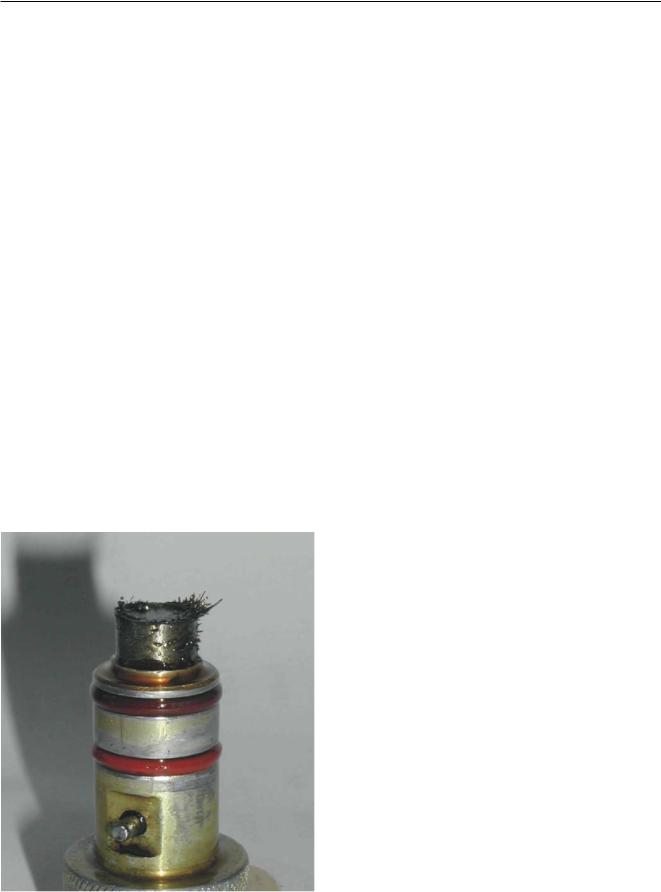
Глава 12 - Системы ГТД
12.3.3.3 - Контроль содержания в масле частиц износа (трибодиагностика)
Методы трибодиагностики
Опыт эксплуатации ГТД в России и в мире свидетельствует о значительном количестве отказов двигателей в связи с выходом из строя смазываемых узлов трения [12.3.9.9]. Это обуславливает важную роль, которую играет трибодиагностика.
Частицы изнашиваемых металлов образуются в результате взаимного перемещения металлических деталей в механических системах, несмотря на наличие смазки. Такое перемещение сопровождается трением и постоянным износом контактирующих поверхностей. Металлические частицы истираемого материала попадают в масляную систему. Следовательно, в масло переходят частицы износа сплавов и покрытий, применяемых для изготовления трущихся деталей и узлов маслосистемы, а также атмосферной пыли. В масле появляется потенциальный источник информации, который непосредственно свидетельствует о состоянии данного узла.
Трибодиагностику, условно, можно разделить на две части – бортовую и лабораторную.
Бортовая трибодиагностика необходима для предупреждения о дефекте узлов трения во время работы двигателя за небольшой период времени до
Рисунок 12.3.3.3_1 – Отложение стружки на магнитной пробке
возникновения опасности их разрушения, т.е. является средством контроля состояния. Лабораторная диагностика предназначена для долгосрочного прогнозирования дефекта и определения его местоположения в двигателе.
В качестве бортовых средств трибодиагностики, в основном, используются магнитные пробки, сигнализаторы стружки в масле и фильтры–сиг- нализаторы. В последнее время все большее применение находят автоматизированные системы предупреждения аварийного износа, основанные на различных физических принципах.
При лабораторной трибодиагностике проводится спектральный анализ проб масла, феррографический анализ, гранулометрический анализ, а так же определение марки материала продуктов износа - стружки. В процессе спектрального анализа определяются концентрации в масле металлов, из которых состоят частицы износа. Как правило, определяется содержание железа и меди, реже серебра. Современные приборы для спектрального анализа позволяют контролировать более 20 элементов. При феррографическом анализе определяются размеры, форма и количество крупных частиц в масле, по которым можно составить картину характера повреждения трущихся поверхностей. При гранулометрическом анализе определяется общая загрязненность масла любыми частицами с определением их размеров и количества и соответствие нормируемому классу чистоты масла по ГОСТ 17216-2001.
Бортовые средства обнаружения частиц износа
а) Простейшим приспособлением для выявления износа стальных (ферромагнитных) деталей является магнитная пробка (МП), которая устанавливается в трубопроводах и полостях двигателя, по которым циркулирует масло [12.3.9.10]. Осмотр МП выполняется при ТО на земле с периодичностью, предусмотренной регламентом. Недостатком МП является невозможность выявления стружки в промежутке между осмотрами. Пример отложения стружки на МП приведен на Рис. 12.3.3.3_1
б) Для контроля наличия стружки в маслосистеме в полете используются электрические детекторы. При накоплении определенного количества продуктов износа происходит замыкание контактов и формирование предупреждающего сигнала на приборную панель экипажу или записывающее устройство.
Одним из примеров конструкции детектора является магнитный сигнализатор стружки (МСС). При замыкании стружкой пространства, разделенного диэлектриком, выдается сигнал.
767

Глава 12 - Системы ГТД
Недостатками МСС являются:
-возможность контроля только магнитных материалов
-выдача сигнала при замыкании контактов единичной крупной частицей, не являющейся продуктом износа трущихся поверхностей
в) Для контроля в маслосистеме наличия любых частиц и сигнализации об их наличии при работе двигателя используется фильтр–сигнализатор (ФС).
На извлекаемой при ТО вставке на сетке 1 ФС отлагаются как металлические частицы, так
èпродукты температурного разложения масла – кокс (см. Рис. 12.3.3.3_2). Сигнал о наличии продуктов износа в маслосистеме формируется при замыкании зазора между изолированными секциями 2 ФС.
Рисунок 12.3.3.3_2 – Вставка фильтра–сигнализа- тора 1 – сетка; 2 - секции
На вставке ФС могут быть выявлены, помимо железистых частиц, частицы цветных сплавов, меди, алюминия, серебра, магния и т.д. Это позволяет сделать предварительный вывод о повреждении детали. Пример отложения стружки на ФС приведен на Рис. 12.3.3.3_3.
г) Опыт ведущих фирм-изготовителей ГТД показывает, что наиболее перспективным является автоматизированный контроль количества и размеров частиц износа, вымываемых с трущихся поверхностей узлов непосредственно во время их работы. Одной из удачных разработок, нашедших практическое применение является система контроля количества стружки QDM (Quantitative Debzis Monitoring) с магнитно–индукционным датчиком, выпускаемая фирмой Vickers (США). Система устанавливается на двигатели Rolls-Royse RB 211
èГТД для газокомпрессорных станций AVON
èPhase 2.
Лабораторные способы обнаружения частиц износа
При эксплуатации авиационных двигателей широко применяется спектральный анализ проб масла, отобранных из маслосистемы двигателя путем контроля концентрации в масле металлов и других примесей в граммах на тонну. В большинстве слу- чаев производится мониторинг концентрации железа и меди. Пробы масла берутся через 15…40 минут после остановки двигателя, пока частицы износа находятся во взвешенном состоянии. Периодичность отборов устанавливается в зависимости от прогнозируемой интенсивности износа и трудоемкости технического обслуживания, как правило, не реже чем через 200 часов полета. При возрастании содержания продуктов износа в масле отбор проб производится чаще.
Рисунок 12.3.3.3_3 – Отложение стружки на фильтре–сигнализаторе (слева - на секциях, справа - на сетке)
768
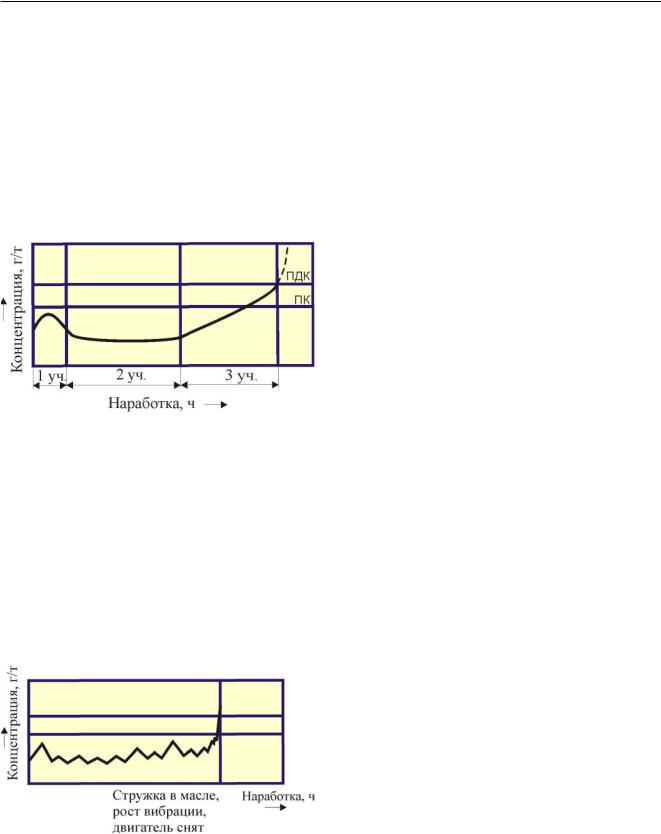
Глава 12 - Системы ГТД
Нормальная кривая закона изменения содержания металла приведена на Рис. 12.3.3.3_4.
1 участок – период приработки узлов двигателя. На графике наблюдается первоначально рост, а затем уменьшение содержания металлов в конце приработки до величины, характеризующей нормальное содержание металлов. Имеет место индивидуальное для каждого двигателя значение концентрации металла в допустимых пределах, зависящее от режимов работы двигателя (от времени работы на различных режимах).
Рисунок 12.3.3.3_4 - Нормальный закон изменения содержания металлов в масле в процессе наработки двигателя ПК – повышенная концентрация, при достижении которой двигатель допускается эксплуатировать «особым контролем» ПДК – предельно-допустимая
концентрация, при достижении которой двигатель подлежит отстранению от эксплуатации
Рисунок 12.3.3.3_5 - Изменение содержания металлов в масле при усталостном повреждении трущихся поверхностей
2 участок – период нормального изнашивания. Может иметь место медленный рост концентрации металла по мере увеличения наработки двигателя.
3 участок – период интенсивного изнашивания. Этот период предшествует разрушению какого – либо узла двигателя (либо связан с частичным разрушением). Интенсивность увеличения концентрации выше, чем на участке 2.
Нормальный закон изменения содержания металлов в масле реализуется только если в двигателе происходит процесс истирания трущихся поверхностей с выделением в масло частиц износа не более 15…30 мкм – размер, который способны учесть большинство современных приборов (как эмиссионнных, так и ренгеновских).
Одним из самых распространенных и опасных видов износа является питтинг – усталостное выкрашивание контактных поверхностей. Началом процесса питтинга является пластическая деформация поверхности и образование на поверхностях трения усталостных микротрещин. Вплоть до появления первой каверны усталостного выкрашивания единственным видом образующихся частиц износа, попадающих в масло, являются сферические частицы размером 3…5 мкм, весовой вклад которых в общую массу образовавшихся при нормальном износе частиц составляет несколько процентов, что соизмеримо с ошибкой измерения спектрометров.
При дальнейшем износе выделяются крупные частицы, не учитываемые при спектральном анализе до тех пор пока не произойдет значительное повреждение с выделением большого количества, как крупных, так и мелких частиц. Изменение содержания металлов в масле при усталостном повреждении деталей приведены на Рис. 12.3.3.3_5.
Имеются технологии спектрального анализа, при котором учитываются все частицы в пробе. Это обеспечивается за счет растворения продуктов износа в растворе кислот и последующего анализа на специальном спектрометре. Значительного распространения этот метод не получил из-за большой трудоемкости и дорогостоящего оборудования.
В настоящее время авиакомпании приобретают новое поколение спектрометров, определяющих 10…15 металлов, что позволяет контролировать повреждения деталей из цветных сплавов, анализировать концентрацию легирующих элементов сталей и сплавов, и тем самым локализовать возможное повреждение.
Для выявления процессов усталостного повреждения применяется феррографический анализ. Как правило используют часть пробы масла для спектрального анализа. Феррограмма исследуется
769
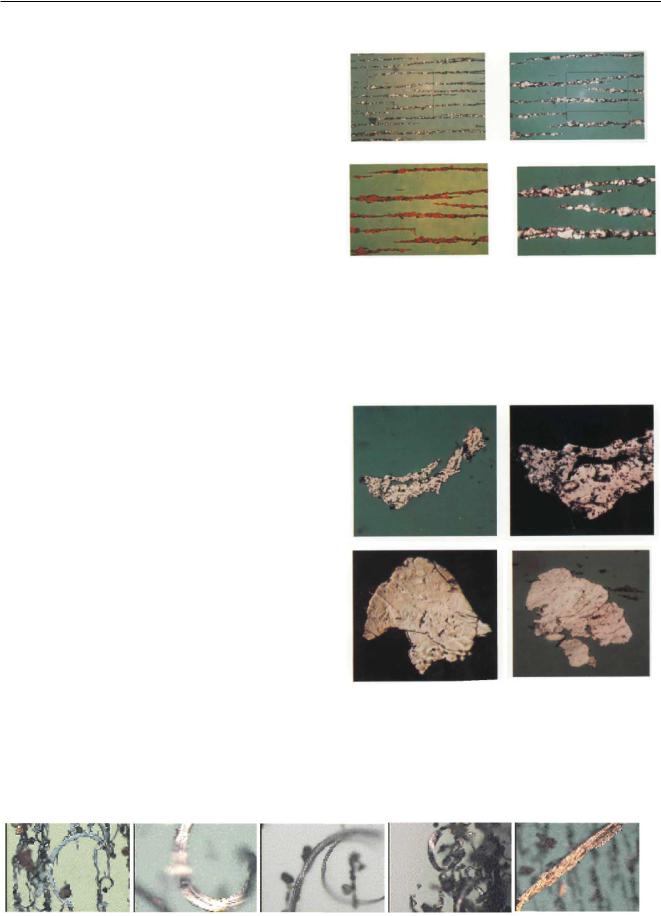
Глава 12 - Системы ГТД
под микроскопом где определяются формы, размеры и количество частиц.
По виду частиц, форме и соотношения размеров, путем сравнения с атласом частиц определяются следующие виды износа [12.3.9.11]:
1. Нормальное изнашивание Частицы, образующиеся при скольжении и име-
ющие форму плоских пластин. Размеры частиц 0,5…15 мкм и менее, толщина частиц 0,15…1 мкм. Отношение большего размера частиц к их толщине колеблется от 10 : 1 для более крупных частиц до 3 : 1 для частиц с размерами около 0,5 мкм. Микрофотографии частиц износа при нормальном изнашивании приведены на Рис. 12.3.3.3_6.
2. Усталостное выкрашивание Частицы усталостного выкрашивания име-
ют форму плоских хлопьевидных пластин с гладкой поверхностью и хаотичную, беспорядочной формы периферию. Размеры частиц 10…100 мкм и более, отношение большего размера к их толщине 10 : 1. При данном виде износа встречаются как ферромагнитные частицы, так и не ферромагнитные. Микрофотографии частиц износа при усталостном выкрашивании приведены на Рис. 12.3.3.3_7.
3. Микрорезание Частицы изнашивания микронеровностей в ви-
де стружки длиной 25…100 мкм и толщиной 2…5 мкм. Частицы абразивного изнашивания в виде кусочков проволочек длиной от 5 мкм и толщиной от 0,25 мкм. Микрофотографии частиц износа при микрорезании приведены на Рис. 12.3.3.3_8.
4. Задир Частицы, образующиеся при усиленном про-
скальзывании одной детали относительно другой с бороздками на поверхности и выступающими прямыми краями. Размеры частиц от 15 мкм, отношение основного размера к толщине частиц составляет 10 : 1. Микрофотографии частиц износа при задире приведены на Рис. 12.3.3.3_9.
При образовании усталостных микротрещин в подшипниках качения заметного роста содержания металлов не происходит, однако возникающий
Рисунок 12.3.3.3_6 - Микрофотографии частиц износа при нормальном изнашивании Увеличение: 500х
Рисунок 12.3.3.3_7 - Микрофотографии частиц износа при усталостном выкрашивании Увеличение: 500х
Рисунок 12.3.3.3_8 - Микрофотографии частиц износа при микрорезании.Увеличение: 500х
770
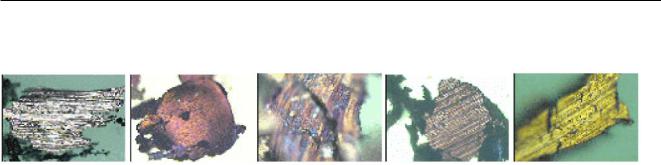
Глава 12 - Системы ГТД
Рисунок 12.3.3.3_9 - Микрофотографии частиц износа при задире. Увеличение: 500х
после достаточного их развития питтинг приводит к поломке. Усталостные трещины обнаруживаются на зубьях шестерен, которые не вызывают какого – либо заметного повышения содержания металлов масле до тех пор, пока зуб не сломается.
Появление в масле сферических частиц может служить диагностическим признаком образования усталостных микротрещин не только в подшипниках качения, но и в зубчатых зацеплениях. При этом сферические частицы, характерные для образования усталостных микротрещин в зубчатых зацеплениях имеют размеры до 20 мкм (для подшипников качения характерен размер сферических частиц 3…5 мкм).
В ряде случаев может быть использован анализ отложений с фильтров маслосистемы. Предварительно производится смыв отложений с использованием ультразвуковых приспособлений,
èфильтрация осадка. Осадок направляется в лабораторию на исследование.
Все шире внедряется определение марки стали (сплава) стружки снятой с МП, МСС, ФС, смывок с фильтров. Знание конкретной марки стали
èместа, где выявлена стружка, позволяет локализовать поврежденный узел и принять оптимальное решение по возможности ремонта двигателя в условиях эксплуатации (путем замены агрегата, модуля) или направление двигателя в ремонт. В ряде случаев выявляются посторонние частицы не являющиеся продуктами износа двигателя, что позволяет после промывки маслосистемы допустить двигатель к продолжению эксплуатации.
Аппаратное обеспечение трибодиагностики
Аппаратура для проведения атомно-эмиссион- ного спектрального анализа смазочных масел.
Для измерения концентрации элементов в смазочном масле используются установки типа МФС (многоканальный фотоэлектрический спектрометр) различных модификаций. Принцип действия всех установок одинаков [12.3.9.12]. Они различаются только способом подачи пробы в источник возбуждения
спектров (дуговой разряд) и аппаратурным оформлением.
Аналогичный принцип действия лежит в основе зарубежных спектрометров с дуговым возбуждением спектров (МОА фирмы Baird, D2R2 фирмы Spectro).
1. Рентгенофлуоресцентная аппаратура
Âпоследнее время в эксплуатации все больше внедряется оборудование, которое отличаются от предшествующего поколения приборов только современной элементной базой и автоматизированным способом обработки поступающей информации [12.3.9.13]. Рентгенофлуоресцентная аппаратура делится на две большие группы по способу разложения в спектр и детектирования флуоресцентного излучения. Процесс анализа на современных рентгеновских флуоресцентных спектрометрах полностью автоматизирован.
à) Кристалл–дифракционная аппаратура (или аппаратура с волновой дисперсией) использует кристалл - анализаторы, обеспечивающие весьма высокое спектральное разрешение по длинам волн. Разложение флуоресцентного излучения в спектр происходит в детекторе и основано на использовании закона Вульфа-Бреггов для монокристаллов.
Кристалл-дифракционная аппаратура представлена, как правило, стационарными установками, использующими мощное первичное излу- чение рентгеновских трубок. Промышленные кристалл-дифракционные спектрометры являются, как правило, многоканальными, имеющими набор жестко фиксированных спектрометрических каналов, настроенных на регистрацию флуоресценции отдельных элементов. Они используются обычно в промышленных лабораториях для определения элементного состава сталей, сплавов, горных пород, цементов, руд, продуктов обогащения и т.д.
Âисследовательских лабораториях, когда набор определяемых элементов заранее неизвестен и требования к экспрессности не так вели-
771

Глава 12 - Системы ГТД
ко, предпочтительнее одноканальные рентгеновские спектрометры, легко настраиваемые на регистрацию флуоресцентного излучения любого элемента.
á) Бездифракционная аппаратура (или аппаратура с энергетической дисперсией) использует энергодисперсионные детекторы рентгеновского излучения. Остальные элементы рентгенофлуоресцентного спектрометра одинаковы для кристаллдифракционной и бездифракционной аппаратуры.
Бездифракционная аппаратура отличается высокой светосилой, сравнительно малыми габаритами, небольшим энергопотреблением и невысокой стоимостью. Важным достоинством этой аппаратуры является возможность получить информацию об интенсивностях почти всех формирующих пробу элементов за одну экспозицию.
Âконструкции двигателя используются сплавы, в частности, стали, концентрация легирующих добавок в которых в 10…100 раз меньше концентрации железа. Так, в стали ЭИ-347-Ш, из которой изготавливаются подшипники, концентрация железа составляет около 85%, вольфрама – 10%, никеля - менее 1%, на другие элементы приходится ~ 4%.
Âслучае развития дефекта при достижении концентрации железа 4 г/т (концентрация, при которой двигатель снимают с эксплуатации) содержание вольфрама и никеля составит ~ 0,4 г/т
è0,01 г/т соответственно. То есть, значения концентраций W и Ni находятся ниже предела обнаружения рентгеноспектральных приборов. Это зна- чит, что концентрация легирующих компонентов не может быть измерена и, соответственно, не может быть обнаружен дефект. Очевидно, что концентрация легирующих элементов будет достаточ- на для измерения в случае чрезмерного увеличения содержания железа.
Приведенный пример показывает, что при использовании диагностической спектральной аппаратуры и существующем методическом обеспечении для двигателей, характеризующихся нормальным износом, возможно определение концентрации, в лучшем случае, только основных металлов. Концентрация легирующих элементов может быть уверенно измерена в случае большого содержания элементов основы, т.е. когда двигатель будет находиться в предотказном, либо отказном состоянии. Поэтому недостаточные пределы обнаружения приводят к низкой достоверности результатов и невозможности отслеживания дефектов на ранней стадии развития.
2. Аппаратура для проведения феррографи- ческого анализа
Феррографический способ анализа, в отличие от спектрального, предоставляет значительно больше информации о частицах износа. Данным способом представляется возможным оценить размер, индекс износа (количественная оценка содержания частиц износа), форму и состояние поверхности частиц, которая позволяет идентифицировать вид износа.
Стандартом [12.3.9.14] установлено около двух десятков типов изнашивания. Поэтому для установления граничных значений, при которых двигатель допускается (не допускается) к эксплуатации необходимо точное определение типа. На практике его определение представляет собой достаточно сложную задачу ввиду большого разнообразия типов
èодновременности действия. Информация, которую представляет феррографический анализ по параметрам частиц износа, является не всегда достаточной для адекватной оценки технического состояния двигателя.
Феррографический способ анализа увеличи- вает количество информации об износных частицах по сравнению со спектрометрическими. Главное достоинство феррографии заключается в том, что по форме частиц имеется принципиальная возможность определения типа изнашивания. Однако здесь возникает задача установления граничных значений для принятия решения о техническом состоянии двигателя.
Особенности конструкции ГТД для обеспечения трибодиагностики
На этапе эскизного проектирования нового авиационного двигателя следует предусмотреть места (в том числе и резервные) для установки МП, МСС, ФС. При этом часть мест для МП и МСС временно может быть заглушена, и установка их может выполняться для поиска места повреждения [12.3.9.3].
Часто в маслосистемы авиационных двигателей устанавливают полнопоточные фильтры с одноразовыми фильтроэлементами в нагнетающей
èоткачивающей магистралях. При такой компоновке основная масса частиц износа оседает на этих фильтроэлементах. Поэтому информативность проб масла очень мала. При этом в объеме масла практически не происходит накопления частиц износа. Это положительно сказывается на условиях работы пар трения, но резко снижает информативность проб масла и вероятность своевременного обнаружения начала износа деталей и узлов двигателя. Поэтому места отбора проб масла следует располагать перед фильтрами.
772