
- •Содержание
- •Глава 1 - Общие сведения о газотурбинных двигателях
- •1.1 — Введение
- •1.2.1.2 — Турбовинтовые двигатели и вертолетные ГТД
- •1.2.1.3 — Двухконтурные турбореактивные двигатели (ТРДД)
- •1.2.1.4 — Двигатели для самолетов вертикального взлета и посадки
- •1.2.1.5 - Комбинированные двигатели для больших высот и скоростей полета
- •1.2.1.6 - Вспомогательные авиационные ГТД и СУ
- •1.2.2 - Авиационные СУ
- •1.2.3 - История развития авиационных ГТД
- •1.2.3.1 - Россия
- •1.2.3.2 - Германия
- •1.2.3.3 – Англия
- •1.3 - ГТД наземного и морского применения
- •1.3.1 - Области применения наземных и морских ГТД
- •1.3.1.1 -Механический привод промышленного оборудования
- •1.3.1.2 - Привод электрогенераторов
- •1.3.1.3 - Морское применение
- •1.3.2 - Основные типы наземных и морских ГТД
- •1.3.2.1 - Стационарные ГТД
- •1.3.2.2 - Наземные и морские ГТД, конвертированные из авиадвигателей
- •1.3.2.3 - Микротурбины
- •1.4 - Основные мировые производители ГТД
- •1.4.1 - Основные зарубежные производители ГТД
- •1.4.2 - Основные российские производители ГТД
- •1.6 - Перечень использованной литературы
- •Глава 2 - Основные параметры и требования к ГТД
- •2.1 - Основы рабочего процесса ГТД
- •2.1.1 - ГТД как тепловая машина
- •2.1.1.1 – Простой газотурбинный цикл
- •2.1.1.2 - Применение сложных циклов в ГТД
- •2.1.2 - Авиационный ГТД как движитель
- •2.1.3 - Полный к.п.д. и топливная эффективность (экономичность) ГТД
- •2.2 - Параметры ГТД
- •2.2.1 - Основные параметры авиационных ГТД
- •2.2.2 - Основные параметры наземных и морских приводных ГТД
- •2.3 - Требования к авиационным ГТД
- •2.3.1 - Требования к тяге (мощности)
- •2.3.2 – Требования к габаритным и массовым характеристикам
- •2.3.3 - Возможность развития ГТД по тяге (мощности)
- •2.3.4 - Требования к используемым горюче-смазочным материалам
- •2.3.4.1 - Топлива авиационных ГТД
- •2.3.4.2 – Авиационные масла
- •2.3.4.3 - Авиационные гидравлические жидкости
- •2.3.5 – Надежность авиационных ГТД
- •2.3.5.1 – Основные показатели
- •2.3.5.1.1 – Показатели безотказности, непосредственно влияющие на безопасность работы двигателя
- •2.3.5.2 – Методология обеспечения надежности
- •2.3.5.2.1 – Этап проектирования
- •2.3.6 - Ресурс авиационных ГТД
- •2.3.6.1 - Методология обеспечения ресурса
- •2.3.6.2 - Количественные показатели ресурса
- •2.3.7 - Требования производственной технологичности
- •2.3.8 - Требования эксплуатационной технологичности
- •2.3.8.1 - Эксплуатационная технологичность - показатель совершенства ГТД
- •2.3.8.2 - Основные качественные характеристики ЭТ
- •2.3.8.3 - Количественные показатели ЭТ
- •2.3.9 - Экономические требования к авиационным ГТД
- •2.3.9.1 - Себестоимость производства
- •2.3.9.2 - Стоимость ЖЦ двигателя
- •2.3.10 - Экологические требования
- •2.3.10.2 - Ограничения по шуму
- •2.3.12 - Соответствие требованиям летной годности
- •2.4 - Особенности требований к ГТД наземного применения
- •2.4.1 - Особенности требований к приводным ГТД для ГПА
- •2.4.1.1 - Требования к характеристикам ГТД
- •2.4.1.2 - Требования к ресурсам и надежности
- •2.4.1.4 - Используемые ГСМ
- •2.4.1.5 - Требования экологии и безопасности
- •2.4.1.6 - Требования производственной и эксплуатационной технологичности
- •2.4.2 - Особенности требований к ГТД энергетических установок
- •2.4.2.1 - Требования к характеристикам ГТД
- •2.4.2.2 - Используемые ГСМ
- •2.4.2.3 - Требования к ресурсам и надежности
- •2.4.2.4 - Требования к экологии и безопасности
- •2.4.2.5 - Требования к контролепригодности, ремонтопригодности и др.
- •2.5 - Методология проектирования
- •2.5.1 - Основные этапы проектирования ГТД
- •2.5.1.1 - Техническое задание
- •2.5.1.2 – Техническое предложение
- •2.5.1.3 – Эскизный проект
- •2.5.1.4 – Технический проект
- •2.5.1.5 – Разработка конструкторской документации
- •2.5.2 - Разработка конструкций ГТД на основе базовых газогенераторов
- •2.5.2.1 - Газогенератор – базовый узел ГТД
- •2.5.2.2 – Основные параметры и конструктивные схемы газогенераторов ГТД
- •2.5.2.3 – Создание ГТД различного назначения на базе единого газогенератора
- •2.6.1.1 — Общие положения по авиационным ГТД
- •2.6.1.2 — Общие положения по сертификации наземной техники
- •2.6.1.3 — Общие положения по сертификации производства и СМК
- •2.6.1.4 — Органы регулирования деятельности
- •2.6.1.4.1 — Авиационная техника
- •2.6.1.4.2 — Органы регулирования деятельности по сертификации производства и СМК
- •2.6.2.1 — Авиационная техника
- •2.6.2.2 — Наземная техника
- •2.6.2.3 Производство и СМК
- •2.6.2.4 — Принятые сокращения и обозначения
- •2.6.3.1 — Основные этапы создания авиационных ГТД
- •2.6.3.2 — Этапы процесса сертификации авиационных ГТД
- •Глава 3 - Конструктивные схемы ГТД
- •3.1 - Конструктивные схемы авиационных ГТД
- •3.1.1 - Турбореактивные двигатели
- •3.1.2 - Двухконтурные турбореактивные двигатели
- •3.1.3 - Турбовинтовые и вертолетные ГТД
- •3.2 - Конструктивные схемы наземных и морских ГТД
- •3.2.1 - Одновальные ГТД
- •3.2.2 - ГТД со свободной силовой турбиной
- •3.2.3 - ГТД со «связанным» КНД
- •3.2.4 - Конструктивные особенности наземных ГТД различного назначения
- •3.2.5 - Конструктивные особенности ГТД сложных циклов
- •3.4 - Перечень использованной литературы
- •Глава 4 - Силовые схемы ГТД
- •4.1 - Усилия, действующие в ГТД
- •4.1.2 - Крутящие моменты от газовых сил
- •Глава 5 - Компрессоры ГТД
- •6.4.4 - Корпуса КС
- •6.4.4.1 - Наружный корпус КС
- •6.4.4.2 - Внутренний корпус КС
- •6.4.4.3 - Разработка конструкции корпусов
- •6.4.5 - Системы зажигания ГТД
- •6.5 - Экспериментальная доводка КС
- •6.6 - Особенности КС двигателей наземного применения
- •6.7 - Перспективы развития камер сгорания ГТД
- •Глава 7 - Форсажные камеры
- •7.1 - Характеристики ФК
- •7.2 - Работа ФК
- •7.3 - Требования к ФК
- •7.4 - Схемы ФК
- •7.4.2 - Вихревые ФК
- •7.4.3 - ФК с аэродинамической стабилизацией
- •7.5 - Основные элементы ФК
- •7.5.1 - Смеситель
- •7.5.2 - Диффузоры
- •7.5.3 - Фронтовые устройства
- •7.5.4 - Корпусы и экраны
- •7.6 - Управление работой ФК
- •7.6.1 - Розжиг ФК
- •7.6.2 - Управление ФК на режимах приемистости и сброса
- •7.6.3 - Управление ФК на стационарных режимах
- •Глава 8 - Турбины ГТД
- •8.2 - Аэродинамическое проектирование турбины
- •8.2.2 - Технология одномерного проектирования турбины
- •8.2.4 - 2D/3D-моделирование невязкого потока в проточной части турбины
- •8.2.5 - 2D/3D-моделирование вязкого потока в турбине
- •8.2.6 - Синтез геометрии профилей и лопаточных венцов
- •8.2.7 - Одномерное проектирование турбины
- •8.2.7.1 - Выбор количества ступеней ТВД
- •8.2.7.2 - Выбор количества ступеней ТНД
- •8.2.7.3 - Аэродинамическое проектирование и к.п.д. турбины
- •8.2.9 - Методы управления пространственным потоком в турбине
- •8.2.10 - Экспериментальное обеспечение аэродинамического проектирования
- •8.2.11 - Перечень использованной литературы
- •8.3 - Охлаждение деталей турбины
- •8.3.1 - Тепловое состояние элементов турбин
- •8.3.1.1 - Принципы охлаждения
- •8.3.2 - Конвективное, пленочное и пористое охлаждение
- •8.3.3 - Гидравлический расчет систем охлаждения
- •8.3.4 - Методология расчета температур основных деталей турбин
- •8.3.5 - Расчет полей температур в лопатках
- •8.3.6 - Перечень использованной литературы
- •8.4 - Роторы турбин
- •8.4.1 - Конструкции роторов
- •8.4.1.1 - Диски турбин
- •8.4.1.2 - Роторы ТВД
- •8.4.1.3 - Роторы ТНД и СТ
- •8.4.1.4 - Примеры доводки и совершенствования роторов
- •8.4.1.5 - Предотвращение раскрутки и разрушения дисков
- •8.4.2 - Рабочие лопатки турбин
- •8.4.2.1 - Соединение рабочих лопаток с диском
- •8.4.3 - Охлаждение рабочих лопаток
- •8.4.4 - Перечень использованной литературы
- •8.5 - Статоры турбин
- •8.5.1 - Корпусы турбин
- •8.5.2 - Сопловые аппараты
- •8.5.3 - Аппараты закрутки
- •8.5.4 – Перечень использованной литературы
- •8.6 - Радиальные зазоры в турбинах
- •8.6.1 - Влияние радиального зазора на к.п.д. турбины
- •8.6.2 - Изменение радиальных зазоров турбины в работе
- •8.6.3 - Управление радиальными зазорами
- •8.6.4 - Выбор радиального зазора при проектировании
- •8.6.5 - Перечень использованной литературы
- •8.7 - Герметизация проточной части
- •8.7.1 - Герметизация ротора и статора от утечек охлаждающего воздуха
- •8.7.2 - Уплотнения между ротором и статором
- •8.7.3 - Перечень использованной литературы
- •8.8 - Материалы основных деталей турбины
- •8.8.1 - Диски и роторные детали турбины
- •8.8.2 - Сопловые и рабочие лопатки
- •8.8.3 - Покрытия лопаток
- •8.8.4 - Корпусы турбин
- •8.9.1 - Перечень использованной литературы
- •8.10.1 - Прогары и трещины лопаток ТВД
- •8.10.3 - Недостаточный циклический ресурс и поломки роторных деталей
- •8.10.4 - Устранение дефектов турбины в ходе доводки
- •8.11 - Перспективы развития конструкций и методов проектирования турбин
- •8.11.1 - 2D-аэродинамика: эффективные охлаждаемые лопатки ТВД
- •8.11.2 - 2D-аэродинамика: сокращение количества лопаток
- •8.11.3 - Противоположное вращение роторов ТВД и ТНД
- •8.11.4 - 2D-аэродинамика: эффективные решетки профилей ТНД
- •8.11.5 - 3D-аэродинамика: эффективные формы лопаточных венцов
- •8.11.6 - Новые материалы и покрытия для лопаток и дисков
- •8.11.7 - Совершенствование конструкций охлаждаемых лопаток
- •8.11.8 - Оптимизированные системы управления радиальными зазорами
- •8.11.9 - Развитие средств и методов проектирования
- •Глава 9 - Выходные устройства ГТД
- •9.1 - Нерегулируемые сопла
- •9.2 - Выходные устройства ТРДД
- •9.2.1 - Выходные устройства со смешением потоков
- •9.2.2 - Выходные устройства ТРДД с раздельным истечением потоков
- •9.3 - Регулируемые сопла
- •9.3.1 - Осесимметричные регулируемые сопла
- •9.3.1.1 - Регулируемое сопло двигателя Д30-Ф6
- •9.3.2 - Плоские сопла
- •9.4 - Выходные устройства двигателей самолетов укороченного и вертикального взлета-посадки
- •9.5 - «Малозаметные» выходные устройства
- •9.6 - Реверсивные устройства
- •9.6.1 - Реверсивные устройства ковшового типа
- •9.6.2 - Реверсивные устройства створчатого типа
- •9.6.3.1 - Гидравлический привод реверсивного устройства
- •9.6.3.3 - Механический замок фиксации положения реверсивного устройства
- •9.7 - Приводы выходных устройств
- •9.7.1 - Пневмопривод
- •9.7.2 - Пневмомеханический привод
- •9.8 - Выходные устройства диффузорного типа
- •9.8.1 - Конические диффузоры
- •9.8.2 - Осекольцевые диффузоры
- •9.8.3 - Улитки
- •9.8.4 - Соединения с выхлопными шахтами
- •9.8.5 - Выходные устройства вертолетных ГТД
- •9.12 - Перечень использованной литературы
- •Глава 10 - Привод агрегатов, редукторы, муфты ГТД
- •10.1 - Привод агрегатов ГТД
- •10.1.1 - Центральный привод
- •10.1.2 - Коробки приводов агрегатов
- •10.2 - Редукторы ГТД
- •10.2.1 - Редукторы ТВД
- •10.2.1.1 - Общие требования, кинематические схемы
- •10.2.1.2 - Конструкция редукторов ТВД
- •10.2.2 - Редукторы привода несущего и рулевого винтов вертолетов
- •10.2.2.1 - Редукторы привода несущего винта
- •10.2.2.1.1 - Кинематические схемы главных редукторов вертолетов
- •10.2.2.1.2 - Конструкция главных редукторов вертолетов
- •10.2.2.2 - Редукторы хвостовые и промежуточные
- •10.2.3 - Редукторы ГТУ
- •10.2.3.1 - Конструкция редукторов
- •10.3 - Муфты приводов ГТД и ГТУ
- •10.3.1 - Требования к муфтам
- •10.3.2 - Конструкция муфт
- •10.4 - Проектирование приводов агрегатов ГТД
- •10.4.1 - Проектирование центрального привода
- •10.4.1.1 - Конструкция центрального привода
- •10.4.2 - Проектирование коробок приводов агрегатов
- •10.4.2.1 - Конструкция коробки приводов агрегатов
- •10. 5 - Проектирование редукторов
- •10.5.1 - Особенности проектирования редукторов ТВД
- •10.5.2 - Особенности проектирования вертолетных редукторов
- •10.5.3 - Особенности проектирования редукторов ГТУ
- •10.6.1 - Требования к зубчатым передачам
- •10.6.2 - Классификация зубчатых передач
- •10.6.3 - Исходный производящий контур
- •10.6.4 - Нагруженность зубчатых передач
- •10.6.5 - Конструктивные параметры зубчатых передач
- •10.6.5.1 - Конструкции зубчатых колес
- •10.6.6 - Материалы зубчатых колес, способы упрочнения
- •Глава 11 - Пусковые устройства
- •11.1 - Общие сведения
- •11.1.1 - Основные типы пусковых устройств современных ГТД
- •11.1.2 - Технические характеристики пусковых устройств современных ГТД
- •11.2 - Электрические пусковые устройства ГТД
- •11.3 - Воздушные пусковые устройства ГТД
- •11.3.1 - Воздушно - турбинные пусковые устройства ГТД
- •11.3.2 - Регулирующие и отсечные воздушные заслонки
- •11.3.3 - Струйное пусковое устройство ГТД
- •11.4 - Турбокомпрессорные пусковые устройства ГТД
- •11.4.1 - Классификация ТКС ГТД
- •11.4.2 - Принцип действия ТКС
- •11.4.3 - Одновальный ТКС
- •11.4.4 - ТКС со свободной турбиной
- •11.4.5 - Особенности систем ТКС
- •11.5 - Гидравлические пусковые устройства ГТД
- •11.5.1 - Конструкция гидравлических стартеров
- •11.6 - Особенности пусковых устройств ГТД наземного применения
- •11.6.1 - Электрические пусковые устройства
- •11.6.2 - Газовые пусковые устройства
- •11.6.3 - Гидравлические пусковые устройства
- •11.7 - Редукторы пусковых устройств
- •11.8 - Муфты свободного хода пусковых устройств
- •11.8.1 - Муфты свободного хода роликового типа
- •11.8.2 – Муфты свободного хода храпового типа
- •11.9 – Системы смазки пусковых устройств
- •11.11 - Перечень используемой литературы
- •Глава 12 - Системы ГТД
- •12.1.1 - Системы автоматического управления и контроля авиационных ГТД
- •12.1.1.1 - Назначение САУ
- •12.1.1.2 - Состав САУ
- •12.1.1.3 - Основные характеристики САУ
- •12.1.1.5.2 - Порядок разработки САУ
- •12.1.1.5.3 - Основные принципы выбора варианта САУ в процессе проектирования
- •12.1.1.5.4 - Структурное построение САУ
- •12.1.1.5.5 - Программы управления ГТД
- •12.1.1.5.6 - Расчет и анализ показателей надежности
- •12.1.2 - САУ наземных ГТУ
- •12.1.2.1 - Назначение САУ
- •12.1.2.2 - Выбор САУ ГТУ и ее элементов
- •12.1.2.3 - Состав САУ ГТУ
- •12.1.2.4 - Основные характеристики САУ
- •12.1.2.5 - Работа САУ ГТУ
- •12.1.2.6 - Блок управления двигателем (БУД)
- •12.1.2.7 - Особенности системы контроля и диагностики наземных ГТД
- •12.1.4 – Перечень использованной литературы
- •12.2 - Топливные системы ГТД
- •12.2.1 - Топливные системы авиационных ГТД
- •12.2.1.1 - Назначение топливной системы
- •12.2.1.2 - Состав топливной системы
- •12.2.1.3 - Основные характеристики топливной системы
- •12.2.1.4 - Работа топливной системы
- •12.2.1.5 - Выбор топливной системы и ее элементов
- •12.2.1.5.1 – Выбор топливной системы
- •12.2.1.5.2 - Выбор насосов топливной системы
- •12.2.1.5.3 - Определение подогревов топлива в топливной системе
- •12.2.1.5.5 - Математическая модель топливной системы
- •12.2.1.6 - Гидроцилиндры
- •12.2.1.7 - Топливные фильтры
- •12.2.2 - Особенности топливных систем ГТУ
- •12.2.2.1 - Назначение топливной системы
- •12.2.2.2 - Выбор топливной системы и ее элементов
- •12.2.2.3 - Основные характеристики топливной системы
- •12.2.2.4 - Работа топливной системы
- •12.2.4 – Перечень использованной литературы
- •12.3 - Системы диагностики
- •12.3.1 - Общие вопросы диагностирования
- •12.3.1.1 - Задачи диагностирования ГТД
- •12.3.1.3 - Диагностируемые системы ГТД
- •12.3.1.4 - Виды наземного и бортового диагностирования ГТД
- •12.3.1.5 - Структура систем диагностики
- •12.3.1.6 - Регламент диагностирования ГТД
- •12.3.1.7 - Регистрация параметров ГТД
- •12.3.2 - Диагностирование системы механизации ГТД, САУ и ТП ГТД
- •12.3.3 - Диагностирование работы маслосистемы и состояния узлов ГТД, работающих в масле
- •12.3.3.1 - Неисправности маслосистемы и узлов ГТД, работающих в масле
- •12.3.3.2 - Диагностирование по параметрам маслосистемы
- •12.3.3.3 - Контроль содержания в масле частиц износа (трибодиагностика)
- •12.3.4 - Контроль и диагностика по параметрам вибрации ГТД
- •12.3.4.1 - Параметры вибрации и единицы изменения
- •12.3.4.2 - Статистические характеристики вибрации
- •12.3.4.3 - Причины возникновения вибрации в ГТД
- •12.3.4.4 - Датчики измерения вибрации
- •12.3.4.5 - Вибрационная диагностика ГТД
- •12.3.5 - Диагностирование ГТД по газодинамическим параметрам
- •12.3.5.1 - Неисправности проточной части ГТД
- •12.3.5.2 - Требования к перечню контролируемых параметров
- •12.3.5.3 - Алгоритмы диагностирования проточной части ГТД
- •12.3.6 - Обеспечение диагностирования ГТД инструментальными методами
- •12.3.6.1 - Виды неисправностей, выявляемых инструментальными методами
- •12.3.6.2 - Методы и аппаратура инструментальной диагностики
- •12.3.6.2.1 - Оптический осмотр проточной части ГТД
- •12.3.6.2.2 - Ультразвуковой метод диагностирования
- •12.3.6.2.3 - Вихретоковый метод диагностирования
- •12.3.6.2.4 - Капиллярный метод диагностирования с применением портативных аэрозольных наборов
- •12.3.6.2.5 - Диагностирование состояния проточной части ГТД перспективными методами
- •12.3.7 - Особенности диагностирования технического состояния ГТД наземного применения на базе авиационных двигателей
- •12.3.7.1 - Особенности режимов эксплуатации
- •12.3.7.2 - Общие особенности диагностирования наземных ГТД
- •12.3.7.3 - Особенности диагностирования маслосистемы
- •12.3.7.5 - Особенности диагностирования проточной части
- •12.4 - Пусковые системы
- •12.4.1 - Пусковые системы авиационных ГТД
- •12.4.1.1 - Назначение
- •12.4.1.2 - Общие требования
- •12.4.1.3 - Состав пусковых систем
- •12.4.1.4 - Область эксплуатации двигателя, область запуска
- •12.4.1.6 - Надежность запуска
- •12.4.1.7 - Характеристики запуска
- •12.4.1.8. - Выбор типа и параметров стартера
- •12.4.1.9 - Особенности запуска двигателей двухроторных схем
- •12.4.1.10 - Системы зажигания
- •12.4.1.11 - Обеспечение характеристик запуска на разгоне
- •12.4.1.12 - Регулирование компрессора на пусковых режимах
- •12.4.2 - Особенности пусковых систем наземных ГТУ
- •12.4.4 - Перечень использованной литературы
- •12.5 - Воздушные системы ГТД
- •12.5.1 - Функции ВС
- •12.5.2 - Основные требования к ВС
- •12.5.3 - Общие и локальные ВС ГТД
- •12.5.4 - Работа локальных ВС
- •12.5.4.1 - ВС охлаждения турбин ГТД
- •12.5.4.2 - ВС наддува и охлаждения опор
- •12.5.4.2.1 - Работа ВС наддува и охлаждения опор
- •12.5.4.2.2 - Типы ВС наддува и охлаждения опор
- •12.5.4.2.3 - Построение общей схемы ВС наддува и охлаждения опор
- •12.5.4.3 - Противообледенительная система (ПОС)
- •12.5.4.4 - Система кондиционирования воздуха
- •12.5.4.5 - Система активного управления зазорами
- •12.5.4.6 - Системы внешнего охлаждения ГТД
- •12.5.4.7 - Системы внешнего обогрева ГТД
- •12.5.5 - Подготовка воздуха для ВС ГТД
- •12.5.6 - Особенности ВС наземных ГТУ
- •12.5.7 - Агрегаты ВС
- •12.5.9 - Перечень использованной литературы
- •12.6.1 - Общие требования
- •12.6.2 - Схемы маслосистем ГТД
- •12.6.2.1 - Маслосистема с регулируемым давлением масла
- •12.6.2.2 - Маслосистема с нерегулируемым давлением масла
- •12.6.2.3 - Маслосистемы ГТД промышленного применения
- •12.6.3 - Маслосистемы редукторов
- •12.6.3.1 - Маслосистемы авиационных редукторов
- •12.6.3.2 - Маслосистемы редукторов ГТУ
- •12.6.4 - Особенности проектирование маслосистем
- •12.6.5 - Агрегаты маслосистемы
- •12.6.5.1 - Бак масляный
- •12.6.5.2 - Насосы масляные
- •12.6.5.3 - Теплообменники
- •12.6.5.4 - Фильтры и очистители
- •12.6.5.5 - Воздухоотделители и суфлеры
- •12.6.6 - Перспективы развития маслосистем
- •12.6.8 – Перечень использованной литературы
- •12.7 - Гидравлические системы ГТД
- •12.7.1 - Гидросистемы управления реверсивными устройствами
- •12.7.1.1 - Централизованная гидросистема управления реверсивным устройством
- •12.7.1.2 - Автономная гидросистема управления реверсивным устройством
- •12.7.1.3 - Порядок проектирования гидросистем
- •12.7.3 - Перечень использованной литературы
- •12.8 - Дренажные системы
- •12.8.1 - Назначение и классификация систем
- •12.8.2 - Характеристика объектов дренажа
- •12.8.3 - Основные схемы и принцип действия систем
- •12.8.4 - Основные требования к дренажным системам
- •12.8.5 - Обеспечение работоспособности дренажных систем
- •12.8.6 - Особенности конструкции дренажных баков
- •12.8.8 - Перечень использованной литературы
- •Глава 13 - Обвязка авиационных ГТД
- •13.1 - Общая характеристика обвязки
- •13.2 - Конструкция обвязки
- •13.2.1 - Трубопроводные коммуникации
- •13.2.1.1 - Основные сведения
- •13.2.1.2 - Трубы и патрубки
- •13.2.1.3 - Соединения
- •13.2.1.4 - Компенсирующие устройства
- •13.2.1.5 - Соединительная арматура
- •13.2.1.6 - Узлы крепления
- •13.2.1.7 - Неисправности трубопроводов
- •13.2.2 - Электрические коммуникации
- •13.2.2.1 - Общие сведения
- •13.2.2.2 - Конструкция элементов
- •13.2.2.2.1 - Электрические жгуты
- •13.2.2.2.2 - Электрические провода
- •13.2.2.2.3 - Электрические соединители
- •13.2.2.2.4 - Материалы для изготовления электрических жгутов
- •13.2.3 - Узлы крепления агрегатов и датчиков
- •13.2.4 - Механическая проводка управления
- •13.3 - Проектирование обвязки
- •13.3.1 - Требования к обвязке
- •13.3.2 - Основные принципы и порядок проектирования обвязки
- •13.3.3 - Методы отработки конструкции обвязки
- •13.3.3.1 - Натурное макетирование
- •13.3.3.2 - Электронное макетирование обвязки
- •13.3.5 - Проектирование трубопроводных коммуникаций
- •13.3.6 - Проектирование электрических коммуникаций
- •13.3.6.1 - Требования к электрическим коммуникациям
- •13.3.6.2 - Порядок проектирования электрических коммуникаций
- •13.3.6.3 - Разработка электрических схем
- •13.3.6.4 - Разработка монтажных схем
- •13.3.6.5 - Разработка чертежей электрических жгутов
- •13.6 - Перечень использованной литературы
- •Глава 14 - Динамика и прочность ГТД
- •14.1 - Теоретические основы динамики и прочности ГТД
- •14.1.1 - Напряженное состояние, тензор напряжений
- •14.1.2 - Уравнения равновесия
- •14.1.3 - Перемещения в деформируемом твердом теле. Тензор деформаций
- •14.1.4 - Уравнения совместности деформаций
- •14.1.5 - Обобщенный закон Гука
- •14.1.7 - Плоская задача теории упругости
- •14.1.8 - Пластическая деформация материала. Простое и сложное нагружение
- •14.1.11 - Ползучесть. Релаксация напряжений. Длительная прочность
- •14.1.12 - Усталостное разрушение элементов конструкций
- •14.1.13 - Малоцикловая усталость. Термическая усталость
- •14.1.14 - Накопление повреждений при нестационарном нагружении
- •14.1.15 - Закономерности развития трещин в элементах конструкций
- •14.1.16 - Свободные колебания системы с одной степенью свободы
- •14.1.17 - Вынужденные колебания системы с одной степенью свободы
- •14.1.18 - Колебания системы с вязким сопротивлением. Демпфирование колебаний
- •14.1.19 - Вынужденные колебания системы с одной степенью свободы под действием произвольной периодической возмущающей силы
- •14.1.21 - Колебания системы с распределенной массой
- •14.2 - Статическая прочность и циклическая долговечность лопаток
- •14.2.1 - Нагрузки, действующие на лопатки. Расчетные схемы лопаток
- •14.2.2 - Напряжения растяжения в профильной части рабочей лопатки от центробежных сил
- •14.2.3 - Изгибающие моменты и напряжения изгиба от газодинамических сил
- •14.2.5 - Суммарные напряжения растяжения и изгиба в профильной части лопатки
- •14.2.6 - Температурные напряжения в лопатках
- •14.2.7 - Особенности напряженного состояния широкохордных рабочих лопаток
- •14.2.9 - Расчет соединения рабочих лопаток с дисками
- •14.2.10 - Расчет на прочность антивибрационных (бандажных) полок и удлинительной ножки лопатки
- •14.2.11 - Особенности расчета на прочность лопаток статора
- •14.2.13 - Анализ трехмерных полей напряжений и деформаций в лопатках
- •14.3 - Статическая прочность и циклическая долговечность дисков
- •14.3.1 - Расчетные схемы дисков
- •14.3.2 - Расчет напряжений в диске в плоской оссесимметричной постановке
- •14.3.3 - Общие закономерности напряженного состояния дисков
- •14.3.7 - Подтверждение циклического ресурса дисков на основе концепции допустимых повреждений
- •14.3.8 - Расчет роторов барабанного типа
- •14.3.9 - Расчет дисков радиальных турбомашин
- •14.3.10 - Оптимальное проектирование дисков. Равнопрочный диск
- •14.4 - Колебания и вибрационная прочность лопаток осевых компрессоров и турбин
- •14.4.2 - Приближенный расчет собственных частот колебаний лопаток
- •14.4.3 - Трехмерные модели колебаний лопаток
- •14.4.4 - Влияние конструктивных и эксплуатационных факторов на собственные частоты колебаний лопатки
- •14.4.6 - Автоколебания лопаток
- •14.4.7 - Демпфирование колебаний лопаток
- •14.4.8 - Вынужденные колебания лопаток. Резонансная диаграмма
- •14.4.9 - Математическое моделирование вынужденных колебаний лопаток
- •14.4.10 - Экспериментальное исследование колебаний лопаток
- •14.4.11 - Коэффициент запаса вибрационной прочности лопаток, пути его повышения
- •14.4.12 - Колебания дисков
- •14.5 - Динамика роторов. Вибрация ГТД
- •14.5.1 - Критическая частота вращения ротора. История вопроса
- •14.5.2 - Динамика одномассового ротора. Поступательные перемещения
- •14.5.3 - Динамика одномассового ротора. Угловые перемещения
- •14.5.4 - Динамика одномассового несимметричного ротора
- •14.5.5 - Ротор с распределенными параметрами
- •14.5.6 - Особенности колебаний системы роторов и корпусов
- •14.5.7 - Демпфирование колебаний роторов
- •14.5.7.1 - Конструкция и принцип действия демпферов колебаний роторов
- •14.5.7.2 - Расчет параметров демпфирования
- •14.5.7.3 - Особенности гидромеханики реальных демпферов
- •14.5.8 - Вибрация ГТД
- •14.5.8.1 - Источники возмущающих сил и спектр вибрации
- •14.5.8.3 - Статистические характеристики вибрации
- •14.5.8.4 - Измерение и нормирование вибрации
- •14.6 - Прочность корпусов и подвески двигателя
- •14.6.1 - Силовая схема корпуса. Условия работы силовых корпусов
- •14.6.4 - Устойчивость корпусных деталей
- •14.6.5 - Расчет корпусов на непробиваемость
- •14.6.6 - Расчет элементов подвески
- •14.8 – Перечень использованной литературы
- •Глава 15 - Шум ГТД
- •15.1 - Источники шума ГТД
- •15.3 - Методы оценки акустических характеристик
- •15.4 - Снижение шума ГТД
- •15.4.1 - Методология проектирования систем шумоглушения
- •15.4.2 - Шумоглушение в выходных устройствах авиационных ГТД
- •15.4.3 - Конструкция звукопоглощающих узлов авиационных ГТД
- •15.4.4 – Глушители шума в наземных ГТУ
- •15.4.5 – Конструкция глушителей шума наземных ГТД
- •15.7 – Список использованной литературы
- •Глава 16 - Газотурбинные двигатели как силовой привод
- •16.1 - ГТД в силовом приводе ГТЭС и ГПА
- •16.2 - ГТД в силовых (энергетических) установках кораблей и судов
- •16.3 - ГТД в силовых установках танков
- •16.5 - Компоновка корабельных и судовых ГГТД
- •16.6 - Компоновка ГТД в силовой установке танка
- •16.8 – Перечень использованной литературы
- •Глава 17 - Автоматизация проектирования и поддержки жизненного цикла ГТД
- •17.1 - Проектирование и информационная поддержка жизненного цикла ГТД (идеология CALS)
- •17.2 - Жизненный цикл изделия. Обзор методов проектирования
- •17.3 - Программные средства проектирования
- •17.4 - Аппаратные средства систем проектирования
- •17.5 - PDM-системы: роль и место в организации проектирования
- •17.6 - Организация производства и ERP-системы
- •17.7 - Параллельный инжиниринг. Интеграция эскизного и технического проектирования
- •17.8 - Переход на безбумажную технологию
- •17.10 - ИПИ-технологии и эксплуатация изделий
- •17.11 - ИПИ-технологии и управление качеством
- •17.12 - Анализ и реинжиниринг бизнес-процессов
- •17.13 - Основы трехмерного проектирования
- •17.13.1 - Общие принципы трехмерного проектирования
- •17.13.1.1 - Способы создания геометрических моделей
- •17.13.1.2 - Основные термины объемной геометрической модели
- •17.13.1.3 - Принцип базового тела
- •17.13.1.4 - Основные термины при проектировании геометрической модели детали
- •17.13.2 - Управляющие структуры
- •17.13.3 - Принцип «Мастер-модели»
- •17.13.5 - Моделирование сборок
- •17.15 - Перечень использованной литературы
- •Глава 18 - Уплотнения в ГТД
- •18.1 - Уплотнение неподвижных соединений
- •18.2 - Уплотнения подвижных соединений
- •18.2.1 - Гидравлический расчет уплотнений подвижных соединений
- •18.3 - Уплотнение газового тракта между ротором и статором ГТД
- •18.3.1 - Лабиринтные уплотнения
- •18.3.2 - Щеточные уплотнения
- •18.3.3 - Скользящие сухие уплотнения газодинамические
- •18.3.4 - Скользящие сухие уплотнения газостатические
- •18.3.5 - Сравнение эффективностей уплотнений газового тракта между ротором и статором ГТД
- •18.4 - Примеры уплотнений газового тракта ГТД
- •18.4.1 - Пример 1
- •18.4.2 - Пример 2. Уплотнение статорной и роторной частей турбины
- •18.5 - Уплотнения масляных полостей опор роторов, редукторов, коробок приводов
- •18.7 - Перечень использованной литературы

Глава 4 - Силовые схемы ГТД
Рис. 4.1.1.6_5 – Осевые силы, действующие на узлы двигателя ПС-90А
гателя, до закрытия клапанов перепуска за 6 и 7 ступенями КВД, по мере увеличения режима работы и параметров двигателя более интенсивным был рост газовых сил «компрессорной» части ротора и суммирующее усилие («осевая сила») направленное «вперед» также увеличивалось. После закрытия клапанов перепуска за 6 и 7 ступенями КВД, более интенсивным стал рост газовых сил «турбинной» части ротора и осевая сила стала уменьшаться при увеличении режима работы. Эта закономерность сохранилась несмотря на скачкообразное увеличение осевой силы в момент закрытия заслонок перепуска воздуха за КНД.
Аналогичным образом можно объяснить изменение осевой силы, действующей на шарикоподшипник ротора ВД, хотя характер изменения ее противоположен (см. Рис. 4.4.1.6_4).
Сумма осевых усилий, приложенных к различ- ным узлам двигателя, численно равна тяге, развиваемой ГТД.
На Рис. 4.1.1.6_5 показано расчетное распределение сил, действующих на узлы двигателя ПС90А на максимальном режиме работы в земных условиях. Внутренние усилия в элементах конструкции двигателя значительно превышают те усилия, которые передаются на силовые элементы самолета или рамы (для наземных установок). Правильное определения этих усилий, построение реальных схем воздействия сил на каждую отдель-
ную основную деталь силовой схемы двигателя позволит принимать оптимальные решения как с точ- ки зрения прочностных и ресурсных, так и с точки зрения массовых показателей для этих деталей.
4.1.2 - Крутящие моменты от газовых сил
C достаточной точностью крутящие моменты от газовых сил, возникающие на лопатках рабочих колес (РК) и НА можно вычислить на основе треугольников скоростей на среднем радиусе ступени перед и за соответствующими элементами [4.7.1]. Таким образом, для РК и НА компрессора (см. Рис. 4.1.2._1) расчетные формулы можно записать:
Ì |
ÊÐ |
ÐÊ = m (R |
2 ÑÐ |
Ñ |
2U |
– R |
1 ÑÐ |
Ñ ) |
(4.1.2-1) |
||||
|
|
|
|
1U |
|
|
|||||||
Ì |
ÊÐ |
ÍÀ = m (R |
|
Ñ |
– R |
2 ÑÐ |
Ñ |
2U |
) |
(4.1.2-2) |
|||
|
|
|
3 ÑÐ 3U |
|
|
|
|
|
ãäå m
R1 ÑÐ , R2 ÑÐ , R3 ÑÐ
Ñ1U ,Ñ2U,Ñ3U
–расход воздуха (газа);
–средний радиус проточной части перед и за РК или НА;
–окружная скорость воздуха (газа) на среднем
радиусе.
169

Глава 4 - Силовые схемы ГТД
Рисунок 4.1.2_1 — Определение крутящего момента на лопатках компрессора
Как видно из формул, крутящие моменты равны разности моментов количеств движения воздуха относительно оси вращения ротора.
Для РК момент имеет положительный знак, что означает подвод энергии к воздушному потоку и увеличение кинетической энергии вращательного движения воздуха. Окружное усилие и момент на рабочем колесе от воздействия воздуха направлены против направления вращения.
Для НА момент получается с отрицательным знаком, что означает уменьшение кинетической энергии вращательного движения и переход ее в давление. Окружное усилие и момент, действующие на НА, направлены в сторону вращения РК.
Крутящие моменты, действующие на ротор и корпус компрессора, суммируются начи- ная с первой ступени. Наибольшие крутящие моменты действуют за последней ступенью компрессора. Крутящий момент для любого промежуточного сечения ротора или корпуса определяется как сумма моментов всех предыдущих ступеней. Расчет этих моментов необходим для оценки прочности элементов конструкций ротора и корпуса.
Величины крутящих моментов, действующих на ротор и статор турбины, определяются аналогич- ным образом. Но процессы, происходящие в турбине, носят противоположный характер, а следовательно - направление действия крутящего момента будет направлено в другую сторону.
4.1.3 — Инерционные силы и моменты
Инерционные силы и моменты возникают в деталях двигателя от статической и динамической неуравновешенности роторов, а также от изменения
скорости и траектории самолета, на котором закреплен двигатель.
Неуравновешенные силы и моменты роторов двигателя передаются на корпуса через подшипниковые опоры. Направление действия этих сил меняется во времени, а величины этих сил пропорциональны квадрату частоты вращения ротора. Благодаря высокой точности балансировки роторов амплитуды этих сил и моментов невелики. Однако, действуя с высокой частотой, они способны вызывать вибрации корпусов и усталостные повреждения в них. Более подробно вопросы статической и динамической неуравновешенности роторов рассмотрены в разделе 14.5.
При разгоне и торможении самолета появляется дополнительная осевая сила (к силе обусловленной газовыми нагрузками), нагружающая ротор двигателя и передаваемая на корпус через упорные подшипники. Значение этой силы может превышать массу ротора в несколько раз. Кроме того, эта дополнительная сила нагружает узлы крепления двигателя к самолету.
При отклонении траектории полета самолета от прямолинейной возникает угловое ускорение, которое вызывает гироскопический момент и инерционные перегрузки. Величина гироскопического момента пропорциональна угловому ускорению и частоте вращения ротора и может быть определена как:
|
ÌÃ = ΙΩωsinα, |
(4.1.3-1) |
ãäå I |
- массовый момент инерции ротора |
относительно оси его вращения; Ω = 2π/τ - средняя угловая скорость вращения
самолета в пространстве
τ- время, необходимое для совер-
|
шения рассматриваемого поворота |
ω |
самолета на угол 360°; |
- угловая скорость вращения |
|
α |
ротора; |
- угол между осями, вокруг которых |
|
|
происходит вращение (как прави- |
|
ло, при расчете берут наиболее не- |
|
благоприятный случай с углом рав- |
|
íûì 90°). |
При отсутствии точных данных момент инерции ротора (кг см сек) можно определять приближенно по формуле:
|
I = k (R/1000)õ, |
(4.1.3-2) |
ãäå R |
- статическая тяга двигателя, кг; |
|
x =1 - для ротора с центробежным |
|
170

Глава 4 - Силовые схемы ГТД
Рисунок 4.1.3_1 — Определение направления действия гироскопического момента на ротора двигателей самолета
компрессором;
x = 2 - для ротора с осевым компрессором; k = 20…30.
Направление гироскопического момента определяется по направлению действия поворотного ускорения. При этом удобно пользоваться правилом: гироскопический момент, возникающий при отклонении самолета от прямолинейной траектории, направлен таким образом, что под действием его самолет стремится повернуться в пространстве так, чтобы направления вращения с угловыми скоростями ω è Ω, видимые от постороннего наблюдателя, совпадали. На Рис. 4.1.3_1 приведен пример определения направления действия гироскопического момента.
Гироскопический момент имеет весьма большую величину. Он передается на корпус от ротора через подшипники и опоры, вызывая в корпусах и роторах напряжения изгиба. Для уменьшения сил, действующих от гироскопического момента на подшипники и опоры, расстояние между последними выбирают как можно больше.
Угловую скорость вращения самолета можно также определить по коэффициенту перегрузки.
При эволюциях самолета возникает центро-
бежная сила инерции ротора (см. Рис. 4.1.3_1):
|
P |
j |
= Ω2rG/g = k G |
(4.1.3-3) |
|
|
1 |
|
|
ãäå G – вес ротора; |
|
|||
r |
– радиус кривизны; |
|
||
k1 |
– коэффициент перегрузки. |
|
||
|
Принимая во внимание, что скорость полета |
по траектории V = Ωr, из выражения (4.1.3-3) можно найти величину Ω:
Ω = k1g/V |
(4.1.3-4) |
ãäå V – скорость полета самолета.
Для самолетов-истребителей величина коэффициента перегрузки k1= 8…10 (десятикратная перегрузка получается, в частности, при выходе самолета из пикирования).
4.2 – Силовые схемы роторов
Силовые схемы роторов отличаются следующим:
-способом соединения дисков ступеней компрессора и турбины между собой;
-числом и расположением опор;
-способом соединения роторов турбины
èкомпрессора для передачи крутящего момента
èосевых сил;
-способом фиксации осевого положения роторов, исключающего их смещение и нарушение осевых и радиальных зазоров между элементами ротора и корпуса двигателя.
В зависимости от числа опор различают двух-, трех-, четырехопорные роторы, а в зависимости от числа роторов – одно-, двух- и трехвальные двигатели. Двухопорные роторы применяются при относительно коротких и жестких роторах компрессора и турбины, чаще всего — в системе газогенератора. Трехопорные роторы применяются в конструкциях многоступенчатых компрессоров и турбин, чаще всего — в системе наружных каскадов двухили трехвальных двигателей. Радиально-упорный подшипник, воспринимающий разность осевых нагрузок на компрессор
èтурбину, стараются расположить исходя из соображений его наименьшей тепловой напряженности, т.е. в «холодной» части двигателя, например в передней части компрессора.
На Рис. 4.2_1 представлены примеры широко применяемых силовых схем роторов авиационных двигателей:
-силовая схема роторов двигателя General Electric CF-6-80 – двухвальная с двухопорным ро-
171

Глава 4 - Силовые схемы ГТД
Рисунок 4.2_1 — Примеры силовых схем роторов авиационных двигателей
тором НД и четырехопорным ротором ВД;
- силовая схема роторов двигателя PW-2037 – двухвальная с трехопорным ротором НД и двухопорным ротором ВД;
-силовая схема роторов двигателя ПС-90А – двухвальная с трехопорным ротором НД и трехопорным ротором ВД;
-силовая схема роторов двигателя Rolls-Royce
172
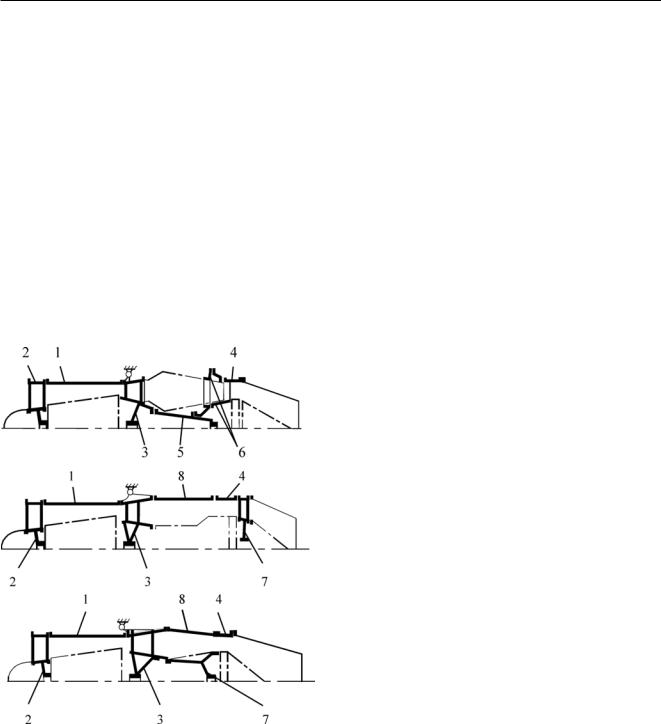
Глава 4 - Силовые схемы ГТД
Trent 800 – трехвальная с трехопорным ротором НД с межвальным расположением шарикоподшипника, трехопорным ротором СД и двухопорным ротором ВД.
Силовые схемы роторов ГТД наземного применения значительно проще. Как правило, они включают в себя одновальный ротор ВД базового авиационного двигателя (с высокой степенью унификации конструктивных решений) или новый специально разработанный ротор.
4.3 – Силовые схемы статоров
Силовые корпуса двигателей предназначены для восприятия и суммирования усилий, действующих в ГТД, и частичной передачи их в виде силы тяги (двигатели воздушных судов) на силовые эле-
Рисунок 4.3_1 – Типовые схемы статоров одноконтурных авиационных двигателей а) с «внутренней» связью; б) с «на-
ружной» связью; в) с комбинированной связью 1 – корпус компрессора; 2 – корпус
переднего подшипника; 3 – корпус среднего подшипника; 4 – корпус турбины; 5 – корпус заднего подшипника; 6 – корпус газосборника; 7 – корпус заднего подшипника; 8 – корпус камеры сгорания
менты самолета или крутящего момента (двигатели, как приводы к другим агрегатам) на подмоторную раму.
К силовым корпусам ГТД относят корпуса компрессора, камеры сгорания, турбины, а также корпуса опор. Все эти корпуса собираются в единую конструкцию - статор с помощью фланцев, которые соединяются болтами, шпильками, штифтами. К силовым корпусам крепятся входные и выходные устройства двигателя, коробки приводов, корпуса наружного контура, устройства форсирования и реверса тяги. На силовых корпусах размещаются узлы крепления двигателя к самолету или к подмоторной раме.
Силовые схемы статоров одноконтурных двигателей различаются, в основном, по виду связи корпусов компрессора, камеры сгорания, турбины и опоры заднего подшипника ротора. На Рис. 4.3_1 приведены четыре типовые схемы статоров одноконтурного двигателя с трехопорным ротором.
На всех схемах корпус 1 компрессора непосредственно связан с корпусом 2 переднего подшипника и корпусом 3 среднего подшипников ротора. На схеме а) корпус турбины 4 связан с корпусом среднего подшипника ротора через корпус 5 заднего подшипника ротора и корпус 6 газосборника. На схеме б) задний подшипник расположен за турбиной и его корпус 7 через корпус турбины и корпус 8 камеры сгорания связан с корпусом среднего подшипника ротора. На схеме в) изображена разветвленная связь корпусов, при которой к корпусу среднего подшипника ротора независимо крепят корпус заднего подшипника ротора, а через корпус камеры сгорания корпус турбины.
Âнастоящее время нашли широкое применение силовые схемы статоров типа б) и в). Силовая схема типа а) широко не распространена на двигателях с прямым потоком газа ввиду относительно небольшой жесткости и сложности конструктивного выполнения. Однако, она применяется на двигателях с петлевым потоком газа, к примеру, на промышленных ГТД или двигателях малой мощности.
Силовые схемы статоров двухконтурных двигателей, в основном, являются развитием какойлибо из вышеперечисленных схем с включением
âнее силового корпуса наружного контура. Рассмотрим одну из таких схем статоров на примере авиационного двигателя ПС –90À.
Âсиловую схему статоров газогенератора двигателя ПС-90А (рис. 4.3_2) входят разделительный корпус 1, корпус 2 КВД, наружный корпус 3 и внутренний корпус 4 камеры сгорания, корпус 5 тур-
173

Глава 4 - Силовые схемы ГТД
Рисунок 4.3_2 – Силовая схема статора двигателя ПС - 90А 1 – разделительный корпус; 2 – корпус КВД; 3 – наружный корпус камеры сгорания;
4 – внутренний корпус камеры сгорания; 5 – корпус турбины; 6 – задняя опора; 7 – стойки (штыри) камеры сгорания; 8 – опора шарикоподшипника ротора низкого давления; 9 – наружный корпус вентилятора; 10 – наружный корпус; 11, 12, 13 – опоры ротора низкого давления; 14, 15, 16 – опоры ротора высокого давления
бины, задняя опора 6. Наружный корпус и внутренний корпус камеры сгорания жестко соединены между собой стойками (штырями) 7. К силовой схеме газогенератора через разделительный корпус жестко присоединены силовые элементы наружного контура – опора 8 шарикоподшипника ротора низкого давления, наружный корпус 9 вентилятора, наружный корпус 10.
В двигателе применены трехопорная схема ротора ВД и трехопорная схема ротора НД. Опоры 11, 12, 13 – опоры ротора НД, причем опора 11 служит для восприятия осевого усилия и передачи его на корпус газогенератора. Опоры 14, 15, 16 – опоры ротора ВД, причем опора 15 служит для восприятия осевого усилия и передачи его на корпус газогенератора. В опорах 11 и 15 установлены радиально-упорные шарикоподшипники, в остальных опорах – роликовые подшипники.
Крепление двигателя ПС-90А к пилону самолета, передача силы тяги к силовым элементам пилона осуществлены деталями системы подвески (более подробно см. раздел 4.5).
4.4 – Опоры роторов ГТД
Опоры ГТД служат для передачи усилия от вращающихся роторов к корпусам. Опоры воспринимают значительные статические и динамические усилия от валов двигателя. Они должны обеспечи- вать достаточную жесткость силовой схемы дви-
гателя и необходимое центрирование валов во всем диапазоне реализуемых нагрузок.
В настоящее время получили распространение следующие типы опор:
-опоры жесткого типа, воспринимающие усилия во всех направлениях;
-упруго-демпферные опоры, устанавливаемые преимущественно на радиальные подшипники;
-опоры межроторного типа.
Êпреимуществам опор первого типа можно отнести достаточно простую конструкцию, возможность передачи значительных осевых и радиальных усилий. Недостатком жестких опор является их большая чувствительность к температурному градиенту, что приводит к значительному изменению посадки наружных колец подшипников. К опорам жесткого типа предъявляются высокие требования по точности механической обработки посадочных мест под подшипники.
Êпреимуществам опор второго типа можно отнести возможность самоустановки опоры в процессе работы, меньшую массу, чем у опор первого типа, возможность некоторого демпфирования передаваемых усилий, меньшую чувствительность
êтемпературным градиентам. Недостатки опор данного типа — относительная сложность конструкции, ограничение использования из-за гибкости. Проявление динамических явлений в таких опорах требует их доводки в процессе разработки.
Опоры межроторного типа не нуждаются в прямой связи с корпусами двигателя. Они передают нагрузку на силовые корпуса через тот ро-
174

Глава 4 - Силовые схемы ГТД
тор, на который опираются. Опоры этого типа наиболее компактны, но требуют серьезной конструктивной проработки и доводки. Они имеют самую сложную систему подачи и отвода масла к подшипнику — детали систем подвода и отвода масла размещаются во вращающихся валах.
4.4.1 — Конструктивные элементы опор ГТД
Конструкции опор ГТД весьма разнообразны. Они учитывают индивидуальные особенности конкретного двигателя и практически не повторяются в различных разработках. Однако, при всем конструктивном разнообразии в конструкции опор всегда можно выделить группы элементов (или деталей), имеющих единое функциональное назна- чение.
Âобщем случае опора ГТД (см. Рис. 4.4.1_1)
âсвоем составе обязательно содержит основные элементы – статорную и роторную части и подшипник. Статорная (корпусная) часть 1 опоры – передает усилия от неподвижного кольца подшипника на корпуса двигателя. Роторная часть 2 опоры – передает усилия от ротора двигателя на подвижное кольцо подшипника. Подшипник 3 опоры – сопрягает подвижный ротор и неподвижный корпус, передает усилия от роторной к статорной части опоры. Все эти элементы опоры являются силовы-
Рисунок 4.4.1_1 – Опора ГТД 1 – статорная часть опоры;
2 – роторная часть опоры;
3 – подшипник; 4 – фланец;
5 – опорная гайка
ми, они обеспечивают передачу усилий от ротора на статорную часть двигателя.
Кроме силовых элементов в состав опоры могут входить отдельные элементы систем обеспече- ния работоспособности подшипника, а именно:
-детали уплотнений масляной полости;
-детали системы смазки подшипника;
-детали наддува уплотнений масляной полости;
-детали системы охлаждения опоры. Деталями и узлами двигателя вокруг каждой
опоры создается замкнутое пространство, в котором организована подача масла на подшипники и откачка масла. Это замкнутое пространство называется масляной полостью опоры. Нередко конструкция двигателя предусматривает одну масляную полость для нескольких опор.
4.4.2 — Статорная часть опоры
Основное назначение статорной части опоры – установка неподвижного кольца подшипника и восприятие усилий от этого кольца для передачи на корпуса двигателя. На статорной части опоры расположено посадочное место неподвижного кольца подшипника. К точности его выполнения предъявляются специальные требования по ОСТ1 00323-79 [4.7.2].
При проектировании статорной части опоры необходимо учитывать, что жесткость опоры непосредственно влияет на величину допустимых зазоров по торцам лопаток компрессора и турбины, а следовательно - на к.п.д. этих узлов. Можно выделить две основные группы опор, в конструкции которых реализуются различные требования по жесткости. Первая группа – жесткие опоры. Вторая группа – опоры с упругими элементами, размещенными под неподвижным кольцом подшипника.
Жесткие опоры подшипника, входящие в статор двигателя, могут быть выполнены двумя различными способами. Они могут быть одним целым с корпусом узла двигателя, в котором размещена опора. При этом цельный корпус узла может быть литой, штампованной или сварной конструкции (примеры таких конструкций приведены на Рис. 4.4.7.1_3, 4.4.7.1_6). По второму способу опоры могут иметь самостоятельный корпус с одним или более фланцевыми соединениями с любым корпусом статора двигателя (см. Рис. 4.4.7.1_9, 4.4.7.1_12, 4.4.7.1_13).
Когда жесткая опора выполнена заодно с корпусом двигателя, в этот корпус нередко запрессовывается стальная гильза, в которую и устанавли-
175

Глава 4 - Силовые схемы ГТД
Рисунок 4.4.1_2 – Применение запрессованной гильзы в корпусе опоры ГТД 1 – подшипник; 2 – корпус узла двигателя; 3 - гильза
вается неподвижное кольцо подшипника (см. Рис. 4.4.1_2, 4.4.7.1_6).
Если корпус имеет в радиальном направлении большой градиент температуры, то для сохранения посадки гильзы в корпусе опоры может использоваться упругий элемент между холодной частью корпуса, омывающейся маслом, и наружной горячей частью корпуса. Ослабление или полное исчезновение натяга запрессованной в корпус гильзы происходит за счет температурной утяжки от горячей части корпуса более холодной части, прилегающей к гильзе. Пример конструкции с упругим элементом корпуса опоры показан на Рис. 4.4.7.1_4, 4.4.7.1_6.
При необходимости отстройки от резонансов изгибных колебаний ротора или для компенсации несоосности опор при многоопорных схемах роторов ГТД в непосредственной близости от неподвижного кольца подшипника могут размещаться упругие, демпферные (сухие или масляные) или упруго-демпферные элементы. Более подробно описание конструкции и работы упруго-демпфер- ных элементов приведено в разделе 4.5.7. Разнообразные конструктивные варианты таких опор представлены в разделе 4.4.7.1.
Следует напомнить, что реализация демпфирования требует увеличения радиальных зазоров по лопаткам компрессора и турбины, а это всегда нежелательно с точки зрения к.п.д. этих узлов.
Иногда с целью минимизации диаметральных размеров опоры беговая дорожка для тел качения подшипника организуется непосредственно на поверхности корпуса опоры (см. Рис. 4.4.7.1_13), т.е.
применяются специальные так называемые интегральные подшипники.
4.4.3 — Роторная часть опоры
Основное назначение роторной части опоры
– установка подвижного кольца подшипника и передача усилия от вала ротора на это подвижное кольцо. На роторной части опоры расположено посадочное место подвижного внутреннего кольца подшипника. К точности выполнения посадоч- ного места предъявляются специальные требования по ОСТ1 00323-79 [4.7.2].
Кроме этого на роторной части опоры могут быть расположены детали подвода масла, если подача смазки организована через внутреннее кольцо подшипника. Конструктивное исполнение подобных решений представлено на Рис. 4.4.7.1_3, 4.4.7.1_7, 4.4.7.1_12.
При установке подвижного кольца подшипника с помощью пакета деталей, одна из которых имеет резьбовое крепление к валу ротора, необходимо обеспечить высокую точность опорных торцев деталей пакета (минимальное биение) и стабильность этого биения в процессе эксплуатации.
В некоторых случаях для обеспечения ремонтопригодности вала под внутреннее кольцо подшипника запрессовывается стальная втулка (см.Рис. 4.4.7.1_2).
Для уменьшения размеров опоры так же, как и для статорной части применяются интегральные подшипники - вместо беговой дорожки подвижного кольца организуется беговая дорожка на поверхности вала или специальной втулки, размещенной на валу. Примеры таких конструкций приведены на Рис. 4.4.7.1_4, 4.4.7.1_13.
4.4.4 – Подшипники
Подшипники являются наиболее ответственными элементами опор ГТД - именно в них происходит непосредственный силовой контакт между ротором и статором двигателя. Подшипники ГТД должны обеспечивать безотказную работу в тече- ние требуемого ресурса при заданных уровнях скоростей и нагрузок. Поэтому для них необходимо обеспечить определенные условия смазки, охлаждения, а также защиты от внешних неблагоприятных воздействий (тепловых потоков, твердых частиц загрязнений и т.д.). Для осуществления этих функций предназначены механические компоненты, образующие масляную и внешние воздушные полости опор, система смазки, а также система наддува уплотнений и охлаждения опор.
176

Глава 4 - Силовые схемы ГТД
4.4.4.1 – Типы подшипников ГТД и их обозначения
В современных ГТД, в основном, применяются подшипники качения, обладающие по сравнению с подшипниками скольжения рядом преимуществ: меньшим коэффициентом трения, большей устойчивостью к попаданию загрязнений и работе с перекосом, меньшими размерами по длине, меньшей потребностью в смазке, возможностью работы в широком диапазоне частот вращения.
Рисунок 4.4.4.1_1 – Типы подшипников ГТД а) шариковый подшипник – вос-
принимает все виды нагрузок; б) роликовый подшипник – воспринимает только радиальные нагрузки
Рисунок 4.4.4.1_2 – Условное обозначение подшипника
Подшипники скольжения в ГТД применяются в конструкции отдельных элементов двигателя и агрегатов воздушной и масляной систем - в тех местах, где требуется конструктивно обеспечить минимальные радиальные размеры в зонах пар трения (поворотные лопатки компрессора, шестеренчатые насосы маслосистемы, заслонки воздушных систем и т.д.).
Подшипники качения классифицируют по следующим признакам:
1)по направлению воспринимаемой нагрузки относительно оси вала - радиальные, радиаль- но-упорные, упорные;
2)по форме тел качения - шариковые, роли-
ковые.
В опорах роторов ГТД применяются, как правило, однорядные шариковые и роликовые подшипники с сепараторами. Наличие сепаратора позволяет распределить тела качения (шарики, ролики) равномерно по окружности. При этом исключается их взаимное задевание (трение) и обеспечивается стабильный процесс распределения нагрузки.
Соотношение габаритных размеров подшипников качения определяет их серию: сверхлегкую, особо легкую, легкую, легкую широкую, среднюю, среднюю широкую и тяжелую.
В ГТД применяются преимущественно подшипники сверхлегкой, особо легкой, легкой и средней серий.
177

Глава 4 - Силовые схемы ГТД
Для российских подшипников качения характеристика типа и исполнения, точности изготовления, его конструктивных особенностей заложена в условном обозначении, узаконенном государственным стандартом ГОСТ 3189-89[4.7.3].
Условное обозначение подшипника состоит из основного и вспомогательного(см. Рис. 4.4.4.1_2). Основное обозначение – цифровое, максимальное количество цифр – семь.
Порядковый номер цифр в основном обозна- чении считают справа налево.
*1 - внутренний диаметр подшипника. Число из первых двух цифр от 04 до 99 умно-
женное на 5 даст внутренний диаметр подшипника. Числа менее 04 обозначают внутренние диаметры: 00 - 10 мм, 01 - 12 мм, 02 - 15 мм, 03 - 17 мм.
*2 - серия подшипников по наружному диаметру:
9 и 8 – сверхлегкая,
1 и 7 – особолегкая,
2 – легкая,
5 – легкая широкая,
3 – средняя,
6 – средняя широкая,
4 – тяжелая,
5 – особо тяжелая (только для упорных подшипников).
*3 - тип подшипника (форма тел качения
èнаправление воспринимаемой нагрузки): 0 – шариковый радиальный однорядный,
1 – шариковый радиальный сферический двухрядный, 2 – роликовый радиальный с короткими цилинд-
рическими роликами, 3 – шариковый радиальный сферический двухрядный,
4 – роликовый радиальный с длинными цилиндрическими роликами или иглами, 5 – роликовый радиальный с витыми роликами,
6 – шариковый радиально-упорный,
7 – роликовый конический,
8 – шариковый упорный,
9 – роликовый упорный.
*4 - условное обозначение конструктивной разновидности подшипника.
*5 - условное обозначение серии по ширине
èвысоте подшипника.
*6 - условное обозначение материала деталей подшипника (например *8, *9 и т.д.).
*7 - условное обозначение специальных технических требований (например *10 и т.д.).
*8 - Р (Р1, Р2...) – детали подшипников из теплостойких сталей.
*9 - Л (Л1, Л2...) – сепаратор из латуни.
*10 - У (У1, У2...) – дополнительные технические требования к шероховатостям поверхности деталей, к радиальному зазору и осевой «игре», к покрытию.
Пример расшифровки обозначений подшипника. Подшипник 6-80202Т2С15 – шариковый радиальный однорядный с двумя защитными шайбами, изготовлен из стали ШХ-15 с габаритными размерами по ГОСТ 7242-70 [4.7.4], по 6 классу точности, с радиальным зазором по основному ряду, с температурой отпуска 250°С (Т2), заполнен пластичной смазкой ВНИИ НП-207 (С15), 02 – внутренний диаметр подшипника, равный 15 мм; 2 – серия наружного диаметра - легкая;
0 – тип подшипника - радиальный шариковый;
08 – конструктивная разновидность - с двумя защитными шайбами; 0 – серия ширины: нормальная.
Дополнительно заводы-изготовители авиационных подшипников указывают индивидуальный номер подшипника и номер партии – год и месяц изготовления подшипника.
Перед постановкой в изделие заводы-изгото- вители авиационных двигателей маркируют подшипники: указывается место установки и номер двигателя (номер комплекта).
4.4.4.2 – Материалы подшипников
Кольца и тела качения подшипников работают при значительных сосредоточенных нагрузках, вызывающих высокие контактные напряжения, в условиях многоциклового воздействия. Одновременно рабочие поверхности этих деталей подвергаются истиранию вследствие проскальзывания, сопровождающего процесс вращения подшипника.
Контактные напряжения в рабочих зонах могут достигать весьма больших значений (порядка 4000 МПа).
В связи с этим к подшипниковым материалам предъявляется ряд специфических требований, основное из которых наличие высокой твердости. Твердость колец и тел качения подшипников, как правило, должна быть не менее 59 HRC. В ряде случаев для специфических условий применения, когда нагрузки на подшипники малы, допускается использование материалов, имеющих твердость в пределах 45…50 HRC. Кроме этого, подшипниковые материалы должны обладать высокими прочностными характеристиками, сопротивлением износу, удовлетворительными усталостными свойствами, вязкостью (сопротивлением хрупкому разрушению). Для определенной группы подшипников необходимо, чтобы материалы могли
178

Глава 4 - Силовые схемы ГТД
противостоять воздействию повышенных температур и агрессивных сред (тепло- и коррозионностойкие подшипниковые материалы).
Материалы для деталей подшипников характеризуются высокой структурной и размерной стабильностью. Для достижения указанного комплекса свойств необходимо, чтобы подшипниковые материалы обладали минимальной загрязненностью неметаллическими вклю- чениями, удовлетворительной макроструктурой, отсутствием микронесплошностей, регламентированными структурными характеристиками перлита, мартенсита, карбидной составляющей и т.п. Принимая это во внимание, подшипниковые материалы можно разделить на три основные группы.
Первая группа — стандартные подшипниковые материалы, включающие в себя высокоуглеродистые хромистые твердокалящиеся стали и низкоуглеродистые легированные конструкционные стали с поверхностным упрочнением.
Вторая группа — теплопрочные и коррозион- но-стойкие высокоуглеродистые легированные стали и сплавы.
Третья группа — неметаллические материалы. При создании авиационных двигателей прослеживается тенденция к увеличению удельной мощности, снижению массы и повышению рабо- чей температуры деталей опор. Поэтому для деталей авиационных подшипников в большинстве случаев приходится использовать специальные материалы. Например, к низколегированным хромистым сталям, широко применяемым в общем машиностроении, прежде всего добавились коррозионностойкие стали, теплопрочные цементируе-
мые стали, а также различные виды керамики. Отечественная промышленность при произ-
водстве подшипников использует следующие материалы:
-ØÕ15-Ø – хромистая высокоуглеродистая твердокалящаяся сталь, изготавливаемая методом электрошлакового переплава. Подшипники, изготовленные из этой стали могут работать при температуре до 120 îС. Для повышения рабочей температуры подшипников необходима дополнительная термообработка стали (отпуск при более высокой температуре), но при этом твердость стали уменьшается. В этом случае подшипники из данной стали применяются при температурах эксплуатации ниже 200 îÑ.
-8Õ4Â9Ô2-Ø (ЭИ347Ш) – легированная вольфрамом теплопрочная подшипниковая сталь, изготавливаемая методом электрошлакового переплава. Подшипники, изготовленные из этой стали
могут работать при температуре до 450 îС, поэтому широко применяются в опорах основных валов ГТД. По сравнению со сталью ШХ15-Ш данная сталь менее технологична и имеет более высокую стоимость.
-95Õ18-Ø – коррозионно-стойкая высокохромистая сталь, изготавливаемая методом электрошлакового переплава. В зависимости от температуры эксплуатации подшипников применяют два варианта термообработки деталей: с низким отпуском 150…160 îС и с отпуском на вторичную твердость при 400…420 îС. Подшипники из данной стали применяются, как правило, в местах неимеющих циркуляционной смазки (шарнирные подшипники для крепления двигателя в мотогондоле, подшипники тросовой системы и т.п.).
В настоящее время для производства авиационных подшипников качения иностранные производители подшипников используют следующие материалы:
-AISI 52100 - высокоуглеродистая хромистая сталь, получаемая методом вакуумно-дугового переплава. Подшипники, выполненные из этой стали могут работать при температуре до 120 îС. Для стабильной работы при более высокой температуре (до 205 îС) необходима дополнительная термообработка стали, но при высокой температуре твердость стали уменьшается. Отечественный аналог — сталь ШХ15-Ш;
-М50 — молибденовая теплопрочная сталь. Высокая чистота материала достигается методом двойного вакуумного переплава (вакуумно-индук- ционная выплавка с последующим вакуумно-дуго- вым переплавом). В настоящее время М50 является преобладающей сталью, используемой для производства авиационных подшипников, работающих при высокой температуре. Подшипники, выполненные из этой стали, могут работать при температуре до 320 îС. У стали М50 существует «барьер», когда из-за большой скорости вращения (приблизительно при d•N = 2,4•106 (ìì•îá/ìèí), ãäå d - внутренний диаметр подшипника (мм), N - скорость вращения вала (об/мин)), натяга при посадке и изгибающих или деформирующих напряжений на дорожке качения подшипника появляются окружные растягивающие напряжения, превышающие величину 190 МПа. Эти напряжения увели- чивают общие напряжения материала, появляющиеся вследствие контакта при качении, что приводит
êусталостному выкрашиванию и растрескиванию вращающегося кольца. Подшипники, выполненные из стали М50 рекомендуется использовать при d•N äî 2•106 (ìì•об/мин). В отечественной подшипниковой промышленности применяется ана-
179

Глава 4 - Силовые схемы ГТД
лог – высоковольфрамовая теплопрочная сталь ЭИ347-Ш;
-М50 Nil – цементируемая сталь, основанная на стали М50, со сниженным содержанием углерода (0,12%). Также, как и М50, сталь М50 Nil получается методом двойного вакуумного переплава. Эта сталь рекомендуется для применения при значении параметра d•N îò 2•106 äî 2,4•106 (ìì•об/ мин). Стойкость стали к напряжениям растяжения достигается благодаря тому, что при цементации
âцементируемом слое возникают остаточные сжимающие напряжения. В отечественной промышленности нет теплопрочных цементируемых подшипниковых сталей;
-М50 SuperNil – это сталь М50 Nil, термообработанная по специальному технологическому процессу. В результате специальной термообработки остаточные внутренние сжимающие напряжения получаются больше, чем у стали М50 Nil. М50 SuperNil рекомендуется для применения при d•N îò 2,5•106 äî 3•106 (ìì•îá/ìèí);
-AISI 440С – коррозионностойкая сталь, имеющая незначительную усталостную прочность в связи с низкой твердостью из-за особенностей структуры материала (наличие избыточных карбидов). Применение этой стали в авиационной промышленности ограничено. Отечественный аналог – сталь 95Х18;
-Cronidur 30 – азотируемая мартенситная нержавеющая сталь. Этот материал, созданный в Германии для подшипников качения, продемонстрировал улучшение коррозионной стойкости в сто раз по сравнению с AISI 440С и в пять раз увеличение срока службы подшипников по сравнению со сталью M50. Cronidur 30 отличается от применяемых для подшипников сталей высоким содержанием хрома.
Из керамических материалов, используемых для производства высокоскоростных подшипников каче- ния, лучше всего зарекомендовал себя нитрид кремния /Si3N4/. Особенности этого материала — высокая прочность, высокая твердость, коррозионная стойкость и низкая плотность — позволяют применять его при более высоких температурах и снизить массу. В то же время увеличение срока службы может быть достигнуто путем снижения тепловыделения, напряженности материала и износа подшипника. Коррозия может быть полностью исключена как причина отказа.
В настоящее время нитрид кремния широко используется для изготовления подшипников. Наибольший эффект дают комбинированные подшипники (подшипники с керамическими телами каче- ния и стальными кольцами).
Чисто керамические подшипники из-за высокой стоимости применяются только в особых слу- чаях: при работе без смазки в условиях очень высоких температур. Вследствие этого их применение в авиации в обозримом будущем ограничено.
Для изготовления сепараторов авиационных подшипников используются следующие материалы:
-безоловянистые бронзы,
-латунь,
-магниевый чугун,
-стали, имеющие закалку до 35…40 HRCÝ,
-алюминиевые сплавы,
-текстолит
При этом сепараторы из алюминиевых сплавов и текстолита используются в подшипниках, рабочая температура которых не превышает 150 îС. Для остальных материалов рабочая температура может быть 300 îÑ è âûøå.
В отдельных случаях (например, в подшипниках главных валов) на сепараторы наносят антифрикционное покрытие:
-свинцово-оловянистое (при рабочей температуре до 250 îÑ);
-серебро (при рабочей температуре 300 îÑ
èâûøå).
Коэффициент теплового расширения материала сепаратора должен быть близок, насколько это возможно, к коэффициенту теплового расширения материалов наружного и внутреннего колец, а также тел качения подшипника. Это необходимо для обеспечения стабильных (или минимально изменяемых) зазоров в подшипнике в процессе работы.
4.4.4.3 – Условия работы и особенности конструкции подшипников ГТД
ÂГТД подшипники опор работают в условиях сравнительно высоких радиальных и осевых нагрузок, высоких окружных скоростей. Кроме того, на работоспособность подшипников оказывают значительное влияние такие факторы, как температурное состояние опоры, организация подачи смазки на тела качения, наличие частиц загрязнений в масле, точность изготовления, а также конструктивные особенности непосредственно самих подшипников.
Âопорах роторов ГТД применяются исклю- чительно подшипники качения: однорядные шариковые – для восприятия радиальных и осевых нагрузок и однорядные роликовые – для восприятия радиальных нагрузок. Основные типы и конструктивные особенности шариковых подшипников показаны на Рис. 4.4.4.3_1.
180

Глава 4 - Силовые схемы ГТД
Рисунок 4.4.4.3_1 – Типы и особенности шариковых подшипников, применяемых в ГТД а) двухточечный; б) трехточечный с разъемным наружным кольцом;
в) четырехточечный с разъемным внутренним кольцом; г) с подводом масла через наружное кольцо;
д) с фланцевым креплением наружного кольца к корпусу опоры; е) с технологическим буртом для демонтажа
Рисунок 4.4.4.3_2 – Типы роликовых подшипников, применяемых в ГТД а) с фиксацией роликов на внутреннем кольце; б) с фиксацией роликов на наружном кольце;
в) без внутреннего кольца, с подводом масла через наружное кольцо; г) без наружного кольца, с подводом масла через внутреннее кольцо.
Подшипник а) применяется как радиальноупорный. Радиус беговой дорожки в нем несколько больше радиуса шара. Под действием осевой силы в подшипнике линия контакта смещается на угол контакта α , величина которого и определяет величину нагрузки. Направление воспринимаемых нагрузок – радиальных и осевых – в обе стороны. Величина допустимой осевой нагрузки может достигать до 70% от неиспользованной допустимой радиальной нагрузки.
Подшипник б) имеет разъемное наружное кольцо с большой глубиной канавки и увеличенный угол контакта α , что позволяет воспринимать большие радиальную и осевую нагрузки. В таких подшипниках шарики имеют контакт с беговыми дорожками в трех точках, их называют трехточечными.
Подшипник в) имеет разъемное внутреннее кольцо с двумя точками контакта и неразъемное наружное кольцо со специальным профилем беговой дорожки, который также обеспечивает контакт с шариком в двух точках с увеличением угла контакта α. Такие подшипники (с четырехточечным контактом) могут воспринимать еще более высокие радиальные и осевые нагрузки. Однако следует учитывать, что увеличение точек контакта не проходит бесследно и приводит к увеличению тепловыделения при работе подшипника, что требует в свою очередь увеличения подачи масла для обеспечения съема тепла. Подшипники с четырехточеч- ным контактом обеспечивают восприятие максимальных радиальных и осевых нагрузок при минимальном осевом люфте подшипника.
181

Глава 4 - Силовые схемы ГТД
Нередки случаи, когда отдельные элементы подшипников проектируются с учетом индивидуальных особенностей конструкции опор, требований технологии и т.д. На Рис. 4.4.4.3_1 приведены такие конструктивные особенности подшипников. Подшипник г) имеет наружное кольцо с отверстиями для подачи масла для смазки шаров. Аналогичные отверстия могут выполняться на внутренних кольцах подшипников.Наружное кольцо подшипника д) имеет фланец для крепления к корпусу опоры. Подшипник е) имеет на наружном кольце специальный буртик для крепления съемного приспособления для демонтажа подшипника.
Основные типы роликовых подшипников, применяемых в ГТД, приведены на Рис. 4.4.4.3_2.
На подшипниках а) и б) осевая фиксация роликов осуществлена бортами, расположенными на подвижном внутреннем кольце и на неподвижном наружном кольце соответственно. У роликовых подшипников для компенсации значительных температурных перемещений вала или корпусных деталей внутреннее или наружное кольцо могут выполняться значительно более широкими. Учитывая большую степень интеграции подшипниковых узлов в конструкцию опор, довольно часто роль наружного или внутреннего кольца возлагают на детали корпуса или ротора, что позволяет уменьшить диаметральные размеры опор. В этом случае применяют подшипники в) и г). На этих же исполнениях на кольцах подшипника показаны отверстия для подвода масла на ролики.
Важным элементом конструкции подшипника, определяющим его работоспособность, являет-
Рисунок 4.4.4.3_3 – Места износа сепаратора роликового подшипника а) при центровке по наружному кольцу;
б) при центровке по внутреннему кольцу.
ся сепаратор, в частности его центровка. Центрировать сепаратор можно как по наружному, так и по внутреннему кольцу. В каждом из этих способов есть свои преимущества и свои недостатки.
При центровке сепаратора по внутреннему кольцу (см. Рис. 4.4.4.3_3) происходит следующее: под действием неуравновешенной силы Ð, сепаратор прижимается к кольцу, его внутренняя поверхность будет изнашиваться в секторе, который был легким. Таким образом, легкая часть сепаратора будет становиться еще более легкой, а неуравновешенная сила сепаратора с центровкой по внутреннему кольцу в процессе износа будет увеличи- ваться. При центровке по внутреннему кольцу температурное расширение сепаратора приводит к увеличению зазора между кольцом и сепаратором, что исключает возможность заклинивания последнего.
При центровке сепаратора по наружному кольцу (см. Рис. 4.4.4.3_3) явление износа сепаратора в «тяжелом» секторе приводит к уменьшению неуравновешенной силы. Отрицательной стороной такой центровки является то, что при изменении температурного режима работы подшипника возможно расширение сепаратора с уменьшением зазора между ним и наружным кольцом до нуля с последующим заклиниванием сепаратора в наружном кольце.
Необходимо отметить, что центровка сепаратора по наружному кольцу улучшает условия смазки, т.к. появляется возможность подачи масла в увеличенный зазор между сепаратором и внутренним кольцом, уменьшает удельное давление на поверхности центрирования, обеспечивает лучший отвод тепла от подшипника через более холодное наружное кольцо.
Для работы подшипника важное значение имеет точность и качество изготовления как самих подшипников, так и посадочных мест на валах
èкорпусах под эти подшипники, получение строго определенной геометрической формы, минимальной эксцентричности и требуемой шероховатости посадочных поверхностей.
Надежная работа подшипников обеспечивается правильным подбором зазоров между телами качения и кольцами с учетом необходимости работы в широком диапазоне нагрузок и температур. Заниженные зазоры, переходящие в натяг при определенных температурных условиях, могут привести к большим контактным напряжениям с последующим выкрашиванием материала тел качения
èколец. Завышенные зазоры могут привести к проскальзыванию тел качения с сопутствующими процессами повышенного износа.
182

Глава 4 - Силовые схемы ГТД
Как показывает практика, на подшипники должны постоянно действовать нагрузки, достаточные для предотвращения в них проскальзывания на всех рабочих и переходных режимах работы двигателя, в том числе и на режимах запуска
èсброса частоты вращения. С достаточной для инженерной практики точностью можно считать, что 30…40% номинального натяга при посадке наружного кольца в корпус опоры и 70…90% номинального натяга при посадке внутреннего кольца на вал идет на уменьшение начального радиального зазора в подшипнике. Как правило, процесс подбора зазора в подшипниках – это тонкий и длительный процесс, во многом определяемый опытной
èэкспериментальной доводкой авиационного двигателя.
Âнастоящее время широкое распространение получила практика проектирования специальных подшипников разработчиками двигателей. В этом случае подшипники индивидуальной конструкции оптимально интегрируются в опоры двигателя, позволяя упростить конструкцию, улучшить массовые характеристики при сохранении или даже улуч- шении показателей долговечности и надежности.
4.4.4.4 – Основные дефекты подшипниковых узлов
Выход из строя подшипников, является одним из самых тяжелых по своим последствиям проявлением дефектов авиационного двигателя.
В основном, выход подшипников из строя обусловлен усталостным выкрашиванием материала на дорожках качения колец и телах качения. Начальными дефектами, по которым развивается выкрашивание материала являются коррозия, намятины и риски, прорыв масляной пленки, высокие контактные напряжения, прижоги при проскальзывании, дефекты материала подшипников.
Кроме этого, к выходу подшипников из строя приводит разрыв сепаратора, фреттинг-коррозия по посадочным поверхностям, износ подшипников без усталостного выкрашивания.
Результаты анализа проявления дефектов подшипников, а также причины, вызывающие вышеперечисленные дефекты и способы их устранения представлены в таблице 4.4.4.4_1.
Кроме того, на работоспособность подшипника влияет ряд факторов, а именно:
1) производственные, обусловленные точностью изготовления и особенностями технологии сборки:
- перекосы внутреннего и наружного подшипника относительно друг друга, изменяющие кине-
матику подшипника и, связанное с этим, дополнительное взаимодействие элементов подшипника;
-забоины на телах качения, наносимые при сборке из-за несовершенства технологии или невнимательности сборщика, влияющие на реальные (фактические) зазоры и возможный дополнительный распор в подшипнике, инициирующий нача- ло выкрашивания;
2) эксплуатационные, обусловленные попаданием в зону контакта между телами качения:
-фрагментов грязи, заносимых смазкой;
-твердых частиц – продуктов износа, выкрашивания или разрушения других элементов, заносимых смазкой или с наддуваемым опору воздухом;
3) дополнительные нагрузки в подшипнике при транспортировке, приводящие к микродеформации поверхности беговых дорожек колец подшипников.
Влияние этих вредных факторов устраняется следующими мероприятиями:
-соблюдение дополнительных конструкторс- ко-технологических требований к процессам изготовления, сборки, эксплуатации двигателя, введение
âконструкцию двигателя регулировочных элементов для устранения несоосностей, перекосов подшипников;
-оснащение процесса сборки специальными приспособлениями, исключающими получение забоин на подшипниках;
-дополнительная очистка воздуха, подаваемого на наддув уплотнений;
-ужесточения условий транспортировки (например, запрет перевозки железнодорожным транспортом или контроль уровня перегрузок при транспортировке).
В большинстве случаев к выходу подшипников из строя приводит сочетание нескольких неблагоприятных факторов, например, сочетание высокой нагрузки, высокой температуры и нали- чия частиц загрязнения в масле и в воздухе, попадающем в масляную полость через лабиринтные уплотнения.
Говоря о дефектах подшипников необходимо отметить, что при работе подшипника в «комфортных условиях» (высокая чистота масла, относительно невысокие температуры и оптимальные нагрузки) подшипник качения становится практи- чески «вечным».
С целью своевременного диагностирования состояния подшипников на авиационных двигателях применяются специальные системы контроля, позволяющие отследить начальные стадии проявления дефекта. В частности, в линиях откачки масла
183

Глава 4 - Силовые схемы ГТД
|
|
Таблица 4.4.4.4_1. |
|
|
Дефекты подшипников ГТД |
||
|
|
|
|
Наименование |
Причины дефекта |
Способ устранения дефекта |
|
дефекта |
|||
|
|
||
|
|
|
|
|
|
Ужесточение контроля за чистотой деталей |
|
|
|
и узлов, поступающих на сборку. Исключение |
|
|
Попадание с маслом в подшипники стружки |
застойных зон в деталях маслосистемы, из |
|
|
и абразивных частиц, оставшихся в полостях при |
которых невозможно удалить загрязнения. |
|
|
изготовлении деталей и узлов двигателя |
Исключение попадания абразивных частиц |
|
|
|
в маслосистему на участках сборки (применение |
|
|
|
заглушек, чехлов и т.п.) |
|
Намятины и риски |
|
Применение покрытий, исключающих |
|
|
образование абразивных частиц. |
||
|
|
Внедрение конструкции уплотнений опор, |
|
|
Попадание продуктов приработки лабиринтных |
обеспечивающей защиту подшипников от |
|
|
попадания в них загрязнений, поступающих |
||
|
уплотнений, поступающих с прорывающимся |
||
|
с прорывающимся через уплотнения воздухом |
||
|
через уплотнения воздухом в подшипники |
||
|
(применение защитных гребешков и т.п.). |
||
|
|
||
|
|
Обеспечение чистоты наддувающего воздуха |
|
|
|
(выбор мест отбора, применение |
|
|
|
воздухоочистителей) |
|
|
|
Применение масел, имеющих более высокую |
|
|
Температура деталей подшипников при работе |
рабочую температуру. |
|
Прорыв масляной |
Снижение температуры деталей подшипников |
||
превышает максимально-допустимую рабочую |
|||
пленки |
(применение теплоизоляции). Применение |
||
температуру масла |
|||
|
теплообменников, снижающих температуру масла |
||
|
|
||
|
|
и наддувающего воздуха. |
|
Повышенные |
Работа подшипника с нагрузкой, превышающей |
Стабилизация действующей на подшипник |
|
нагрузки. |
|||
контактные |
расчетную. |
||
Применение подшипника с оптимальным зазором, |
|||
напряжения |
Выборка зазора в подшипнике при работе |
||
исключающим работу подшипника с натягом. |
|||
|
|
||
|
|
|
|
|
|
Стабилизация действующей на подшипник |
|
Прижоги при |
Отсутствие нагрузки на подшипник. |
нагрузки. |
|
проскальзывании |
Применение подшипников специальной |
||
|
|||
|
|
конструкции. |
|
|
Наличие в материале подшипников |
Применение подшипников из сталей |
|
|
электрошлакового и вакуумного (двойного |
||
|
неметаллических включений |
||
Дефекты материала |
вакуумного) переплава |
||
|
|||
|
|
||
|
Соблюдение технологии изготовления |
||
подшипников |
|
||
Прижоги на деталях подшипников при |
подшипников. Внедрение неразрушающих видов |
||
|
|||
|
шлифовании. |
контроля для выявления повышенных остаточных |
|
|
|
напряжений. |
|
Разрыв сепаратора |
Работа подшипника с перекосом |
Устранение перекоса при работе подшипника. |
|
|
|
|
|
|
Потеря посадочного натяга на валу, |
Снижение температуры деталей подшипников. |
|
|
проворачивание подшипника в корпусе вследствие |
||
|
Оптимизация подачи масла. |
||
|
неправильно выбранной посадки подшипника, |
Применение подшипников из теплостойкой стали. |
|
|
либо ослабление затяжки гайки. |
||
|
|
||
Фреттинг-коррозия |
|
|
|
Потеря посадочного натяга на валу, |
|
||
|
|
||
|
проворачивание подшипника в корпусе, |
Увеличение посадочного натяга. |
|
|
вследствие увеличения размеров подшипников |
||
|
Увеличение момента затяжки гайки. |
||
|
при работе с температурой, превышающей |
||
|
|
||
|
рабочую (для сталей ШХ15, 95Х18). |
|
|
|
Работа подшипников на загрязненном масле |
Применение в маслосистеме фильтров более |
|
Износ подшипников |
тонкой очистки |
||
|
|||
|
Работа подшипников с проскальзыванием |
См. прижоги при проскальзывании |
|
|
|
|
|
Коррозия |
Несоблюдение правил хранения и консервации, |
Соблюдение правил хранения и консервации |
|
как подшипников, так и двигателей в целом. |
|||
|
|
184

Глава 4 - Силовые схемы ГТД
от узлов подшипников устанавливаются фильтрысигнализаторы и магнитные сигнализаторы стружки, которые в случае появления стружки в масле дают сигнал оповещения в кабину пилота. Также
âлиниях откачки масла устанавливаются магнитные пробки, которые регулярно осматриваются в процессе эксплуатации для контроля появления стружки. Появление стружки на магнитной пробке позволит точно определить место расположения дефектного подшипника, т.к. каждая магнитная пробка конструктивно привязана к линии откачки от конкретной опоры (подшипника).
Кроме того, в настоящее время, например, на двигателе ПС-90А внедрен периодический контроль проб масла из двигателя для определения в нем количества металла. Увеличение количества металла
âмасле является сигналом для проявления особого внимания к работе опор двигателя, ужесточению контроля другими методами диагностики, а в слу- чае превышения установленной нормы двигатель может быть отстранен от эксплуатации.
4.4.5 – Элементы систем обеспечения работоспособности подшипников
Конструктивно опора ротора ГТД представляет сложный узел, в который кроме силовых элементов входят и отдельные элементы систем обеспече- ния работоспособности подшипников, а именно:
- детали систем смазки подшипников;
-детали уплотнений масляных полостей;
-детали системы наддува уплотнений и охлаждения опоры.
Конструктивные особенности силовых элементов опор (корпусная и роторная части опоры, подшипник) рассмотрены в предыдущих разделах.
Âэтом разделе остановимся более подробно на работе и конструктивном исполнении деталей систем, обеспечивающих оптимальные условия работы наиболее нагруженной части опоры – подшипника.
Надежная и безотказная работа подшипников роторов ГТД во многом обеспечивается организацией подачи масла в узлы опор. Масло, подаваемое в больших количествах на подшипники (от нескольких десятков до нескольких сотен килограммов в час в зависимости от размера подшипника, частоты вращения ротора, места расположения и величины воспринимаемых им нагрузок), предназначено не только для смазки трущихся ча- стей, но и для отвода от них тепла.
В условиях работы на двигателе рост температуры подшипника обусловлен «внутренним» нагревом подшипника и внешним подводом тепла. «Внутренний» нагрев подшипников качения вызы-
вается упругой деформацией тел качения и беговых дорожек колец при приложении к ним нагрузок. При этом происходит деформация нагружаемых участков и последующее возвращение их в исходное состояние. Внутреннее трение между частицами металла в таком процессе приводит к выделению тепла. Кроме того, подшипники, расположенные
â«горячих зонах» двигателя (в районе камеры сгорания и турбины), испытывают значительный дополнительный подогрев от горячих деталей, что приводит к необходимости организации повышенного теплосъема с помощью прокачиваемого масла.
Максимальная эффективность работы подшипника достигается при постоянном наличии масляной пленки между поверхностями контакта наружного и внутреннего кольца и телами качения. Для того, чтобы выполнить это условие и обеспе- чить постоянное наличие масляной пленки желательно обеспечить прямую и непрерывную пода- чу масла на контактирующие поверхности деталей подшипника.
Практика показывает, что для этой цели луч- ше подавать масло в виде струек через калиброванные отверстия в зазор между внутренним кольцом подшипника и сепаратором. В этом случае масло хорошо омывает рабочую поверхность внутреннего кольца, поверхности тел качения, под действием центробежных сил попадает на беговую дорожку наружного кольца, омывает ее и вытекает
âмасляную полость опоры. Пример такого конструктивного решения представлен на Рис. 4.4.7.1_5.
Весьма эффективна подача масла на тела ка- чения через отверстия во внутреннем кольце подшипника. Но конструктивно решить эту задачу значительно сложнее, так как необходимо организовать подвод масла через вращающийся вал (см. Рис. 4.4.7.1_2).
Надежность работы подшипников в значи- тельной степени зависит от уровня и равномерности нагревания деталей подшипника. Разность температур между внутренними и наружными кольцами и по ширине колец подшипников должна быть минимальной для исключения искажения формы рабочих поверхностей подшипников из-за температурного градиента. Для обеспечения равномерного охлаждения подшипников подвод масла рекомендуется организовывать с двух сторон (см. Рис. 4.4.7.1_6).
Вокруг каждой опоры детали и узлы ГТД создают «замкнутое» пространство, в котором организуются процессы подачи масла на подшипники и его откачки - масляную полость опоры. К масляным полостям предъявляются специфические требования:
185

Глава 4 - Силовые схемы ГТД
1.Для исключения коксования масла температура деталей в масляных полостях опор не должна превышать предельно допустимую температуру масла на всех режимах работы двигателя. Выполнение этого требования обеспечивается постановкой теплозащитных экранов или кожухов на деталях масляной полости, введением охлаждения деталей опоры продувкой относительно холодным воздухом.
2.Внутри масляных полостей не должно быть малоподвижных объемов масла, а также застойных зон. Конструкция деталей внутри масляной полости должна исключать наличие глухих отверстий
è«карманов».
3.Масляные полости опор должны обладать необходимым объемом, не позволяющим переполнять их масляно-воздушной смесью, образующейся при работе подшипника. Форма масляных полостей, расположение и площадь каналов откачки должны обеспечивать немедленное удаление масляновоздушной смеси из рабочей зоны подшипника. Для полного удаления масла отверстие для слива
èоткачки должно быть расположено в самой нижней точке масляной полости. Необходимо учитывать, что объем принудительно откачиваемой мас- ляно-воздушной смеси примерно в четыре раза больше, чем объем масла, подаваемого в подшипник.
4.Масляные полости, расположенные в «горячих» зонах двигателя, должны иметь минимально возможную площадь поверхности с целью снижения величины тепловых потоков, передаваемых через стенки.
5.Уплотнения масляных полостей должны обеспечивать надежную защиту, с одной стороны, воздушных полостей двигателя от попадания масла, а также его паров и аэрозолей, а с другой стороны – самих масляных полостей от попадания в них загрязнений, поступающих с прорывающимся че- рез уплотнения воздухом.
6.При применении наддува лабиринтных уплотнений масляных полостей должен обеспечи- ваться положительный перепад давлений на всех режимах работы двигателя, (включая переменные), т.е. давление в масляной полости всегда должно быть ниже давления наддува.
Подробно конструкция, расчет и особенности работы уплотнений масляных полостей рассмотрены в главе 18, а особенности работы системы наддува и охлаждения опор - в главе 12.
В разделе 4.4.7 на примере российского двигателя ПС-90А и американского двигателя РW2037 показаны различные варианты конструктивного исполнения опор.
4.4.6 – Проектирование опор ГТД
Опоры ГТД, как объект проектирования, представляют собой комплекс, состоящий из механических компонентов конструкции двигателя, а также элементов систем обеспечения работоспособности подшипников. Основные элементы опор ГТД представлены на Рис. 4.4.6_1.
Одной из основных особенностей опор ГТД является их глубокая геометрическая и функциональная интеграция с конструкцией двигателя и его систем, причем это касается как силовых элементов, так и систем обеспечения работоспособности подшипников. Границы между опорами и остальными элементами двигателя могут быть выделены, как правило, только условно. Поэтому разработка опор должна проводиться одновременно с разработкой как отдельных узлов, систем, так и двигателя в целом на каждом этапе проектирования ГТД.
Разработка опор ГТД представляет собой комплекс конструкторских, расчетных и экспериментальных работ, включающий:
1.Проектирование элементов опор (силовых элементов, оболочек масляных и воздушных полостей, элементов подвода масла к подшипникам
èотвода его из масляных полостей опор, уплотнений и т.д.).
2.Проектирование или подбор подшипников.
3.Расчет теплового состояния опор.
4.Расчет напряженно-деформированного состояния элементов опор.
5.Экспериментальные исследования отдельных элементов опор и систем обеспечения работоспособности подшипников на специальных установках или двигателях.
Следует обратить внимание, что приведенный перечень отражает лишь состав работ, при этом он не определяет хронологическую последовательность их выполнения.
Например, экспериментальные исследования
èдоводка отдельных элементов опор и систем обеспечения работоспособности подшипников на специальных установках могут проводиться на любом этапе проектирования двигателя. То же самое можно сказать и о расчетах отдельных элементов опор.
4.4.6.1 – Исходные данные, их разработка
Этапу собственно проектирования опор ГТД предшествует этап формирования исходных данных, включающих в себя параметры силового взаимодействия элементов опор, их теплового состояния, а также требования по обеспечению экологических или
186

Глава 4 - Силовые схемы ГТД
Рисунок 4.4.6_1 – Основные элементы опор ГТД
ресурсных показателей, надежности, весовых характеристик и т.д.
Исходные данные на проектирование опор могут быть представлены в виде трех основных групп:
1.Определяемые национальными, международными, а также отраслевыми стандартами, правилами и т.д.
2.Определяемые внешними условиями функционирования опор, которые в свою очередь подразделяются на:
- определяемые условиями эксплуатации ГТД
âсоставе объекта;
- определяемые типом, конструкцией, параметрами, а также технико-экономическими показателями ГТД.
3. Определяемые условиями обеспечения заданных показателей ресурса и надежности под-
шипников, весовых характеристик.
В исходные данные первой группы включе- ны общие требования, направленные на обеспе- чение безопасной эксплуатации, охраны окружающей среды и т.п. Как правило, они не могут корректироваться разработчиком ГТД. Применительно к опорам ГТД это может быть, например, порядок и методика установления ресурса подшипникам.
Исходные данные второй группы формируются на основе технического задания на разработку ГТД, результатов предварительной проработки конструкции двигателя, результатов газодинамического и прочностного расчетов, опыта эксплуатации аналогов и т.д. Эта часть исходных данных может частично корректироваться в процессе проектирования.
187

Глава 4 - Силовые схемы ГТД
Исходные данные, определяемые условиями эксплуатации ГТД в составе объекта применения, обусловлены следующими факторами:
-типом и условиями эксплуатации объекта применения ГТД (для авиационных ГТД определяются типовым полетным циклом);
-диапазоном возможных перегрузок при работе, монтаже и транспортировке;
-условиями и частотой запуска и останова;
-характером переменных режимов работы;
-диапазоном возможных положений осей ГТД при работе, монтаже и транспортировке;
-типом и маркой масел;
-составом и параметрами атмосферного воз-
äóõà.
Исходные данные, определяемые типом, конструкцией, параметрами, обусловлены следующими факторами:
-выбранной силовой схемой и схемой расположения опор ГТД;
-предельными внешними габаритами опор;
-взаимными смещениями и перекосами осей ротора (роторов) и статора ГТД в сечениях посадочных мест подшипников;
-осевыми и радиальными нагрузками, передаваемыми от ротора (роторов) на статор;
-частотами вращения роторов;
-параметрами воздуха во вторичных воздушных системах;
температурами и массами смежных роторных
èстаторных деталей.
Исходные данные третьей группы определяются условиями обеспечения заданных показателей ресурса и надежности подшипников. Как правило, сюда относятся:
-надежность ГТД;
-контролепригодность ГТД;
-стоимости жизненного цикла ГТД;
-масса составных частей ГТД.
В исходных данных, в частности, могут устанавливаться предельно-допустимые значения следующих параметров:
-внешних нагрузок, действующих на подшипники и их элементы;
-окружных скоростей в подшипниках (скоростной параметр d•N);
-взаимных перекосов колец подшипников;
-отклонений размеров и формы посадочных мест под подшипники;
-температуры деталей подшипников;
-разности температур колец подшипников между собой и по ширине кольца;
-размеров и концентрации твердых частиц загрязнений в воздухе, поступающем в масляные
полости опор из системы наддува уплотнений;
-значений физико-химических характеристик
èчистоты масла, поступающего к поверхностям качения подшипников;
-температуры воздуха, поступающего в масляные полости опор из системы наддува уплотнений;
-температуры поверхностей, контактирующих с маслом.
На основе исходных данных разрабатывается техническое задание на проектирование опор, в котором отражаются наиболее важные требования
èпоказатели, в частности, значения требуемой рас- четной долговечности подшипников. Кроме этого, в техническом задании указываются дополнительные специальные требования к конструкции и технологии сборки опор.
4.4.6.2 – Определение нагрузок
Нагрузки, действующие на подшипник в рабочих условиях, в наибольшей степени определяют выбор подшипника и его работоспособность. В зависимости от характера возникновения можно различать нагрузки:
1)двигательные, обусловленные конструкцией и процессами, происходящими в двигателе при его работе:
- от массы ротора, приходящейся на его опору; - от центробежных сил вращающегося ротора
ñучетом дисбалансов, в том числе от центробежных сил шаров или роликов подшипника;
- от осевой силы ротора (суммы осевых сил, действующих на элементы ротора);
- от механических колебаний ротора (вибрации), передающихся на опору, с частотами, кратными частоте вращения ротора;
- от неравномерного нагрева вала, колец подшипника, корпуса и связанного с этим дополнительного взаимодействия элементов подшипника;
2)самолетные, возникающие при изменении величины или направления скорости полета и обусловленные эволюцией самолета:
- эксплуатационными перегрузками; - гироскопическими моментами роторов.
Современные расчетные методики подбора подшипников и определения их долговечности ча- стично или в полной мере учитывают влияние двигательных и самолетных нагрузок.
В стационарных наземных установках нагрузки на опоры ГТД, связанные с перемещениями двигателя в пространстве, отсутствуют.
Рассмотрим несколько подробнее содержание конструкторских, расчетных и экспериментальных работ, выполняемых при разработке опор ГТД.
188

Глава 4 - Силовые схемы ГТД
4.4.6.3 – Конструирование элементов опор
Конструирование собственно опор производится в процессе конструирования как отдельных узлов (компрессора, турбины и т.д.), так и двигателя в целом и состоит из следующих этапов:
-выбор силовой схемы и схемы расположения опор двигателя;
-выбор типа исполнения для каждой из опор (упругая, упруго-демпферная и т.д.);
-определение посадочных диаметров валов;
-определение внешних предельных габаритов
îïîð;
-выбор типа уплотнений масляных полостей
îïîð;
-определение внешних механических нагрузок (нагрузок между ротором и статором);
-предварительное определение внешних габаритов подшипников;
-определение температуры деталей и узлов, расположенных в непосредственной близости от опор;
-определение параметров воздуха в полостях, где будут расположены опоры;
-выбор способа подвода масла к подшипни-
êàì;
-выбор общей схемы маслосистемы двигателя;
-выбор схемы системы наддува уплотнений масляных полостей и охлаждения опор.
При конструировании опор разработчики ча- сто руководствуются соображениями минимального проектного риска и отдают предпочтение схемам, хорошо отработанным на прототипах. При этом принимаются во внимание следующие ограничения:
-по окружным скоростям в подшипниках (скоростной параметр d•N);
-по внешним нагрузкам, действующих на подшипники и их элементы.
При выполнении эскизных или рабочих компоновок опор также принимаются меры по обеспечению возможно более полного соответствия конструкции исходным требованиям на проектирование, а именно:
-по исключению недопустимых взаимных перекосов колец подшипников, возникающих вследствие взаимных смещений и перекосов осей ротора (роторов) и статора ГТД в сечениях посадочных мест подшипников;
-ïî максимально-возможному снижению внешнего теплоподвода к подшипникам, а также температуры поверхностей, контактирующих с маслом;
-по обеспечению заданных значений физико-
химических характеристик и чистоты масла, поступающего к поверхностям качения подшипников;
-по защите подшипников от попадания на их рабочие поверхности твердых частиц загрязнений содержащихся в воздухе, поступающем в масляные полости опор из системы наддува уплотнений;
-по исключению попадания на рабочие поверхности подшипников продуктов приработки (в частности, по недопустимости работы подшипников
â«масляной ванне» во всем предусмотренном условиями работы диапазоне положений осей ГТД);
-по исключению задержки продуктов износа (стружки) в масляных полостях опор.
Результатом конструирования опор являются их эскизные или рабочие компоновки (в зависимости от этапа проектирования ГТД), на основе которых определяются геометрические параметры различных элементов, необходимые для проектирования или подбора подшипников, а также для выполнения расчетов теплового и напряжен- но-деформированного состояния опор.
4.4.6.4 – Проектирование или подбор подшипников
Проектирование или подбор подшипников производится на основании технического задания,
âкотором, в частности, оговариваются:
-значения расчетной долговечности подшипников;
-диапазон внешних осевых и радиальных нагрузок;
-диапазон рабочих температур деталей подшипников;
-диапазон рабочих частот вращения роторов;
-тип, марка, а также значения физико-хими- ческих характеристик и чистоты масла;
-предельные внешние габариты подшипников, значения посадочных диаметров валов и корпусов и т.д.
Выбор подшипников ГТД и определение их расчетной долговечности производится в соответствии с ГОСТ 18855-94 (ИСО 251-90) [4.7.5], Спра- вочником-каталогом [4.7.6] и Ограничительным перечнем подшипников [4.7.7] по методике, изложенной в [4.7.8].
Расчет на долговечность подшипников производится по формуле:
ãäå Lh |
Lh = (Ñr /Pr)α106 / (60n) |
(4.4.6.4-1) |
- расчетная долговечность, ч; |
||
n |
- частота вращения подшипника, |
|
Ñr |
îá/ìèí; |
|
- радиальная динамическая |
|
189

Глава 4 - Силовые схемы ГТД
грузоподъемность подшипника, Н; Pr - эквивалентная динамическая
нагрузка на подшипник, Н; α=3 - для шарикоподшипников, α=3,33 - для роликоподшипников.
Динамическая радиальная грузоподъемность подшипников определяется следующим образом:
(4.4.6.4-2) ãäå ÑrÊÀÒ - базовая динамическая радиальная
грузоподъемность подшипника по каталогу [4.7.6], Н;
- коэффициент влияния качества, зависит от точности изготовления, материала деталей и конструкции подшипника (ÊÊÀ× =1,0…1,8);
- коэффициент влияния тонкости фильтрации масла, (ÊÔ =0,9…1,3);
- коэффициент влияния окружной скорости поверхностей тел качения, зависит от величины dmN (dm - диаметр окружности центров тел качения, N - ча- стота вращения подшипника, об/мин)
(ÊdN =1…1,2);
- коэффициент влияния вязкости масла, (Ê =0,8…1,2)
Эквивалентная динамическая радиальная нагрузка Ðr вычисляется по формуле:
- для шарикового подшипника
Ðr=(VÕFr + YFà)ÊÁÊ , (4.4.6.4-3)
- для роликового подшипника
Ðr=VFrÊÁÊ , (4.4.6.4-4)
ãäå Fr,Fà - соответственно радиальная и осевая нагрузки на подшипник, постоянные по величине и направлению, нагрузка на подшипники определяется как реакция в опорах от усилий на роторе. Расчетная долговечность подшипников определяется для средней за полетный (или рабочий) цикл нагрузки;
Õ è Y - коэффициенты радиальной и осевой нагрузки соответственно, определятся по справочнику [4.7.6] в зависимости от конструкции подшипника;
V=1 - при вращении внутреннего кольца подшипника относительно направления нагрузки;
V=1,2 - при вращении наружного кольца подшипника;
ÊÁ |
- коэффициент безопасности, |
|
учитывающий вибрационные перегруз- |
|
ки в зависимости от места установки |
Ê |
подшипника (ÊÁ = 1…1,3); |
- температурный коэффициент, |
|
|
учитывающий теплостойкие свойства |
материала подшипника, Ê = 1,0 для подшипников с твердостью поверхностей качения колец и тел качения HRC ≥ 59 и температурой отпуска ко-
лец и тел качения tÎÒÏ ≤ 225 °C при рабочей температуре tÐÀÁ ≤ 180 °C.
Проектирование подшипников может выполняться или специализированными фирмами, или непосредственно самим разработчиком ГТД. Подбор готовых подшипников осуществляется разработчиком ГТД по согласованию с разработчиком или поставщиком упомянутых подшипников. Результатом проектирования или подбора подшипников являются подробные данные о конфигурации, размерах, а также материалах их основных компонентов (колец, тел качения, сепараторов), необходимые для выполнения расчетов теплового и нап- ряженно-деформированного состояния опор.
4.4.6.5 – Расчет теплового состояния опор
Âпроцессе работы двигателя детали опор,
âтом числе и подшипники, подвергаются нагреву. Причинами нагрева являются внутреннее тепловыделение в подшипнике, обусловленное процессами трения, а также воздействие внешних тепловых потоков от расположенных в непосредственной близости от опор нагретых деталей ротора и статора. Источником внешних тепловых потоков может являться также горячий воздух, находящийся в полостях, непосредственно примыкающих к опоре.
Тепло от подшипников отбирается маслом, которое подается на смазку подшипников. Таким же образом осуществляется отвод тепла и от других омываемых маслом элементов опоры, таких как силовых элементов, внутренних поверхностей оболочек масляных полостей, элементов валов, контактных уплотнений и т.д.
Âрезультате происходящих сложных процессов теплообмена между деталями опор, другими деталями ГТД, а также потоками воздуха и масла, устанавливается определенный уровень температуры каждого из перечисленных компонентов, уча- ствующих в процессах теплообмена. Температура компонентов при этом, очевидно, будет зависеть как от режима работы ГТД, так и от внешних ус-
190

Глава 4 - Силовые схемы ГТД
ловий (например, от температуры атмосферного воздуха, температуры масла на входе в двигатель и т.д.). Работоспособность подшипников в течение заданного ресурса может быть обеспечена при условии, если уровень температуры их деталей, а также масла в зоне контакта поверхностей качения не будет превышать предельно-допустимых значений, которые, в основном, определяются:
-материалами деталей подшипников;
-типом и марками применяемых масел. Предельно-допустимые значения температу-
ры деталей подшипников и масел принимаются во внимание разработчиком ГТД при назначении максимальных рабочих температур упомянутых компонентов. Максимальные рабочие температуры, как указано выше, затем вносятся в техническое задание на проектирование подшипников и учитываются при выборе конфигурации, размеров, а также материалов их основных деталей.
Для проектирования подшипника, наиболее подходящего для данной конкретной опоры, часто оказывается недостаточным знание только максимальной рабочей температуры его деталей. В ряде случаев требуется проведение подробного анализа влияния изменения температуры деталей подшипника на его работу по всему диапазону режимов полетного цикла. Для высоконагруженных скоростных подшипников, кроме этого, иногда бывает необходимым выполнить оценку изменения температуры деталей и на неустановившихся режимах работы двигателя. Эти температуры необходимы для оценки изменения радиальных зазоров и углов контакта в подшипниках, которыми, в свою очередь, определяются возникающие в подшипниках внутренние нагрузки. И, наконец, радиальные зазоры и углы контакта в подшипниках, особенно «горячих» опор, могут определяться не только температурой самих колец подшипников, но и температурными деформациями непосредственно сопряженных с кольцами подшипников деталей двигателя (силовых элементов статора, валов и т.д.).
Сказанным выше, в основном, и обусловлена необходимость выполнения расчета теплового состояния при проектировании опор ГТД.
Расчет теплового состояния опор выполняется с целью определения:
-температуры деталей подшипников;
-температуры непосредственно сопряженных
ñкольцами подшипников деталей двигателя (силовых элементов статора, валов и т.д.);
-температуры масла на выходе из опор. Результаты расчета теплового состояния опор
в дальнейшем используются для оценки соответствия выбранных конструкции и параметров как
собственно опор, так и систем обеспечения работоспособности подшипников (маслосистемы и воздушной системы наддува уплотнений и охлаждения) требованиям по поддержанию рабочей температуры подшипников, масла, деталей, контактирующих
ñмаслом и т.д. в заданных пределах. Кроме этого, результаты расчета теплового состояния используются для анализа напряженно-деформированного состояния деталей опор.
Расчет теплового состояния опор на стадии проектирования проводится, как правило, как проверочный в следующем порядке:
1)разработка исходных данных для расчета;
2)расчет рабочей температуры подшипников, масла, деталей, контактирующих с маслом, силовых элементов и т.д. на всех интересующих режимах работы двигателя;
3)анализ результатов расчета и разработка (при необходимости) рекомендаций по корректировке конструкции и параметров опор и систем обеспечения работоспособности подшипников.
В качестве исходных данных для расчета принимаются:
- данные по конфигурации и размерам конструктивных элементов опоры, полученные по результатам эскизной или рабочей компоновки;
- данные по температуре расположенных в непосредственной близости от опор деталей ротора и статора, а также по температуре воздуха в полостях, непосредственно примыкающих к опоре, полу- ченные на основании анализа теплового состояния узлов двигателя;
- данные по параметрам воздуха в системе наддува и охлаждения опор, полученные по результатам гидравлического расчета этой системы (подробнее о системе наддува и охлаждения опор см. раздел 12.5);
- данные по параметрам маслосистемы (тип и марка масла, температура масла на входе в опору, прокачка масла через опору), полученные по результатам анализа прототипа или по результатам экспериментальных исследований на двигателях или специальных установках;
- данные по рабочим и предельно-допустимым значениям температуры деталей подшипников;
- данные по предельно-допустимым значениям температуры непосредственно сопряженных
ñкольцами подшипников деталей двигателя (силовых элементов статора, валов и т.д.);
- данные по предельно-допустимым значениям температуры масла на выходе из опор.
Перечисленные исходные данные используются для задания граничных условий, необходимых для расчета температуры участвующих в процессе
191

Глава 4 - Силовые схемы ГТД
теплообмена компонентов опор и систем обеспече- ния работоспособности подшипников, в первую очередь температуры деталей подшипников и температуры масла на выходе из опор. В основу рас- чета положен принцип определения температуры компонентов, участвующих в процессе теплообмена, как результата совместного воздействия на них внешних тепловых потоков и внутреннего тепловыделения в подшипниках. Для расчета внешних тепловых потоков используются методики, аналогичные методикам, применяемым при расче- те систем охлаждения турбин (см. раздел 8.3). Рас- чет внутреннего тепловыделения в подшипниках производится на основе методик анализа теплового режима подшипников, приведенных, например, в [4.7.9]. При расчете теплового состояния опор применяют пакеты прикладных программ для тепловых расчетов, например ANSYS. Результаты теплового расчета опоры роликоподшипника КВД авиационного ТРДД на одном из режимов полетного цикла, выполненные с применением пакета ANSYS, представлены на Рис. 4.4.6.5_1.
Для удобства работы результаты расчета представлены в виде графического изображения опоры с цветовой индикацией. Шкала для расшифровки цветовой гаммы, привязки ее к значениям температуры приведена рядом с изображением. Зона максимального нагрева подшипника расположена на контактной поверхности роликов с беговой дорожкой внутреннего кольца подшипника. Необходимо обратить внимание на довольно большую
неравномерность температурного состояния подшипника (относительно холодная наружная обойма, неравномерный прогрев внутреннего кольца). Все это необходимо учитывать при подборе или проектировании подшипников, анализе изменения рабочих зазоров при работе.
Анализ результатов теплового расчета опор сводится, прежде всего, к сравнению полученных значений температуры деталей подшипников с температурами этих деталей, указанными в техническом задании на проектирование. Кроме этого сравниваются полученные значения температуры масла на выходе из опоры, а также температуры поверхностей деталей, контактирующих с маслом, с пре- дельно-допустимыми значениями этих параметров. В случае расхождения заданных и полученных в расчете значений температуры производится корректировка конфигурации и параметров элементов опор и систем обеспечения работоспособности подшипников, которая включает:
-изменение температуры масла на входе в опору;
-изменение величины прокачки масла через опору;
-изменение температуры и расхода воздуха, охлаждающего опору;
-изменение конструкции собственно опоры (элементов теплоизоляции, элементов подвода масла к подшипникам и т.д.).
После соответствующей корректировки исходных данных проводится повторный расчет теплового состояния опоры и повторный анализ ре-
Рисунок 4.4.6.5_1 – Результаты расчета теплового состояния опоры роликоподшипника КВД авиационного ТРДД 1 - корпус опоры; 2 – наружное кольцо подшипника; 3 – внутреннее кольцо подшипника;
4 – ролики; 5 – вал; 6 – упруго-демпферная опора
192

Глава 4 - Силовые схемы ГТД
зультатов расчета. Подобные циклы повторяются до тех пор, пока не будет получена удовлетворительная сходимость расчетных и заданных величин температуры компонентов, участвующих в процессе теплообмена. На основании результатов расче- та теплового состояния опор производится соответствующая корректировка исходных требований к маслосистеме (например, по величинам теплосъема в топливно-масляных и воздушно-масляных теплообменниках, производительности масляных насосов и т.д., (подробнее о маслосистеме см. раздел 12.6.), а также исходных требований к воздушной системе охлаждения опор (температуре, расходу охлаждающего воздуха, конфигурации схемы охлаждения и т.д.). Результаты расчета теплового состояния опор используются также в качестве исходных данных для расчета НДС опор.
4.4.6.6 – Расчет напряженно-дефор- мированного состояния элементов опор
Расчет напряженно-деформированного состояния (НДС) элементов опор в общем случае сводится к решению двух задач:
1.Определение НДС силовых элементов опор;
2.Определение внутренних зазоров в подшип-
никах.
При расчете НДС силовых элементов опор для различных режимов полетного цикла производится оценка запасов прочности силовых элементов
по внешним нагрузкам, сохранения посадок колец подшипников в корпусах и на валах, осевой затяжки «пакетов» деталей опор с наружными и внутренними кольцами подшипников.
Расчет внутренних зазоров в подшипниках производится на основе результатов расчета НДС элементов опор. По результатам этого расчета определяются:
-для шарикоподшипников – диапазон изменения углов контакта;
-для роликоподшипников - диапазон изменения радиальных зазоров.
На примере расчета НДС опоры роликоподшипника ТНД авиационных ГТД, выполненных
ñприменением пакета ANSYS, рассмотрим последовательность выполнения отдельных этапов этой работы.
Сначала были сформированы исходные данные, представляющие описание условий работы деталей опоры для разных режимов работы двигателя. Эти исходные данные базируются на результатах предварительных тепловых расчетов модулей двигателя, опыта эксплуатации аналогов и т.д. В нашем случае предварительная расчетная модель температурного состояния деталей опоры и давлений в ее полостях для максимального режима представлена на Рис. 4.4.6.6_1.
Для расчета НДС в пакете ANSYS создана конечно-элементная модель узла опоры, представленная на Рис. 4.4.6.6_2 (подробно о создании ко- нечно-элементных моделей см. в разделе 14.1).
Рисунок 4.4.6.6_1 – Исходные данные. Давление в полостях и температура деталей опоры роликоподшипника ТНД на максимальном режиме
193

Глава 4 - Силовые схемы ГТД
Расчет НДС выполнен в осесимметричной |
На следующем этапе проведена оценка темпе- |
постановке с учетом взаимодействия деталей опо- |
ратурной деформации деталей опоры на максималь- |
ры между собой. Температура деталей принима- |
ном режиме работы двигателя (см. Рис. 4.4.6.6_4). |
лась по окружности равномерной. Проведенный |
Она показала, что из-за различного расширения |
анализ НДС для условий монтажа (т.е. для «холод- |
деталей переходная посадка кольца роликоподшип- |
ной» опоры) показал, что напряженным местом |
ника трансформируется в натяг. Все эти данные |
является область переднего паза под уплотнение |
необходимы для выполнения расчета НДС в рабо- |
обоймы демпфера (Рис. 4.4.6.6_3). |
чих условиях. |
Рисунок 4.4.6.6_2 – Опора роликоподшипника ТНД. Конечно-элементная модель 1 – корпус; 2 – опора; 3 – обойма демпфирующая; 4 – кольцо наружное; 5 – крышка; 6 – фланец лабиринта; 7 – гайка; 8 – лабиринт
Рисунок 4.4.6.6_3 – НДС деталей опоры роликоподшипника ТНД при монтаже
194

Глава 4 - Силовые схемы ГТД
НДС узла опоры на максимальном режиме представлено на Рис. 4.4.6.6_5. На рисунке хорошо видны места концентрации напряжений, определена их величина. На базе полученных результатов производится расчетная оценка долговечности для наиболее нагруженных мест конструкции. Расчетная долговечность сравнивается с заданной в техническом задании.
Результаты расчета используются для оценки внутренних усилий в подшипниках, а также для
Рисунок 4.4.6.6_4 – Радиальные температурные перемещения деталей опоры роликоподшипника ТНД на максимальном режиме
уточнения изменения температуры колец от внутреннего тепловыделения в подшипниках. По результатам расчета НДС опор могут вноситься соответствующие корректировки как в конструкцию силовых элементов опор, так и в конфигурацию и размеры деталей подшипников.
4.4.6.7 – Экспериментальные исследования отдельных элементов опор
Основными целями проведения экспериментальных исследований опор, проводимых на этапе проектирования ГТД являются:
-уточнение исходных данных на проектирование опор и систем обеспечения работоспособности подшипников;
-уточнение методик теплового расчета опор. Экспериментальные исследования прово-
дятся или на специальных установках, или на двигателях-прототипах. В процессе исследований на физической полноразмерной модели проектируемой опоры определяется зависимость различных параметров (например, температуры колец подшипников, температуры масла на выходе из опоры) от частоты вращения, нагрузки, прокачки масла, внешнего подогрева и т.д. Подробнее с вопросами экспериментальных исследований опор на установках можно ознакомиться, например в [4.7.9].
Рисунок 4.4.6.6_5 – НДС деталей опоры роликоподшипника ТНД 1, 2, 3 - места концентрации напряжений.
195

Глава 4 - Силовые схемы ГТД
4.4.7 – Конструктивное исполнение опор современных ГТД
Выбор силовой схемы ГТД, несмотря на необходимость выполнения общих требований изложенных выше, во многом определяется традициями и практикой работы разработчика двигателя. Наиболее удачные конструктивные решения, реализованные в ранних конструкциях ГТД и проверенные временем, тиражируются и развиваются
âпоследующих разработках. Как правило, накапливается бесценный опыт, существующий в виде конкретных рекомендаций:
-осевая нагрузка через радиально-упорные подшипники должна передаваться, предпочтительно, через бурты, выполненные за одно целое с валом и корпусом (пример такого исполнения корпусной детали можно увидеть на опоре шарикоподшипника ротора ВД двигателя ПС-90А – см. Рис. 4.4.7.1_5). При невозможности выполнить данное требование необходимо, чтобы элементы конструкции, через которые передается осевое усилие, обеспечивали стабильность биения опорных торцев
âзаданных пределах допуска в течение всего времени работы двигателя;
-при значительном влиянии допусков на долевые и угловые размеры (пакеты деталей, большие габаритные размеры и т.д.) необходимо предусмотреть индивидуальную регулировку соосности опор с применением клиновых и эксцентриковых регулировочных колец (регулирование соосности опор с помощью эксцентрикового кольца применяется на опоре роликоподшипника ТВД двигателя ÏÑ-90À – ñì. Ðèñ. 4.4.7.1_6);
-допуск соосности опор, оговоренный в конструкторской документации, должен быть обеспе- чен в течение всего времени эксплуатации;
-в случае, когда подшипник собирается с предварительным натягом, посадка выбирается таким образом, чтобы обеспечить оптимальные зазоры по телам качения с учетом теплового состояния деталей опоры. Подробнее об условиях выполнения этого требования можно ознакомиться в разделе 4.4.4.3;
-конструкции шариковых подшипников и их опор должны обеспечивать демонтаж подшипников без передачи усилия через тела качения;
-диаметр посадочного места под подшипник должен быть определен из условия обеспечения параметра d N, ãäå d - посадочный диаметр вала под подшипник или внутренний посадочный диаметр подшипника (мм), N - частота вращения вала (об/мин). Для подшипников из отечествен-
ной теплопрочной стали 8Х4В9Ф2-Ш (ЭИ347-Ш) d N ≤ 2,0 10 6 (мм об/мин), для подшипников из за-
рубежной теплопрочной стали М50Nil VIM VAR d N ≤ 2,4 10 6 (ìì îá/ìèí);
- максимальная температура опоры должна быть не менее, чем на 50 îС ниже температуры отпуска материала подшипников. При этом следует учитывать, что максимальную температуру опора может иметь уже после останова двигателя (из-за поступающего тепла от дисков турбины и т.п. при отсутствии охлаждения).
При температуре свыше 250 îС происходит активное разложение даже синтетических масел, оставшихся в масляной полости, а значит необходимо предусмотреть конструктивные решения по предотвращению перегрева опор после останова двигателя (теплозащитные покрытия, экраны, продувка холодным воздухом). Примеры реализации таких решений представлены на Рис. 4.4.7.1_5 и 8.1.2.4_2.
4.4.7.1 – Конструкция опор авиационных ГТД
Как показывает анализ существующих конструкций авиационных двигателей, при проектировании ГТД разработчики широко используют свой опыт, проверенные временем конструктивные решения, при обязательном выполнении тех общих требований к конструкции опор, о которых говорилось выше. Это наглядно можно увидеть на примерах российского двигателя ПС-90А и американского двигателя PW 2037.
Двигатель ПС-90А (см. Рис. 4.4.7_1) имеет трехопорную конструкцию роторов ВД и НД. На Рис. 4.4.7.1_1 показана схема расположения опор на двигателе ПС-90А Силовые схемы роторов и корпусов этого двигателя представлены в разделах 4.2 и 4.3 (см. Рис. 4.2_1 и 4.3_2).
Опора шарикоподшипника ротора НД (см. Рис. 4.4.7.1_2) расположена в «холодной» зоне и не требует специальных мероприятий по обеспечению теплового режима. На этой опоре происходит передача осевого усилия с ротора НД на корпус. В ней установлен радиально-упорный подшипник 1. На внутреннем кольце подшипника выполнен технологический бурт для съема подшипника при разборке. Наружное кольцо подшипника установлено в корпус 2. Внутреннее разъемное кольцо подшипника установлено на валу 3 ротора. Подача масла на шарикоподшипник осуществляется через форсунку 4 во внутреннюю коническую полость резьбовой втулки 5. Под действием центробежных сил во внутренней конической полости втулки создается масляная ванна, откуда масло по пазам в вале ротора поступает под внутреннее кольцо подшипника и через
196

Глава 4 - Силовые схемы ГТД
Рисунок 4.4.7.1_1 Двигатель ПС-90А. Схема расположения опор двигателя ПС-90А
отверстия в кольце – на тела качения. Уплотнения масляной полости осуществляется лабиринтами 6 и 7, причем на лабиринте выполнен маслоотбойный буртик. Для наддува лабиринтов используется воздух из противообледенительной системы двигателя.
На Рис. 4.4.7.1_3 показана промежуточная опора ротора НД. Роликоподшипник 1 установлен в разделительном корпусе 2 на упруго-демпферной опоре 3 типа «беличье колесо» (раздел 14.5.7). Подача масла на подшипник осуществляется че- рез форсунку 4.
Передняя опора ротора ВД (см. Рис. 4.4.7.1_4) также расположена в разделительном корпусе. Роликоподшипник 1 установлен на упруго-демпфер- ной опоре 2. Уплотнение масляной полости осуществляется лабиринтами 3 и 4, при этом производится наддув межлабиринтной полости воздухом из-за компрессора НД.
Все вышеуказанные опоры расположены в единой масляной полости разделительного корпуса с объединенной откачкой масла в нижней части.
Для снижения давления в масляной полости и обеспечения рабочего перепада давления на ла-
биринтных уплотнениях полость соединена с окружающей атмосферой через систему суфлирования. Подсоединение системы суфлирования производится в верхней части масляной полости разделительного корпуса.
Опора шарикоподшипника ротора ВД (см. Рис. 4.4.7.1_5) предназначена для передачи осевого усилия с ротора ВД на корпусные детали двигателя. В состав опоры входит радиально-упорный шарикоподшипник 1, имеющий разъемное внутреннее кольцо 2. Наружное кольцо 3 установлено в обойму 4, запрессованную в корпус 5 кожуха внутреннего камеры сгорания. Подача масла осуществляется через форсунки 6 в зазор между сепаратором 7 и внутренним кольцом подшипника. Уплотнение масляной полости производится лабиринтами 8 и 9, имеющими маслоотбойный буртик.
Опора расположена в зоне высоких температур, поэтому для нее предусмотрены особые меры по устранению перегрева – установка теплозащитного экрана 10 на наружных деталях масляной полости, а также введение продувки корпусных деталей относительно «холодным» воздухом. На первых двигателях воздух для охлаждения опоры брался из-за
197

Глава 4 - Силовые схемы ГТД
Рисунок 4.4.7.1_2 - Опора шарикоподшипника ротора НД 1 - радиально-упорный подшипник; 2 - корпус; 3 – вал ротора; 4 – форсунка; 5 – втулка; 6 и 7 – лабиринты
Рисунок 4.4.7.1_3 – Промежуточная опора ротора НД с роликоподшипником 1 – роликоподшипник; 2 - корпус;
3- упруго-демпферная опора;
4- форсунка
КНД, но как показал опыт эксплуатации, из-за низкого давления охлаждающего воздуха не удавалось реализовать надежный режим охлаждения опоры. В связи с этим отбор воздуха для охлаждения опоры стал производиться из-за седьмой ступени КВД, но с обязательным охлаждением в воздушном теплообменнике, расположенном в наружном контуре двигателя. Таким образом, вокруг опоры шарикоподшипника конструктивно сформирована полость 11,
Рисунок 4.4.7.1_4 - Передняя опора ротора ВД с роликоподшипником 1 – роликоподшипник; 2 - упруго-
демпферная опора; 3 и 4 - лабиринты
через которую пропускается охлаждающий воздух. Задняя опора ротора ВД (см.Рис. 4.4.7.1_6)
двигателя ПС-90А подробно описана в разделе 8.1.2.4 на примере конструктивно аналогичной опоры ТВД двигателя ПС-90А2 (см.Рис. 8.1.2.4_2). Опора шарикоподшипника и задняя опора ротора ВД, межвальный подшипник двигателя ПС-90А установлены в одной масляной полости, организованной кожухом вала камеры сгорания.
198

Глава 4 - Силовые схемы ГТД
Рисунок 4.4.7.1_5 - Опора шарикоподшипника ротора ВД 1 – шарикоподшипник; 2 - внут-
реннее кольцо; 3 - наружное кольцо; 4 - обойма; 5 - корпус кожуха внутренний камеры сгорания; 6 - форсунка; 7 - сепаратор;
8 и 9 - лабиринты; 10 - теплозащитный экран; 11 - воздушная полость
Âмасляной полости в нижней части находятся два трубопровода отвода масла (отдельно – для шарикоподшипника КВД и для роликоподшипника ТВД), причем в каждой линии откачки установлены элементы системы диагностики состояния подшипника – магнитный сигнализатор стружки
èдатчик температуры масла. Верхняя часть масляной полости соединена с окружающей атмосферой через систему суфлирования.
Âзадней опоре ротора НД (см. Рис. 4.4.7.1_7) расположен роликоподшипник 1. Подшипник установлен на «жестком» фланце 2, имеющем упругодемпферную опору 3. Фланец находится на задней опоре 4 двигателя. Подвод масла на роликоподшипник – принудительный через форсунки. Уплотнения масляной полости осуществляется лабиринтами 5 и 6. Роликоподшипник расположен в масляной полости задней опоры, в которой организованы откачка масла - в нижней части, и суфлирование с наружной атмосферой – в верхней части. В системе откачки масла установлены элементы диагностики подшипника – магнитная пробка и датчик температуры.
Двигатель PW2037 имеет двухопорную конструкцию ротора ВД и трехопорную конструкцию ротора НД. На Рис. 4.4.7.1_8 показана схема рас-
Рисунок 4.4.7.1_6 - Задняя опора ротора ВД с роликоподшипником
Рисунок 4.4.7.1_7 - Задняя опора ротора НД с роликоподшипником 1 - роликоподшипник; 2 - фла-
нец; 3 - упруго-демпферная опора; 4 - опора задняя двигателя; 5 и 6 - лабиринтные уплотнения
положения опор на двигателе PW2037.
Силовая схема роторов представлена в разделе 4.2 (см. Рис. 4.2_1).
Рассматриваемые двигатели – российский ПС-90А и американский PW2037 – являются двигателями одного класса и имеют много общих конструктивных решений в исполнении опор, но остановимся на отличиях. В первую очередь у двигателя PW2037 необходимо отметить следующее:
199

Глава 4 - Силовые схемы ГТД
Рисунок 4.4.7.1_8 - Двигатель PW2037. Схема расположения опор на двигателе PW2037
-для ротора ВД принята двухопорная силовая схема, причем опора шарикоподшипника размещена в относительно холодном месте перед КВД;
-уплотнения масляных полостей осуществлены с помощью контактных уплотнений;
-подшипники опор специально спроектированы с учетом применения в конкретной опоре.
На Рис. 4.4.7.1_9…4.4.7.1_13 показаны исполнения опор двигателя PW2037 с описанием особенностей принятых конструктивных решений.
Наружное кольцо 1 шарикоподшипника 2 крепится к фланцу 3. Подвод масла осуществляется под внутренний буртик маслосборного кольца 4,
àзатем по отверстиям в опорном бурте вала 5 и пазам внутреннего кольца 6 на тело качения.
Наружное кольцо 1 роликоподшипника 2 имеет фланец для крепления к корпусу 3 опоры. Подвод масла осуществлен под внутреннее кольцо роликоподшипника. Рядом с роликоподшипником расположено два контактных уплотнения 4, изолирующих масляную полость опоры от межвальной полости роторов ВД и НД.
Передача осевого усилия на шарикоподшипник 1 с вала 2 и далее на корпусной фланец осуществлена через бурты на валу ротора и фланце 3.
Опора расположена в «горячей» зоне. Фланец 1 имеет V-образную форму для компенсации различ- ных температурных расширений наружной и внутренней части. Опора защищена теплоизоляционным корпусом 2. Наружное кольцо роликоподшипника 3 имеет увеличенную длину для компенсации монтажных неточностей и теплового расширения.
Наружное кольцо роликоподшипника 1 имеет упругий элемент, а внутреннее кольцо – увели- ченную длину. Опора защищена теплоизоляционным кожухом 2.
4.4.7.2 – Конструкция опор наземных ГТД
В конструкции опор наземных ГТД применяются те же конструктивные решения, что и в опорах авиационных двигателей. В случае создания наземных ГТУ на базе существующих авиационных
200

Глава 4 - Силовые схемы ГТД
|
Рисунок 4.4.7.1_11 - Опора шарикоподшипника |
|
ротора ВД |
Рисунок 4.4.7.1_9 - Опора шарикоподшипника |
1 – радиально-упорный шари- |
ротора НД |
коподшипник; 2 – вал ротора |
1 – наружное кольцо с фланцем; |
ВД; 3 – силовой фланец; |
2 – радиально-упорный шарико- |
4 – корпус; 5 – вал ротора НД; |
подшипник; 3 – фланец подшип- |
6 – контактное уплотнение |
ника; 4 – маслосборное кольцо; |
|
5 – вал ротора НД; 6 – внутрен- |
|
нее разъемное кольцо; 7 – кон- |
|
тактное уплотнение; 8 – корпус |
|
Рисунок 4.4.7.1_10 - Промежуточная опора ротора |
Рисунок 4.4.7.1_12 - Задняя опора ротора ВД с |
|
роликоподшипником |
||
НД с роликоподшипником |
1 |
– фланец подшипника; |
1 – наружное кольцо подшип- |
2 – теплоизоляционный кожух; |
|
ника с фланцем; 2 – роликопод- |
3 |
– роликоподшипник; 4 – вал |
шипник; 3 – корпус опоры; |
ротора ВД; 5 – вал ротора НД; |
|
4 - контактное уплотнение |
6 |
– контактные уплотнения; |
(уплотнение межвального про- |
7 – корпус |
|
странства) ; 5 – вал ротора |
|
|
НД; 6 – вал ротора ВД |
|
|
201

Глава 4 - Силовые схемы ГТД
Рисунок 4.4.7.1_13 - Задняя опора ротора НД с роликоподшипником 1 – роликоподшипник; 2 – теп-
лоизоляционный кожух; 3 – вал ротора НД; 4 – контак-
тное уплотнение; 5 – корпус
конструкция опор предусматривает большую степень унификации применяемых деталей и узлов, что позволяет значительно удешевить производство.
4.5 – Подвеска ГТД
Как рассматривалось выше (см. раздел 4.1) часть усилий, возникающих в узлах ГТД, передается на силовые элементы самолета (для авиационных двигателей) и на силовую раму (для двигателей наземного применения).
Совокупность деталей ГТД, обеспечивающих передачу этих усилий, определяет систему подвески двигателя. Кроме того, детали подвески фиксируют двигатель относительно силовых элементов самолета или рамы с обеспечением необходимых степеней свободы.
В общем случае на детали системы подвески действуют следующие силы и моменты:
-осевая сила (сила тяги для авиационного
ÃÒÄ);
-вес двигателя;
-инерционные нагрузки от неуравновешенности ротора;
-неуравновешенная часть момента кручения на статорных деталях.
Для авиационных ГТД, кроме того, необходи-
мо учитывать инерционные нагрузки и гироскопи- ческий момент от ротора двигателя, возникающие при движении летательного аппарата.
Конструктивно система подвески включает в себя силовые корпуса двигателя, к которым прикреплены стержневые тяги, кронштейны, оси, соединяющие эти корпуса с силовыми элементами пилона (крыла, корпуса) самолета или рамы.
Как правило, каждая подвеска состоит из двух поясов – переднего и заднего. Центр масс ГТД обычно размещается примерно посредине между плоскостями крепления. Для упрощения условимся пояс передней подвески обозначать ППП, а пояс задней подвески – ПЗП.
Для анализа работы деталей подвески ГТД используется понятие схемы подвески. Это не что иное, как условное обозначение элементов подвески, показывающее взаимное положение и виды связей силовых элементов корпусов двигателя и самолета (рамы). Схема подвески позволяет определить распределение нагрузок между элементами подвески, провести необходимые прочностные рас- четы, оценку деформации корпусов.
Основная тенденция современных схем подвески двигателя - стремление к уменьшению прогиба геометрической оси силового корпуса двигателя (для ТРДД – силового корпуса газогенератора). От величины прогиба геометрической оси ГТД зависит выбор величины радиального зазора по лопаткам роторов, который является одним из факторов, определяющих КПД узлов компрессора и турбины, а следовательно – экономичность двигателя. Главное влияние на прогиб геометрической оси оказывает размещение на корпусе точки крепления, через которую передаются осевые нагрузки. Чем ближе точка «снятия» осевых нагрузок к оси двигателя, тем меньше изгибные деформации, тем более легким может быть выполнен корпус двигателя, с меньшими зазорами по лопаткам роторов, а следовательно – с более стабильными характеристиками экономичности в процессе эксплуатации.
В меньшей степени на прогиб корпусов влияет расположение точки крепления по оси двигателя. Она может быть расположена вблизи ППП,
вблизи ПЗП или между поясами подвески. От размещения этой точки крепления зависит характер эпюры изгибающего момента по оси двигателя.
На выбор схемы подвески ГТД влияет и конструкция силового корпуса, от которого зависит изменение радиальных зазоров между ротором и статором. Количество опор роторов и наличие жестких радиальных связей в корпусах в месте расположения этих опор, в частности в районе задней опоры
202

Глава 4 - Силовые схемы ГТД
КВД, исключает овализацию корпусов в месте расположения опор и при прогибах корпусов позволяет опорам отслеживать перемещения корпусов
âсоответствующих сечениях. Таким образом, силовой корпус является одним из элементов подвески, и подвеска вместе с корпусом составляют статически определимую ферму.
Для широко применяемых ТРДД в ряде слу- чаев в качестве силового корпуса подвески используется не только корпус газогенератора, но и часть корпуса наружного контура. Именно с корпуса наружного контура передается тяга на силовые элементы самолета.
Преимущества такой схемы следующие:
-простота конструкции элементов крепления и более короткие связи с самолетом;
-более высокий КПД силовой установки за счет меньшего загромождения канала наружного контура, через который эти связи (стержни) не проходят;
-использование жесткости самого наружного контура, наличие жестких радиальных связей в зоне ППП, как это осуществлено, например, на ТРДД RB-211, или промежуточный (разделительный) корпус, как на Д-30КУ и Д-30КП.
Так как при расположении точки снятия «осевого» усилия на наружном контуре плечо изгибающего корпус момента больше, то приходится усиливать корпус газогенератора. Этим исключаются большие прогибы геометрической оси ТРДД по сравнению с расположением такой же точки на газогенераторе. С другой стороны, при размещении переднего пояса подвески на газогенераторе приходится усиливать корпус газогенератора силовым кольцом - шпангоутом, на котором размещаются точки крепления.
На основании существующей практики проектирования можно сформулировать следующие общие требования, предъявляемые к конструкции и расположению на двигателе узлов крепления:
-удобство замены ГТД и его технического обслуживания в эксплуатации;
-точки подвески должны быть расположены на двигателе так, чтобы обеспечивалось крепление двигателя в направлении всех шести степеней свободы - в осевом, вертикальном и боковом направлениях, вокруг продольной, вертикальной и горизонтальной осей. При этом система подвески должна быть статически определима, т.е. не допускается двойного крепления в направлении и вокруг указанных осей. Благодаря этому корпусная система двигателя изолируется от деформации самолетной конструкции и предупреждается возникновение
âузлах подвески нерасчетных нагрузок;
-конструкция элементов крепления двигателя при всех условиях полета и режимах работы не должна препятствовать термическим деформациям корпуса двигателя;
-точки подвески должны быть расположены на силовых корпусах газогенератора в зоне расположения внутренних связей опор;
-форсажная камера может иметь дополнительную «точку» подвески в плоскости корпуса реактивного сопла. Для обеспечения статической определимости конструкция дополнительной «точ- ки» подвески должна обеспечивать необходимую степень свободы (применение шарнирного соединения и т.д.);
-для проведения такелажных, монтажных
èтранспортировочных работ на двигателе предусматриваются специальные точки крепления
èподдержки. Обычно их располагают в районах
ППП и ПЗП и проектируют с выполнением требований, предъявляемых к основным элементам подвески.
4.5.1 – Схемы подвески ГТД на самолете
Выбор схемы подвески двигателя на самолете, конструктивное исполнение элементов подвески определяется необходимостью выполнения «двигательных» требований, о которых говорилось выше, а с другой стороны - диктуется также нали- чием «самолетных» требований (расположение двигателя на летательном аппарате, конструкция силовых элементов самолета, особенности эксплуатации и т.д.).
В настоящее время в гражданской и транспортной авиации наиболее часто двигатель на самолете подвешивается на пилоне под крылом. Пример такого расположения двигателя представлен на Рис. 4.5.1_1. Для двигателей, устанавливаемых на пилонах под крылом самолета, обязательно выполнение элементов крепления к самолету в верхней части в районе расположения пилона. На Рис. 4.5.1_2 показана схема подвески двигателя RB-211. Подвеска двигателя выполнена по «класси- ческой» схеме, с наличием ППП и ПЗП и предназначена для крепления двигателя на пилоне под крылом самолета.
Как упоминалось выше, в качестве силового элемента в ППП использован корпус наружного контура, а в ПЗП - корпус газогенератора.
Схема подвески двигателя Д-30КП на самолете Ил-76 (см. Рис. 4.5.1_3) весьма похожа на предыдущую конструкцию подвески ГТД на пилоне, под крылом.
203

Глава 4 - Силовые схемы ГТД
Рисунок 4.5.1_1 – Самолет Ил-96-300 с двигателями ПС-90А, расположенными на пилонах под крылом
Рисунок 4.5.1_2 – Схема подвески ТРДД RB-211 (Печатается с разрешения Rolls-Royce plc.)
1, 2, 4, 5, 6 – стержни, воспринимающие вертикальные, боковые нагрузки и крутящий момент; 3 – штырь, воспринимающий осевые усилия (тягу двигателя); 7, 8 – кронштейны силовой подвески на пилоне самолета; 9, 10 - силовой элемент пилона самолета
В случае расположения ГТД в хвостовой час- |
У двигателя Д-30 (см. Рис. 4.5.1_7) точки креп- |
ти самолета или в фюзеляже самолета (для воен- |
ления силовых элементов расположены на наруж- |
ной авиации) применяется боковая подвеска само- |
ном контуре. Несомненно, это позволило значитель- |
ëåòà (ñì. Ðèñ. 4.5.1_4, 4.5.1_5, 4.5.1_6). |
но упростить конструкцию системы подвески, но |
204

Глава 4 - Силовые схемы ГТД
Рисунок 4.5.1_3 – Схема подвески ТРДД Д-30КП 1, 2, 4 – стержни, воспринимающие вертикальные, боковые нагрузки и крутящий момент;
3 – штырь, воспринимающий осевые усилия (тягу двигателя); 5 – силовой элемент пилона самолета
Рисунок 4.5.1_4 – Самолет Ил-62М с двигателями Д-30КУ
Рисунок 4.5.1_5 – Самолет Ту-134А с «боковым» расположением двигателей Д-30
205

Глава 4 - Силовые схемы ГТД
повлекло за собой необходимость усиления корпус- |
Рассмотрим более подробно схему подвески |
ных деталей и введения радиальных ребер между |
двигателя ПС-90А на самолетах Ил-96-300 и Ту-204. |
наружным и внутренним корпусом в зоне ПЗП. |
Эта схема подвески была реализована позднее, чем |
|
показанные выше для двигателей RВ-211 и Д-30КП. |
|
В схеме был учтен опыт предыдущих разработок |
|
и введен дополнительный элемент – пояс средней |
|
подвески (ПСП), позволяющий уменьшить дефор- |
|
мацию корпусов газогенератора. |
|
В схему подвески двигателя ПС-90А(см. |
|
Рис. 4.5.1_8) входят разделительный корпус 1, си- |
|
ловое кольцо 2 компрессора, силовое кольцо 3 зад- |
|
ней опоры, передние тяги 4 и 5, горизонтальная тяга |
|
6, кронштейн 7 средней подвески с тягой 8, тяга на- |
|
клонная 9, тяги задние 10,11,12 и кронштейн 13 зад- |
|
него пояса подвески. Наличие ПСП позволяет раз- |
|
грузить корпуса газогенератора и уменьшить |
|
величину их прогибов. Передача силы тяги от си- |
|
ловых корпусов газогенератора двигателя (см. раз- |
Рисунок 4.5.1_6 – Самолет МиГ-31 с двигателями |
дел 4.3) осуществляется через кронштейн задней |
Ä-30Ô6 |
подвески. Тяги ППП имеют шарнирное соединение |
|
как с корпусами газогенератора, так и с силовыми |
Рисунок 4.5.1_7 – Схема подвески ТРДД Д-30 1, 2, 3, 4, 5 - стержни, воспринимающие вертикальные, боковые нагрузки и крутящий
момент; 6 – стержень, воспринимающий осевые усилия (тягу двигателя); 7 – силовые элементы корпуса самолета, 8 – радиальные ребра
206

Глава 4 - Силовые схемы ГТД
Рисунок 4.5.1_8 – Схема системы подвески двигателя ПС-90А 1 - разделительный корпус; 2 - силовое кольцо компрессора; 3 - силовое кольцо задней
опоры; 4 и 5 - тяги передние; 6 - тяга горизонтальная; 7 - кронштейн средней подвески; 8 -тяга средней подвески; 9 - тяга наклонная; 10, 11, 12 - тяги задние; 13 - кронштейн заднего пояса подвески, 14 – корпус газогенератора
Рисунок 4.5.1_9 – Самолет А-40 с «верхним» расположением двигателя
элементами пилона самолета. Тяги ПЗП также шарнирно закреплены и к корпусам газогенератора, и к кронштейну 13, но сам кронштейн жестко закреплен за пилон самолета.
Для гидросамолетов характерно расположение двигателя на пилоне над крылом летательного аппарата (см. Рис. 4.5.1_9). Как правило, в таких случаях осуществляется «нижняя» подвеска двигателя, т.е. элементы крепления к самолету распо-
лагается в нижней части двигателя, но это не является обязательным. В случае применения существующего ГТД с «боковой» или даже «верхней» подвеской во избежание переделки отработанной силовой схемы двигателя может быть принято решение о сохранении двигательной части системы подвески. Это приводит к необходимости установки на летательном аппарате дополнительных силовых ферм, обеспечивающих принятую систему подвески для ГТД.
4.5.2 – Схемы подвески наземных ГТД
При выборе схемы подвески ГТД наземного применения также обязательно выполнение требований по двигателю, которые предъявляются для авиации. Но если для авиационных двигателей элементы подвески предназначены прежде всего для передачи тяги двигателя в качестве основной нагрузки, то для двигателей наземного применения элементы подвески должны в первую очередь обеспечивать передачу крутящего момента.
207

Глава 4 - Силовые схемы ГТД
Размещение двигателя наземных установок на специальной раме, при менее жестких, чем в авиации, требованиях по массе и габаритам позволяет упростить конструкцию подвески. Как правило, на наземных установках применяется два пояса подвески с системой простых по конструкции стержней (тяг) и шарниров.
На Рис. 4.5.2_1 в качестве примера представлена схема подвески наземной установки ГТУ-16П.
4.6 – Конструкция подвесок ГТД
Как упоминалось выше, детали подвески ГТД осуществляют его фиксацию относительно силовых элементов самолета (для авиационных двигателей) или силовой рамы (для двигателей наземного применения). Кроме того, именно детали подвески обеспечивают передачу усилий, возникающих в узлах ГТД, на силовые элементы самолета (рамы).
Рисунок 4.5.2_1 – Схема подвески установки ГТУ-16П 1 - двигатель; 2 – рама; 3 – стержни, воспринимающие вертикальные, боковые нагрузки
и крутящий момент; 4 – стержень, воспринимающий осевое усилие
208

Глава 4 - Силовые схемы ГТД
Конструктивное исполнение систем подвесок ГТД разнообразно и зависит от индивидуальных конструктивных особенностей как двигателя, так и объекта его применения. Большое влияние на выбор конструктивных решений имеют опыт и традиции фирм-разработчиков. Даже при выполнении одинаковых схем подвески конструкция деталей, узлов крепления бывают весьма различными не только у ГТД различных разработчиков, но и у модификаций одного двигателя.
4.6.1 – Конструкция подвески авиационных ГТД
Рассмотрим конструктивное исполнение системы подвески и ее отдельных узлов на примере крепления двигателя ПС-90А на самолетах Ил-96- 300, Ту-204. Двигатели ПС-90А на этих самолетах расположены на пилонах под крыльями и имеют «верхнюю» подвеску.
Схема системы подвески двигателя ПС-90А показана на Рис. 4.5.1_8.
Система подвески двигателя имеет три пояса. Передний силовой пояс (ñì. Ðèñ. 4.6.1_1, сече- ние А-А) образован разделительным корпусом 1, пе-
редним силовым кольцом 2 компрессора, передней опорой ротора вентилятора и подпорных ступеней, задней опорой ротора вентилятора и передней опорой КВД. На разделительном корпусе расположены два транспортировочных фланца 3 для крепления двигателя на технологической тележке, два кронштейна 4 для такелажных работ и две тяги 5 для крепления двигателя к силовой балке 6 пилона самолета. Передняя подвеска двигателя осуществляется двумя тягами, расположенными V-образ- но. Нижними концами тяги шарнирно крепятся к переднему силовому кольцу, а верхними концами надеваются на конические цапфы кронштейна силовой балки пилона самолета или траверсе люльки транспортировочного ящика (см. Рис. 4.6.1_1, элемент Г).
Средний силовой пояс (см. Рис. 4.6.1_1, сече- ние Б-Б) образован задним силовым кольцом подвески 7, расположенным на корпусе КВД , корпусом опоры шарикового подшипника ротора КВД, опорой роликового подшипника ТВД. На заднем силовом кольце шарнирно закреплены тяга 8 средней подвески 8 и кронштейн силовой подвески средней 9.
Задний силовой пояс (см. Рис. 4.6.1_1, сечение В-В) образован задней опорой двигателя и опорой роликового подшипника ТНД. Задняя подвеска образована тремя тягами 10, расположенными в виде буквы “И” и кронштейном подвески 11. Тяги зак-
реплены нижними концами на силовом кольце 12 задней опоры, а верхними на кронштейне подвески. Кронштейн при помощи сферического шарнира
èдвух тяг силовой балки крепится к силовой балке пилона самолета (см. Рис. 4.6.1_1, элемент Д) или к траверсе люльки транспортировочного ящика.
Все три силовых пояса связаны между собой корпусами газогенератора и системой тяг: передний
èсредний силовые пояса - тягой горизонтальной 13, а средний и задний - тягой наклонной 14. Горизонтальная тяга шарнирно прикреплена одним концом к разделительному корпусу, другим - к кронштейну средней подвески. Наклонная тяга одним концом шарнирно крепится к кронштейну средней подвески, другим - к кронштейну подвески.
Передняя подвеска передает на пилон самолета в точках крепления инерционные и аэродинамические силы, воздействующие на двигатель
èгондолу в вертикальной плоскости. Задняя подвеска передает на пилон самолета прямую и обратную тяги двигателя, инерционные и аэродинами- ческие силы, действующие в горизонтальной
èвертикальной плоскостях перпендикулярно оси двигателя, а также возникающий крутящий момент в плоскости, перпендикулярной оси двигателя. Тяги горизонтальная и наклонная, поддерживая средний силовой пояс, повышают изгибную жесткость корпуса газогенератора и, таким образом, препятствуют прогибу корпуса газогенератора
èроторов двигателя.
Остановимся более подробно на конструкции разделительного корпуса и задней опоры, являющихся обязательной принадлежностью переднего и заднего поясов подвесок современных авиационных двигателей.
Разделительный корпус современного ГТД, является важной частью силовой схемы двигателя. Он осуществляет жесткую силовую радиальную связь корпусов газогенератора с передними опорами двигателя. Как правило, в одновальных ГТД в разделительном корпусе расположена передняя опора компрессора, а в двухвальных ГТД – передняя опора КВД и задняя опора вентилятора. В более сложных силовых схемах двухконтурных двигателей разделительный корпус обеспечивает силовую связь корпусов газогенератора с наружными силовыми корпусами (корпус вентилятора, кожух наружный, реверс, сопло). Как правило, именно на разделительном корпусе находится передний пояс подвески ГТД к самолету или раме в наземных установках.
Разделительный корпус представляет собой сложную тонкостенную литую конструкцию. На некоторых изделиях элементы корпусов соедине-
209

210 |
Глава |
|
ГТД схемы Силовые - 4 |
Рисунок 4.6.1_1 – Система подвески двигателя ПС-90А 1 - разделительный корпус; 2 – переднее силовое кольцо компрессора; 3 – фланец транс-ортировочный; 4 – кронштейн такелаж-
ный; 5 - тяги передние; 6 – силовая балка пилона самолета; 7 – заднее силовое кольцо компрессора; 8 – тяга средней подвески; 9 – кронштейн средней подвески; 10 - тяги задние; 11 - кронштейн заднего пояса подвески; 12 – силовое кольцо задней опоры; 13 – тяга горизонтальная; 14 – тяга наклонная

Глава 4 - Силовые схемы ГТД
ны при помощи сварки. Корпуса приводов имеют фланцы для крепления к корпусам опор двигателя, для установки различных крышек, элементов подвода и отвода масла и т.п. Для увеличения жесткости конструкции корпуса, как правило, имеют ребра. Корпуса центральных приводов большинства изделий изготовляются из литейных сплавов на основе магния или титана.
На Рис. 4.6.1_2 представлен разделительный корпус двигателя ПС-90А. Разделительный корпус расположен между вентилятором 1, компрессором 2 низкого давления – с одной стороны и компрессором 3 высокого давления – с другой стороны. Конструктивно он состоит из двух частей: наружного 4 и внутреннего 5 корпусов, соединенных между собой шпильками.
Разделительный корпус изготовлен методом литья из сплава магния МЛ-5. В проточной части наружного контура (см. Рис. 4.6.1_3) имеются 12 стоек - четыре радиальных (верхняя 1, нижняя 2, две
горизонтальные 3) и четыре пары наклонных стоек 4, воспринимающих крутящие моменты. В проточ- ной части внутреннего контура расположены шесть радиальных стоек, равномерно расположенных по окружности.
Во внутренней полости разделительного корпуса расположен центральный привод, который служит для отбора мощности на коробку приводов от ротора компрессора высокого давления. Кинемати- ческая схема центрального привода представляет собой две пары зубчатых колес: цилиндрическую и коническую. На валу ротора компрессора высокого давления установлено ведущее цилиндрическое зубчатое колесо 6. Ведомое цилиндрическое зуб- чатое колесо и пара конических зубчатых колес смонтированы в одном блоке - в корпусе приводов 7. Корпус приводов монтируется во внутренней полости внутреннего корпуса. В корпусе приводов расположена задняя опора 8 вентилятора.
В задней части внутреннего корпуса расположена передняя опора 9 КВД. На переднем фланце внутреннего корпуса установлен корпус опоры вентилятора 10, в которой расположена передняя опора вентилятора 11.
Задняя опора является силовым элементом двигателя, обеспечивающим жесткую радиальную связь корпуса газогенератора с задней опорой двигателя. Как правило, задняя опора часто является
Рисунок 4.6.1_2 – Разделительный корпус двигате- |
|
|
ëÿ ÏÑ-90À |
|
|
1 |
- вентилятор; 2 - КВД; |
|
3 |
- КНД; 4 - корпус наружный; |
Рисунок 4.6.1_3 – Силовые элементы (ребра) разде- |
5 |
- корпус внутренний; 6 - колесо |
|
зубчатое; 7 - корпус привода; |
лительного корпуса двигателя |
|
8 |
- опора задняя вентилятора; |
ÏÑ-90À |
9 |
- передняя опора КВД; 10 - кор- |
1 - стойка верхняя; 2 - стойка |
пус опоры вентилятора; 11 - опо- |
нижняя; 3 - стойка боковая; |
|
ра передняя вентилятора |
4 - стойки наклонные |
211

Глава 4 - Силовые схемы ГТД
частью заднего пояса подвески ГТД к самолету или раме наземных установок.
Кроме того, узел задней подвески двигателя обеспечивает установку датчиков для контроля температуры и полного давления газа за турбиной, детали подвода и отвода масла, а также крепление элементов смесительного устройства двигателя.
Пример конструкции задней опоры двигателя ПС-90А приведен на Рис. 4.6.1_4.
Задняя опора включает в себя шестистоечный корпус 1, силовое кольцо 2, внутренний корпус 3, соединенные между собой болтами и образующие силовой корпус задней опоры, кожух защитный 4, который служит для защиты силового кольца от соприкосновения с горячими газами.
В заднюю опору также входят:
-передняя диафрагма 5 для защиты внутренних полостей опоры от попадания горячих газов, выходящих из турбины;
-обтекатели 6 для защиты шестистоечного корпуса от горячих газов;
-корпус термопар 7;
-козырьки 8 для забора воздуха из наружного контура двигателя для охлаждения внутренних полостей задней опоры;
-кронштейны 9 и тяги 10 для соединения задней опоры с наружным корпусом;
-тяги 11 и кронштейн 12 для подвески двигателя на самолете;
-кронштейны 13 крепления термопар, термопары 14 для контроля температуры газа за турбиной;
-смеситель 15 и конус 16, являющиеся элементами смесительного устройства;
-диафрагма 17.
Через три стойки опоры проходят трубы подвода и откачки масла на охлаждение подшипника и труба суфлирования масляной полости задней опоры. Через одну стойку выводятся проводники термопар.
Силовое кольцо, шестистоечный корпус, внутренний корпус выполнены из жаропрочного титанового сплава. Кожух защитный и обтекатели выполнены из жаростойкого сплава. Тяги и кронштейн подвески выполнены из сплава типа ЭП517.
На Рис. 4.6.1_5 показана система подвески двигателя фирмы Rolls-Royce RВ 211-22В.Двига- тель имеет традиционную схему системы подвески, имеющую два силовых пояса – ППП и ПЗП. Кронштейн 1 ППП крепится к корпусу 2 наружного контура, поэтому в силовую конструкцию ППП
Рисунок 4.6.1_4 - Опора задняя 1 – корпус со стойками; 2 – кольцо силовое; 3 – корпус внутренний; 4 – кожух защитный;
5 – диафрагма; 6 – обтекатель; 7 – корпус термопар; 8 – козырек; 9 – кронштейн; 10 – тяга; 11 – тяга; 12 – кронштейн; 13– кронштейн; 14 – термопары; 15 – смеситель; 16 – конус; 17 - диафрагма
212

Глава 4 - Силовые схемы ГТД
Рисунок 4.6.1_5 – Двигатель Rolls-Royce RВ 211-22В (Печатается с разрешения Rolls-Royce plc.)
1 – кронштейн ППП; 2 – корпус наружного контура; 3 – тяга; 4 - корпус газогенератора; 5 – кронштейн ПЗП
необходимо ввести силовые радиальные связи – |
мации корпуса газогенератора. |
тяги 3 между корпусом 2 и силовым корпусом 4 |
Боковую систему подвески двигателя рассмот- |
газогенератора. На ПЗП расположен кронштейн 5, |
рим на примере крепления двигателя Д-30 III се- |
который как и кронштейн 1 служит для крепления |
рии на самолете Ту-134А и Д-30Ф6 на самолете |
двигателя к пилону самолета |
ÌÈÃ-31. |
На Рис. 4.6.1_6 показано конструктивное ис- |
Двигатель Д-30 (см. Рис. 4.6.1_9) имеет два |
полнение системы подвески двигателя RR Trent |
пояса подвески. В ППП в верхней части входного |
800. Система подвески имеет два силовых пояса – |
корпуса компрессора находится кронштейн 1 с ко- |
ППП и ПЗП с кронштейнами 1 и 2 соответственно |
нической цапфой, к которой монтируется две тяги |
крепления двигателя к пилону самолета. В отличие |
2. В ПЗП находится силовой корпус 3 подвесок, на |
от ранее рассмотренной схемы подвески двигате- |
котором установлены семь кронштейнов 4 (один – |
лей RB-211 и Trent 800 для разгрузки корпусов га- |
в верхней части, шесть – симметрично вертикаль- |
зогенератора между кронштейном ПЗП и силовым |
ной оси двигателя). В зависимости от того, в пра- |
корпусом компрессора, входящим в ППП, установ- |
вой или левой мотогондоле расположен двигатель, |
лена наклонная тяга 3. |
будут заняты только четыре задних точки подвес- |
На Рис. 4.6.1_7 представлен двигатель фирмы |
ки (верхняя и три боковых с какой-либо стороны). |
Pratt & Whitney PW4000. На двигателе PW4000 |
В ПЗП к кронштейну 4 подсоединены тяга 5, две |
максимально реализовано требование приближе- |
тяги 6 и тяга 7, с помощью которых передаются |
ния точки «снятия» осевых нагрузок к оси двига- |
крутящий момент, боковые и вертикальные нагруз- |
теля. Пилон 1 через силовые кронштейны 2 и 3 со- |
ки. Передача осевого усилия производится через |
единен практически непосредственно с корпусом |
тягу 8. Для подъема двигателя имеются три крон- |
газогенератора 4. Подобное конструктивное реше- |
штейна, из которых два кронштейна 9 закреплены |
ние позволяет минимизировать изгибные дефор- |
на шпильках заднего фланца разделительного кор- |
213

Глава 4 - Силовые схемы ГТД
Рисунок 4.6.1_6 – Двигатель Rolls-Royce Trent 800 (Печатается с разрешения Rolls-Royce plc.)
1 – кронштейн ППП; 2 – кронштейн ПЗП; 3 – наклонная тяга
Рисунок 4.6.1_7 – Двигатель Pratt & Whitney PW4000
1 – пилон крыла самолета; 2 – кронштейн ППП; 3 – кронштейн ПЗП; 4 – корпус газогенератора
214

Глава 4 - Силовые схемы ГТД
Рисунок 4.6.1_8 – Крепление двигателя Д-30 на самолете Ту-134 1 – кронштейн; 2 – тяги ППП; 3 – силовой корпус ПЗП; 4 – кронштейн ПЗП;
5, 6, 7, 8 – тяги; 9, 10 – кронштейны для подъема двигателя; 11 – технологические фланцы разделительного корпуса
Рисунок 4.6.1_9 – Крепления двигателя Д30-Ф6 в двигательном отсеке самолета МИГ-31 1 – кронштейн ППП; 2 – болт подвески; 3 – контровочный замок; 4 - кронштейн ПЗП;
5 – подвеска боковая транспортировочная; 6 – кронштейн такелажный; 7 – кронштейн крепления приспособления для закатки двигателя в двигательный отсек; 8 – передний кронштейн; 9 – задний кронштейн; 10 – тяга; 11 – упор; 12 – кронштейны «стяжки»
215

Глава 4 - Силовые схемы ГТД
пуса и один кронштейн 10 прикреплен болтами к заднему фланцу диффузора и переднему фланцу заднего корпуса камеры сгорания. В транспортировочном ящике, а также на монтажной тележке двигатель крепится в задней части за два боковых кронштейна 4 и в передней части – за цапфы, устанавливаемые на два боковых фланца 11 разделительного корпуса.
Двигатель Д-30Ф6 в двигательном отсеке самолета МИГ-31 крепится к самолетным подвескам
âдвух силовых поясах (см. Рис. 4.6.1_9). ППП расположен на разделительном корпусе, ПЗП – на силовом кольце задней опоры.
Крепление двигателя в переднем поясе осуществляется в одной точке с помощью передней подвески, а в заднем поясе – в трех точках с помощью двух кронштейнов.
Передняя подвеска состоит из кронштейна 1, болта-подвески 2 со сферическим подшипником и контровочного замка. Кронштейн крепится двумя призонными болтами к верхней стойке разделительного корпуса и четырнадцатью – к его фланцам . На заднем фланце кронштейна имеются три такелажных отверстия. Болт-подвеска вворачивается в резьбовое отверстие верхней цилиндрической части кронштейна и контрится замком 3. В болт-подвес- ку завальцован сферический подшипник, в который вставляется болт регулируемой тяги подвески переднего крепления двигателя в двигательном отсеке самолета.
Кронштейны 4 силового кольца задней опоры крепятся к фланцам наружного силового кольца задней опоры. На кронштейне имеются по две проушины, за которые крепятся тяги крепления двигателя
âдвигательном отсеке самолета. Правый двигатель крепится с помощью двух тяг к проушинам левого кронштейна и одной тягой к верхней проушине правого кронштейна. Левый двигатель крепится с помощью двух тяг к проушинам правого кронштейна и одной тягой к верхней проушине левого кронштейна.
Боковые транспортировочные подвески на разделительном корпусе используются при транспортировке двигателя на специальной тележке и установке двигателя на транспортировочную «люльку». Узел боковой транспортировочной подвески состоит из боковой подвески 5 и деталей крепления. Боковая подвеска крепится к разделительному корпусу. На боковой подвеске имеется фланец с посадочным отверстием под цилиндрический выступ бокового транспортировочного кронштейна и четыре резьбовых отверстия для крепления бокового транспортировоч- ного кронштейна.
Такелажные кронштейны 6 служат для подъема двигателя спецприспособлением и используются при монтаже и демонтаже двигателя в транспортировочную люльку. Такелажный кронштейн пятью болтами с самоконтрящимися гайками крепится к фланцу переднего корпуса ФК. Кроме того, для такелажных работ используются отверстия на кронштейне передней подвески.
Задние кронштейны 7 крепления приспособления для закатки двигателя установлены на заднем фланце корпуса ФК и служат для крепления кронштейна задней каретки приспособления для закатки.
Передние кронштейны «закатки» предназначены для крепления «лыж» при закатке двигателя в двигательный отсек самолета. Они расположены на входном корпусе КНД. Для закатки двигателя в двигательный отсек самолета применяются большой кронштейн и малый кронштейн. Эти два кронштейна аналогичны по конструкции, но различаются по размерам. Каждый из кронштейнов состоит из переднего кронштейна 8, заднего кронштейна 9 и тяги 10, соединяющей эти кронштейны. Конструкция тяги позволяет регулировать ее длину.
На правом двигателе большой кронштейн ставится с правой стороны двигателя, а малый кронштейн - с левой. На левом двигателе – наоборот.
Расположенные на корпусе ФК упоры 11 предназначены для передачи осевого усилия от тяг задней каретки приспособления для закатки двигателя в самолет на корпуса двигателя. Каждый упор крепится к ребру жесткости корпуса.
Кронштейны 12 «стяжки», расположенные на фланцевом разъеме корпуса с экранами ФК и регулируемого сопла, служат для крепления самолетных тяг, соединяющих регулируемые сопла правого и левого двигателей.
4.6.2 – Конструкция подвесок наземных ГТД
Конструктивное исполнение систем подвесок ГТД на наземных установках также многообразно, как и на авиационных двигателях. Часто в комплект поставки наземных ГТУ входит и силовая рама, на которой закреплен двигатель. Таким образом на за- воде-изготовителе производится полный монтаж ГТД на силовой раме с установкой элементов системы подвески. Транспортируется и монтируется на месте уже готовый модуль ГТУ. Пример такого исполнения рассмотрим на установке ГТУ-16П (см. Рис. 4.6.2_1).
Рама двигателя представляет собой сварную конструкцию из стальных катаных профилей, на
216

Глава 4 - Силовые схемы ГТД
Рисунок 4.6.2_1 – Установка ГТУ-16П 1 и 2 – кронштейны; 3 и 4 – тяги подвески; 5 – опорная лапа; 6 – втулка; 7 – рама;
8 – штырь; 9 – сферический подшипник
которой смонтированы кронштейны 1, 2 крепления тяг 3, 4. Рама имеет четыре опорные лапы 5 для крепления ее на раме ГТУ или в транспортировочном контейнере. На торцах рамы приварены втулки 6 для установки колес при монтаже двигателя на раму ГТУ. Для исключения перемещения в осевом направлении двигатель фиксируется при помощи штыря 8, расположенного на силовом кольце задней опоры свободной турбины. Штырь входит в сферический подшипник 9, закрепленный на раме двигателя.
4.7 - Англо-русский словарьминимум
applied force – приложенная сила axial clearance – осевой зазор axial force – осевая сила
axial load – осевая нагрузка
balance chamber - разгрузочная полость ball bearing – шарикоподшипник bearing – подшипник, опора
bearing cage – обойма подшипника
217

Глава 4 - Силовые схемы ГТД
bearing chamber – полость подшипника bearing housing - корпус подшипника bending load - изгибающая нагрузка bearing package – узел подшипника bearing race – обойма подшипника
bearing sump – масляная полость подшипника bearing support – опора подшипника
bracket - подвеска, кронштейн case – корпус
clearance – зазор
coking – коксообразование connection – соединение
contact seal - контактное уплотнение contamination - загрязнения, посторонние включения damperдемпфер
elastically supported bearing - подшипник с упругой установкой в опоре
engine front mount – передний узел подвески engine mount – узел подвески двигателя engine mount structure – подмоторная рама
engine-mounting trunnion – цапфа подвески двигателя
engine rear mount – задний узел подвески flange connection - фланцевое соединение
fluid stream lubrication - смазка масляной струей frame - рама, силовой корпус
gravity load – весовая нагрузка
grooved restrictor – лабиринтное уплотнение gyroscopic moment – гироскопический момент handling trunnion – цапфа для транспортировки двигателя
hanger – подвеска hoist – точка подвески
inertial force – сила инерции inertial load - инерционная нагрузка inner bearing – внутренняя обойма
internal diameter – внутренний диаметр intershaft bearing - межвальный подшипник joint – соединение, связь
link – тяга, звено
link connection – шарнирное соединение load bearing case - силовой корпус lubrication - смазка
main bearing – подшипник ротора ГТД
moment of momentum - момент количества движения mount – подвеска, крепление
mounting bracket - узел подвески oil baffle – маслоотражатель
oil damped bearing - подшипник с масляным демпфером
oil film - масляная пленка
oil film damper - масляный демпфер (подшипника) oil jet - масляная форсунка
oil nozzle – масляная форсунка
oil sample – проба масла
outer bearing – наружная обойма outer diameter - наружный диаметр pressure force – сила давления pylon – пилон
raceway – беговая дорожка подшипника radial bearing - опорный подшипник radial clearance – радиальный зазор restrictor – бесконтактное уплотнение roller – ролик
roller bearing – роликоподшипник
rotor support damper - демпфер опоры ротора shaft – вал
shield – защитная оболочка split bearing – разрезная обойма
spray-jet lubrication – смазка струйной форсункой static pressure – статическое давление
structural member– силовой элемент temperature strain – температурная деформация
thermal insulation blanket – теплоизоляционный слой
thrust bearing – упорный подшипник
under-race lubrication – смазка с подводом через отверстия во внутренней обойме подшипника
4.8 – Перечень использованной литературы
4.8.1.Конструкция и проектирование авиационных газотурбинных двигателей. Под ред. Д.В. Хронина. - М.: Машиностроение, 1989.
4.8.2.ÎÑÒ 100323-79. Валы и отверстия корпусов газотурбинных двигателей, посадки шариковых и роликовых подшипников.
4.8.3.ÃÎÑÒ 3189-89. Подшипники шариковые и роликовые. Система условных обозначений.
4.8.4.ÃÎÑÒ 7274-70.
4.8.5.ÃÎÑÒ 18855-94 (ИСО 251-90). Подшипники качения. Динамическая расчетная грузоподъемность и расчетный ресурс (долговечность).
4.8.6.Подшипники качения. Справочник-каталог. Под ред. В.И. Нарышкина и Корасташевского Р.В. - М.: Машиностроение, 1984.
4.8.7.Подшипники. Ограничительный перечень. – М.: 1989.
4.8.9.Методика расчетной оценки долговечности подшипников качения авиационных двигателей и их агрегатов, требования к конструктивным параметрам опор. ЦИАМ, 1996.
4.8.10.В.М. Демидович Исследование теплового режима подшипников ГТД - М.: Машиностроение, 1978.
218